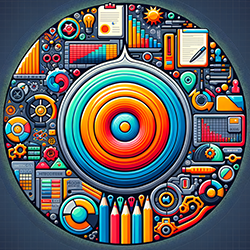
ANSYS CFX: ANSYS Fluent CFD Simulation Training Course
Workshop
Price:
$1,060.00
$149.00
Experience comprehensive CFD mastery with our “ANSYS CFX: All Levels” training course, featuring 10 in-depth tutorials that cover a wide range of fluid mechanics concepts. From basic fluid flow to advanced topics like turbulence modeling and multiphase flows, this course guides you through interactive, step-by-step simulations using ANSYS CFX software. You’ll learn essential skills in meshing, CFX setup, and post-processing, tackling diverse projects such as storage tank analysis, heat exchanger design, propeller simulation, and combustion chamber modeling. Whether you’re a beginner or an experienced engineer, this course will enhance your CFD capabilities, enabling you to set up, run, and interpret complex simulations for real-world engineering challenges.
Particle Transport in Bent Pipe CFD Simulation
Master Particle Transport Simulation in Bent Pipes with ANSYS CFX Dive into the intricate world of multiphase flow dynamics with our comprehensive tutorial on “Particle Transport in Bent Pipe” using ANSYS CFX. This essential episode in our “ANSYS CFX: All Levels” course offers an in-depth exploration of particle-fluid interactions, crucial for engineers in various industries dealing with particle-laden flows. Unlock Advanced CFD Techniques for Multiphase Flow Analysis Learn to harness the power of ANSYS CFX to simulate and analyze complex particle transport phenomena in bent pipes. This tutorial provides a detailed approach to modeling particle-fluid interactions, essential for optimizing pipeline designs, preventing erosion, and enhancing overall system efficiency. Key Learning Objectives: - Master the setup of 3D bent pipe models in SpaceClaim for particle transport simulations - Develop proficiency in unstructured mesh generation for complex geometries with multiphase flow - Understand the application of Fully Coupled Particle Transport Fluid Morphology - Analyze particle distribution, pressure drop, and flow patterns in bent pipes Comprehensive Simulation Setup and Methodology Gain hands-on experience in configuring and executing a professional-grade CFD simulation for particle transport in bent pipes, covering all aspects from geometry creation to advanced flow visualization. 1. Precise 3D Geometry and Advanced Mesh Generation - Create optimized 3D models of bent pipes using SpaceClaim - Implement unstructured meshing strategies with ANSYS Meshing for accurate multiphase flow simulation - Optimize mesh quality for complex geometries (139,461 elements) 2. ANSYS CFX Configuration for Particle Transport Simulation - Set up Fully Coupled Particle Transport Fluid Morphology for accurate particle-fluid interaction modeling - Configure Scalable k-Epsilon turbulence model for robust flow prediction - Implement High Resolution schemes for Advection and Turbulence Numerics 3. Advanced Data Analysis and Visualization Techniques - Extract and interpret velocity, pressure, and turbulence kinetic energy distributions - Analyze particle volume fraction to understand particle distribution and accumulation - Evaluate flow patterns and vortex formation using streamlines and vector plots Real-World Applications and Industry Relevance This tutorial is crucial for professionals and researchers in: Oil and gas pipeline engineering Chemical process industry Water treatment and distribution systems Pneumatic conveying systems design Key Simulation Outcomes and Engineering Insights 1. Particle Distribution Analysis - Interpret the complex patterns of particle distribution throughout the bent pipe - Understand the mechanisms of particle accumulation and potential erosion hotspots 2. Flow Dynamics Evaluation - Analyze velocity patterns and vortex formation in the bent section - Assess the impact of pipe geometry on pressure drop and flow characteristics 3. Performance Optimization - Evaluate the effectiveness of the pipe design in transporting particles - Understand the relationship between flow conditions and particle behavior Elevate Your CFD Skills in Multiphase Flow Simulation By completing this specialized tutorial, you’ll gain: Cutting-edge skills in applying CFD to complex particle transport problems Proficiency in setting up and analyzing multiphase flow simulations in ANSYS CFX Deep understanding of particle-fluid interaction mechanisms in bent pipes Insights into optimizing pipe designs for improved particle transport and reduced erosion Who Should Take This Advanced Tutorial Pipeline engineers in oil, gas, and chemical industries Process engineers dealing with particle-laden flows CFD specialists focusing on multiphase flow simulations Graduate students in chemical or mechanical engineering studying multiphase flows Don’t miss this opportunity to significantly advance your CFD simulation skills in particle transport analysis. Enroll now in our “ANSYS CFX: All Levels” course and master the art of simulating particle transport in bent pipes using ANSYS CFX!
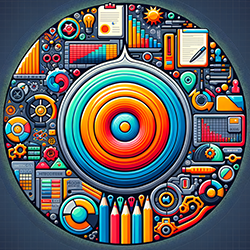
ANSYS CFX: ANSYS Fluent CFD Simulation Training Course
Workshop
Price:
$1,060.00
$149.00
Experience comprehensive CFD mastery with our “ANSYS CFX: All Levels” training course, featuring 10 in-depth tutorials that cover a wide range of fluid mechanics concepts. From basic fluid flow to advanced topics like turbulence modeling and multiphase flows, this course guides you through interactive, step-by-step simulations using ANSYS CFX software. You’ll learn essential skills in meshing, CFX setup, and post-processing, tackling diverse projects such as storage tank analysis, heat exchanger design, propeller simulation, and combustion chamber modeling. Whether you’re a beginner or an experienced engineer, this course will enhance your CFD capabilities, enabling you to set up, run, and interpret complex simulations for real-world engineering challenges.
Particle Transport in Bent Pipe CFD Simulation
Master Particle Transport Simulation in Bent Pipes with ANSYS CFX Dive into the intricate world of multiphase flow dynamics with our comprehensive tutorial on “Particle Transport in Bent Pipe” using ANSYS CFX. This essential episode in our “ANSYS CFX: All Levels” course offers an in-depth exploration of particle-fluid interactions, crucial for engineers in various industries dealing with particle-laden flows. Unlock Advanced CFD Techniques for Multiphase Flow Analysis Learn to harness the power of ANSYS CFX to simulate and analyze complex particle transport phenomena in bent pipes. This tutorial provides a detailed approach to modeling particle-fluid interactions, essential for optimizing pipeline designs, preventing erosion, and enhancing overall system efficiency. Key Learning Objectives: - Master the setup of 3D bent pipe models in SpaceClaim for particle transport simulations - Develop proficiency in unstructured mesh generation for complex geometries with multiphase flow - Understand the application of Fully Coupled Particle Transport Fluid Morphology - Analyze particle distribution, pressure drop, and flow patterns in bent pipes Comprehensive Simulation Setup and Methodology Gain hands-on experience in configuring and executing a professional-grade CFD simulation for particle transport in bent pipes, covering all aspects from geometry creation to advanced flow visualization. 1. Precise 3D Geometry and Advanced Mesh Generation - Create optimized 3D models of bent pipes using SpaceClaim - Implement unstructured meshing strategies with ANSYS Meshing for accurate multiphase flow simulation - Optimize mesh quality for complex geometries (139,461 elements) 2. ANSYS CFX Configuration for Particle Transport Simulation - Set up Fully Coupled Particle Transport Fluid Morphology for accurate particle-fluid interaction modeling - Configure Scalable k-Epsilon turbulence model for robust flow prediction - Implement High Resolution schemes for Advection and Turbulence Numerics 3. Advanced Data Analysis and Visualization Techniques - Extract and interpret velocity, pressure, and turbulence kinetic energy distributions - Analyze particle volume fraction to understand particle distribution and accumulation - Evaluate flow patterns and vortex formation using streamlines and vector plots Real-World Applications and Industry Relevance This tutorial is crucial for professionals and researchers in: Oil and gas pipeline engineering Chemical process industry Water treatment and distribution systems Pneumatic conveying systems design Key Simulation Outcomes and Engineering Insights 1. Particle Distribution Analysis - Interpret the complex patterns of particle distribution throughout the bent pipe - Understand the mechanisms of particle accumulation and potential erosion hotspots 2. Flow Dynamics Evaluation - Analyze velocity patterns and vortex formation in the bent section - Assess the impact of pipe geometry on pressure drop and flow characteristics 3. Performance Optimization - Evaluate the effectiveness of the pipe design in transporting particles - Understand the relationship between flow conditions and particle behavior Elevate Your CFD Skills in Multiphase Flow Simulation By completing this specialized tutorial, you’ll gain: Cutting-edge skills in applying CFD to complex particle transport problems Proficiency in setting up and analyzing multiphase flow simulations in ANSYS CFX Deep understanding of particle-fluid interaction mechanisms in bent pipes Insights into optimizing pipe designs for improved particle transport and reduced erosion Who Should Take This Advanced Tutorial Pipeline engineers in oil, gas, and chemical industries Process engineers dealing with particle-laden flows CFD specialists focusing on multiphase flow simulations Graduate students in chemical or mechanical engineering studying multiphase flows Don’t miss this opportunity to significantly advance your CFD simulation skills in particle transport analysis. Enroll now in our “ANSYS CFX: All Levels” course and master the art of simulating particle transport in bent pipes using ANSYS CFX!
-
Section 1
Storage Tank (Thermal)
-
Master Storage Tank CFD Simulation with ANSYS CFX Dive into the intricate world of fluid dynamics in storage systems with our comprehensive tutorial on “Storage Tank CFD Simulation” using ANSYS CFX. This pivotal episode in our “ANSYS CFX: All Levels” course offers an in-depth exploration of thermal fluid dynamics, essential for engineers and designers in various industries. Unlock Advanced CFD Techniques for Storage Tank Analysis Learn to harness the power of ANSYS CFX to simulate and analyze complex fluid behavior in storage tanks. This tutorial provides a detailed approach to modeling temperature-controlled fluid mixing, crucial for optimizing storage systems in chemical, petroleum, and process industries. Key Learning Objectives: - Master the setup of 2.5D storage tank models in ANSYS Design Modeler - Develop proficiency in structured mesh generation for fluid containment simulations - Understand the application of k-Epsilon turbulence models with Scalable Wall Functions - Analyze thermal mixing processes and fluid flow patterns in storage tanks Comprehensive Simulation Setup and Methodology Gain hands-on experience in configuring and executing a professional-grade CFD simulation for storage tanks, covering all aspects from geometry creation to advanced flow analysis. 1. Precise 2.5D Geometry and Mesh Generation - Create optimized 2.5D models of square-shaped storage tanks using ANSYS Design Modeler - Implement structured meshing strategies with ANSYS Meshing - Optimize mesh quality for accurate flow and thermal simulations (10,100 elements) 2. ANSYS CFX Configuration for Thermal Fluid Simulation - Set up Thermal Energy model for heat transfer analysis - Configure k-Epsilon turbulence model with Scalable Wall Function for accurate flow prediction - Implement High Resolution Advection Scheme and Turbulence Numerics for enhanced accuracy 3. Advanced Data Analysis and Visualization Techniques - Extract and interpret pressure, temperature, and velocity distributions - Analyze Eddy viscosity patterns and their impact on fluid mixing - Evaluate the effectiveness of inlet configurations on overall tank performance Real-World Applications and Industry Relevance This tutorial is crucial for professionals and researchers in: Chemical and petrochemical storage system design Food and beverage processing tank optimization Environmental engineering and water treatment facilities Thermal energy storage for renewable energy systems Key Simulation Outcomes and Engineering Insights 1. Thermal Mixing Analysis - Interpret the complex temperature distributions created by multiple inlets - Understand the influence of inlet configurations on overall tank temperature control 2. Flow Dynamics Evaluation - Analyze velocity patterns and pressure distributions within the tank - Assess the impact of inlet placement on fluid circulation and mixing efficiency 3. Performance Optimization - Evaluate the effectiveness of the tank design in achieving desired outlet temperatures - Understand the relationship between inlet conditions and overall system performance Elevate Your CFD Skills in Storage System Simulation By completing this specialized tutorial, you’ll gain: Cutting-edge skills in applying CFD to complex storage tank problems Proficiency in setting up and analyzing thermal fluid simulations in ANSYS CFX Deep understanding of turbulence modeling and heat transfer in contained flows Insights into optimizing storage tank designs for improved efficiency and temperature control Who Should Take This Advanced Tutorial Process engineers in chemical and petrochemical industries Thermal system designers for industrial applications Environmental engineers working on water treatment systems Graduate students in mechanical or chemical engineering Don’t miss this opportunity to significantly advance your CFD simulation skills in storage system analysis. Enroll now in our “ANSYS CFX: All Levels” course and master the art of simulating storage tanks with ANSYS CFX!
Episode 1 1h 10m 3s Free Episode
-
-
Section 2
Heat Exchanger
-
Master Plate Heat Exchanger CFD Simulation with ANSYS CFX Dive into the intricate world of heat transfer and fluid dynamics with our comprehensive tutorial on “Plate Heat Exchanger CFD Simulation” using ANSYS CFX. This essential episode in our “ANSYS CFX: All Levels” course offers an in-depth exploration of conjugate heat transfer, crucial for engineers and designers in thermal management and energy systems. Unlock Advanced CFD Techniques for Heat Exchanger Analysis Learn to harness the power of ANSYS CFX to simulate and analyze complex heat transfer phenomena in plate heat exchangers. This tutorial provides a detailed approach to modeling both fluid flow and heat conduction, essential for optimizing thermal systems across various industries. Key Learning Objectives: - Master the setup of 2.5D plate heat exchanger models in ANSYS Design Modeler - Develop proficiency in unstructured mesh generation with inflation layers for accurate boundary layer resolution - Understand the application of k-Epsilon turbulence models with Scalable Wall Functions in heat transfer simulations - Analyze conjugate heat transfer processes in multi-domain fluid-solid systems Comprehensive Simulation Setup and Methodology Gain hands-on experience in configuring and executing a professional-grade CFD simulation for plate heat exchangers, covering all aspects from geometry creation to advanced thermal analysis. 1. Precise 2.5D Geometry and Advanced Mesh Generation - Create optimized 2.5D models of four-plate heat exchangers with integrated fluid domains using ANSYS Design Modeler - Implement unstructured meshing strategies with 5-layer inflation in fluid pipes using ANSYS Meshing - Optimize mesh quality for accurate flow and thermal simulations (5,096,686 elements) 2. ANSYS CFX Configuration for Conjugate Heat Transfer Simulation - Set up Thermal Energy model for comprehensive heat transfer analysis - Configure k-Epsilon turbulence model with Scalable Wall Function for accurate flow prediction - Implement High Resolution Advection Scheme and Turbulence Numerics for enhanced accuracy 3. Advanced Data Analysis and Visualization Techniques - Extract and interpret pressure, temperature, and velocity distributions in fluid domains - Analyze turbulence kinetic energy patterns and their impact on heat transfer efficiency - Evaluate temperature gradients and heat flux in solid plates Real-World Applications and Industry Relevance This tutorial is crucial for professionals and researchers in: HVAC system design and optimization Chemical process industry heat management Power plant thermal system engineering Food and beverage processing thermal control Key Simulation Outcomes and Engineering Insights 1. Conjugate Heat Transfer Analysis - Interpret the complex interplay between convection in fluids and conduction in solids - Understand the influence of fluid velocity on overall heat transfer rates 2. Flow Dynamics Evaluation - Analyze velocity patterns and pressure distributions within the pipe network - Assess the impact of pipe geometry on fluid flow and heat transfer efficiency 3. Performance Optimization - Evaluate the effectiveness of the heat exchanger design in achieving desired temperature changes - Understand the relationship between inlet conditions and overall system thermal performance Elevate Your CFD Skills in Thermal System Simulation By completing this specialized tutorial, you’ll gain: Cutting-edge skills in applying CFD to complex heat exchanger problems Proficiency in setting up and analyzing conjugate heat transfer simulations in ANSYS CFX Deep understanding of turbulence modeling and its impact on heat transfer predictions Insights into optimizing heat exchanger designs for improved efficiency and performance Who Should Take This Advanced Tutorial Thermal system engineers in HVAC and process industries Mechanical engineers specializing in heat transfer applications Energy system designers for power plants and industrial facilities Graduate students in mechanical or chemical engineering focusing on thermal management Don’t miss this opportunity to significantly advance your CFD simulation skills in thermal system analysis. Enroll now in our “ANSYS CFX: All Levels” course and master the art of simulating plate heat exchangers with ANSYS CFX!
Episode 1 1h 29m 15s
-
-
Section 3
Pond Overflow (Multi-Phase)
-
Master Pond Overflow CFD Simulation with ANSYS CFX Dive into the dynamic world of hydraulic engineering with our comprehensive tutorial on “Pond Overflow CFD Simulation” using ANSYS CFX. This pivotal episode in our “ANSYS CFX: All Levels” course offers an in-depth exploration of free-surface flow dynamics, essential for water resource engineers, hydraulic structure designers, and environmental scientists. Unlock Advanced CFD Techniques for Hydraulic Structure Analysis Learn to harness the power of ANSYS CFX to simulate and analyze complex water flow patterns in pond overflow systems. This tutorial provides a detailed approach to modeling multiphase flows and free-surface dynamics, crucial for optimizing hydraulic structures and water management systems. Key Learning Objectives: - Master the setup of 2.5D ogee spillway and pond models in ANSYS Design Modeler - Develop proficiency in structured mesh generation for complex hydraulic geometries - Understand the application of k-Epsilon turbulence models with Scalable Wall Functions - Analyze free-surface flow behavior and water level control in overflow systems Comprehensive Simulation Setup and Methodology Gain hands-on experience in configuring and executing a professional-grade CFD simulation for pond overflows, covering all aspects from geometry creation to advanced flow visualization. 1. Precise 2.5D Geometry and Structured Mesh Generation - Create optimized 2.5D models of ogee spillways and ponds using ANSYS Design Modeler - Implement structured meshing strategies with ANSYS Meshing - Optimize mesh quality for accurate free-surface flow simulations (55,418 elements) 2. ANSYS CFX Configuration for Multiphase Flow Simulation - Set up Homogeneous Multiphase model with standard Free Surface Model - Configure k-Epsilon turbulence model with Scalable Wall Function for accurate flow prediction - Implement High Resolution Advection Scheme and Turbulence Numerics for enhanced accuracy 3. Advanced Data Analysis and Visualization Techniques - Extract and interpret velocity, pressure, and volume fraction distributions - Analyze turbulence patterns and their impact on overflow performance - Evaluate water height and mass flow rate using volume fraction results Real-World Applications and Industry Relevance This tutorial is crucial for professionals and researchers in: Dam and reservoir engineering Flood control system design Stormwater management Environmental impact assessment of hydraulic structures Key Simulation Outcomes and Hydraulic Insights 1. Free-Surface Flow Analysis - Interpret the complex behavior of water flow over the ogee spillway - Understand the influence of spillway geometry on overflow characteristics 2. Flow Dynamics Evaluation - Analyze velocity patterns and pressure distributions in the overflow system - Assess the impact of spillway design on energy dissipation and flow control 3. Performance Quantification - Calculate water height and mass flow rate using volume fraction data - Evaluate the effectiveness of the overflow system in managing water levels Elevate Your CFD Skills in Hydraulic Engineering Simulation By completing this specialized tutorial, you’ll gain: Cutting-edge skills in applying CFD to complex hydraulic structure problems Proficiency in setting up and analyzing multiphase flow simulations in ANSYS CFX Deep understanding of free-surface flow dynamics and spillway hydraulics Insights into optimizing overflow designs for improved efficiency and safety Who Should Take This Advanced Tutorial Civil engineers specializing in hydraulic structures Water resource managers and hydrologists Environmental engineers focusing on water systems Graduate students in hydraulic engineering or water resources Don’t miss this opportunity to significantly advance your CFD simulation skills in hydraulic engineering. Enroll now in our “ANSYS CFX: All Levels” course and master the art of simulating pond overflows with ANSYS CFX!
Episode 1 1h 25m 51s
-
-
Section 4
Von Kármán
-
Master Von Kármán Effect Simulation with ANSYS CFX Delve into the fascinating world of fluid dynamics with our comprehensive tutorial on “Von Kármán Effect over Cylinder” using ANSYS CFX. This pivotal episode in our “ANSYS CFX: All Levels” course offers an in-depth exploration of vortex shedding phenomena, essential for aerospace engineers, mechanical designers, and fluid dynamics researchers. Unlock Advanced CFD Techniques for Complex Flow Analysis Learn to harness the power of ANSYS CFX to simulate and analyze the intricate Von Kármán vortex street behind a cylinder. This tutorial provides a detailed approach to modeling both steady and unsteady flow conditions, crucial for understanding fluid-structure interactions and optimizing designs in various engineering applications. Key Learning Objectives: - Master the setup of 2.5D cylinder models in ANSYS Design Modeler - Develop proficiency in advanced meshing techniques, including Body of Influence and inflation layers - Understand the application of Shear Stress Transport (k-ε SST) turbulence model - Analyze steady-state and transient flow behavior in vortex shedding scenarios Comprehensive Simulation Setup and Methodology Gain hands-on experience in configuring and executing professional-grade CFD simulations for vortex shedding, covering all aspects from geometry creation to advanced flow visualization. 1. Precise 2.5D Geometry and Advanced Mesh Generation - Create optimized 2.5D models of cylinders in flow domains using ANSYS Design Modeler - Implement tetrahedral meshing with Body of Influence for enhanced accuracy around the cylinder - Apply 10-layer inflation for boundary layer resolution, resulting in a high-quality mesh of 77,262 elements 2. ANSYS CFX Configuration for Steady and Transient Simulations - Set up both steady-state and transient simulations for comprehensive flow analysis - Configure Shear Stress Transport (k-ε SST) turbulence model for accurate vortex prediction - Implement High Resolution Advection Scheme and Second Order Backward Euler Transient Scheme 3. Advanced Data Analysis and Visualization Techniques - Extract and interpret velocity, pressure, and Turbulence Kinetic Energy distributions - Analyze vortex formation and shedding patterns using 2D contours, vectors, and streamlines - Evaluate periodic flow behavior through animated visualizations in CFD-Post Real-World Applications and Industry Relevance This tutorial is crucial for professionals and researchers in: Aerospace engineering for aircraft and spacecraft design Civil engineering for wind load analysis on structures Marine engineering for offshore structure design Energy sector for wind turbine optimization Key Simulation Outcomes and Fluid Dynamics Insights 1. Vortex Street Formation Analysis - Interpret the complex vortex shedding patterns behind the cylinder - Understand the influence of Reynolds number on vortex street characteristics 2. Flow Dynamics Evaluation - Analyze velocity patterns and pressure distributions around the cylinder - Assess the impact of vortex shedding on drag and lift forces 3. Transient Behavior Study - Evaluate the periodic nature of vortex shedding over time - Understand the implications of asymmetrical flow patterns on structural vibrations Elevate Your CFD Skills in Complex Flow Simulation By completing this specialized tutorial, you’ll gain: Cutting-edge skills in applying CFD to vortex shedding problems Proficiency in setting up and analyzing both steady and transient simulations in ANSYS CFX Deep understanding of turbulence modeling for external flows Insights into the effects of vortex shedding on engineering designs Who Should Take This Advanced Tutorial Aerospace engineers working on aircraft or spacecraft aerodynamics Mechanical engineers focusing on external flow problems Civil engineers analyzing wind effects on structures Graduate students in fluid dynamics or aerodynamics Don’t miss this opportunity to significantly advance your CFD simulation skills in complex flow analysis. Enroll now in our “ANSYS CFX: All Levels” course and master the art of simulating the Von Kármán effect with ANSYS CFX!
Episode 1 1h 14m 30s
-
-
Section 5
Porous Zone
-
Master 3D Porous Zone CFD Simulation with ANSYS CFX Dive into the intricate world of fluid dynamics through porous media with our comprehensive tutorial on “Porous Zone Inside 3D Channel” using ANSYS CFX. This essential episode in our “ANSYS CFX: All Levels” course offers an in-depth exploration of flow behavior through perforated plates, crucial for process engineers, chemical engineers, and fluid dynamics researchers. Unlock Advanced CFD Techniques for Porous Media Flow Analysis Learn to harness the power of ANSYS CFX to simulate and analyze complex fluid flow through porous zones in 3D channels. This tutorial provides a detailed approach to modeling pressure drop and velocity changes in porous media, essential for optimizing designs in various industrial applications. Key Learning Objectives: - Master the setup of 3D channel models with perforated plates in ANSYS Design Modeler - Develop proficiency in structured mesh generation for complex geometries - Understand the application of Shear Stress Transport (SST) turbulence model in porous media simulations - Analyze pressure drop and velocity changes through porous zones Comprehensive Simulation Setup and Methodology Gain hands-on experience in configuring and executing a professional-grade CFD simulation for porous media flow, covering all aspects from geometry creation to advanced flow visualization. 1. Precise 3D Geometry and Structured Mesh Generation - Create optimized 3D models of channels with perforated plates using ANSYS Design Modeler - Implement structured meshing strategies with ANSYS Meshing - Optimize mesh quality for accurate flow simulations (1,308,762 elements) 2. ANSYS CFX Configuration for Porous Media Simulation - Set up steady-state simulation with Isotropic Porous Model - Configure Shear Stress Transport (SST) turbulence model for accurate flow prediction - Implement High Resolution Advection Scheme and Turbulence Numerics for enhanced accuracy 3. Advanced Data Analysis and Visualization Techniques - Extract and interpret pressure and velocity distributions in 2D and 3D - Analyze flow behavior before, through, and after the porous zone - Evaluate the impact of porosity on pressure drop and velocity changes Real-World Applications and Industry Relevance This tutorial is crucial for professionals and researchers in: Chemical process engineering for reactor design Environmental engineering for filtration systems Petroleum engineering for reservoir simulations Biomedical engineering for tissue engineering applications Key Simulation Outcomes and Engineering Insights 1. Pressure Drop Analysis - Interpret the dramatic pressure change across the perforated plate - Understand the influence of porosity on overall system pressure loss 2. Velocity Profile Evaluation - Analyze velocity patterns before, through, and after the porous zone - Assess the impact of porous media on flow acceleration and deceleration 3. Performance Optimization - Evaluate the effectiveness of the perforated plate design in controlling flow - Understand the relationship between porous zone properties and flow characteristics Elevate Your CFD Skills in Porous Media Simulation By completing this specialized tutorial, you’ll gain: Cutting-edge skills in applying CFD to complex porous media problems Proficiency in setting up and analyzing 3D channel flows with porous zones in ANSYS CFX Deep understanding of pressure drop mechanisms in perforated plates Insights into optimizing porous media designs for improved flow control and efficiency Who Should Take This Advanced Tutorial Process engineers in chemical and petrochemical industries Environmental engineers working on filtration and separation systems Petroleum engineers studying reservoir flow dynamics Graduate students in chemical or mechanical engineering focusing on porous media flow Don’t miss this opportunity to significantly advance your CFD simulation skills in porous media analysis. Enroll now in our “ANSYS CFX: All Levels” course and master the art of simulating 3D channel flows with porous zones using ANSYS CFX!
Episode 1 1h 20m 27s
-
-
Section 6
Propeller (Steady-State)
-
Master Boat Propeller CFD Simulation with ANSYS CFX Dive into the dynamic world of marine propulsion with our comprehensive tutorial on “Boat Propeller, Steady State” using ANSYS CFX. This pivotal episode in our “ANSYS CFX: All Levels” course offers an in-depth exploration of rotational fluid dynamics, essential for marine engineers, naval architects, and propulsion system designers. Unlock Advanced CFD Techniques for Marine Propulsion Analysis Learn to harness the power of ANSYS CFX to simulate and analyze complex flow patterns around rotating boat propellers. This tutorial provides a detailed approach to modeling steady-state rotational flow, crucial for optimizing propeller designs and enhancing vessel performance. Key Learning Objectives: - Master the setup of 3D propeller models in SpaceClaim - Develop proficiency in tetrahedral mesh generation with inflation layers for rotating geometries - Understand the application of Shear Stress Transport (SST) turbulence model in propeller simulations - Analyze thrust generation and vortex formation in steady-state rotational flow Comprehensive Simulation Setup and Methodology Gain hands-on experience in configuring and executing a professional-grade CFD simulation for boat propellers, covering all aspects from geometry creation to advanced flow visualization. 1. Precise 3D Geometry and Advanced Mesh Generation - Create optimized 3D models of boat propellers using SpaceClaim - Implement tetrahedral meshing with 5-layer inflation for enhanced boundary layer resolution - Optimize mesh quality for accurate flow simulations (over 4 million elements across stationary and rotating zones) 2. ANSYS CFX Configuration for Rotational Flow Simulation - Set up steady-state simulation with rotating domain for the propeller zone - Configure Shear Stress Transport (SST) turbulence model for accurate flow prediction - Implement Frozen Rotor frame change model for interface handling 3. Advanced Data Analysis and Visualization Techniques - Extract and interpret velocity, pressure, and turbulence kinetic energy distributions - Analyze vortex formation and thrust generation using 2D contours, vectors, and streamlines - Evaluate propeller performance through pressure distribution visualization Real-World Applications and Industry Relevance This tutorial is crucial for professionals and researchers in: Marine engineering and naval architecture Offshore industry propulsion system design Recreational boat manufacturing Underwater vehicle propulsion optimization Key Simulation Outcomes and Propulsion Insights 1. Thrust Generation Analysis - Interpret the complex pressure distribution on propeller blades - Understand the mechanism of thrust production in rotating propellers 2. Flow Dynamics Evaluation - Analyze velocity patterns and vortex formation behind the propeller - Assess the impact of blade design on water displacement and thrust efficiency 3. Performance Optimization - Evaluate the effectiveness of the propeller design in generating thrust - Understand the relationship between rotational speed and flow characteristics Elevate Your CFD Skills in Marine Propulsion Simulation By completing this specialized tutorial, you’ll gain: Cutting-edge skills in applying CFD to complex rotational flow problems Proficiency in setting up and analyzing steady-state propeller simulations in ANSYS CFX Deep understanding of thrust generation mechanisms in marine propellers Insights into optimizing propeller designs for improved efficiency and performance Who Should Take This Advanced Tutorial Marine engineers specializing in propulsion systems Naval architects working on vessel design optimization Mechanical engineers focusing on rotating machinery Graduate students in marine engineering or fluid dynamics Don’t miss this opportunity to significantly advance your CFD simulation skills in marine propulsion analysis. Enroll now in our “ANSYS CFX: All Levels” course and master the art of simulating boat propellers with ANSYS CFX!
Episode 1 1h 41m 12s
-
-
Section 7
Propeller (Transient)
-
Master Transient Boat Propeller Simulation with ANSYS CFX Delve into the dynamic world of marine propulsion with our advanced tutorial on “Boat Propeller Transient Solution” using ANSYS CFX. This crucial episode in our “ANSYS CFX: All Levels” course offers an in-depth exploration of time-dependent rotational fluid dynamics, essential for marine engineers, naval architects, and propulsion system designers seeking to optimize performance and efficiency. Unlock Cutting-Edge CFD Techniques for Time-Accurate Propulsion Analysis Learn to harness the full power of ANSYS CFX to simulate and analyze complex, time-dependent flow patterns around rotating boat propellers. This tutorial provides a comprehensive approach to modeling transient rotational flow, crucial for understanding the nuanced behavior of propeller systems and enhancing vessel performance over time. Key Learning Objectives: - Master the setup of 3D propeller models in SpaceClaim for transient analysis - Develop proficiency in high-quality tetrahedral mesh generation with inflation layers for rotating geometries - Understand the application of Shear Stress Transport (SST) turbulence model in time-dependent propeller simulations - Analyze thrust generation, vortex formation, and flow evolution in transient rotational flow Comprehensive Transient Simulation Setup and Methodology Gain hands-on experience in configuring and executing a professional-grade transient CFD simulation for boat propellers, covering all aspects from geometry creation to advanced time-dependent flow visualization. 1. Precise 3D Geometry and Advanced Mesh Generation - Create optimized 3D models of boat propellers using SpaceClaim for transient analysis - Implement tetrahedral meshing with 5-layer inflation for enhanced boundary layer resolution over time - Optimize mesh quality for accurate flow simulations (over 4 million elements across stationary and rotating zones) 2. ANSYS CFX Configuration for Transient Rotational Flow Simulation - Set up time-dependent simulation with rotating domain for the propeller zone - Configure Shear Stress Transport (SST) turbulence model for accurate transient flow prediction - Implement Transient Rotor Stator model for interface handling between rotating and stationary zones 3. Advanced Transient Data Analysis and Visualization Techniques - Extract and interpret time-varying velocity, pressure, and turbulence kinetic energy distributions - Analyze vortex formation and thrust generation evolution using 2D contours, vectors, and streamlines - Evaluate propeller performance through time-dependent pressure distribution visualization Real-World Applications and Industry Relevance This advanced tutorial is crucial for professionals and researchers in: Marine engineering and naval architecture focusing on dynamic propulsion systems Offshore industry propulsion system design for varying operational conditions High-performance boat manufacturing requiring precise thrust control Underwater vehicle propulsion optimization for complex maneuvers Key Transient Simulation Outcomes and Propulsion Insights 1. Time-Dependent Thrust Generation Analysis - Interpret the evolving pressure distribution on propeller blades over time - Understand the mechanism of thrust production and fluctuation in rotating propellers 2. Dynamic Flow Evaluation - Analyze time-varying velocity patterns and vortex formation behind the propeller - Assess the impact of blade design on water displacement and thrust efficiency throughout the rotation cycle 3. Transient Performance Optimization - Evaluate the effectiveness of the propeller design in generating consistent thrust over time - Understand the relationship between rotational speed and time-dependent flow characteristics Elevate Your CFD Skills in Advanced Marine Propulsion Simulation By completing this specialized tutorial, you’ll gain: Cutting-edge skills in applying transient CFD to complex rotational flow problems Proficiency in setting up and analyzing time-dependent propeller simulations in ANSYS CFX Deep understanding of dynamic thrust generation mechanisms in marine propellers Insights into optimizing propeller designs for improved efficiency and performance across various operational scenarios Who Should Take This Advanced Tutorial Experienced marine engineers specializing in dynamic propulsion systems Naval architects working on advanced vessel design optimization CFD specialists focusing on time-dependent rotating machinery Graduate students and researchers in marine engineering or fluid dynamics pursuing cutting-edge propulsion analysis Don’t miss this opportunity to significantly advance your CFD simulation skills in advanced marine propulsion analysis. Enroll now in our “ANSYS CFX: All Levels” course and master the art of simulating transient boat propeller dynamics with ANSYS CFX!
Episode 1 1h 44m 8s
-
-
Section 8
Bullet (Dynamic Mesh / Compressible Flow)
-
Master High-Speed Aerodynamics: AK-47 Bullet CFD Simulation with ANSYS CFX Dive into the cutting-edge world of supersonic flow dynamics with our advanced tutorial on “AK-47 Bullet CFD Simulation” using ANSYS CFX. This pivotal episode in our “ANSYS CFX: All Levels” course offers an in-depth exploration of compressible flow and shock wave formation, essential for ballistics experts, aerospace engineers, and advanced CFD practitioners. Unlock Advanced CFD Techniques for Supersonic Flow Analysis Learn to harness the full power of ANSYS CFX to simulate and analyze complex, high-speed flow patterns around an AK-47 bullet. This tutorial provides a comprehensive approach to modeling compressible flow and shock wave phenomena, crucial for understanding ballistic performance and aerodynamic behavior in supersonic regimes. Key Learning Objectives: - Master the setup of 3D bullet models in SpaceClaim for high-speed simulations - Develop proficiency in unstructured mesh generation for complex geometries in supersonic flow - Understand the application of High Speed (Compressible) Wall Heat Transfer Model - Analyze shock wave formation, pressure distribution, and temperature variations in supersonic flow Comprehensive Simulation Setup and Methodology Gain hands-on experience in configuring and executing a professional-grade CFD simulation for supersonic projectiles, covering all aspects from geometry creation to advanced flow visualization. 1. Precise 3D Geometry and Advanced Mesh Generation - Create optimized 3D models of AK-47 bullets using SpaceClaim - Implement unstructured triangular meshing strategies with ANSYS Meshing - Optimize mesh quality for accurate supersonic flow simulations (3,236,698 elements) 2. ANSYS CFX Configuration for Compressible Flow Simulation - Set up High Speed (Compressible) Wall Heat Transfer Model for accurate shock wave prediction - Configure Ideal Air Gas material properties to model air compressibility at Mach 2.04082 - Implement advanced numerical schemes for stable supersonic flow calculations 3. Advanced Data Analysis and Visualization Techniques - Extract and interpret pressure, temperature, and velocity distributions in supersonic flow - Analyze shock wave formation and propagation using 2D contours - Evaluate bullet aerodynamics through surface pressure distribution visualization Real-World Applications and Industry Relevance This advanced tutorial is crucial for professionals and researchers in: Ballistics and weapon system design Aerospace engineering for supersonic and hypersonic vehicle development Defense industry R&D for projectile optimization Academic research in high-speed aerodynamics and compressible flow Key Simulation Outcomes and Aerodynamic Insights 1. Shock Wave Analysis - Interpret the complex shock wave patterns around the supersonic bullet - Understand the formation and propagation of shock waves in compressible flow 2. Thermodynamic Evaluation - Analyze temperature and pressure variations in the flow field - Assess the impact of supersonic flight on the bullet's surface conditions 3. Performance Characterization - Evaluate the aerodynamic efficiency of the bullet design at supersonic speeds - Understand the relationship between bullet geometry and shock wave formation Elevate Your CFD Skills in High-Speed Flow Simulation By completing this specialized tutorial, you’ll gain: Cutting-edge skills in applying CFD to complex supersonic flow problems Proficiency in setting up and analyzing compressible flow simulations in ANSYS CFX Deep understanding of shock wave physics and their impact on projectile performance Insights into optimizing designs for improved aerodynamic efficiency in supersonic regimes Who Should Take This Advanced Tutorial Ballistics engineers and weapon system designers Aerospace engineers working on supersonic and hypersonic projects CFD specialists focusing on high-speed compressible flows Graduate students and researchers in aerodynamics or computational fluid dynamics Don’t miss this opportunity to significantly advance your CFD simulation skills in high-speed aerodynamics. Enroll now in our “ANSYS CFX: All Levels” course and master the art of simulating supersonic projectile dynamics with ANSYS CFX!
Episode 1 1h 13m 21s
-
-
Section 9
Combustion Chamber
-
Master Combustion Chamber CFD Simulation with ANSYS CFX Delve into the complex world of combustion dynamics with our comprehensive tutorial on “Combustion Chamber CFD Simulation” using ANSYS CFX. This pivotal episode in our “ANSYS CFX: All Levels” course offers an in-depth exploration of reactive flow modeling, essential for combustion engineers, thermal system designers, and advanced CFD practitioners. Unlock Advanced CFD Techniques for Combustion Analysis Learn to harness the full power of ANSYS CFX to simulate and analyze intricate combustion processes within a cylindrical chamber. This tutorial provides a detailed approach to modeling fuel-air mixing, chemical reactions, and heat transfer, crucial for optimizing combustion systems and enhancing energy efficiency. Key Learning Objectives: - Master the setup of 3D combustion chamber models in SpaceClaim - Develop proficiency in mesh generation for reactive flow simulations - Understand the application of Eddy Dissipation combustion models - Analyze temperature distribution, pressure variations, and species concentration in combustion processes Comprehensive Simulation Setup and Methodology Gain hands-on experience in configuring and executing a professional-grade CFD simulation for combustion chambers, covering all aspects from geometry creation to advanced flow and reaction visualization. 1. Precise 3D Geometry and Advanced Mesh Generation - Create optimized 3D models of cylindrical combustion chambers using SpaceClaim - Implement effective meshing strategies with ANSYS Meshing for accurate combustion modeling - Optimize mesh quality for complex reactive flows (1,147,748 elements) 2. ANSYS CFX Configuration for Combustion Simulation - Set up Eddy Dissipation combustion model for ethane-air reactions - Configure Thermal Energy model for heat transfer and Scalable K-Epsilon for turbulence - Implement appropriate numerical schemes for stable combustion calculations 3. Advanced Data Analysis and Visualization Techniques - Extract and interpret temperature, pressure, and velocity distributions in the combustion chamber - Analyze species concentration and reaction progress using 2D contours and volume rendering - Evaluate combustion efficiency through flow pattern visualization and product formation Real-World Applications and Industry Relevance This advanced tutorial is crucial for professionals and researchers in: Power generation and energy systems Aerospace propulsion system design Automotive engine development Industrial furnace and boiler optimization Key Simulation Outcomes and Combustion Insights 1. Reaction Dynamics Analysis - Interpret the complex mixing and reaction patterns of ethane and air - Understand the formation and distribution of combustion products 2. Thermal Performance Evaluation - Analyze temperature variations and heat transfer within the combustion chamber - Assess the impact of fuel injection and air inlet conditions on combustion efficiency 3. Flow Characterization - Evaluate the velocity and pressure distributions throughout the chamber - Understand the relationship between flow patterns and combustion stability Elevate Your CFD Skills in Combustion System Simulation By completing this specialized tutorial, you’ll gain: Cutting-edge skills in applying CFD to complex reactive flow problems Proficiency in setting up and analyzing combustion simulations in ANSYS CFX Deep understanding of the interplay between fluid dynamics and chemical kinetics in combustion processes Insights into optimizing combustion chamber designs for improved efficiency and reduced emissions Who Should Take This Advanced Tutorial Combustion engineers in power generation and propulsion industries Thermal system designers working on furnaces and boilers CFD specialists focusing on reactive flows and heat transfer Graduate students and researchers in combustion science and engineering Don’t miss this opportunity to significantly advance your CFD simulation skills in combustion analysis. Enroll now in our “ANSYS CFX: All Levels” course and master the art of simulating complex combustion processes with ANSYS CFX!
Episode 1 1h 24m 8s
-
-
Section 10
Particle Transport
-
Master Particle Transport Simulation in Bent Pipes with ANSYS CFX Dive into the intricate world of multiphase flow dynamics with our comprehensive tutorial on “Particle Transport in Bent Pipe” using ANSYS CFX. This essential episode in our “ANSYS CFX: All Levels” course offers an in-depth exploration of particle-fluid interactions, crucial for engineers in various industries dealing with particle-laden flows. Unlock Advanced CFD Techniques for Multiphase Flow Analysis Learn to harness the power of ANSYS CFX to simulate and analyze complex particle transport phenomena in bent pipes. This tutorial provides a detailed approach to modeling particle-fluid interactions, essential for optimizing pipeline designs, preventing erosion, and enhancing overall system efficiency. Key Learning Objectives: - Master the setup of 3D bent pipe models in SpaceClaim for particle transport simulations - Develop proficiency in unstructured mesh generation for complex geometries with multiphase flow - Understand the application of Fully Coupled Particle Transport Fluid Morphology - Analyze particle distribution, pressure drop, and flow patterns in bent pipes Comprehensive Simulation Setup and Methodology Gain hands-on experience in configuring and executing a professional-grade CFD simulation for particle transport in bent pipes, covering all aspects from geometry creation to advanced flow visualization. 1. Precise 3D Geometry and Advanced Mesh Generation - Create optimized 3D models of bent pipes using SpaceClaim - Implement unstructured meshing strategies with ANSYS Meshing for accurate multiphase flow simulation - Optimize mesh quality for complex geometries (139,461 elements) 2. ANSYS CFX Configuration for Particle Transport Simulation - Set up Fully Coupled Particle Transport Fluid Morphology for accurate particle-fluid interaction modeling - Configure Scalable k-Epsilon turbulence model for robust flow prediction - Implement High Resolution schemes for Advection and Turbulence Numerics 3. Advanced Data Analysis and Visualization Techniques - Extract and interpret velocity, pressure, and turbulence kinetic energy distributions - Analyze particle volume fraction to understand particle distribution and accumulation - Evaluate flow patterns and vortex formation using streamlines and vector plots Real-World Applications and Industry Relevance This tutorial is crucial for professionals and researchers in: Oil and gas pipeline engineering Chemical process industry Water treatment and distribution systems Pneumatic conveying systems design Key Simulation Outcomes and Engineering Insights 1. Particle Distribution Analysis - Interpret the complex patterns of particle distribution throughout the bent pipe - Understand the mechanisms of particle accumulation and potential erosion hotspots 2. Flow Dynamics Evaluation - Analyze velocity patterns and vortex formation in the bent section - Assess the impact of pipe geometry on pressure drop and flow characteristics 3. Performance Optimization - Evaluate the effectiveness of the pipe design in transporting particles - Understand the relationship between flow conditions and particle behavior Elevate Your CFD Skills in Multiphase Flow Simulation By completing this specialized tutorial, you’ll gain: Cutting-edge skills in applying CFD to complex particle transport problems Proficiency in setting up and analyzing multiphase flow simulations in ANSYS CFX Deep understanding of particle-fluid interaction mechanisms in bent pipes Insights into optimizing pipe designs for improved particle transport and reduced erosion Who Should Take This Advanced Tutorial Pipeline engineers in oil, gas, and chemical industries Process engineers dealing with particle-laden flows CFD specialists focusing on multiphase flow simulations Graduate students in chemical or mechanical engineering studying multiphase flows Don’t miss this opportunity to significantly advance your CFD simulation skills in particle transport analysis. Enroll now in our “ANSYS CFX: All Levels” course and master the art of simulating particle transport in bent pipes using ANSYS CFX!
Episode 1 1h 24m 23s
-
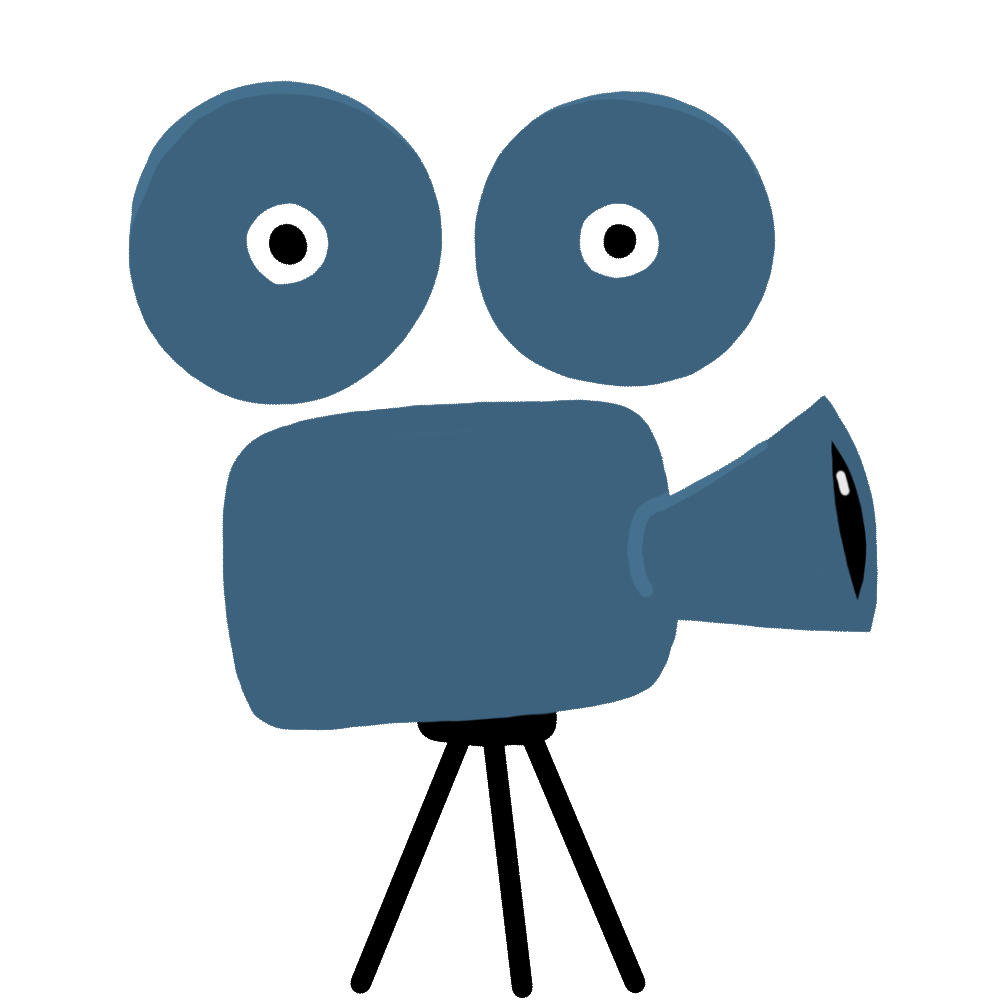
Course In Progress
Course still in development. Check back often for updates.
Master CFD with ANSYS CFX: Comprehensive All-Levels Training Course
Unlock the power of computational fluid dynamics with our “ANSYS CFX: All Levels” course. This comprehensive training package is designed to elevate your CFD skills, whether you’re a beginner or an experienced engineer looking to refine your expertise.
Dive Deep into ANSYS CFX with 10 Practical Tutorials
Our course offers a unique blend of theoretical knowledge and hands-on experience through 10 carefully crafted tutorials. Each project is designed to tackle real-world engineering challenges, ensuring you gain practical skills applicable to your professional endeavors.
What You'll Learn:
- Fundamentals of CFD modeling - ANSYS Meshing techniques for complex geometries - CFX setup for various flow scenarios - Post-processing and result interpretation using CFD-Post - Advanced concepts like turbulence modeling and multiphase flows
Comprehensive Curriculum Covering Diverse Applications
Our tutorial lineup includes:
- Storage Tank CFD Simulation
- Plate Heat Exchanger Analysis
- Pond Overflow Dynamics
- Von Kármán Effect over Cylinder
- Porous Zone Modeling in 3D Channels
- Boat Propeller Performance (Steady-State)
- Transient Boat Propeller Analysis
- High-Speed AK-47 Bullet Aerodynamics
- Combustion Chamber Optimization
- Particle Transport in Bent Pipes
Interactive Learning Experience
Each tutorial features:
- Step-by-step guides for easy navigation
- Interactive elements to enhance engagement
- Practical tips for efficient simulation setup
- Insights into result analysis and interpretation
From Basics to Advanced Applications
For Beginners:
- Grasp fundamental CFD concepts - Learn essential ANSYS CFX workflows - Build confidence in setting up basic simulations
For Experienced Users:
- Explore advanced turbulence models - Master complex multiphase flow simulations - Optimize your CFD workflow for efficiency
Industry-Relevant Skills and Knowledge
Upon completion, you’ll be equipped to:
- Set up and run sophisticated CFD simulations
- Analyze a wide range of fluid mechanics problems
- Apply CFD techniques to real-world engineering challenges
- Interpret and present simulation results effectively
Why Choose Our ANSYS CFX Course?
- Comprehensive coverage of ANSYS CFX capabilities
- Practical, industry-relevant projects
- Flexible learning with full access to simulation files
- Expert-designed curriculum for all skill levels
Elevate your CFD skills and unlock new career opportunities. Enroll in our “ANSYS CFX: All Levels” course today and transform your approach to fluid dynamics simulation!
Buy Course
Benefits of buying the whole course
- Complete access to chapters Without Price
- Special discount
- Unlimited access to course content
- Free access to all new and updated content
- Access to course forever without any additional payment
* You can select chapters seperately, but you won't benefit from the list above.
* The items that do not have a price cannot be bought separately and are only available when you buy the whole course.
Congratulations
Congratulations! Your purchase was successful.
You can now start learning the course by clicking the button "Start Learning".
Add Payment Method
Please enter your payment method details.