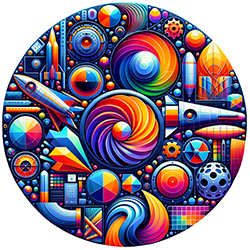
CFD Simulation Projects by ANSYS Fluent
Workshop Price: Free
Due to the contribution of numerical simulation towards analysis in engineering, learning ANSYS Fluent is critical in solving heat and mechanical problems. ANSYS Fluent learning is appropriate for beginners and intermediate learners and covers 39 simulation exercises with varied content on heat transfer, aerodynamics, multiphase flows, and compressible flows. This course introduces you to geometry modeling using Design Modeler and Space Claim, meshing using ANSYS Meshing, and varied options for setups in Fluent. By the end of the course, you will learn to extract results, analyze data, and produce contours and varied plots in CFD-Post so that you can conduct advanced numerical simulations professionally.
Flow Behavior Passing Through a Porous Medium, CFD Approach
Overview of Fluid Flow in Porous Media Simulation Project Description Aiming to grasp fluid dynamics via various porosities, this work uses ANSYS Fluent to look at fluid behaviour inside porous media. Industries include food, oil, textiles, and filtration are common with porous materials. Methodology Geometry and Meshing: The model is made up of an upstream flow domain, a porous medium domain, and a downstream flow domain. The model, which has a structured mesh of 35,017 components, was created in ANSYS Design Modeller and meshed in ANSYS Meshing. Porous Medium Definition: A porosity coefficient defines the porous media; it is the ratio of void space to whole space. Three porosities—0.5, 0.7, and 0.9—are examined to evaluate their influence on fluid flow. Conclusion The simulation findings produce contours of static pressure drop, turbulent viscosity, velocity, and pressure. Pressure and Flow Dynamics: A pressure drop is seen as fluid moves through the porous medium, hence verifying the porous material's function in lowering fluid pressure. Comparative Analysis: Different porosities show different pressure drops, hence stressing the effect of porosity on fluid behaviour. This paper shows how porous media change the properties of fluid flow, hence providing ideas for use in many sectors.
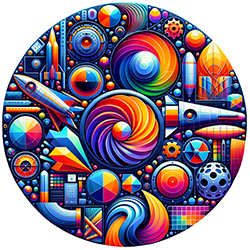
CFD Simulation Projects by ANSYS Fluent
Workshop Price: Free
Due to the contribution of numerical simulation towards analysis in engineering, learning ANSYS Fluent is critical in solving heat and mechanical problems. ANSYS Fluent learning is appropriate for beginners and intermediate learners and covers 39 simulation exercises with varied content on heat transfer, aerodynamics, multiphase flows, and compressible flows. This course introduces you to geometry modeling using Design Modeler and Space Claim, meshing using ANSYS Meshing, and varied options for setups in Fluent. By the end of the course, you will learn to extract results, analyze data, and produce contours and varied plots in CFD-Post so that you can conduct advanced numerical simulations professionally.
Flow Behavior Passing Through a Porous Medium, CFD Approach
Overview of Fluid Flow in Porous Media Simulation Project Description Aiming to grasp fluid dynamics via various porosities, this work uses ANSYS Fluent to look at fluid behaviour inside porous media. Industries include food, oil, textiles, and filtration are common with porous materials. Methodology Geometry and Meshing: The model is made up of an upstream flow domain, a porous medium domain, and a downstream flow domain. The model, which has a structured mesh of 35,017 components, was created in ANSYS Design Modeller and meshed in ANSYS Meshing. Porous Medium Definition: A porosity coefficient defines the porous media; it is the ratio of void space to whole space. Three porosities—0.5, 0.7, and 0.9—are examined to evaluate their influence on fluid flow. Conclusion The simulation findings produce contours of static pressure drop, turbulent viscosity, velocity, and pressure. Pressure and Flow Dynamics: A pressure drop is seen as fluid moves through the porous medium, hence verifying the porous material's function in lowering fluid pressure. Comparative Analysis: Different porosities show different pressure drops, hence stressing the effect of porosity on fluid behaviour. This paper shows how porous media change the properties of fluid flow, hence providing ideas for use in many sectors.
-
Section 1
Forced Convection
-
Forced Convection Heat Transfer in an U-Bend Using ANSYS Fluent: CFD Simulation Statement This work uses ANSYS Fluent to replicate forced convection heat transfer in an U-Bend pipe with applied heat flux on its outer sides. With water as the working fluid, the main emphasis is on knowing heat transfer dynamics in a laminar flow regime. Geometry: Made in ANSys Design Modeler, the 3D model shows a 13 mm diameter pipe. Plates with 70 mm diameter holes are set in the bend at an axial spacing of 20 mm and a transverse distance of 16 mm. Mesh: ANSYS Meshing generates 2,595,714 unstructured mesh using To further simulation fidelity, the mesh is then changed in ANSYS Fluent to a polyhedral mesh. Methodology Flow Conditions: With water entering the domain at 0.0158 m/s, laminar flow regime results. The viscous model is laminar. Heat Transfer Setup: The exterior wall of the pipe is subjected to an external heat flow of 32,087 W/m². The energy equation is set up to record temperature fluctuations brought on by forced convection. Results and Analysis Different contours and coefficients are obtained when finishing the simulation, which helps one understand the fluid and thermal behaviour inside the U-Bend: Temperature, Velocity, and Pressure Contours: These forms show efficient fluid dynamics and heat transport inside the U-Bend. Heat Transfer Coefficients: Computed to be 220.9961, the local heat transfer coefficient has an average Nusselt number of 25.78288. Pressure Drop and Friction Factor: Determined are a friction factor of 0.35 and a pressure drop of 2.15, so suggesting flow resistance properties. The applicability of forced convection ideas in heat transfer inside complicated geometries is convincingly shown by the simulation. Design and optimization of thermal systems including fluid flow through bends and convoluted paths depends on this knowledge. Please reach out for further information or project help!
Episode 1 20m 58s Free Episode -
Thermal Analysis in a Storage Tank: ANSYS Fluent Based CFD Simulation Understanding Storage Tank Thermal Dynamics Crucially significant components in many different industrial applications, storage tanks hold liquids under various temperature conditions. This large-scale CFD simulation explores the thermal behavior inside a square-shaped storage tank having two inlets and a single exit with specific focus on temperature control capacities. Geometric Configuration and Model Guidelines The simulation makes use of a 2D square domain with following main width: Tank height: 2 meters Inlet diameters: 0.2 meters (two inlets) Outlet diameter: 0.3 meters (positioned at the top) Design software: ANSYS Design Modeler Generation of Mesh and Computational Framework Features of the computational domain include: Mesh type: Structured elements Element count: 10,056 Meshing software: ANSYS Meshing Solver Settings and Simulating Methodology The work uses specific computing environments: Pressure-based solver type (considering fluid incompressibility) in accounting Time dependence: steady-state modeling Focus of the analysis: fluid mixing patterns and thermal behavior Results and Thermal Performance Analysis Insights Combining Dynamics and Flow Patterns The simulation creates exhaustive two-dimensional visualizations of: Pressure distribution Temperature gradients Turbulence kinetic energy Velocity vectors Thermal Mixing Behavior The results show how twin inlet flows converge toward the central outlet to produce a mixing zone that greatly affects both temperature distribution and velocity profiles all across the tank. The characteristics of the exit temperature depend considerably on this mixing phenomena. Engineering Applications For maximizing storage tank designs in purposes requiring accurate temperature control, this thermal analysis provides relevant information including: Systems of industrial process heating and cooling. Facilities for storage of thermal energy Systems for water heating Chemical processing tanks
Episode 2 17m 16s Free Episode -
Comprehension of Cylindrical Heat Source Simulation Project Overview Using ANSYS Fluent software, this simulation looks at the steady heating process of airflow inside a cylindrical form. Aiming to study the thermal behavior and flow dynamics in the presence of a volumetric heat source by means of comprehensive CFD analysis. Geometry and Meshing Model Design Using Design Modeler software, the geometry of the model is meticulously developed, stressing correct representation of the cylindrical configuration. Meshing Details Using ANSYS Meshing tool, the model is meshed using an unstructured mesh of 1,600,000 cells to guarantee resolution of important thermal and flow characteristics. Cylindrical Heat Source Methodology Heat Source Definition The simulation uses cell zone condition to build a cylindrical heat source. This heat source represents a constant volumetric heat generation rate of 252,972 W/m³ from the solid aluminum cylinder, continuously distributed across the domain. Results and Conclusion Simulation Outcomes At the end of the simulation, contour plots for temperature, velocity, and pressure are generated. Attributed to the reduced cross-sectional flow area, the entrance average of 0.00878484 m/s to the outflow of 0.0353417 m/s shows an increase in velocity. Thermal Analysis Corresponding to a computed heat transfer rate of 3.4 W/m², the air temperature moves from 300 K at the entrance to 1758 K at the outlet. A temperature profile along the axial direction also shows a gradual rise in fluid temperature, with the most notable increase close to the model's start areas, hence stressing areas of maximum thermal activity.
Episode 3 14m 34s Free Episode -
Rough Surface Heat Transfer CFD Simulation with ANSYS Fluent Project Description Using ANSYS Fluent, investigate the heat transport mechanism on a rough surface with serrated fringes. Using a laminar model to solve fluid flow equations, this work looks at how surface roughness influences heat transfer efficiency in low Reynolds number conditions; the energy model is used for temperature distribution computations. Geometry and Meshing Design and Mesh: ANSYS Design Modeller builds the geometry; ANSYS Meshing software meshes it. For thorough investigation, the structured mesh has 102,694 components. CFD Simulation Settings Key Assumptions: Results free of time define steady-state simulation. Gravity influence in the Y direction is -9.81 m/s². Models and Boundary Conditions: Viscous Model: Laminar Energy Model: Activated Inlet: Velocity of 0.0134 m/s at 300 K Outlet: Pressure outlet with 0 Pa gauge pressure Walls: Stationary, with a heat flux of 1000 W/m² Solution Methods: Pressure-Velocity Coupling: SIMPLE Spatial Discretization: Second order for energy, momentum, and pressure Initialization: Standard approach at 300 K temperature and a speed of (0.0134, 0, 0) m/s Results and Discussion Temperature Contours: Indicate a rise in fluid temperature after passing the serrated fringes on the lower wall, changing the flow regime from laminar to turbulent and improving total heat transfer. Velocity and Streamline Analysis:Show vortex creation after fringes to show the shift to turbulence, which raises the heat transfer coefficient over that of laminar flow. By use of this simulation, one may see how surface roughness affects heat transmission and fluid movement, hence providing ideas for design optimisation to improve thermal performance.
Episode 4 13m 35s Free Episode -
Heat Transfer in Pipe with Twisted Tape Inserts: CFD Validation Using ANSYS Fluent Project Overview Using ANSYS Fluent, this project models heat transmission in a pipe with a twisted tape. The goal is to confirm and duplicate findings from the reference paper "Analysis of Heat Transfer in Pipe with Twisted Tape Inserts." Geometry and Meshing Model Design: Comprising a twisted tape with a screw pitch of 0.110 m (pitch-to-diameter ratio of 5), a 3D tube measuring 0.022 m in diameter and 2.2 m in length. Meshing: Created in ANSYS Meshing, unstructured mesh with 476,442 components. Methodology Fluid Dynamics: Fluid: Water Reynolds Number: 800 Velocity: 0.0365 m/s Inlet Temperature: 298.15 K Boundary Conditions: Pipe Wall: Constant heat flux of 5725 W/m² Twisted Tape: Thermally insulated, influencing heat transfer efficiency Results and Conclusion Understanding heat transfer efficiency depends on the Nusselt number on the pipe wall, hence the main emphasis is Under the identical circumstances, the simulation produces a Nusselt number of 25.737018, which nearly corresponds to the figure of 24.78 from the reference study. Validation: A comparison table for P/D=5 and Re=800 helps to check the findings against the reference publication. Visualizations: To show the flow and heat transfer dynamics, 3D contours of pressure, temperature, velocity, and pathlines are produced. By means of twisted tape inserts, this work clearly shows their impact on heat transport in pipes, hence offering insights useful for enhancing thermal management systems.
Episode 5 16m 15s Free Episode -
Overview of CFD Simulation of Heat Transfer Over Serrated Finned Tube Project Description Using ANSYS Fluent software, this project simulates the cooling process of a serrated finned tube. The simulation is evaluated against the findings of a reference paper called "A characteristic correlation for heat transfer over serrated finned tubes." Model Design Designed in Design Modeller, the 3D model features a tube encircled by steel fins. At 313.15 K, the wind interacts with the fins to promote heat transfer. A structured mesh comprising 356,240 components built in ANSYS Meshing is used in the simulation. Methodology A symmetric border condition simulates a segment of the tube. The inner wall temperature is steady at 473.15 K. The Nusselt number is used to examine cooling rates at various Reynolds numbers. Results and Conclusion We computed the Nusselt number on the tube wall and compared it to reference values for Reynolds numbers 2000, 5000, and 10000. The simulation also offers 2D temperature, velocity, and pressure contours.
Episode 6 16m 36s Free Episode -
Overview of CFD Simulation of Laminar Flow and Heat Transfer in a U-Bend Project Description Validated against the paper "Laminar flow and heat transfer in U-bends: The effect of secondary flows in ducts with partial and full curvature," this ANSYS Fluent simulation models laminar flow through a U-shaped tube. Model Design The fluid, therminol, has particular characteristics: density of 793.9 kg/m³, specific heat capacity of 2315 J/kg·K, thermal conductivity of 0.116 W/m·K, and viscosity of 0.00173 kg/m·s. With an inlet speed of 0.21791 m/s, the simulation runs at a Reynolds number of 1000. Designed in Design Modeller, the U-bend model has a pipe diameter of 0.01 m and a bend radius of 0.015 m. There are 2,268,000 components in the structured mesh. Methodology A constant heat flux of 1156 W/m²·K is applied as the thermal boundary condition on the pipe wall to analyze fluid behavior and heat transfer through the U-bend. Results and Conclusion Validated against Figure 14-b of the reference paper, the simulation seeks to confirm fluid temperature variations along the inner wall of the pipe. A graph of dimensionless position versus dimensionless temperature backs this confirmation. The Nusselt number is also evaluated at P1 to P5 along the bend; ratios are computed in relation to section P1. These results are contrasted with dimensionless Nusselt numbers in Figure 19-b of the paper.
Episode 7 17m 51s Free Episode -
Description This comprehensive course covers the basics of geometry generation using Design Modeler and explores advanced meshing techniques with ANSYS Meshing. A detailed setup produces 2268000 elements, ensuring a robust and accurate model for analysis.
Episode 8 25m 26s Free Episode -
Comprehension of CFD Simulation of Mountain External Airflow Considering Heat Transfer Project Description This study analyses airflow and heat transmission across a mountain terrain, crucial for understanding air passageways for aeroplanes. The simulation is conducted using ANSYS Fluent. Model Design Designed in ANSYS Design Modeller, the computational domain consists of three distinct pressure outlets, the mountain, and an airflow intake. The geometry is covered by an unstructured mesh of 1,250,044 parts. Methodology Air enters the domain at a speed of 8 m/s and a temperature of 297.5 K. To take heat transfer into account, the Energy model is activated. The k-epsilon Standard model is used to examine the turbulent flow dynamics since it is expected that flow separation and vortex creation will occur. Conclusion Using 16-time steps and a step size of 7 seconds, the simulation is transitory. Results show contours of pressure, velocity, temperature, streamlines, and velocity vectors, so illuminating the flow behaviour around the mountain.
Episode 9 13m 42s Free Episode -
Project Description Using ANSYS Fluent, this paper models the heat transmission of water flow through a zigzag channel. With angles set at 15 degrees in the first model and 45 degrees in the second, the channel has ten zigzag bends. At a Reynolds number of 107, the flow is laminar. Exiting at atmospheric pressure, water enters the channel with a temperature of 393.15 K and a speed of 0.0334 m/s. While the upper wall keeps a steady temperature of 276.65 K, the lower wall of the channel is insulated. Geometry & Mesh Using Spaceclaim, the 2D model shows a zigzag pattern with ten turns. Two versions are modelled: one with a 15-degree and the other with a 45-degree slant. Using a structured mesh with 48,000 components, ANSYS Meshing does meshing. CFD Simulation Key assumptions for the simulation include: Pressure-based solver Steady state Neglecting gravity effects The simulation involves: Laminar viscous model Velocity inlet and pressure outlet boundary conditions Second-order spatial discretisation coupled with SIMPLE pressure-velocity coupling characterises solution techniques. Results For both channel angles—15 and 45 degrees—the simulation offers 2D contours of velocity, pressure, and temperature. The Nusselt number distribution over the upper wall is also examined for both setups.
Episode 10 12m 16s Free Episode -
Description This comprehensive course covers the basics of geometry generation using Space Claim and explores advanced meshing techniques with ANSYS Meshing. A detailed setup produces 48,000 elements, ensuring a robust and accurate model for analysis.
Episode 11 10m 30s Free Episode
-
-
Section 2
Moving Reference Frame (MRF)
-
Single Reference Frame (SRF) Axial Pump: Advanced CFD Simulation Analysis Understanding Axial Pump Dynamics Through Computational Fluid Dynamics In applications needing high flow rates with modest pressure requirements, axial pumps are essential fluid handling tool. Using the Single Reference Frame (SRF) approach, this extensive CFD simulation investigates the intricate flow dynamics inside an axial pump, therefore offering important new perspectives on performance aspects. Pump Configuration and Operating Parameters The simulation examines an axial pump with the following operational specifications: Inlet water velocity: 2 m/s Outlet condition: Atmospheric pressure Impeller rotational speed: 200 RPM Modeling approach: Frame Motion module Geometric Modeling and Computational Domain The study makes advantage of a two-dimensional axisymmetric model with certain dimensions: Domain length: 118 mm Domain width: 117 mm Design software: SpaceClaim Mesh Generation and Numerical Framework Features of the computational domain include: Mesh type: Unstructured elements Element count: 36,865 Meshing software: ANSYS Meshing Simulation Methodology and Solver Configuration The study applies specific computing parameters: Pressure-based solver type (considering water incompressibility) Style of analysis: Simulating steady-states Gravitational effects: Not paid attention to Rotational modeling is: Approach of Multiple Reference Frame (MRF) Particularly careful: Axisymmetric Swirl possibility enabled Performance Results and Flow Behavior Analysis Velocity Profile and Pressure Distribution The simulation exposes important aspects of performance: Component of radial velocity: notable change from input to exit brought about by blade rotation Dynamic pressure: Correspondent proportional rise based on fluid velocity changes Engineering Implications The results demonstrate how the rotational motion of the impeller transfers energy to the fluid, converting mechanical energy into hydraulic energy. This analysis provides essential data for: Optimizing axial pump design for specific applications Predicting performance under various operational conditions Understanding flow patterns and potential areas of efficiency improvement Identifying optimal operating parameters for maximum pump effectiveness
Episode 1 9m 27s Free Episode -
Description This comprehensive course covers the basics of geometry generation using Space Claim and explores advanced meshing techniques with ANSYS Meshing. A detailed setup produces 36,865 elements, ensuring a robust and accurate model for analysis.
Episode 2 7m 52s Free Episode
-
-
Section 3
Gas & Petrochemical
-
Overview of Compressible Flow in a Bent Pipe CFD Simulation using ANSYS Fluent Project Description This project involves simulating compressible flow inside a bent pipe to analyze the formation and effects of a shock wave. Air at 5°C enters the pipe with a Mach number of 0.9, causing an extreme pressure gradient that results in a shock wave. To accurately capture flow characteristics in high-gradient zones, gradient adaption in ANSYS Fluent is employed. Geometry and Meshing Geometry Creation: Designed in ANSYS Design Modeler, featuring a bent pipe with a 3 cm diameter. Initial Meshing: Unstructured mesh grid created using ANSYS Meshing with 191,479 elements. Refined Meshing: After applying gradient adaption, the mesh refined to 1,450,983 elements. Methodology: Compressible Flow in a Bent Pipe Solver Type: Density-based solver used for simulation. Simulation Type: Performed in Transient form. Viscous Model: K-Omega SST model employed for accurate fluid behavior capture, especially near walls. Conclusion The simulation reveals air entering the pipe with a Mach number of 0.9 and a temperature of 5°C, experiencing a significant pressure drop at the bend, known as a shock wave. The analysis requires a high-quality mesh, and the gradient adaption technique was utilized to refine the mesh in high y-plus zones. Pressure Drop: Approximately 120 kPa along the pipe, resulting in significant variable distribution. Due to the coarse tetrahedron mesh grid limitations, the y-plus value was addressed with mesh refinement through gradient adaption.
Episode 1 13m 57s Free Episode -
Description This comprehensive course covers the basics of geometry generation using Design Modeler and explores advanced meshing techniques with ANSYS Meshing. A detailed setup produces 1,450,983 elements, ensuring a robust and accurate model for analysis.
Episode 2 11m 54s Free Episode
-
-
Section 4
Aerodynamics & Aerospace
-
Description This comprehensive course covers the basics of geometry generation using Design Modeler and explores advanced meshing techniques with ANSYS Meshing. A detailed setup produces 1,744,624 elements, ensuring a robust and accurate model for analysis.
Episode 1 11m 34s Free Episode -
Summary of Supersonic Flow over Blackbird Aircraft CFD Simulation, SR- 71 Project Description Using ANSYS Fluent, this project models the supersonic flow over an SR-71 Blackbird aircraft. In dry air at 20°C, suersonic speed is defined as speeds above the speed of sound, roughly 343 m/s. Traveling at 446 m/s in this simulation, the SR-71 aircraft produces a Mach number of 1.3 with a 2-degree angle of attack. Geometry and Meshing Geometry Design: Design Modeler imports the three-dimensional geometry of the SR-71 Blackbird and positions it inside an enclosure. Initial Meshing: Unstructured mesh produced with ANSYS Meshing with 1,744,624 components. Mesh Conversion: ANSYS Fluent transformed tetrahedron mesh to polyhedra for improved simulation accuracy. Methodology: Supersonic Flow over SR-71 Blackbird Aircraft Solver Type: Pressure-based solver modelling compressible flows by include ideal-gas behaviour of air density using a coupled pressure-velocity algorithm. Simulation Type: performed in steady state with the Sutherland model modeling viscosity as a function of temperature. Conclusion Over the SR-71 aircraft, the simulated supersonic flow (Mach number 1.3) emphasizes important observations: Solver Choice: Although compressible flow usually employs a density-based solver, a pressure-based solver was efficiently applied using the linked velocity-pressure technique. Shock Waves: Extreme velocity and pressure gradients were found near the nose and engines of the aircraft from shock waves. Density Variations: Important density differences verified the need of including compressibility into the model. Correlation: Pressure, density, and temperature showed the expected direct link.
Episode 2 15m 7s Free Episode -
Description This comprehensive course covers the basics of geometry generation using Design Modeler and explores advanced meshing techniques with ANSYS Meshing. A detailed setup produces 3,190,893 elements, ensuring a robust and accurate model for analysis.
Episode 3 16m 55s -
Using ANSYS Fluent, overview of airflow simulation around an aircraft. Project Description This simulation uses ANSYS Fluent to explore airflow dynamics around a computational domain-designed airplane. The objective is to examine the pressure applied on the fuselage of the aircraft together with the profiles of velocity and pressure close by. Approaching the airplane at a 100 m/s speed, the airflow strikes the fuselage. Geometry and Meshing 3D Geometry Design:Designed with Design Modeler, it simulates airflow by including an aircraft inside a big cubic computational zone. Meshing Details: ANSYS Meshing program produced unstructured mesh with 3,190,893 cells for thorough investigation. Methodological Approach Simulation Setup: steady-state simulation with a pressure-based solver including incompressible airflow circumstances. Turbulence Modeling: Simulating turbulence with gravity effects omitted using SST k-omega model. Conclusion The simulation outputs offer interesting 2D and 3D contours regarding pressure and speed around the aircraft: Pressure Analysis: At the front of the airplane fuselage, one finds maximum pressure. Velocity Analysis: At the back of the aircraft is found a separation zone. Forces Calculated: On the airplane, the simulation determines a drag force of 16,516.279 N and a lift force of 104,220.68 N.
Episode 4 9m 7s Free Episode -
An overview of the container effect on truck aerodynamic CFD simulation Project Description With an eye toward lowering drag force—which is absolutely essential for increasing forward movement, fuel economy, and environmental impact—this research centers on the aerodynamics of a vehicle. The aerodynamic drag force on a vehicle with and without a container is investigated in ANSYS Fluent using CFD simulation. Geometry and Meshing Design Tools: Solidworks and Design Modeler help to design truck geometry. Meshing: Using a polyhedral mesh in ANSYS Meshing, create 663,127 elements for the truck alone and 1,095,371 elements for the truck including a container. Methodology: Container Impact on Truck Aerodynamics Simulation Comparison: Evaluates two configurations—truck with and without a container. Turbulence Model:Gets better results by using the k-w SST model with a standard wall function. Solver Type: Solver based on pressure with SIMPLE momentum and coupling. Conclusion For both layouts, the simulation offers understanding of speed, pressure, and drag force: Drag Reduction: It is better for low air resistance since the drag force is less without the container. Flow Separation: By lowering the angle at the end of the container relative to the truck roof edge, the container delays flow separation at the rear, therefore lowering drag. Vortex Intensity: Images of flow lines show that, without the container, the angle of the truck's top edge influences vortex intensity. Pressure Coefficient: Pressure coefficient diagram analysis supports observations and highlights variations between the two setups.
Episode 5 1h 21m 29s Free Episode -
Using ANSYS Fluent, a summary of Ahmed Body Aerodynamic Study Project Description A simple model to investigate aerodynamic traits pertinent to car design is the Ahmed body. This work analyzes the incompressible isothermal airflow around the Ahmed body, a 1-meter automobile model inside a 25-meter wind tunnel using an ANSYS Fluent CFD simulation. Simulating an automobile speed of 72 km/h, the intention is to evaluate numerical models and compute drag values at an input speed of 20 m/s. Geometry and Meshing Geometry Setup: The Ahmed body is housed in a wind tunnel; the blue face serves as the inlet and the red face as the outlet. Meshing: ANSYS Meshing produces a 624,482 element mesh. With 10 prism layers added to precisely capture the border layer, a maximum skewness of 0.84 and an average of 0.22 guarantee sufficient quality. Methodology: Body Aerodynamic Study of Ahmed Solver Setup: Solver based on pressure with consistent-state flow behavior. Turbulence Model: Simulates turbulence using the k-w SST model in view of gravitational influences. Conclusion Many results are observed upon convergence of the solution: Convergence Criteria: Drag force stabilization and residuals less than 10^-5 mark the convergence of the solution. With a maximum Y-plus value of 60, boundary layer resolution is clearly efficient. Validation: A chaotic benchmark for verifying numerical models is the Ahmed body. Results of this work can be matched with drag, flow separation, and separation angle experiments. LES/DES Suitability: The Ahmed body is fit for high-quality LES/DES simulations to investigate turbulence features in automotive applications because of its basic form. Results Velocity and Pressure Fields: While maximum pressure develops at the front face's center where velocity is lowest, highest velocity is seen at the corners. Streamlines: Share observations on flow patterns surrounding the Ahmed body. Drag Force: computed for the specified model and conditions to be 15.091 N, exact.
Episode 6 24m 58s Free Episode -
ANSYS Fluent Aerodynamic Study of a Dimpled Golf Ball Problem Statement This work uses ANSYS Fluent to investigate, under particular conditions, the aerodynamic performance of a dimpled golf ball relative to a smooth spherical. To grasp their aerodynamic behavior, both objects are investigated with a velocity of 94 meters per second and a zero-degree angle of attack. Introduction Quasi-experimental aerodynamic coefficients in dynamic simulations might contain mistakes. A more exact approach for computing these coefficients and calibrating those acquired using semi-experimental software is computational fluid dynamics (CFD). This work computes and validates aerodynamic coefficients for enhanced accuracy using numerical simulations in ANSYS Fluent. Golf Ball Geometry & Mesh Geometry and Meshing Approach The work contrasts a smooth spherical with a dimpled golf ball. Accurate results in numerical simulations depend on high-quality mesh generating. The rest uses an unstructured grid; the boundary layer of the geometry is meshed using a prism grid. Combining Octree and Delaunay techniques with ICEM software guarantees seamless mesh production appropriate for the complex geometrical features such as dimples. Solution Settings Numerical Setup Software: ANSYS Fluent Mode: Steady-state simulation applied with a pressure-based solution. Fluid Properties: The fluid in the experiment is air, with qualities fit for incompressible flow. Boundary Conditions Inlet: Velocity at 94 m/s. Outlet: Pressure outlet having 0 Pascal's gauge pressure. Wall: Conditions of stationary wall applied to the object surfaces. Models and Methods Turbulence Model: Realizable K-epsilon having a standard wall function. Discretization: Second order for pressure and first order upwind for other variables. Convergence Residuals less than 10e-3 mark convergence, guaranteeing a stable and precise solution. Results & Discussion Important results derived from the simulation consist in: Flow Characteristics: At high Reynolds numbers, dimpled surface roughness enhances turbulence in the boundary layer and delays flow separation, hence increasing momentum on the surface. Drag force falls as a result. Drag Coefficient Analysis: The fast separation of the flow at low Reynolds numbers produces comparable drag coefficients for both smooth and dimpled spheres. Especially under different flow conditions, the study clarifies how dimples on a golf ball affect its aerodynamic performance. Together with a thorough training film, access to geometry and mesh data offers further understanding of the process of solving problems and result extraction.
Episode 7 1h 3m 43s Free Episode -
Airflow Modeling across a Flying Bird, ANSys Fluent CFD Simulation Training This work is to examine airflow modeling across a flying bird. Engineers could find motivation in the aerodynamic study to create more sensible wings with improved performance. Methodology The working fluid, air, is incompressible so the pressure-based solver is applied. Furthermore hired in order to represent the expected flow complexity and wakes is the k-epsilon Realizable two-equation turbulence model. Results Under this study, we looked at airflow across a bird. Birds' forms help to minimize the separation of the boundary layer and improve lift generation so the bird may fly through the air with the least possible effort. The acquired data indicates that the pressure distribution on the top surface of the wing (airfoil) is smaller than the pressure on the bottom face since the airflow velocity is more than that of the bottom surface. Lift force creation on the bird's wings will start from this pressure distribution.
Episode 8 1h 3m 25s Free Episode -
Comprehension of Steady Airflow over a Flapped Airfoil Project Overview Using ANSYS Fluent software, this CFD study thoroughly analyzes the constant airflow over a flapping airfoil with an attack angle of 12 degrees. Detailed CFD studies help us to know the aerodynamic qualities and flow dynamics. Geometry and Meshing Model Design Focusing on capturing the fundamental characteristics of the flapping airfoil, the current model is two-dimensionally constructed using the Design Modeler tool. Meshing Details Executed with ANSYS Meshing software, the meshing procedure produced a model of 64,731 elements, so striking a compromise between accuracy and computational efficiency. Flap Methodology High-Lift Device Analysis Reducing the stalling speed of an aircraft wing depends on a flap, which is a high-lift device. Usually installed on the trailing edges of a fixed-wing aircraft, flaps are evaluated for their influence on both lift and drag. Simulation Parameters The SST k-omega model is used in this work to properly capture flow patterns and compute drag and lift forces; 45 m/s of velocity interacts with the airfoil. Results and Conclusion Flow Contours and Aerodynamic Forces The solution method reveals two-dimensional contours of turbulent viscosity, pressure, and velocity. These contours show the pressure disparity between the pressure and suction sides of the airfoil, which is essential for lift creation. At the leading edge, the stagnation point is also seen; in velocity contours, the wake zone is rather noticeable. Lift and Drag Coefficients Moreover, the drag coefficient of the airfoil in the presence of a flap is equal to -0.0273, which is less than airfoil without a flap, where the drag coefficient is equal to -0.0822, which proves that flap presence is effective in drag force reduction that is favorable in aerodynamics applications.
Episode 9 10m 29s Free Episode -
Badminton Shuttlecock Flight CFD Simulation with ANSYS Fluent Project Overview Using ANSYS Fluent, this project studies the aerodynamic behavior of a badminton shuttlecock by means of airflow around it. The simulation emphasizes how the velocity of the shuttlecock is affected by interaction of 94 m/s with its geometry. Geometry and Meshing Design: Created in ANSYS Design Modeler. Mesh: Unstructured with 1,935,891 elements for capturing detailed flow features. CFD Simulation Settings Solver: Pressure-based Flow Model: Realizable k-epsilon with standard wall functions for turbulence. Boundary Conditions: Inlet velocity: 94 m/s Outlet: Pressure outlet at 0 Pa Walls: Stationary Solution Methods: Coupling: Pressure-velocity coupled Discretization: Pressure: Second order Momentum: Second-order upwind Turbulent features: First-order upwind Initialization: Velocity: (94, 0, 0) m/s Turbulent kinetic energy: 33.135 m²/s² Turbulent dissipation rate: 676464.7 m²/s³ Results and Analysis The simulation shows how the shuttlecock design influences airflow patterns and aerodynamic performance by providing contours for pressure, velocity, and temperature. These revelations assist to maximize design for improved stability and performance of flights.
Episode 10 12m 29s Free Episode -
Description Using ANSYS Fluent software, this project will investigate an incompressible isothermal air flow next to an Audi-A4-2017 automobile. Testing is done at a maximum speed of 77.76 m/s, which is fairly high, and the drag force value is derived. Methodology Design Modeler software creates the 3-D geometry of the model. The current model has a rectangular cubic computational domain measuring 20 m * 10 m * 5 m for airflow, in which a AUDI car sits. Unstructured mesh type is used; ANSYS Meshing tool was used to complete the model meshing. The element number is 4,950,697, and the meshing accuracy is better near the vehicle surfaces. Conclusion Results might be seen via post-processing once the solution has converged. The drag value was tracked during the solution iterations to guarantee a good convergence. The solution in this work was a convergent one when the drag force attained a constant value and the residuals fell below 10-5 values. Most drag forces are pressure forces, according to the findings; the proportion of frictional forces in drag is small. The front and back of the car experienced the most pressure, which resulted from the least velocity contour. The velocity vectors show flow separation at the front and rear of the car. This separation is more concentrated in the front of the automobile and is wider in the back of the vehicle, which can be ascribed to the broader geometry in the back of the car. Though in places with more angle to the flow direction, this pressure is larger. Pressure on the surface increases the more perpendicular it is to the flow. The pressure on the sharp edges, particularly on the front wheel and the edge of the front glass, is negative as well; the speed in these regions has risen, which may be ascribed to the fast shift in the flow angle caused by the change in fracture. The Shear force contours also indicate that the flow separation began when these contours changed sign. The drag force calculated in this issue is 1684.74 Newtons.
Episode 11 18m 36s Free Episode -
Comprehension of UAV External Airflow Simulation Project Description Focussing on aerodynamic forces, stability, and design optimisation, this project uses ANSYS Fluent to simulate the airflow around a UAV (drone). Because of their remote control features, UAVs are commonly utilised in military and aviation sectors, therefore aerodynamic study is very vital. Methodology Aerodynamic Design: CATIA was used to design the UAV's shape; SpaceClaim was used to hone it; ANSYS Meshing's unstructured mesh of 3,079,338 components was used to mesh it. Turbulence Modeling: High-speed airflow causes turbulence and flow separation that the conventional k-epsilon model with standard wall functions captures. Conclusion The simulation offers knowledge on pressure and velocity contours, streamlines, and velocity vectors surrounding the UAV. Among the main results are: Maximum Pressure and Velocity: Occur at the front and top of the UAV, respectively, with maximum velocity reaching roughly 43 m/s against an incoming airflow speed of 30 m/s—emphasizing acceleration due to the UAV’s structure. Flow Dynamics: The study shows vortex generation, flow separation, and other important aerodynamic phenomena, guiding design changes.
Episode 12 21m 46s Free Episode -
Overview of Train Airflow Simulation Project Description Focussing on lowering the drag force to improve energy efficiency, this work uses ANSYS Fluent to study the aerodynamic behaviour around a moving train. High-speed train movement creates airflow-induced events such separations and vortex generation, hence stressing the need of aerodynamic design. Methodology Geometry and Meshing: Using an unstructured mesh with 1,013,277 components, SpaceClaim and ANSYS Meshing model and mesh the train and fluid domain correspondingly. Turbulence Modeling: Studying vortex dynamics and flow separation, the simulation looks at turbulent flow characteristics around the train. Conclusion Key insights from the simulation include: Pressure Distribution: The front surface of the train experiences most pressure; as speed climbs away from the wall, aerodynamic suction grows. Boundary Layer and Turbulence: Greater boundary layer thickness at the rear of the train suggests more turbulence from flow separation. Energy Efficiency: A drag force works against the motion of the train, therefore aerodynamic design helps to reduce energy loss by lowering drag. This work shows how simulating train aerodynamics may guide design plans to maximise energy economy and save building costs.
Episode 13 13m 24s Free Episode -
Description This comprehensive course covers the basics of geometry generation using Design Modeler and explores advanced meshing techniques with ANSYS Meshing. A detailed setup produces 296533 elements, ensuring a robust and accurate model for analysis.
Episode 14 18m 58s Free Episode -
Overview of Airflow Around a NACA 0008 Airfoil CFD Simulation Project Description Using ANSYS Fluent to examine airflow behaviour, pressure distribution, and drag and lift forces, this project mimics the airflow around a NACA 0008 aerofoil. Important geometric variables are the chord line, angle of attack, leading edge, and trailing edge. With the chord length and aerofoil width both 1 unit, the angle of attack is fixed at 16 degrees. The velocity of the input air flow is 20.78736 m/s. Using the chord length altered by the sine and cosine of the 16-degree angle, respectively, together with the cross-sectional width, the drag and lift forces are computed. Geometry & Mesh Design Modeller builds the 2D geometry by importing point coordinates of the aerofoil wall. Drawn to standard criteria, the model has a far-field border for airflow study. Using ANSYS Meshing, which has an unstructured mesh of 296,533 components, meshing is done. Methodology Ignoring gravitational influences, the simulation presumes a steady flow model and a pressure-based solver. Turbulence modelling employs the k-epsilon RNG improved wall treatment approach. Results Apart from 2D pathlines, the simulation offers 2D contours of pressure, velocity, and turbulent kinetic energy. It also computes the forces and coefficients of drag and lift, hence providing information on the aerodynamic performance of the aerofoil.
Episode 15 13m 46s Free Episode
-
-
Section 5
Mechanical
-
Heat Transfer Simulation for Impinging Jets on a U-Shaped Plate using ANSYS Fluent: An Overview Project Description This work uses ANSys Fluent for the simulation to examine the heat transport characteristics of an impinging jet on a U-shaped plate. Effective heat transmission properties of impinging jets are widely used in many different industrial uses including ventilation and cooling. This work is to investigate convection heat transfer behavior in particular respect to Reynolds numbers and investigate how heat transfer rates are affected by thermal boundary layer thickness. Geometry and Meshing Geometry Design: developed with Design Modeler utilizing a jet-impacted U-shaped plate. Mesh Details: Using hexahedral components totaling 2,700,000, structured meshing with ICEM CFD. Methodology Simulation Setup: Steady-state simulation incorporating a gravity effect of -9.81 m/s² on the fluid, using pressure-based solver in place of incompressible flow assumptions. Turbulence Model: SST k-w model to depict turbulence properties. Boundary Conditions: Inlet: Velocity inlet at 34.89 m/s; temperature at 298 K. Outlet: Pressure outlet with 0 atm set as gauge pressure. Wall Conditions: Applied on a U-shaped plate and jet wall, flux at 5000 W/m². Results and Analysis Flow Dynamics: Regions of the impinging jet show free jet, stagnation zone, and later wall jet. Maximum pressure noted at the stationary point the jet passes across to impact the plate. Nusselt Number Analysis: Peak Nusselt number at stagnation increases heat transfer because of minimum boundary layer thickness. Boundary layer thickening outside the stagnation zone causes Nusselt number to drop. The study at many Reynolds numbers—23,000, 14,000, and 40,000—showcases the clear impact on Nusselt number distribution. Induction Vortices and Secondary Peaks: Large-scale vortices during stagnation raise fluid velocity, hence improving heat transfer. Secondary peaks on the Nusselt number curve connected to boundary layer transitional vortex formation. Influence of Geometric Parameters: Heat transfer in the nozzle portion depends on aspect ratio; higher ratios produce better results. Maximum heat transfer found by ideal nozzle-positioning (H/d ratio).
Episode 1 15m 25s Free Episode -
ANSYS Fluent Simulations of Methane Gas Flow Through an Orifice Problem Statement This work simulates methane gas flow across an aperture inside a channel using a CFD model. Designed in 3D with Design Modeler tools, the model represents a 12-inch long channel with a 0.5-inch diameter and a center orifice with a 0.25-inch diameter. Orifice Model and Meshing A perforated plate placed perpendicularly to the direction of fluid flow forms the most basic orifice model. Using a structured mesh with 54,648 elements to guarantee accurate simulation results, this model is meshed using ANSYS Meshing software. Orifice Methodology Mass flow through pressure difference transmitters is routinely measured using the orifice equipment. Following Bernoulli's principle and mass conservation, a fluid's velocity increases as it passes through an aperture from decreased cross-sectional area. Velocity reduces as the area grows upon leaving, which raises flow pressure. Key Parameters and Simulation Setup Fluid Properties: methane gas with viscosity of 0.00001087 kg/m.s. and density of 0.6679 kg/m³. Flow Conditions: Methane leaves at atmospheric pressure after entering the pipe at 0.033 m/s. Turbulence Model: The RNG k-epsilon model is applied in the simulation to solve turbulent flow equations. Results and Conclusion Along with graphs of pressure and velocity changes across the central axis and through the orifice section, the simulation generates two- and three-dimensional velocity and pressure contours. Results Analysis Reduced cross-sectional area causes visible increased velocity at the oracle to match Bernoulli's principle's expectations. Pressure differential measurements let one to examine the clearly visible matching pressure drop in the fluid flow through the oracle. This study exemplifies the orifice’s capability in determining fluid flow rates accurately by analyzing pressure differences, providing valuable insights into flow dynamics for engineering applications. If you’re interested in further details or need guidance on similar simulations, feel free to reach out!
Episode 2 12m 21s Free Episode -
Overview of CFD Simulation of External Airflow over a Flat Plate Project Description Focussing on the behaviour of airflow and heat transfer dynamics, this simulation uses ANSYS Fluent to describe the external flow of air over a flat plate. The air's thermal conductivity is 0.0242 W/m·K, viscosity 0.000017894 kg/m·s, and density 1.225 kg/m³. With ambient air at 273 K, the plate keeps a steady temperature of 333 K. Flat Plate Geometry & Mesh Created in ANSYS Design Modeller, the 2D model has lower edge depicting the flat plate. There are 3,000 element structured meshes in the geometry. The left and right borders are the inlet and outflow for airflow. CFD Simulation Settings Solver: Pressure-based, steady-state Viscous Model: Laminar (Re < 50,000) Boundary Conditions: Inlet: Variable velocity, temperature 273 K Outlet: Pressure outlet at 0 Pascal Walls: Stationary Solution Methods: Coupling: SIMPLE Discretization: Second order for pressure and momentum Results and Conclusion The simulation investigates the hydrodynamic boundary layer as well as velocity and temperature distributions. Results comprise 2D contours for temperature and velocity, velocity vectors, and diagrams of heat transfer coefficients and boundary layer thickness for Reynolds numbers 10,000 to 50,000.
Episode 3 12m 22s Free Episode -
Description This comprehensive course covers the basics of geometry generation using Design Modeler and explores advanced meshing techniques with ANSYS Meshing. A detailed setup produces 3000 elements, ensuring a robust and accurate model for analysis.
Episode 4 5m 49s Free Episode -
Overview of Turbine Blade Cooling Simulation Project Description Using ANSYS Fluent, this work replicates the cooling process of a turbine blade. Using the symmetrical design of the turbine body and blades, only one blade is modelled to investigate temperature distribution and thermal energy variations on the turbine blade. Cool airflow through an empty space within the blade's inner walls, with perforations to maximise contact with the cold flow and improve the cooling effect, is the method of cooling. Geometry & Mesh CATIA builds the 3D model; Design Modeller gets it for more modelling. Using ANSYS Meshing, an unstructured mesh of 10,154,723 components is created. Methodology Both the inner and outer sides of the blade have heat transfer boundary conditions applied to them. The exterior surface exposed to hot working airflow has a temperature of 1672 K and a heat transfer coefficient of 200 W/m². Under a flow of 300 K, the inner surface, chilled by cold airflow, likewise exhibits a heat transfer coefficient of 200 W/m². Results The simulation produces 2D and 3D temperature contours for the area between the outer and inner walls of the blade. It also offers heat transfer coefficients for the blade base and these surfaces. 2D contours in the XZ section are also visualised at many distances (0.004, 0.016, 0.028, and 0.04 meters) from the blade base top surface, as well as in the XY section at varying distances.
Episode 5 19m 30s Free Episode -
Overview of Fluid Flow Around a Wavy Tape in a Tube CFD Simulation Project Description This study studies fluid flow through a circular tube including a wavy tape as a thermal insulating barrier using ANSYS Fluent. The research focuses on heat transfer analysis within the tube. Assumptions Using a pressure-based solver, the simulation is steady-state; gravitational influences are ignored. Geometry & Mesh Designed in Design Modeller, the 3D model has a semi-cylinder with wavy boundaries indicating the symmetrical tube. Using an unstructured mesh with 653,307 components, ANSYS Meshing performs meshing. CFD Simulation Procedure Models and Boundary Conditions Viscous Model: Laminar Energy Equation: Enabled Inlet: Velocity of 0.0110334 m/s, Temperature of 293.15 K Outlet: Pressure set to 0 Pa Wall: Wave wall with heat flux of 0 W/m², Outer wall temperature at 360 K Solution Methods Pressure-velocity coupling using SIMPLE Second-order upwind discretization for pressure, momentum, and energy equations Initialization Standard initialization with z-velocity set at -0.0110334 m/s, Temperature at 293.15 K Results The simulation produces 3D and 2D contours of pressure, temperature, and velocity as well as flow lines and velocity vectors in both 2D and 3D formats post-solution, therefore offering thorough knowledge of the fluid dynamics and heat transfer properties around the wavy tape.
Episode 6 12m 50s Free Episode -
Description This comprehensive course covers the basics of geometry generation using Design Modeler and explores advanced meshing techniques with ANSYS Meshing. A detailed setup produces 653307 elements, ensuring a robust and accurate model for analysis.
Episode 7 22m 6s Free Episode
-
-
Section 6
HVAC
-
Steady Airflow Over a Ventilated Air Cavity: CFD Study Using ANSYS Fluent Statement Using ANSYS Fluent software, this CFD project models the continuous airflow over a ventilated air chamber. Designed with Design Modeler, the three-dimensional geometry features a cavity connected into a rectangle domain. Using ANSYS Meshing software, the meshing procedure produces 853,616 elements overall. Methodologies for Ventilated Cavities The study aims to comprehend the interaction between a cavity with an aperture along its length and airflow: Geometry and Mesh: A thorough mesh catches complex flow dynamics both inside and outside of the hollow. Flow Dynamics: Crucially for applications in fluid mechanics and aerodynamics, the simulation looks at how airflow enters the hollow. The hole in the cavity lets flow in and out, therefore lowering pressure drop across the cavity and hence drag force. Simulation Setup Inlet Airflow Velocity: 1.7 m/s. Turbulence Model: The K-epsilon model is used since the great speed helps to properly solve fluid flow equations. Results and Conclusion The simulation offers insightful analysis of the flow properties and ventilated cavity performance: Velocity and Pressure Analysis: At the leading edge of the cavity, contours point to a maximum speed of 2.32 m/s. Mass Flow Rate and Drag Force: The resulting drag force on the cavity is computed to be 0.0001168629 N; the air mass flow rate at the outflow is 6.747232 kg/s. The results underline the advantage of cavity ventilation in lowering drag by minimising pressure variations, therefore providing significant design implications for aerodynamics and fluid mechanics. Please ask for extra information or help with comparable analysis.
Episode 1 8m 41s Free Episode
-
-
Section 7
Chemical
-
Plate Heat Exchanger CFD Simulation, ANSYS CFX Software
Introduction to Plate Heat Exchanger CFD Simulation This CFD project simulates a plate heat exchanger system by modelling four solid plates with pipes at their corners. Studying heat transmission mechanisms, the water flows in opposite directions through these pipes at varying temperatures. Geometry and Meshing DesignModeler creates the 2.5D geometry using solid plates of 2x2 meters and pipes with a 0.15-meter diameter. Totalling more than 5 million components, the mesh is generated in ANSYS Meshing using unstructured elements and 5 layers of inflation inside the pipes. Simulation Methodology The simulation operates in a steady-state, ignoring gravitational influences, using ANSYS CFX. Conduction inside solids and convection between water and pipes help to study heat transmission. The k-epsilon turbulence model depicts the kinetics of heat transmission. Results and Analysis The CFD-Post program offers analysis of velocity, turbulence kinetic energy, temperature, and water pressure. With faster speeds improving convective heat transfer rates, the paper underlines how fluid velocity affects heat transfer efficiency.
Episode 1 Coming Soon Free Episode
-
-
Section 8
Architectural
-
Description of Conjugate Heat Transfer in Wind Tower Project Overview Using ANSYS Fluent software, this study investigates the conjugate heat transfer (CHT) process of airflow inside a simplified four-story wind tower. By means of CFD study, we investigate the interaction of convective and conductive heat transport inside this architectural component intended for natural ventilation. Geometry and Meshing Model Design Design Modeler is used to carefully create the 2D shape of the wind tower, hence capturing the necessary characteristics for heat transfer study. Meshing Details The computational grid is generated using ANSYS Meshing software, featuring a structured mesh with 6,375 elements to facilitate accurate simulation of heat and flow dynamics. Wind Tower Methodology Heat Transfer Modeling Conjugate heat transfer modeling consists of both convective and conductive heat transfer mechanisms inside the wind tower. With a heat generation rate of 1000 W/m³, the diagonal wall on the right side of the computational domain is kept at 305 K. Inlet Conditions and Airflow Inlet Boundary: Top left side of the wind tower Inlet Velocity: 12 m/s Initial Temperature: 300 K Aiming to promote ventilation and temperature lowering, air flows through the four stories of the structure. Gravity and Buoyancy Effects Gravity is activated in the Y direction to mimic natural convection. With an initial air density of 1.225 Kg/m³ and a thermal expansion coefficient of 0.00331 1/K, the Boussinesq model is used to account for changes in air density caused by temperature variations. Results and Conclusion Two-dimensional contours connected to velocity, pressure, temperature, streamlines, and velocity vectors inside the computational domain help the simulation to uncover various important discoveries. Temperature Distribution The temperature contour showcases the thermal distribution along the heated wall, illustrating how temperature varies throughout the wind tower. Airflow Dynamics Contours of velocity, streamlines, and velocity vectors reveal that: Top Levels: Experience higher momentum and velocity airflow due to reduced hydraulic resistance. Bottom Levels: Display rotating airflow patterns induced by the forced airflow, as seen in the velocity vector contour. Driven by the natural convection effect started by contact with the diagonal heated wall, the airflow finally rises to depart through the pressure outlet boundary on the top right.
Episode 1 13m 7s Free Episode -
Project Description Acting as barriers, three structures set in a triangular pattern will have simulated airflow around them for this project. The buildings are struck by wind entering the region horizontally at 5 m/s. Project Objective The goal is to look at how wind flow around the structures changes after impact and to analyse the area between the buildings' circulation. Methodology Design Modeller software runs the 3D modelling; ANSYS Meshing with an unstructured mesh type handles meshing. With smaller and more precise cells next to the structures, the total number of elements is 6,392,910. Conclusion Velocity and pressure contours, velocity vectors and 2D pathlines, as well as velocity vectors, are produced upon finishing the solution procedure. The findings draw attention to the development of maximum wind speeds at the building tips and the generation of separation vortices behind the structures. Especially, the vortex behind the middle building is symmetrical and larger because of vortex interaction. The pressure contour shows highest pressure in front of the centre building.
Episode 2 14m 39s Free Episode
-
-
Section 9
Hydraulic Structure & Civil
-
Comprehension of CFD Simulation of Water Flow in a Zigzag Channel Project Description Based on the paper "CFD Simulations of Flow and Heat Transfer in a Zigzag Channel with Flow Pulsation," ANSYS Fluent is used in this simulation to model the flow of water through a zigzag canal. These findings are confirmed by comparison with this reference article. Model Design Angled at 15 degrees, the channel is made up of 10 horizontal oscillation stages. While intake temperature remains constant at 293.15 K, water flow changes with Reynolds number. The channel is 1 mm deep and 8 mm wide with a 3D pattern. Including boundary layer mesh on the walls, ANSYS Meshing offers an unstructured mesh of 144,713 components. Methodology Low Reynolds numbers (53 to 534) suggest laminar flow. Simulations seek to explore the Nusselt number close to the upper wall, which has a steady temperature of 276.65 K. Results and Conclusion The study determines the Nusselt number for several Reynolds numbers by comparing them to reference data. Results verify the temperature-dependent link of the Nusselt number, which changes with velocity and Reynolds value. Key Reynolds number results: Re 53: Nu = 5.5198 Re 107: Nu = 6.6144 Re 534: Nu = 11.1337 For Reynolds numbers 53, 266, and 534, three-dimensional velocity, pressure, and temperature contours are examined.
Episode 1 17m 19s Free Episode -
Comprehension of CFD Simulation of Water Flow Around a Dimpled Cylinder Project Description This simulation models water flow within a rectangular domain around a dimpled cylindrical body using ANSYS Fluent. It is validated against the study “Control of flow past a dimpled circular cylinder.” Model Design The model runs on water with a Reynolds number of 17,980, which corresponds to an inlet speed of 0.45 m/s. Applied with a DF (dimple full) pattern, the vertical cylinder inside the flow domain has dimples on its inner surface. Designed in SOLIDWORKS, the computational domain is a rectangular cube (6 m x 0.3 m x 0.4 m), with a cylinder (0.4 m length, 0.04 m diameter). Composed of 1,966,490 components, the mesh is organised. Methodology The emphasis is on evaluating aerodynamic forces, such lift and drag, on the surface of the cylinder. These forces and coefficients are obtained by means of steady and transient simulations 60s with 1s time steps. Results and Conclusion In transient simulations, drag and lift coefficients stabilise and are compared with reference data. Dimple size is determined by diameter-to-cylinder ratio: 0.1 for diameter and 0.05 for depth. Simulations produce 2D pressure and velocity contours for more study.
Episode 2 15m 3s Free Episode -
Description This comprehensive course covers the basics of geometry generation using SolidWorks and explores advanced meshing techniques with ANSYS Meshing. A detailed setup produces 1,966,490 elements, ensuring a robust and accurate model for analysis.
Episode 3 24m 27s Free Episode -
Overview of Bridge Pillars External Two-Phase Flow CFD Simulation Project Description Focussing on the interplay between air and water around the structures using ANSYS Fluent, this work looks at how fluid flow affects bridge pillars. The study draws attention to issues including scouring, which compromises bridge foundations. Model Design The geometry consists of two bridge columns orientated in the flow direction to examine their interaction. Designed in ANSYS Design Modeller, it is meshed using 415,860 components using ANSYS Meshing. Methodology Two-Phase Flow: Modelled utilising the Volume of Fluid (VOF) method, air being the first phase and water the second. Turbulence: Modelled using conventional wall functions using the RNG k-epsilon approach. Solver: Considering gravitational effects, pressure-based, steady-state. Conclusion The simulation produces volume fractions for water and air, streamlines, velocity, and pressure contours. Among the main findings are: Around columns, water creates vortices and eddies, hence increasing turbulence. Air over pillars forms a boundary layer. Interaction between air and water creates a mixing layer that helps to create turbulence close to pillars.
Episode 4 28m 41s Free Episode
-
-
Section 10
Multi-Phase Flow
-
Project Description This project simulates a shower drain system within an inclined channel, analyzing water input dynamics using ANSYS Fluent. Such systems are critical in various settings like bathrooms, carwashes, and pools. Model Design Designed in ANSYS Meshing, the geometry has an unstructured mesh of 1,310,945 components created in ANSYS Design Modeller. Methodology Multi-phase Flow: To represent the two-phase flow of air and water inside the channel, the Volume of Fluid (VOF) approach is used. Gravity: The effect of gravity is incorporated, set at -9.81 m/s² in the Y direction. Conclusion Included in the simulation findings are 2D and 3D volume fraction, pressure, and velocity contours. They explain how channel slopes matter by making sure water drains towards the shower drain and verifying that an ideal configuration really points water flow towards the lowest point.
Episode 1 28m 41s Free Episode
-
-
Section 11
Porous
-
Overview of Fluid Flow in Porous Media Simulation Project Description Aiming to grasp fluid dynamics via various porosities, this work uses ANSYS Fluent to look at fluid behaviour inside porous media. Industries include food, oil, textiles, and filtration are common with porous materials. Methodology Geometry and Meshing: The model is made up of an upstream flow domain, a porous medium domain, and a downstream flow domain. The model, which has a structured mesh of 35,017 components, was created in ANSYS Design Modeller and meshed in ANSYS Meshing. Porous Medium Definition: A porosity coefficient defines the porous media; it is the ratio of void space to whole space. Three porosities—0.5, 0.7, and 0.9—are examined to evaluate their influence on fluid flow. Conclusion The simulation findings produce contours of static pressure drop, turbulent viscosity, velocity, and pressure. Pressure and Flow Dynamics: A pressure drop is seen as fluid moves through the porous medium, hence verifying the porous material's function in lowering fluid pressure. Comparative Analysis: Different porosities show different pressure drops, hence stressing the effect of porosity on fluid behaviour. This paper shows how porous media change the properties of fluid flow, hence providing ideas for use in many sectors.
Episode 1 13m 39s Free Episode
-
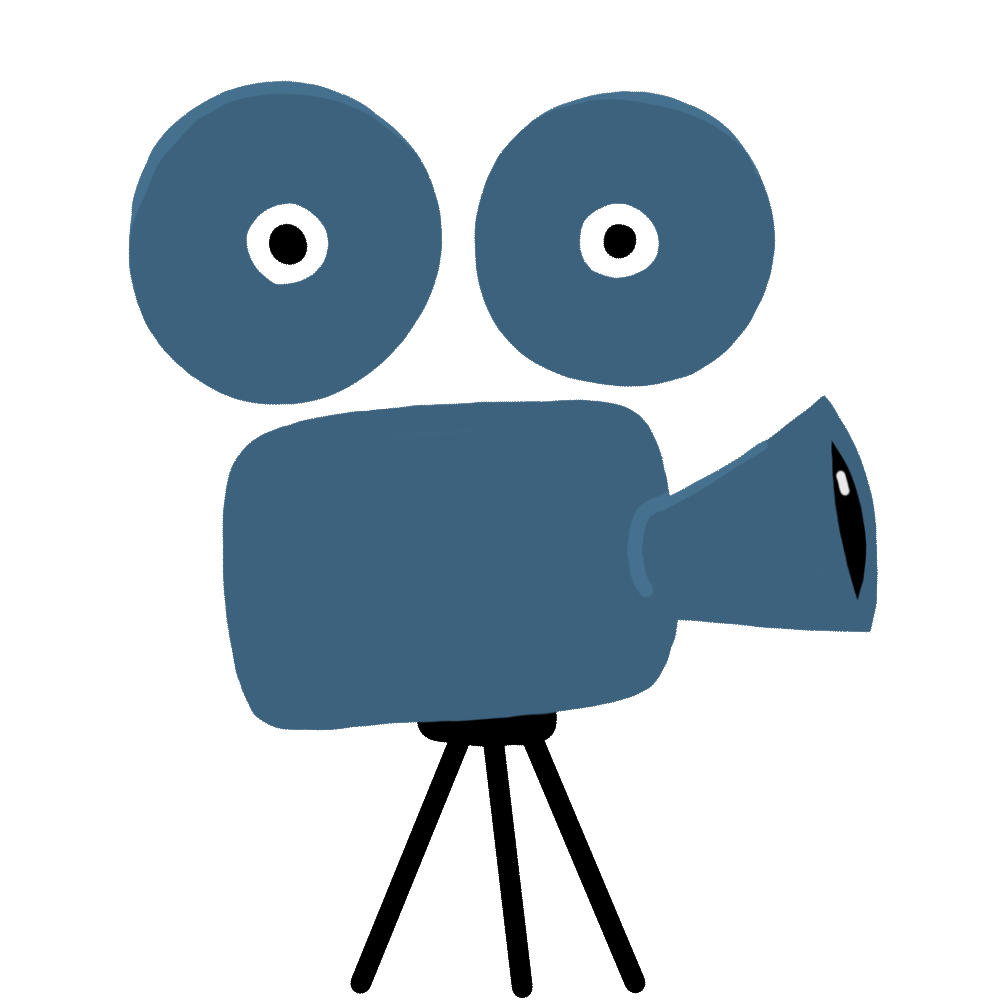
Course In Progress
Course still in development. Check back often for updates.
Total Review of ANSYS Fluent CFD Simulation Projects
Heat Transfer Projects
Forced Convection Heat Transfer at U-Bend
Investigate forced convection heat transfer dynamics in a U-bend arrangement with an eye toward thermal performance optimization.
Thermal Analysis within a CFD Simulation for Storage Tank
Thermal study inside a storage tank will help one grasp heat distribution and transfer efficiency.
CFD Simulation using Cylindrical Heat Source
Analyze the heat behavior of a cylindrical heat source to enhance heat dissipation techniques.
Flight Simulation and Aerodynamics and Flow
Golf Ball Aerodynamics, ANSYS Fluent CFD Simulation Training
Examine a golf ball's aerodynamic qualities to learn how dimple patterns influence flight dynamics.
Airflow around an aircraft in a CFD simulation ANSYS fluent training
To maximize aerodynamic efficiency, replicate the airflow surrounding an aircraft in design.
Supersonic Flow across Blackbird CFD Simulation, SR- 71
Examine the supersonic airflow properties over the SR-71 Blackbird with an eye toward drag reduction techniques.
Studies of Advanced Fluid Flow
Single Reference Frame (SRF) Axial Pump CFD Simulation
Improve performance of an axial pump by simulating fluid dynamics with the Single Reference Frame technique.
Flow Behavior Through a Porous Media: ANSYS Fluent Training
Analyze the complicated flow behavior via porous media; this is essential for applications in fluid absorption and filtration systems.
Compressible Flow in a Simulated Bent Pipe CFD
With an eye toward pressure and velocity changes, investigate the difficulties of modeling compressible flow through a bent pipe.
Benchmarking and validation using computational design tools
Heat Transfer Using Twisted Tape Inserts: Validation
Verify the heat transfer efficiency of pipes including twisted tape inserts to maximize thermal control systems.
Dimpled Cylinder Flow Control; ANSYS Fluent Training; Paper Numerical Validation
Understand the decrease in drag and improvement in heat transfer by simulating and verifying the flow control around a dimpled cylinder.
Laminar Flow Heat Transfer in U-Bend, Paper Validation
Compare laminar flow heat transfer in a U-bend with current knowledge by means of a comprehensive validation study.
Applications in Structural and Environmental Fields
Three Buildings' Wind Flow Around: ANSys Fluent Tutorial, CFD Simulation
Examine wind load effects and enhance structural design for urban planning by modeling airflow around a cluster of structures.
External Flow Passing Over a Flat Plate: ANSYS Fluent CFD Training
Investigate the external flow dynamics across a flat plate to improve understanding of boundary layer evolution.
Anansys Fluent Training: Bridge Pillars External Two-Phase Flow CFD Simulation
To learn how bridge pillars affect structural stability and water flow patterns, replicate two-phase flow interactions around them.
Buy Course
Benefits of buying the whole course
- Complete access to chapters Without Price
- Special discount
- Unlimited access to course content
- Free access to all new and updated content
- Access to course forever without any additional payment
* You can select chapters seperately, but you won't benefit from the list above.
* The items that do not have a price cannot be bought separately and are only available when you buy the whole course.
Congratulations
Congratulations! Your purchase was successful.
You can now start learning the course by clicking the button "Start Learning".
Add Payment Method
Please enter your payment method details.