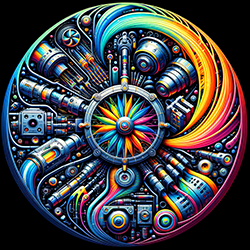
Combustion: ANSYS Fluent CFD Simulation Training Course
Workshop
Price:
$1,300.00
$199.00
Master the art of Combustion CFD Simulation with our comprehensive training course. Dive deep into the world of combustion modeling using ANSYS Fluent, covering everything from basic principles to advanced techniques. This course offers hands-on experience with various combustion types, including premixed, non-premixed, and partially premixed combustion. Learn to implement different turbulence-chemistry interaction models, simulate pollution formation, and utilize powerful tools like PDF transport and DPM combusting particle models. Through 10 detailed lessons and a final project, you’ll gain the skills to perform high-fidelity combustion simulations, making you a true expert in the field. Perfect for engineers, researchers, and students looking to excel in combustion CFD modeling.
Wet Combustion Using DPM Combusting Particle CFD Simulation
Wet Combustion Using DPM Combusting Particle CFD Simulation Welcome to this advanced episode of our “Combustion: All Levels” course. In this lesson, we delve into the intricate world of wet combustion simulation using the Discrete Phase Model (DPM) with combusting particles. This episode, which is the fourth chapter of our DPM training course, offers a unique exploration of complex combustion scenarios involving anthracite volatile in a combustion chamber. Project Overview Our simulation focuses on tracking fuel particles through the entire combustion process, from devolatilization to oxidation, resulting in the production of carbon dioxide and water vapor. This advanced model incorporates: A 2% liquid fraction in the fuel A 0.5-second injection duration Hot air introduction to the combustion chamber This setup allows us to investigate the intricate dynamics of wet combustion, mimicking real-world scenarios in advanced combustion systems. Simulation Methodology Our simulation employs a sophisticated approach to model the complex processes involved in wet combustion. Model Components We utilize a combination of advanced modeling techniques: Species Transport Model: For accurate tracking of chemical species Discrete Phase Model (DPM): To simulate anthracite particles Combusting Particle Type: With a 2% liquid fraction Particle Characteristics The anthracite particles are modeled with specific properties: Initial temperature: 325K Non-spherical shape Rosin-Rammler diameter distribution Geometry and Meshing The simulation environment is carefully crafted: Geometry designed using ANSYS Design Modeler software Unstructured mesh grid generated with ANSYS Meshing software Conversion to polyhedron cells for reduced computational costs Final mesh count: 810,000 cells Combustion Process and Reactions The wet combustion process in our simulation follows a specific sequence: Evaporation of the wet fraction of anthracite Release of the volatile fraction Oxidation of the volatile fraction The key reaction modeled is: 1An-vol + 2.207 O2 → 0.1 CO2 + 4.408 H2O This reaction leads to a significant temperature increase in the chamber, reaching up to 2400K. Results and Analysis Our simulation provides comprehensive insights into the wet combustion process: Temperature distribution throughout the combustion chamber Particle tracking from injection to complete combustion Species concentration profiles for O2, CO2, and H2O Energy release patterns during the combustion process To enhance understanding, we’ve extracted animations that visually demonstrate these processes. Learning Outcomes and Applications By the end of this episode, you’ll have gained: Advanced understanding of wet combustion simulation techniques Insights into DPM and combusting particle modeling in CFD Skills to interpret complex CFD results for multi-phase combustion systems Knowledge of how particle properties affect combustion dynamics These skills are directly applicable to: Designing efficient coal-fired power plants Optimizing biomass combustion systems Improving efficiency in industrial furnaces and boilers Advancing research in multi-phase combustion phenomena Join us in this cutting-edge exploration of wet combustion simulation using DPM and combusting particles in ANSYS Fluent. Elevate your CFD expertise to new heights in advanced combustion modeling and gain valuable insights into complex industrial processes!
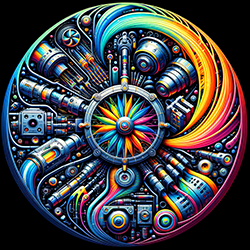
Combustion: ANSYS Fluent CFD Simulation Training Course
Workshop
Price:
$1,300.00
$199.00
Master the art of Combustion CFD Simulation with our comprehensive training course. Dive deep into the world of combustion modeling using ANSYS Fluent, covering everything from basic principles to advanced techniques. This course offers hands-on experience with various combustion types, including premixed, non-premixed, and partially premixed combustion. Learn to implement different turbulence-chemistry interaction models, simulate pollution formation, and utilize powerful tools like PDF transport and DPM combusting particle models. Through 10 detailed lessons and a final project, you’ll gain the skills to perform high-fidelity combustion simulations, making you a true expert in the field. Perfect for engineers, researchers, and students looking to excel in combustion CFD modeling.
Wet Combustion Using DPM Combusting Particle CFD Simulation
Wet Combustion Using DPM Combusting Particle CFD Simulation Welcome to this advanced episode of our “Combustion: All Levels” course. In this lesson, we delve into the intricate world of wet combustion simulation using the Discrete Phase Model (DPM) with combusting particles. This episode, which is the fourth chapter of our DPM training course, offers a unique exploration of complex combustion scenarios involving anthracite volatile in a combustion chamber. Project Overview Our simulation focuses on tracking fuel particles through the entire combustion process, from devolatilization to oxidation, resulting in the production of carbon dioxide and water vapor. This advanced model incorporates: A 2% liquid fraction in the fuel A 0.5-second injection duration Hot air introduction to the combustion chamber This setup allows us to investigate the intricate dynamics of wet combustion, mimicking real-world scenarios in advanced combustion systems. Simulation Methodology Our simulation employs a sophisticated approach to model the complex processes involved in wet combustion. Model Components We utilize a combination of advanced modeling techniques: Species Transport Model: For accurate tracking of chemical species Discrete Phase Model (DPM): To simulate anthracite particles Combusting Particle Type: With a 2% liquid fraction Particle Characteristics The anthracite particles are modeled with specific properties: Initial temperature: 325K Non-spherical shape Rosin-Rammler diameter distribution Geometry and Meshing The simulation environment is carefully crafted: Geometry designed using ANSYS Design Modeler software Unstructured mesh grid generated with ANSYS Meshing software Conversion to polyhedron cells for reduced computational costs Final mesh count: 810,000 cells Combustion Process and Reactions The wet combustion process in our simulation follows a specific sequence: Evaporation of the wet fraction of anthracite Release of the volatile fraction Oxidation of the volatile fraction The key reaction modeled is: 1An-vol + 2.207 O2 → 0.1 CO2 + 4.408 H2O This reaction leads to a significant temperature increase in the chamber, reaching up to 2400K. Results and Analysis Our simulation provides comprehensive insights into the wet combustion process: Temperature distribution throughout the combustion chamber Particle tracking from injection to complete combustion Species concentration profiles for O2, CO2, and H2O Energy release patterns during the combustion process To enhance understanding, we’ve extracted animations that visually demonstrate these processes. Learning Outcomes and Applications By the end of this episode, you’ll have gained: Advanced understanding of wet combustion simulation techniques Insights into DPM and combusting particle modeling in CFD Skills to interpret complex CFD results for multi-phase combustion systems Knowledge of how particle properties affect combustion dynamics These skills are directly applicable to: Designing efficient coal-fired power plants Optimizing biomass combustion systems Improving efficiency in industrial furnaces and boilers Advancing research in multi-phase combustion phenomena Join us in this cutting-edge exploration of wet combustion simulation using DPM and combusting particles in ANSYS Fluent. Elevate your CFD expertise to new heights in advanced combustion modeling and gain valuable insights into complex industrial processes!
-
Section 1
Concept
-
Master Combustion Fundamentals and ANSYS Fluent Modeling Techniques Dive into the world of combustion simulation with our comprehensive episode, “Combustion Concepts, ANSYS Fluent”. This foundational lesson is the first installment of our “Combustion: All Levels” course, designed to equip you with essential knowledge and skills for advanced CFD modeling. Episode Overview In this crucial introductory episode, we’ll lay the groundwork for your journey into combustion simulation. You’ll gain a solid understanding of combustion principles and discover how ANSYS Fluent can be leveraged to model complex combustion processes. What You'll Learn 1. Combustion Fundamentals - Explore the basic concepts and definitions of combustion - Understand the chemical and physical processes involved in combustion reactions - Learn about the importance of combustion in various industrial applications 2. Types of Combustion - Dive deep into premixed combustion scenarios and their characteristics - Explore non-premixed combustion and its unique challenges - Understand partially premixed combustion and its real-world applications 3. Physics of Combustion - Examine the underlying physical principles governing combustion processes - Learn about heat transfer, mass transfer, and fluid dynamics in combustion - Understand the role of turbulence in combustion phenomena 4. ANSYS Fluent Combustion Models - Get an overview of combustion modeling techniques available in ANSYS Fluent - Explore fast chemistry models for efficient simulations - Understand finite rate chemistry models for detailed reaction kinetics Why This Episode is Essential Build a strong foundation in combustion theory Gain insights into selecting appropriate combustion models for different scenarios Prepare for advanced combustion simulations in later episodes Who Should Watch This Episode? This episode is perfect for: Engineers new to combustion CFD Experienced CFD users looking to specialize in combustion modeling Researchers and students in thermal sciences and energy engineering Industry professionals seeking to enhance their combustion simulation skills Kickstart Your Combustion Modeling Journey By completing this episode, you’ll be equipped to: Understand the fundamental concepts of combustion processes Identify different types of combustion scenarios in real-world applications Navigate ANSYS Fluent’s combustion modeling capabilities Lay the groundwork for advanced combustion simulations in future lessons Don’t miss this opportunity to build a solid foundation in combustion modeling with ANSYS Fluent. Enroll now and ignite your expertise in combustion CFD!
Episode 1 9m 56s Free Episode
-
-
Section 2
Non-Premixed Combustion
$149.00-
Master Non-Premixed Combustion Simulation with Eddy Dissipation in ANSYS Fluent Dive deep into advanced combustion modeling with our comprehensive episode on “Non-Premixed Combustion, Eddy Dissipation, ANSYS Fluent CFD Training”. This hands-on tutorial is the second installment of our “Combustion: All Levels” course, designed to elevate your simulation skills to professional standards. Episode Overview In this practical session, you’ll learn to simulate non-premixed combustion in a combustion chamber using ANSYS Fluent. We’ll guide you through the entire process, from geometry creation to result analysis, focusing on the Eddy Dissipation model for turbulence-chemistry interactions. What You'll Learn 1. Geometry and Meshing - Create a 2D combustion chamber model using Design Modeler - Implement structured meshing techniques with ANSYS Meshing - Optimize mesh quality for combustion simulations 2. Combustion Model Setup - Configure the Species Transport model for non-premixed combustion - Set up the one-reaction methane-air mixture - Implement the Eddy Dissipation model for turbulence-chemistry interactions 3. Advanced Simulation Techniques - Enable and configure the Energy Equation for temperature calculations - Set up the Standard k-epsilon model for turbulence modeling - Optimize solver settings for combustion simulations 4. Result Analysis and Visualization - Generate and interpret temperature and velocity contours - Analyze species mass fraction distributions - Visualize and understand streamlines and secondary flows in the chamber Simulation Methodology Our step-by-step approach ensures you grasp every aspect of the simulation: Setting up the Species Transport model for non-premixed combustion Configuring the Eddy Dissipation model for accurate chemistry-turbulence interactions Implementing volumetric combustion modeling Optimizing mesh and solver settings for stability and accuracy Results and Analysis Learn to extract meaningful insights from your simulation: Interpret temperature contours to verify combustion occurrence Analyze velocity profiles and species distributions Understand the role of secondary flows in enhancing combustion efficiency Why This Episode is Essential Gain practical experience with real-world combustion chamber design Master the application of the Eddy Dissipation model in ANSYS Fluent Enhance your understanding of non-premixed combustion processes Develop skills applicable to various industrial combustion simulations Who Should Watch This Episode? This episode is perfect for: Mechanical and chemical engineers focusing on combustion systems CFD specialists looking to expand their combustion modeling skills Researchers in thermal sciences and energy engineering Graduate students pursuing advanced studies in combustion dynamics Take Your CFD Skills to the Next Level By completing this episode, you’ll be equipped to: Simulate complex non-premixed combustion scenarios Apply advanced turbulence-chemistry interaction models Analyze and optimize combustion chamber designs Elevate your CFD simulation capabilities in ANSYS Fluent Don’t miss this opportunity to master Non-Premixed Combustion Simulation using the Eddy Dissipation model in ANSYS Fluent. Enroll now and ignite your expertise in advanced combustion modeling!
Episode 1 36m 29s -
Non-Premixed Combustion, Non-Adiabatic, Chemical Equilibrium, ANSYS Fluent CFD Training Welcome to the third episode of our comprehensive “Combustion: All Levels” course. In this advanced lesson, we dive deep into the intricacies of non-premixed, non-adiabatic combustion simulation using ANSYS Fluent software. This episode focuses on chemical equilibrium modeling and provides valuable insights into real-world combustion scenarios. Simulation Overview Our simulation centers on a two-dimensional combustion chamber model, where we’ll investigate non-premixed combustion dynamics under non-adiabatic conditions. This episode aims to provide a thorough understanding of the complex interactions between fuel and air when introduced separately into the combustion chamber. Model Geometry and Meshing The foundation of our simulation lies in a carefully crafted model: Geometry designed using Design Modeler software for precision Meshing performed with ANSYS Meshing software Structured mesh type for optimal accuracy 63,280 elements ensuring detailed results and high-resolution analysis This meticulous setup ensures that our simulation captures the nuances of the non-premixed combustion process with high fidelity. Simulation Methodology Non-Premixed Combustion Model We employ the Non-Premixed Combustion model to simulate the combustion process effectively: Non-adiabatic energy treatment for realistic heat transfer modeling Chemical equilibrium approach for accurate species prediction Separate fuel and air inlets to simulate real-world combustion chambers This approach allows for a comprehensive analysis of the complex mixing and reaction processes occurring during non-premixed combustion. Probability Density Function (PDF) Table A key component of our simulation is the pre-generated PDF table: Stores data on temperature variations, mixture density, and species mass fractions Enhances computational efficiency during main calculations Provides a robust framework for chemical equilibrium modeling Additional Settings To ensure a comprehensive simulation, we also: Enable the Energy equation to track temperature changes accurately Utilize the Standard k-epsilon model for turbulence modeling Results and Analysis Upon completion of the simulation, we’ll analyze a range of outputs: Temperature distribution contours Velocity profiles throughout the chamber Mass fractions of various species Streamlines revealing flow patterns and mixing zones These results will provide valuable insights into: The progression of combustion in a non-premixed environment Temperature evolution due to non-adiabatic conditions Species formation and consumption patterns The role of secondary flows in enhancing mixing and combustion Learning Outcomes and Applications By the end of this episode, you’ll have gained: Advanced understanding of non-premixed, non-adiabatic combustion simulation techniques Insights into chemical equilibrium modeling in CFD Skills to interpret CFD results for complex combustion systems Knowledge of how secondary flows impact mixing and combustion efficiency These skills are directly applicable to: Designing more efficient industrial furnaces and combustors Optimizing fuel injection systems in gas turbines Improving combustion chamber designs for reduced emissions Advancing research in non-premixed combustion phenomena Join us in this cutting-edge exploration of non-premixed, non-adiabatic combustion simulation using ANSYS Fluent, and elevate your CFD expertise to new heights in combustion modeling!
Episode 2 16m 20s -
Non-premixed Combustion, Steady Diffusion Flamelet, ANSYS Fluent CFD Training Welcome to the fourth episode of our comprehensive “Combustion: All Levels” course. In this advanced lesson, we delve into the intricacies of non-premixed combustion simulation using ANSYS Fluent software, with a focus on the Steady Diffusion Flamelet model. This episode provides valuable insights into complex combustion processes commonly found in industrial applications. Simulation Overview Our simulation centers on a two-dimensional combustion chamber model, where we’ll investigate non-premixed combustion dynamics using a sophisticated CFD approach. This episode aims to provide in-depth understanding of the interaction between fuel and air when introduced separately into the combustion chamber, mimicking real-world scenarios. Model Geometry and Meshing The foundation of our simulation lies in a carefully crafted model: Geometry designed using Design Modeler software for precision Meshing performed with ANSYS Meshing software Structured mesh type for optimal accuracy 63,280 elements ensuring detailed results and high-resolution analysis This meticulous setup ensures that our simulation captures the nuances of the non-premixed combustion process with high fidelity. Simulation Methodology Non-Premixed Combustion Model We employ the Non-Premixed Combustion model to simulate the combustion process effectively: Non-adiabatic energy treatment for realistic heat transfer modeling Steady Diffusion Flamelet approach for accurate flame structure prediction Separate fuel and air inlets to simulate real-world combustion chambers This approach allows for a comprehensive analysis of the complex mixing and reaction processes occurring during non-premixed combustion. Chemkin Mechanism and Flamelet Generation A key component of our simulation is the use of a Chemkin mechanism: Imported into Fluent to create the flamelet Models the turbulent flame brush as an ensemble of discrete, steady laminar flames Provides a detailed representation of chemical kinetics Probability Density Function (PDF) Table To enhance computational efficiency, we generate a PDF table: Stores data on temperature variations, mixture density, and species mass fractions Pre-computed before the main simulation for faster calculations Allows for accurate representation of turbulence-chemistry interactions Additional Settings To ensure a comprehensive simulation, we also: Enable the Energy equation to track temperature changes accurately Utilize the Standard k-epsilon model for turbulence modeling Results and Analysis Upon completion of the simulation, we’ll analyze a range of outputs: Temperature distribution contours Velocity profiles throughout the chamber Mass fractions of various species Streamlines revealing flow patterns and mixing zones These results will provide valuable insights into: The structure and behavior of non-premixed flames Temperature evolution in different regions of the combustion chamber Species formation and consumption patterns The role of secondary flows in enhancing mixing and combustion efficiency Learning Outcomes and Applications By the end of this episode, you’ll have gained: Advanced understanding of non-premixed combustion simulation techniques Insights into the Steady Diffusion Flamelet model and its applications Skills to interpret CFD results for complex combustion systems Knowledge of how to use Chemkin mechanisms in Fluent for detailed chemistry modeling These skills are directly applicable to: Designing more efficient industrial burners and furnaces Optimizing fuel injection systems in gas turbines and diesel engines Improving combustion chamber designs for reduced emissions Advancing research in non-premixed combustion phenomena Join us in this cutting-edge exploration of non-premixed combustion simulation using the Steady Diffusion Flamelet model in ANSYS Fluent, and elevate your CFD expertise to new heights in advanced combustion modeling!
Episode 3 21m 20s
-
-
Section 3
Premixed Combustion
$149.00-
Premixed Combustion Eddy Dissipation CFD Simulation Welcome to the third episode of our “Combustion: All Levels” course. In this comprehensive lesson, we’ll dive deep into the world of premixed combustion simulation using ANSYS Fluent CFD software. This episode focuses on the Eddy Dissipation model and its application in combustion chamber analysis. Overview of the Simulation Our simulation revolves around a two-dimensional combustion chamber model, where we’ll explore the intricacies of premixed combustion. We’ll use the Species Transport model and employ the Eddy Dissipation approach to account for turbulence-chemistry interactions. Geometry and Meshing We begin by creating our model using Design Modeler software. The meshing process, a crucial step in CFD simulation, is performed using ANSYS Meshing software. Our model features: A structured mesh type 86,002 elements for accurate results Simulation Methodology Species Transport Model We utilize the Species Transport model to simulate the combustion process. This approach allows us to: Model a one-reaction methane-air mixture Use the volumetric option for chamber combustion modeling Eddy Dissipation Model The Eddy Dissipation model is key to our simulation, as it: Accounts for turbulence-chemistry interactions Focuses on mixing effects rather than detailed kinetic mechanisms Additional Settings To ensure a comprehensive simulation, we also: Enable the Energy equation to calculate temperature changes Set the Viscous model to Standard k-epsilon Simulation Results and Analysis Upon completion of the simulation, we’ll analyze various contours and data, including: Temperature distribution Velocity profiles Mass fractions of different species Streamlines showing secondary flows These results will provide insights into the combustion process, temperature increases, and the role of secondary flows in enhancing fuel-air mixing and combustion efficiency. Conclusion and Learning Outcomes By the end of this episode, you’ll have a solid understanding of: Premixed combustion simulation techniques The application of the Eddy Dissipation model in CFD Interpreting CFD results for combustion chamber analysis The importance of secondary flows in combustion processes Join us in this exciting exploration of premixed combustion simulation and take your CFD skills to the next level!
Episode 1 12m 40s -
Premixed Combustion (Eddy Dissipation/Finite Rate Model) for Pollution Formation CFD Simulation Welcome to the fourth episode of our “Combustion: All Levels” course. In this advanced lesson, we’ll explore the intricacies of premixed combustion simulation using ANSYS Fluent software, with a focus on pollution formation. This episode builds upon previous knowledge and introduces the combined Eddy Dissipation/Finite Rate model for a more comprehensive analysis. Simulation Overview Our simulation focuses on a two-dimensional combustion chamber model, where we’ll investigate premixed combustion dynamics and their impact on pollution formation. We’ll use cutting-edge CFD techniques to provide insights into real-world combustion scenarios. Model Setup and Meshing The foundation of our simulation lies in a carefully crafted model: Geometry designed using Design Modeler software Meshing performed with ANSYS Meshing software Structured mesh type for optimal accuracy 86,002 elements ensuring detailed results This meticulous setup ensures that our simulation captures the nuances of the combustion process. Simulation Methodology Species Transport Model We employ the Species Transport model to simulate the combustion process effectively: One-reaction methane-air mixture for simplicity and clarity Volumetric option to model combustion throughout the chamber Eddy Dissipation/Finite Rate Model The core of our simulation lies in the Eddy Dissipation/Finite Rate model: Accounts for turbulence-chemistry interactions Balances mixing effects with reaction rates Provides insights into pollution formation mechanisms This advanced model allows us to capture both mixing-limited and kinetically-limited aspects of the combustion process. Additional Settings To ensure a comprehensive simulation, we also: Enable the Energy equation to track temperature changes Utilize the Standard k-epsilon model for turbulence modeling Results and Analysis Upon completion of the simulation, we’ll analyze a range of outputs: Temperature distribution contours Velocity profiles throughout the chamber Mass fractions of various species, including pollutants Streamlines revealing secondary flow patterns These results will provide valuable insights into: Combustion efficiency and completeness Pollutant formation zones and mechanisms The role of secondary flows in mixing and combustion enhancement Learning Outcomes and Applications By the end of this episode, you’ll have gained: Advanced understanding of premixed combustion simulation techniques Insights into the Eddy Dissipation/Finite Rate model and its advantages Skills to interpret CFD results for pollution formation analysis Knowledge of how secondary flows impact combustion and pollution These skills are directly applicable to: Designing cleaner combustion systems Optimizing existing combustion chambers for reduced emissions Predicting and mitigating pollution in industrial processes Join us in this cutting-edge exploration of premixed combustion and pollution formation simulation, and take your CFD expertise to new heights!
Episode 2 32m 34s -
Premixed Combustion Finite Rate/No TCI Simulation Welcome to the fifth episode of our comprehensive “Combustion: All Levels” course. In this advanced lesson, we delve into the intricacies of premixed combustion simulation using ANSYS Fluent software, with a focus on the Finite Rate/No TCI (Turbulence-Chemistry Interaction) model. This episode builds upon previous knowledge and introduces a more detailed approach to combustion modeling. Simulation Overview Our simulation centers on a two-dimensional combustion chamber model, where we’ll investigate premixed combustion dynamics using a sophisticated CFD approach. This episode aims to provide in-depth insights into the chemical kinetics of combustion processes without considering turbulence-chemistry interactions. Model Geometry and Meshing The foundation of our simulation lies in a carefully crafted model: Geometry designed using Spaceclaim software for precision Meshing performed with ANSYS Meshing software Structured mesh type for optimal accuracy 4,800 elements ensuring detailed results while maintaining computational efficiency This meticulous setup ensures that our simulation captures the nuances of the combustion process with high fidelity. Simulation Methodology Species Transport Model We employ the Species Transport model to simulate the combustion process effectively: Utilization of a Chemkin mechanism file for detailed reaction modeling Incorporation of 35 different reactions and 17 chemical species Volumetric option to model combustion throughout the chamber This approach allows for a comprehensive analysis of the complex chemical processes occurring during combustion. Finite Rate/No TCI Model The core of our simulation lies in the Finite Rate/No TCI model: Focuses on detailed kinetic mechanisms Neglects the effect of turbulence on chemical reactions Provides insights into pure chemical kinetics of combustion This advanced model allows us to isolate and study the chemical aspects of combustion without the complicating factor of turbulence-chemistry interactions. Additional Settings To ensure a comprehensive simulation, we also: Enable the Energy equation to track temperature changes accurately Utilize the Standard k-epsilon model for turbulence modeling Results and Analysis Upon completion of the simulation, we’ll analyze a range of outputs: Temperature distribution contours Velocity profiles throughout the chamber Mass fractions of various species Streamlines revealing flow patterns These results will provide valuable insights into: The progression of chemical reactions in the combustion chamber Temperature evolution due to chemical kinetics Species formation and consumption patterns Learning Outcomes and Applications By the end of this episode, you’ll have gained: Advanced understanding of premixed combustion simulation techniques Insights into the Finite Rate/No TCI model and its applications Skills to interpret CFD results for detailed chemical kinetics analysis Knowledge of how to isolate and study chemical aspects of combustion These skills are directly applicable to: Developing more efficient combustion systems Optimizing fuel compositions for specific applications Understanding pollutant formation mechanisms at a chemical level Advancing research in combustion chemistry Join us in this cutting-edge exploration of premixed combustion simulation using the Finite Rate/No TCI model, and elevate your CFD expertise to new heights in chemical kinetics modeling!
Episode 3 16m 17s
-
-
Section 4
Advanced Combustion
$149.00-
Partially Premixed Combustion, Non-Adiabatic, Chemical Equilibrium, ANSYS Fluent CFD Training Welcome to the eighth episode of our comprehensive “Combustion: All Levels” course. In this advanced lesson, we delve into the complexities of partially premixed, non-adiabatic combustion simulation using ANSYS Fluent software. This episode focuses on chemical equilibrium modeling in a unique setup where pure air and a fuel-air mixture interact within the combustion chamber. Simulation Overview Our simulation centers on a two-dimensional combustion chamber model, where we’ll investigate the dynamics of partially premixed combustion under non-adiabatic conditions. This episode aims to provide a thorough understanding of the complex interactions between pure air and a pre-mixed fuel-air mixture, mimicking scenarios commonly found in advanced combustion systems. Model Geometry and Meshing The foundation of our simulation lies in a carefully crafted model: Geometry designed using Design Modeler software for precision Meshing performed with ANSYS Meshing software Structured mesh type for optimal accuracy 4,700 elements ensuring detailed results while maintaining computational efficiency This meticulous setup ensures that our simulation captures the nuances of the partially premixed combustion process with high fidelity. Simulation Methodology Partially Premixed Combustion Model We employ the Partially Premixed Combustion model to simulate the combustion process effectively: Non-adiabatic energy treatment for realistic heat transfer modeling Chemical equilibrium approach for accurate species prediction Separate inlets for pure air and fuel-air mixture to simulate advanced combustion systems Probability Density Function (PDF) Table A key component of our simulation is the pre-generated PDF table: Stores data on temperature variations, mixture density, and species mass fractions Enhances computational efficiency during main calculations Provides a robust framework for chemical equilibrium modeling Turbulent Flame Speed Model We utilize the Zimont model for the Turbulent Flame Speed: Accurately predicts flame propagation in turbulent flows Accounts for the interaction between turbulence and chemical reactions Simulation Stages Our simulation process is divided into two key stages: Cold flow simulation: Initial solution for flow patterns without combustion Combustion simulation: Enabling combustion equations and using the patch option for progress variable initialization Additional Settings To ensure a comprehensive simulation, we also: Enable the Energy equation to track temperature changes accurately Utilize the Standard k-epsilon model for turbulence modeling Results and Analysis Upon completion of the simulation, we’ll analyze a range of outputs: Temperature distribution contours Velocity profiles throughout the chamber Mass fractions of various species Streamlines revealing flow patterns and mixing zones These results will provide valuable insights into: The progression of combustion in a partially premixed environment Temperature evolution due to non-adiabatic conditions Species formation and consumption patterns The role of secondary flows in enhancing mixing and combustion Learning Outcomes and Applications By the end of this episode, you’ll have gained: Advanced understanding of partially premixed, non-adiabatic combustion simulation techniques Insights into chemical equilibrium modeling in CFD Skills to interpret CFD results for complex combustion systems Knowledge of how to simulate and analyze multi-stage combustion processes These skills are directly applicable to: Designing advanced gas turbine combustors Optimizing dual-fuel engine systems Improving combustion efficiency in industrial furnaces Advancing research in partially premixed combustion phenomena Join us in this cutting-edge exploration of partially premixed, non-adiabatic combustion simulation using ANSYS Fluent, and elevate your CFD expertise to new heights in advanced combustion modeling!
Episode 1 27m 31s -
Partially Premixed Combustion Composition PDF Transport Welcome to the ninth episode of our comprehensive “Combustion: All Levels” course. In this advanced lesson, we delve into the intricate world of partially premixed combustion and Composition PDF Transport using ANSYS Fluent software. This episode offers a unique exploration of complex combustion scenarios, combining multiple inlet conditions and sophisticated modeling techniques. Simulation Overview Our simulation focuses on a two-dimensional combustion chamber model with three distinct inlet boundaries: Pure air inlet Fuel-air mixture inlet Pilot inlet (combusted flow for activation energy) This setup allows us to investigate the intricate dynamics of partially premixed combustion in a controlled environment, mimicking advanced combustion systems found in industry. Model Geometry and Meshing The foundation of our simulation is a meticulously crafted model: Geometry designed using Design Modeler software for precision Meshing performed with ANSYS Meshing software Structured mesh type for optimal accuracy 2,352 elements ensuring detailed results while maintaining computational efficiency Simulation Methodology Our simulation process is divided into three distinct phases, each building upon the previous to achieve a comprehensive and accurate result. Phase 1: Partially Premixed Combustion Model In this initial stage, we: Utilize a Partially Premixed Combustion model Implement Non-Adiabatic energy treatment Apply a Chemical Equilibrium model for combustion processes Generate a PDF table for efficient data storage and retrieval Employ the Zimont model for turbulent flame speed calculations Phase 2: Composition PDF Transport Building on the initial solution, we: Enable Composition PDF Transport for more detailed modeling Incorporate a Chemkin Mechanism for comprehensive reaction modeling Implement ISAT (In Situ Adaptive Tabulation) along with Chemistry Agglomeration Balance simulation speed with acceptable error margins Phase 3: Final Accurate Solution In the final stage, we refine our results by: Disabling Chemistry Agglomeration for increased accuracy Continuing to utilize the ISAT table populated in Phase 2 Achieving a high-fidelity solution that captures complex combustion dynamics Additional Settings Throughout all phases, we maintain: Enabled Energy equation for accurate temperature change calculations Standard k-epsilon model for turbulence modeling Results and Analysis Upon completion of the simulation, we analyze a range of outputs including: Temperature distribution contours Velocity profiles throughout the chamber Mass fractions of various species Streamlines revealing flow patterns and mixing zones These results provide invaluable insights into: The progression of combustion in a partially premixed environment Temperature evolution across different chamber regions Species formation and consumption patterns The impact of the pilot inlet on overall combustion dynamics Learning Outcomes and Applications By the end of this episode, you’ll have gained: Advanced understanding of partially premixed combustion simulation techniques Insights into Composition PDF Transport modeling in CFD Skills to interpret complex CFD results for multi-inlet combustion systems Knowledge of balancing computational efficiency with simulation accuracy These skills are directly applicable to: Designing advanced gas turbine combustors Optimizing multi-fuel combustion systems Improving efficiency in industrial furnaces and boilers Advancing research in complex combustion phenomena Join us in this cutting-edge exploration of partially premixed combustion and Composition PDF Transport simulation using ANSYS Fluent, and elevate your CFD expertise to new heights in advanced combustion modeling!
Episode 2 38m 22s -
Wet Combustion Using DPM Combusting Particle CFD Simulation Welcome to this advanced episode of our “Combustion: All Levels” course. In this lesson, we delve into the intricate world of wet combustion simulation using the Discrete Phase Model (DPM) with combusting particles. This episode, which is the fourth chapter of our DPM training course, offers a unique exploration of complex combustion scenarios involving anthracite volatile in a combustion chamber. Project Overview Our simulation focuses on tracking fuel particles through the entire combustion process, from devolatilization to oxidation, resulting in the production of carbon dioxide and water vapor. This advanced model incorporates: A 2% liquid fraction in the fuel A 0.5-second injection duration Hot air introduction to the combustion chamber This setup allows us to investigate the intricate dynamics of wet combustion, mimicking real-world scenarios in advanced combustion systems. Simulation Methodology Our simulation employs a sophisticated approach to model the complex processes involved in wet combustion. Model Components We utilize a combination of advanced modeling techniques: Species Transport Model: For accurate tracking of chemical species Discrete Phase Model (DPM): To simulate anthracite particles Combusting Particle Type: With a 2% liquid fraction Particle Characteristics The anthracite particles are modeled with specific properties: Initial temperature: 325K Non-spherical shape Rosin-Rammler diameter distribution Geometry and Meshing The simulation environment is carefully crafted: Geometry designed using ANSYS Design Modeler software Unstructured mesh grid generated with ANSYS Meshing software Conversion to polyhedron cells for reduced computational costs Final mesh count: 810,000 cells Combustion Process and Reactions The wet combustion process in our simulation follows a specific sequence: Evaporation of the wet fraction of anthracite Release of the volatile fraction Oxidation of the volatile fraction The key reaction modeled is: 1An-vol + 2.207 O2 → 0.1 CO2 + 4.408 H2O This reaction leads to a significant temperature increase in the chamber, reaching up to 2400K. Results and Analysis Our simulation provides comprehensive insights into the wet combustion process: Temperature distribution throughout the combustion chamber Particle tracking from injection to complete combustion Species concentration profiles for O2, CO2, and H2O Energy release patterns during the combustion process To enhance understanding, we’ve extracted animations that visually demonstrate these processes. Learning Outcomes and Applications By the end of this episode, you’ll have gained: Advanced understanding of wet combustion simulation techniques Insights into DPM and combusting particle modeling in CFD Skills to interpret complex CFD results for multi-phase combustion systems Knowledge of how particle properties affect combustion dynamics These skills are directly applicable to: Designing efficient coal-fired power plants Optimizing biomass combustion systems Improving efficiency in industrial furnaces and boilers Advancing research in multi-phase combustion phenomena Join us in this cutting-edge exploration of wet combustion simulation using DPM and combusting particles in ANSYS Fluent. Elevate your CFD expertise to new heights in advanced combustion modeling and gain valuable insights into complex industrial processes!
Episode 3 29m 50s
-
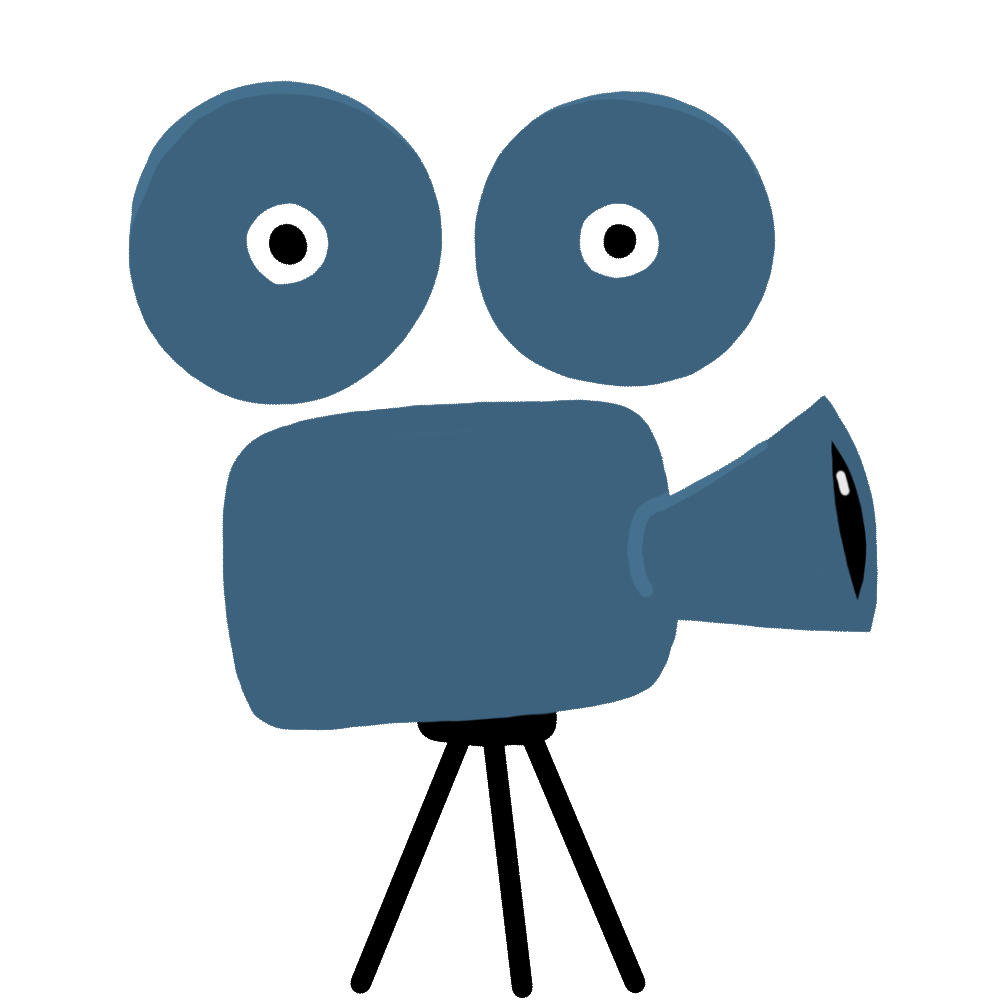
Course In Progress
Course still in development. Check back often for updates.
Master Combustion CFD Simulation: From Basics to Advanced Techniques
Unlock the power of computational fluid dynamics (CFD) in combustion analysis with our comprehensive “Combustion: All Levels” course. Whether you’re a beginner or an experienced engineer, this course will elevate your skills in modeling complex combustion processes using ANSYS Fluent.
Course Overview
Dive deep into the world of combustion simulation, covering everything from fundamental principles to advanced modeling techniques. This course is designed to transform you into a Combustion CFD Simulation expert through hands-on experience and in-depth theoretical knowledge.
What You'll Learn
1. Combustion Fundamentals
- Understand the physics of combustion processes - Explore different types of combustion: premixed, non-premixed, and partially premixed - Learn about various combustion applications in industry
2. ANSYS Fluent Mastery
- Set up and configure ANSYS Fluent for combustion simulations - Utilize species transport models for accurate combustion modeling - Implement various turbulence-chemistry interaction models
3. Advanced Simulation Techniques
- Model pollution formation (NOx, SOx, Soot) - Apply PDF transport models for complex combustion scenarios - Simulate wet combustion using DPM Combusting Particle models
4. Practical Applications
- Analyze combustion in various chamber designs - Optimize fuel and oxidant ratios for efficient energy release - Design and simulate efficient combustion chambers
Course Structure
Our course comprises 10 comprehensive video lessons, each focusing on specific aspects of combustion simulation:
- Introduction to Combustion and CFD Modeling
- Non-premixed Combustion with Eddy Dissipation
- Premixed Combustion Modeling
- Pollution Formation and Advanced Premixed Combustion
- Finite Rate Combustion Modeling
- Chemical Equilibrium in Non-premixed Combustion
- Steady Diffusion Flamelet Modeling
- Partially-premixed Combustion Simulation
- PDF Transport Model for Complex Combustion
- Wet Combustion and DPM Combusting Particle Model
Why Choose This Course?
- Gain hands-on experience with real-world combustion scenarios
- Learn from industry experts and cutting-edge research
- Access to comprehensive, step-by-step tutorials
- Develop skills applicable to various industries: power generation, aerospace, automotive, and more
- Earn a Combustion Certification upon course completion
Who Should Enroll?
This course is ideal for:
- Mechanical and chemical engineers
- CFD specialists and researchers
- Graduate students in engineering fields
- Industry professionals working with combustion systems
Transform Your Career in Combustion Engineering
By the end of this course, you’ll be equipped to:
- Perform high-fidelity combustion simulations
- Optimize combustion processes for efficiency and reduced emissions
- Tackle complex industrial combustion challenges
- Stand out in the competitive field of combustion engineering
Don’t miss this opportunity to become a Combustion CFD Simulation expert. Enroll now and ignite your career in advanced combustion modeling!
Buy Course
Benefits of buying the whole course
- Complete access to chapters Without Price
- Special discount
- Unlimited access to course content
- Free access to all new and updated content
- Access to course forever without any additional payment
* You can select chapters seperately, but you won't benefit from the list above.
* The items that do not have a price cannot be bought separately and are only available when you buy the whole course.
Congratulations
Congratulations! Your purchase was successful.
You can now start learning the course by clicking the button "Start Learning".
Add Payment Method
Please enter your payment method details.