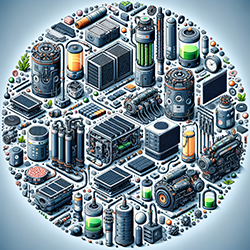
Fuel Cell: ANSYS Fluent CFD Simulation Training Course
Workshop
Price:
$1,350.00
$199.00
The “Fuel Cell: All Levels” CFD simulation training course by ANSYS Fluent offers a comprehensive journey through fuel cell modeling using advanced CFD techniques. Starting with fundamental concepts, the course progresses through various fuel cell types and configurations, including serpentine and radial PEMFCs, PEMFC stacks, and SOFCs with cooling systems and unresolved electrolytes. Participants gain hands-on experience in using ANSYS Fluent for fuel cell design optimization and performance analysis, applicable to diverse industrial and research scenarios.
Solid Oxide Fuel Cell (SOFC) Cooling System CFD Simulation
Solid Oxide Fuel Cell (SOFC) with Cooling System: Advanced CFD Simulation Using ANSYS Fluent Welcome to the sixth chapter of our comprehensive Fuel Cell Training Course, focusing on the CFD simulation of a Solid Oxide Fuel Cell (SOFC) with an integrated cooling system using ANSYS Fluent. This advanced module offers in-depth insights into modeling high-temperature fuel cells with thermal management solutions. Understanding SOFC with Cooling Systems Solid Oxide Fuel Cells operate at extremely high temperatures, necessitating effective cooling strategies. This simulation explores the complex interplay between electrochemical processes and thermal management in SOFCs. Key Components of an SOFC with Cooling Anode and cathode layers Electrolyte layer Current collectors and gas channels Cooling channels on both anode and cathode sides High-temperature operating environment Understanding these components and their interactions is crucial for accurate CFD modeling and performance analysis of thermally managed SOFC systems. CFD Methodology for SOFC with Cooling Simulation Our approach utilizes ANSYS Fluent’s advanced capabilities to create a comprehensive 3D model of the SOFC with integrated cooling channels. Simulation Process Overview 3D geometry creation using ANSYS Design Modeler Unstructured mesh generation with ANSYS Meshing (4,984,882 cells) Simulation setup in ANSYS Fluent using the SOFC model with coolant channel option Post-processing and analysis of electrochemical and thermal processes ANSYS Fluent SOFC Model Configuration with Cooling We employ the Fuel Cell and Electrolysis model, specifically the SOFC submodel, with additional cooling channel options to accurately simulate the electrochemical and thermal processes. Key Model Settings for SOFC with Cooling Simulation Layer definition including cooling channels Coolant channel option activation Species transport model for H2, O2, and H2O Electric and protonic potential equations Thermal management modeling in high-temperature conditions Advanced Analysis of SOFC with Cooling Simulation Results The CFD simulation provides valuable insights into the SOFC’s performance, internal processes, and thermal management effectiveness. Visualization of Key Parameters in SOFC with Cooling Our analysis focuses on critical fuel cell parameters and thermal characteristics, providing a comprehensive understanding of the system’s operation under thermal management. Contour Plots and Their Significance in SOFC with Cooling Design Temperature distribution across the cell and cooling channels Electric potential gradients with thermal effects Protonic potential variations in high-temperature operation Current flux density magnitude under thermal management Transfer current patterns with cooling influence Mass fractions of H2, O2, and H2O in thermally managed flow channels These visualizations offer deep insights into how the cooling system affects electrochemical reactions, transport phenomena, and overall system efficiency in high-temperature SOFCs. Interpretation of User-Defined Scalars (UDS) and Memories (UDM) for SOFC with Cooling ANSYS Fluent’s advanced features allow for detailed analysis of complex behaviors in thermally managed fuel cells. Key UDS and UDM Outputs in SOFC with Cooling Context Electric potential (UDS 0) distribution with thermal effects Protonic potential (UDS 1) variations under cooling influence Current flux density magnitude (UDM 3) in thermally managed configuration Transfer current (UDM 13) patterns with cooling system integration These outputs provide a comprehensive view of how the cooling system influences the fuel cell’s electrochemical performance and efficiency at high temperatures. Why SOFC with Cooling Simulation is Crucial for Advanced Energy Solutions This advanced CFD simulation of an SOFC with cooling offers: Insights into thermal management strategies for high-temperature fuel cells Understanding of the impact of cooling on electrochemical processes Analysis of efficiency improvements through effective thermal control Optimization opportunities for next-generation SOFC designs Applications and Benefits of SOFC with Cooling Simulation Improved overall system efficiency through optimized thermal management Enhanced understanding of material behavior under controlled high-temperature conditions Potential for extended SOFC lifespan through effective cooling Advancement in high-power, high-efficiency fuel cell applications Target Audience for SOFC with Cooling Simulation This module is ideal for: Fuel cell engineers focusing on high-temperature systems and thermal management Thermal engineers specializing in energy systems Clean energy researchers exploring advanced SOFC designs Advanced ANSYS Fluent users tackling complex multiphysics simulations Master the art of SOFC simulation with integrated cooling using ANSYS Fluent and contribute to the advancement of high-efficiency, thermally managed fuel cell technology. This comprehensive guide equips you with the skills to model, analyze, and optimize complex SOFC designs with cooling systems, pushing the boundaries of clean energy innovation for high-power applications.
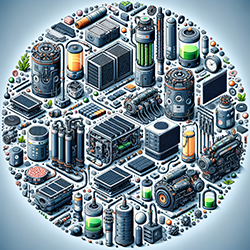
Fuel Cell: ANSYS Fluent CFD Simulation Training Course
Workshop
Price:
$1,350.00
$199.00
The “Fuel Cell: All Levels” CFD simulation training course by ANSYS Fluent offers a comprehensive journey through fuel cell modeling using advanced CFD techniques. Starting with fundamental concepts, the course progresses through various fuel cell types and configurations, including serpentine and radial PEMFCs, PEMFC stacks, and SOFCs with cooling systems and unresolved electrolytes. Participants gain hands-on experience in using ANSYS Fluent for fuel cell design optimization and performance analysis, applicable to diverse industrial and research scenarios.
Solid Oxide Fuel Cell (SOFC) Cooling System CFD Simulation
Solid Oxide Fuel Cell (SOFC) with Cooling System: Advanced CFD Simulation Using ANSYS Fluent Welcome to the sixth chapter of our comprehensive Fuel Cell Training Course, focusing on the CFD simulation of a Solid Oxide Fuel Cell (SOFC) with an integrated cooling system using ANSYS Fluent. This advanced module offers in-depth insights into modeling high-temperature fuel cells with thermal management solutions. Understanding SOFC with Cooling Systems Solid Oxide Fuel Cells operate at extremely high temperatures, necessitating effective cooling strategies. This simulation explores the complex interplay between electrochemical processes and thermal management in SOFCs. Key Components of an SOFC with Cooling Anode and cathode layers Electrolyte layer Current collectors and gas channels Cooling channels on both anode and cathode sides High-temperature operating environment Understanding these components and their interactions is crucial for accurate CFD modeling and performance analysis of thermally managed SOFC systems. CFD Methodology for SOFC with Cooling Simulation Our approach utilizes ANSYS Fluent’s advanced capabilities to create a comprehensive 3D model of the SOFC with integrated cooling channels. Simulation Process Overview 3D geometry creation using ANSYS Design Modeler Unstructured mesh generation with ANSYS Meshing (4,984,882 cells) Simulation setup in ANSYS Fluent using the SOFC model with coolant channel option Post-processing and analysis of electrochemical and thermal processes ANSYS Fluent SOFC Model Configuration with Cooling We employ the Fuel Cell and Electrolysis model, specifically the SOFC submodel, with additional cooling channel options to accurately simulate the electrochemical and thermal processes. Key Model Settings for SOFC with Cooling Simulation Layer definition including cooling channels Coolant channel option activation Species transport model for H2, O2, and H2O Electric and protonic potential equations Thermal management modeling in high-temperature conditions Advanced Analysis of SOFC with Cooling Simulation Results The CFD simulation provides valuable insights into the SOFC’s performance, internal processes, and thermal management effectiveness. Visualization of Key Parameters in SOFC with Cooling Our analysis focuses on critical fuel cell parameters and thermal characteristics, providing a comprehensive understanding of the system’s operation under thermal management. Contour Plots and Their Significance in SOFC with Cooling Design Temperature distribution across the cell and cooling channels Electric potential gradients with thermal effects Protonic potential variations in high-temperature operation Current flux density magnitude under thermal management Transfer current patterns with cooling influence Mass fractions of H2, O2, and H2O in thermally managed flow channels These visualizations offer deep insights into how the cooling system affects electrochemical reactions, transport phenomena, and overall system efficiency in high-temperature SOFCs. Interpretation of User-Defined Scalars (UDS) and Memories (UDM) for SOFC with Cooling ANSYS Fluent’s advanced features allow for detailed analysis of complex behaviors in thermally managed fuel cells. Key UDS and UDM Outputs in SOFC with Cooling Context Electric potential (UDS 0) distribution with thermal effects Protonic potential (UDS 1) variations under cooling influence Current flux density magnitude (UDM 3) in thermally managed configuration Transfer current (UDM 13) patterns with cooling system integration These outputs provide a comprehensive view of how the cooling system influences the fuel cell’s electrochemical performance and efficiency at high temperatures. Why SOFC with Cooling Simulation is Crucial for Advanced Energy Solutions This advanced CFD simulation of an SOFC with cooling offers: Insights into thermal management strategies for high-temperature fuel cells Understanding of the impact of cooling on electrochemical processes Analysis of efficiency improvements through effective thermal control Optimization opportunities for next-generation SOFC designs Applications and Benefits of SOFC with Cooling Simulation Improved overall system efficiency through optimized thermal management Enhanced understanding of material behavior under controlled high-temperature conditions Potential for extended SOFC lifespan through effective cooling Advancement in high-power, high-efficiency fuel cell applications Target Audience for SOFC with Cooling Simulation This module is ideal for: Fuel cell engineers focusing on high-temperature systems and thermal management Thermal engineers specializing in energy systems Clean energy researchers exploring advanced SOFC designs Advanced ANSYS Fluent users tackling complex multiphysics simulations Master the art of SOFC simulation with integrated cooling using ANSYS Fluent and contribute to the advancement of high-efficiency, thermally managed fuel cell technology. This comprehensive guide equips you with the skills to model, analyze, and optimize complex SOFC designs with cooling systems, pushing the boundaries of clean energy innovation for high-power applications.
-
Section 1
Concept
-
Mastering Fuel Cell Concepts in ANSYS Fluent: A Comprehensive Guide Welcome to the first chapter of our Fuel Cell Training Course, focusing on Fuel Cell Concepts in ANSYS Fluent. This foundational module provides a detailed introduction to fuel cell modeling, setting the stage for advanced simulations in computational fluid dynamics (CFD). Introduction to Fuel Cell Modeling in ANSYS Fluent ANSYS Fluent offers three powerful add-on modules for fuel cell simulation, each designed to address specific types of fuel cells and electrolyzers. Understanding these modules is crucial for effective CFD modeling of electrochemical systems. Available Fuel Cell Modules Fuel Cell and Electrolysis Model PEM Fuel Cell Model SOFC with Unresolved Electrolyte Model Each module caters to different fuel cell types, providing specialized tools for accurate simulations. Exploring the Fuel Cell and Electrolysis Model The Fuel Cell and Electrolysis model is a versatile tool, encompassing multiple sub-models for various electrochemical systems. Sub-models within the Fuel Cell and Electrolysis Model PEMFC (Proton Exchange Membrane Fuel Cell) SOFC (Solid Oxide Fuel Cell) Electrolysis This comprehensive model allows for the simulation of both fuel cells and electrolyzers, offering flexibility in electrochemical system modeling. Fundamental Fuel Cell Concepts Before diving into the software-specific aspects, it’s essential to grasp the core concepts of fuel cell technology. Key Components of Fuel Cell Configuration Overall structure and layering Electrochemistry principles Electrochemical reactions in fuel cells Critical properties and boundary conditions Understanding these fundamental aspects is crucial for accurate modeling and interpretation of simulation results. Advanced Modeling Features in ANSYS Fluent ANSYS Fluent provides powerful tools for detailed fuel cell modeling, including specialized user-defined functions. User-Defined Scalars (UDS) and Memories (UDM) These features allow for: Custom variable tracking Advanced performance analysis Tailored output for specific fuel cell parameters Mastering UDS and UDM usage is key to extracting maximum value from your fuel cell simulations. Why This Module is Essential for Fuel Cell CFD This introductory module lays the groundwork for all subsequent fuel cell simulations in ANSYS Fluent. By thoroughly understanding these concepts, you’ll be better equipped to: Choose the appropriate fuel cell model for your specific needs Set up accurate and efficient simulations Interpret results with greater insight and precision Target Audience This module is ideal for: CFD engineers new to fuel cell modeling Researchers exploring electrochemical system simulation Industry professionals seeking to enhance their ANSYS Fluent skills Learning Outcomes Upon completing this module, you will: Understand the different fuel cell models available in ANSYS Fluent Grasp fundamental fuel cell concepts and their relevance to CFD simulation Be prepared to set up basic fuel cell models in ANSYS Fluent Appreciate the role of advanced features like UDS and UDM in fuel cell modeling Start your journey into advanced fuel cell CFD simulation with this comprehensive introduction to Fuel Cell Concepts in ANSYS Fluent. Build a strong foundation for mastering complex electrochemical system modeling and contribute to the advancement of clean energy technologies!
Episode 1 1h 12m 18s Free Episode
-
-
Section 2
Serpentine Fuel Cell (PEMFC)
-
Serpentine PEMFC Fuel Cell: Advanced CFD Simulation with ANSYS Fluent Welcome to the second chapter of our comprehensive Fuel Cell Training Course, focusing on the CFD simulation of a Serpentine Proton Exchange Membrane Fuel Cell (PEMFC) using ANSYS Fluent. This advanced module offers in-depth insights into modeling complex fuel cell geometries and analyzing their performance. Understanding Serpentine PEMFC Fuel Cells Proton Exchange Membrane Fuel Cells (PEMFCs) are at the forefront of clean energy technology. The serpentine configuration, characterized by spiral gas flow channels, offers unique advantages in fuel cell design. Key Components of a PEMFC Anode and Cathode electrodes Electrolyte layer Catalyst layers Gas diffusion layers Current collectors Serpentine flow channels Understanding these components is crucial for accurate CFD modeling and performance analysis. CFD Methodology for Fuel Cell Simulation Our approach utilizes ANSYS Fluent’s advanced capabilities to create a comprehensive 3D model of the serpentine PEMFC. Simulation Process Overview Geometry creation using ANSYS Design Modeler Mesh generation with ANSYS Meshing (9,396,122 cells) Simulation setup in ANSYS Fluent Post-processing and result analysis ANSYS Fluent Fuel Cell Model Configuration We employ the Fuel Cell and Electrolysis model, specifically the PEMFC submodel, to accurately simulate the electrochemical processes. Key Model Settings Layer definition (anode, cathode, electrolyte) Species transport model activation (H2, O2, H2O) Electric and protonic potential equations Water content modeling Advanced Analysis of Simulation Results The CFD simulation provides valuable insights into the PEMFC’s performance and internal processes. Visualization of Key Parameters Our analysis focuses on critical fuel cell parameters, providing a comprehensive understanding of the PEMFC operation. Contour Plots and Their Significance Electric potential distribution Protonic potential variations Water content throughout the cell Current flux density magnitude Transfer current patterns Mass fractions of H2, O2, and H2O These visualizations offer deep insights into the electrochemical reactions and transport phenomena within the fuel cell. Interpretation of User-Defined Scalars (UDS) and Memories (UDM) ANSYS Fluent’s advanced features allow for detailed analysis of complex fuel cell behaviors. Key UDS and UDM Outputs Electric potential (UDS 0) Protonic potential (UDS 1) Water content (UDS 3) Current flux density magnitude (UDM 3) Transfer current (UDM 13) These outputs provide a comprehensive view of the fuel cell’s electrochemical performance and efficiency. Why This Simulation is Crucial for Fuel Cell Development This advanced CFD simulation of a serpentine PEMFC offers: Detailed insights into complex flow patterns in serpentine channels Understanding of water management in PEMFCs Analysis of current distribution and potential gradients Optimization opportunities for fuel cell design and performance Applications and Benefits Improved fuel cell efficiency and power output Enhanced understanding of internal fuel cell processes Optimization of serpentine channel designs Advancement in clean energy technology research Target Audience This module is ideal for: Fuel cell researchers and developers CFD engineers specializing in electrochemical systems Clean energy technology innovators Advanced ANSYS Fluent users focusing on complex simulations Master the art of serpentine PEMFC simulation with ANSYS Fluent and contribute to the advancement of fuel cell technology. This comprehensive guide equips you with the skills to model, analyze, and optimize complex fuel cell designs, pushing the boundaries of clean energy innovation.
Episode 1 35m 9s
-
-
Section 3
Radial Fuel Cell (PEMFC)
-
Radial PEMFC Fuel Cell: Advanced CFD Simulation Using ANSYS Fluent Welcome to the third chapter of our comprehensive Fuel Cell Training Course, focusing on the CFD simulation of a Radial Proton Exchange Membrane Fuel Cell (PEMFC) using ANSYS Fluent. This module offers in-depth insights into modeling unique fuel cell geometries and analyzing their performance. Understanding Radial PEMFC Fuel Cells Proton Exchange Membrane Fuel Cells (PEMFCs) are at the forefront of clean energy technology. The radial configuration, characterized by gas flow channels entering radially from the center and exiting at the periphery, presents unique advantages and challenges in fuel cell design. Key Components of a Radial PEMFC Anode and Cathode electrodes Electrolyte layer Catalyst layers Gas diffusion layers Current collectors Radial flow channels Understanding these components and their radial arrangement is crucial for accurate CFD modeling and performance analysis. CFD Methodology for Radial Fuel Cell Simulation Our approach utilizes ANSYS Fluent’s advanced capabilities to create a comprehensive 3D model of the radial PEMFC. Simulation Process Overview Geometry creation using ANSYS Design Modeler Mesh generation with ANSYS Meshing (2,393,706 cells) Simulation setup in ANSYS Fluent Post-processing and result analysis ANSYS Fluent Fuel Cell Model Configuration We employ the Fuel Cell and Electrolysis model, specifically the PEMFC submodel, to accurately simulate the electrochemical processes in the radial configuration. Key Model Settings Layer definition for radial geometry Species transport model activation (H2, O2, H2O) Electric and protonic potential equations Water content modeling in radial flow Advanced Analysis of Radial PEMFC Simulation Results The CFD simulation provides valuable insights into the radial PEMFC’s performance and internal processes, highlighting the unique aspects of this configuration. Visualization of Key Parameters in Radial Flow Our analysis focuses on critical fuel cell parameters, providing a comprehensive understanding of the radial PEMFC operation. Contour Plots and Their Significance in Radial Design Electric potential distribution across the radial plane Protonic potential variations from center to periphery Water content throughout the radial cell Current flux density magnitude in radial flow Transfer current patterns in radial configuration Mass fractions of H2, O2, and H2O along radial channels These visualizations offer deep insights into how the radial design affects electrochemical reactions and transport phenomena within the fuel cell. Interpretation of User-Defined Scalars (UDS) and Memories (UDM) for Radial PEMFC ANSYS Fluent’s advanced features allow for detailed analysis of complex behaviors unique to radial fuel cells. Key UDS and UDM Outputs in Radial Context Electric potential (UDS 0) distribution in radial geometry Protonic potential (UDS 1) variations from center to edge Water content (UDS 3) management in radial flow Current flux density magnitude (UDM 3) across radial plane Transfer current (UDM 13) patterns in radial configuration These outputs provide a comprehensive view of how the radial design influences the fuel cell’s electrochemical performance and efficiency. Why Radial PEMFC Simulation is Crucial for Fuel Cell Advancement This advanced CFD simulation of a radial PEMFC offers: Insights into unique flow patterns in radial channels Understanding of water management challenges in radial designs Analysis of current distribution and potential gradients in circular geometry Optimization opportunities specific to radial fuel cell designs Applications and Benefits of Radial PEMFC Simulation Improved fuel cell efficiency through optimized radial flow Enhanced understanding of mass transport in circular geometries Potential for compact and efficient fuel cell designs Advancement in specialized PEMFC applications Target Audience for Radial PEMFC Simulation This module is ideal for: Fuel cell researchers exploring novel geometries CFD engineers specializing in circular flow systems Clean energy technology innovators Advanced ANSYS Fluent users focusing on complex, non-traditional simulations Master the art of radial PEMFC simulation with ANSYS Fluent and contribute to the advancement of specialized fuel cell technology. This comprehensive guide equips you with the skills to model, analyze, and optimize radial fuel cell designs, pushing the boundaries of clean energy innovation in unique geometries.
Episode 1 36m 16s
-
-
Section 4
Stack Fuel Cell (PEMFC)
-
PEMFC Stack Fuel Cell System: Advanced CFD Simulation with ANSYS Fluent Welcome to the fourth chapter of our comprehensive Fuel Cell Training Course, focusing on the CFD simulation of a Proton Exchange Membrane Fuel Cell (PEMFC) Stack using ANSYS Fluent. This advanced module offers in-depth insights into modeling complex fuel cell systems and analyzing their performance at scale. Understanding PEMFC Stack Systems Proton Exchange Membrane Fuel Cell stacks represent a significant advancement in clean energy technology, combining multiple individual cells to generate substantial power output. This configuration presents unique challenges and opportunities for optimization. Key Components of a PEMFC Stack Multiple individual PEMFC units Interconnected anode and cathode layers Shared electrolyte systems Integrated cooling mechanisms Complex manifold designs for reactant distribution Understanding these components and their interactions is crucial for accurate CFD modeling and performance analysis of stack systems. CFD Methodology for Fuel Cell Stack Simulation Our approach utilizes ANSYS Fluent’s advanced capabilities to create a comprehensive 3D model of the PEMFC stack. Simulation Process Overview Geometry creation using ANSYS Design Modeler Mesh generation with ANSYS Meshing (9,046,409 cells) Simulation setup in ANSYS Fluent, including stack management Post-processing and result analysis for the entire stack ANSYS Fluent Fuel Cell Model Configuration for Stacks We employ the Fuel Cell and Electrolysis model, specifically the PEMFC submodel, with additional stack management features to accurately simulate the electrochemical processes across multiple cells. Key Model Settings for Stack Simulation Layer definition for multiple cells Stack management option activation Species transport model for H2, O2, and H2O across the stack Electric and protonic potential equations for interconnected cells Water management modeling in stack configuration Advanced Analysis of PEMFC Stack Simulation Results The CFD simulation provides valuable insights into the PEMFC stack’s performance and internal processes, highlighting the complexities of multi-cell systems. Visualization of Key Parameters in Stack Configuration Our analysis focuses on critical fuel cell parameters across the entire stack, providing a comprehensive understanding of the system’s operation. Contour Plots and Their Significance in Stack Design Electric potential distribution across multiple cells Protonic potential variations throughout the stack Water content management in interconnected cells Current flux density magnitude in stack configuration Transfer current patterns across the entire system Mass fractions of H2, O2, and H2O in stack flow channels These visualizations offer deep insights into how the stack configuration affects electrochemical reactions, transport phenomena, and overall system efficiency. Interpretation of User-Defined Scalars (UDS) and Memories (UDM) for PEMFC Stacks ANSYS Fluent’s advanced features allow for detailed analysis of complex behaviors unique to fuel cell stacks. Key UDS and UDM Outputs in Stack Context Electric potential (UDS 0) distribution across multiple cells Protonic potential (UDS 1) variations in interconnected systems Water content (UDS 3) management throughout the stack Current flux density magnitude (UDM 3) in stack configuration Transfer current (UDM 13) patterns across interconnected cells These outputs provide a comprehensive view of how the stack design influences the overall system’s electrochemical performance and efficiency. Why PEMFC Stack Simulation is Crucial for Large-Scale Energy Solutions This advanced CFD simulation of a PEMFC stack offers: Insights into scaling effects in multi-cell systems Understanding of reactant distribution and water management challenges in stacks Analysis of current distribution and potential gradients across interconnected cells Optimization opportunities for large-scale fuel cell applications Applications and Benefits of PEMFC Stack Simulation Improved overall system efficiency through optimized stack design Enhanced understanding of heat management in multi-cell configurations Potential for high-power output fuel cell systems Advancement in large-scale clean energy applications Target Audience for PEMFC Stack Simulation This module is ideal for: Fuel cell engineers working on large-scale energy projects CFD specialists focusing on complex, multi-unit systems Clean energy technology developers aiming for high-power applications Advanced ANSYS Fluent users tackling intricate, interconnected simulations Master the art of PEMFC stack simulation with ANSYS Fluent and contribute to the advancement of large-scale fuel cell technology. This comprehensive guide equips you with the skills to model, analyze, and optimize complex fuel cell stack designs, pushing the boundaries of clean energy innovation for high-power applications.
Episode 1 39m 46s
-
-
Section 5
Solid Oxide Fuel Cell (SOFC)
-
Solid Oxide Fuel Cell (SOFC) CFD Simulation: Advanced ANSYS Fluent Training Welcome to the fifth chapter of our comprehensive Fuel Cell Training Course, focusing on the CFD simulation of a Solid Oxide Fuel Cell (SOFC) using ANSYS Fluent. This advanced module offers in-depth insights into modeling high-temperature fuel cells and analyzing their unique performance characteristics. Understanding Solid Oxide Fuel Cells (SOFC) SOFCs represent a cutting-edge technology in the field of high-temperature fuel cells, offering exceptional efficiency and fuel flexibility. This simulation explores the complex internal processes of SOFCs, providing valuable insights for researchers and engineers. Key Components of an SOFC Cathode and anode sections Ceramic electrolyte layer Porous electrode layers Current collectors with gas channels High-temperature operating environment Understanding these components and their interactions at elevated temperatures is crucial for accurate CFD modeling and performance analysis of SOFC systems. CFD Methodology for SOFC Simulation Our approach utilizes ANSYS Fluent’s advanced capabilities to create a comprehensive 3D model of the SOFC, focusing on the unique aspects of high-temperature operation. Simulation Process Overview 3D geometry creation using ANSYS Design Modeler Structured mesh generation with ANSYS Meshing (930,240 cells) Simulation setup in ANSYS Fluent using the “SOFC with unresolved electrolyte” model Post-processing and analysis of high-temperature electrochemical processes ANSYS Fluent SOFC Model Configuration We employ the “SOFC with unresolved electrolyte” model, a specialized add-on module in ANSYS Fluent, to accurately simulate the complex electrochemical processes in high-temperature conditions. Key Model Settings for SOFC Simulation Electrolyte layer defined as an interface (wall and wall shadow) Automatic application of source and sink terms Electric current set to 10 Amp Porous electrode layers with 0.5 porosity and 2 tortuosity Conductivity of 0.1 S/m in collector and electrode layers Species transport model for H2, O2, and H2O Advanced Analysis of SOFC Simulation Results The CFD simulation provides valuable insights into the SOFC’s performance and internal processes, highlighting the unique aspects of high-temperature fuel cell operation. Visualization of Key Parameters in SOFC Our analysis focuses on critical fuel cell parameters specific to SOFC operation, providing a comprehensive understanding of the system’s electrochemistry at high temperatures. Contour Plots and Their Significance in SOFC Design Oxygen, hydrogen, and water concentration distributions Electric potential gradients across the cell Electric current generation and flow patterns Temperature distribution and its effects on reactions These visualizations offer deep insights into how high-temperature operation affects electrochemical reactions, ion transport, and overall system efficiency in SOFCs. Interpretation of Electrochemical Processes in SOFC The simulation results provide a detailed view of the complex interactions within the SOFC, crucial for optimizing high-temperature fuel cell designs. Key Insights from SOFC Simulation Oxygen ion transport through the ceramic electrolyte Water formation on the anode side Electric current generation and distribution Impact of high temperature on reaction kinetics and efficiency These outputs provide a comprehensive view of how the SOFC design and operating conditions influence the overall system’s electrochemical performance and efficiency at elevated temperatures. Why SOFC Simulation is Crucial for Advanced Energy Solutions This advanced CFD simulation of an SOFC offers: Insights into high-temperature electrochemical processes Understanding of material behavior under extreme conditions Analysis of fuel flexibility and efficiency in SOFCs Optimization opportunities for next-generation fuel cell technologies Applications and Benefits of SOFC Simulation Improved overall system efficiency through optimized high-temperature operation Enhanced understanding of ceramic electrolyte performance Potential for integration with various fuel sources Advancement in stationary power generation and industrial applications Target Audience for SOFC Simulation This module is ideal for: Fuel cell engineers specializing in high-temperature systems Materials scientists working on ceramic electrolytes Energy researchers focused on efficient power generation Advanced ANSYS Fluent users tackling complex electrochemical simulations Master the art of SOFC simulation with ANSYS Fluent and contribute to the advancement of high-temperature fuel cell technology. This comprehensive guide equips you with the skills to model, analyze, and optimize complex SOFC designs, pushing the boundaries of clean energy innovation for high-efficiency power generation.
Episode 1 44m 22s
-
-
Section 6
Cooling System (SOFC)
-
Solid Oxide Fuel Cell (SOFC) with Cooling System: Advanced CFD Simulation Using ANSYS Fluent Welcome to the sixth chapter of our comprehensive Fuel Cell Training Course, focusing on the CFD simulation of a Solid Oxide Fuel Cell (SOFC) with an integrated cooling system using ANSYS Fluent. This advanced module offers in-depth insights into modeling high-temperature fuel cells with thermal management solutions. Understanding SOFC with Cooling Systems Solid Oxide Fuel Cells operate at extremely high temperatures, necessitating effective cooling strategies. This simulation explores the complex interplay between electrochemical processes and thermal management in SOFCs. Key Components of an SOFC with Cooling Anode and cathode layers Electrolyte layer Current collectors and gas channels Cooling channels on both anode and cathode sides High-temperature operating environment Understanding these components and their interactions is crucial for accurate CFD modeling and performance analysis of thermally managed SOFC systems. CFD Methodology for SOFC with Cooling Simulation Our approach utilizes ANSYS Fluent’s advanced capabilities to create a comprehensive 3D model of the SOFC with integrated cooling channels. Simulation Process Overview 3D geometry creation using ANSYS Design Modeler Unstructured mesh generation with ANSYS Meshing (4,984,882 cells) Simulation setup in ANSYS Fluent using the SOFC model with coolant channel option Post-processing and analysis of electrochemical and thermal processes ANSYS Fluent SOFC Model Configuration with Cooling We employ the Fuel Cell and Electrolysis model, specifically the SOFC submodel, with additional cooling channel options to accurately simulate the electrochemical and thermal processes. Key Model Settings for SOFC with Cooling Simulation Layer definition including cooling channels Coolant channel option activation Species transport model for H2, O2, and H2O Electric and protonic potential equations Thermal management modeling in high-temperature conditions Advanced Analysis of SOFC with Cooling Simulation Results The CFD simulation provides valuable insights into the SOFC’s performance, internal processes, and thermal management effectiveness. Visualization of Key Parameters in SOFC with Cooling Our analysis focuses on critical fuel cell parameters and thermal characteristics, providing a comprehensive understanding of the system’s operation under thermal management. Contour Plots and Their Significance in SOFC with Cooling Design Temperature distribution across the cell and cooling channels Electric potential gradients with thermal effects Protonic potential variations in high-temperature operation Current flux density magnitude under thermal management Transfer current patterns with cooling influence Mass fractions of H2, O2, and H2O in thermally managed flow channels These visualizations offer deep insights into how the cooling system affects electrochemical reactions, transport phenomena, and overall system efficiency in high-temperature SOFCs. Interpretation of User-Defined Scalars (UDS) and Memories (UDM) for SOFC with Cooling ANSYS Fluent’s advanced features allow for detailed analysis of complex behaviors in thermally managed fuel cells. Key UDS and UDM Outputs in SOFC with Cooling Context Electric potential (UDS 0) distribution with thermal effects Protonic potential (UDS 1) variations under cooling influence Current flux density magnitude (UDM 3) in thermally managed configuration Transfer current (UDM 13) patterns with cooling system integration These outputs provide a comprehensive view of how the cooling system influences the fuel cell’s electrochemical performance and efficiency at high temperatures. Why SOFC with Cooling Simulation is Crucial for Advanced Energy Solutions This advanced CFD simulation of an SOFC with cooling offers: Insights into thermal management strategies for high-temperature fuel cells Understanding of the impact of cooling on electrochemical processes Analysis of efficiency improvements through effective thermal control Optimization opportunities for next-generation SOFC designs Applications and Benefits of SOFC with Cooling Simulation Improved overall system efficiency through optimized thermal management Enhanced understanding of material behavior under controlled high-temperature conditions Potential for extended SOFC lifespan through effective cooling Advancement in high-power, high-efficiency fuel cell applications Target Audience for SOFC with Cooling Simulation This module is ideal for: Fuel cell engineers focusing on high-temperature systems and thermal management Thermal engineers specializing in energy systems Clean energy researchers exploring advanced SOFC designs Advanced ANSYS Fluent users tackling complex multiphysics simulations Master the art of SOFC simulation with integrated cooling using ANSYS Fluent and contribute to the advancement of high-efficiency, thermally managed fuel cell technology. This comprehensive guide equips you with the skills to model, analyze, and optimize complex SOFC designs with cooling systems, pushing the boundaries of clean energy innovation for high-power applications.
Episode 1 43m 47s
-
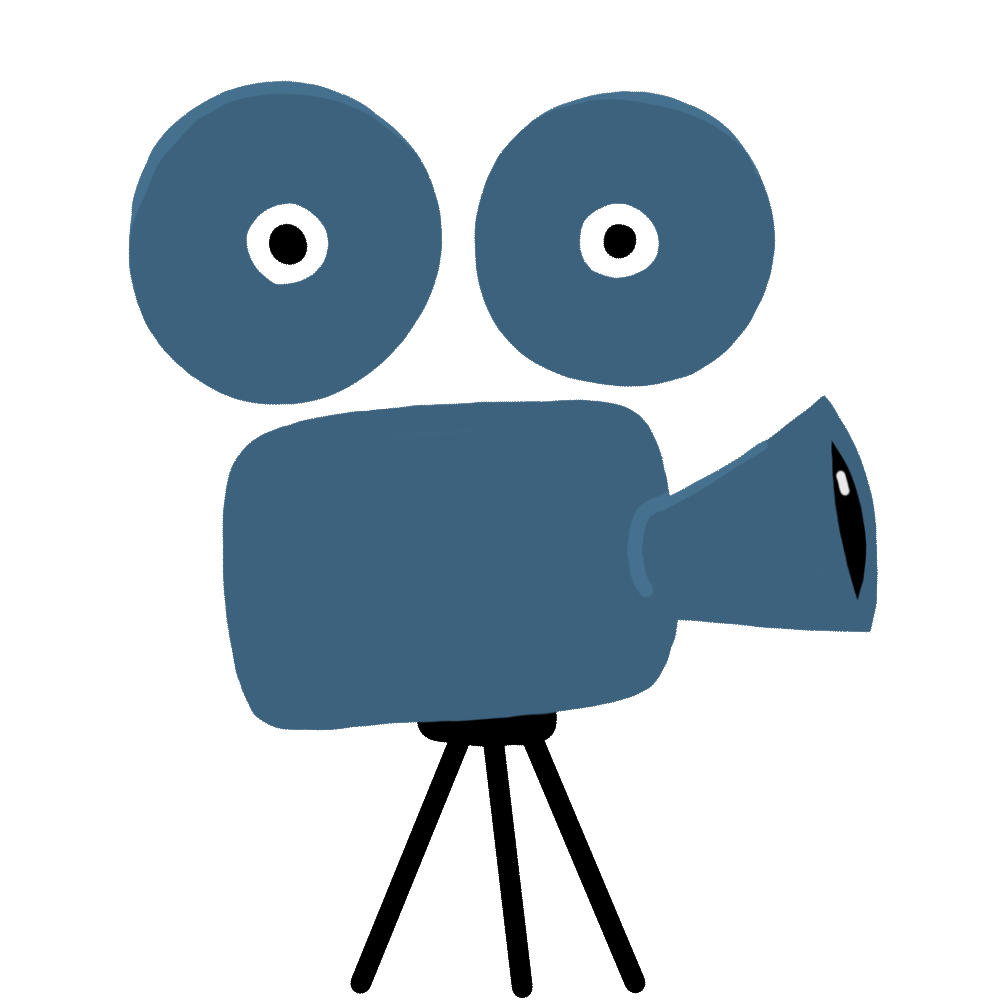
Course In Progress
Course still in development. Check back often for updates.
ANSYS Fluent Fuel Cell CFD Simulation: Comprehensive Training Course
Welcome to our advanced “Fuel Cell: All Levels” CFD simulation training course powered by ANSYS Fluent. This comprehensive program is designed to equip you with the skills necessary to master fuel cell modeling using cutting-edge computational fluid dynamics techniques.
Course Overview
Our training package covers a wide range of fuel cell types and modeling approaches, providing you with a robust foundation in fuel cell simulation. From basic concepts to complex stack configurations, this course offers hands-on experience with ANSYS Fluent’s powerful fuel cell modules.
ANSYS Fluent Fuel Cell Models
The course explores three main fuel cell models available in ANSYS Fluent:
- Fuel Cell and Electrolysis model (with PEMFC and SOFC sub-models)
- PEM Fuel Cell model
- SOFC with Unresolved Electrolyte model
Course Structure
Our carefully crafted syllabus ensures a logical progression through fuel cell simulation concepts and practical applications.
Chapter 1: Fuel Cell Concepts
This foundational chapter covers:
- Introduction to fuel cell principles
- Electrochemical reactions and equations
- Fuel cell properties
- User-Defined Scalars (UDSs) and User-Defined Memories (UDMs)
- Detailed overview of ANSYS Fluent fuel cell modules
Chapter 2: Serpentine PEMFC Fuel Cell
Learn to simulate a Serpentine Fuel Cell using the “fuel cell and electrolysis” model with the PEMFC submodel. This chapter focuses on modeling gas flow channels in a serpentine arrangement.
Chapter 3: Radial PEMFC Fuel Cell
Master the CFD simulation of a Radial Fuel Cell, exploring the unique challenges of modeling fuel cells with radial layer configurations.
Chapter 4: Fuel Cell PEMFC Stack
Advance your skills by simulating a Fuel Cell Stack, learning how to model multiple fuel cell units mounted together for increased power output.
Chapter 5: Fuel Cell SOFC with Cooling System
Tackle the complexities of high-temperature fuel cells by simulating an SOFC with an integrated cooling system using the SOFC submodel.
Chapter 6: SOFC with Unresolved Electrolyte
Explore advanced modeling techniques for solid-oxide fuel cells using the “SOFC with Unresolved Electrolyte” model, focusing on simulations where the electrolyte layer is not included in the computational domain.
Why Choose Our Fuel Cell CFD Training Course?
Our comprehensive training package offers:
- In-depth understanding of various fuel cell types and configurations
- Hands-on experience with ANSYS Fluent’s advanced fuel cell modules
- Practical skills applicable to real-world fuel cell design and optimization
- Progressive learning path from basic concepts to complex stack simulations
Target Audience
This course is ideal for:
- Engineers and researchers in the renewable energy sector
- CFD specialists focusing on electrochemical systems
- Industry professionals involved in fuel cell development and optimization
- Academic researchers exploring advanced energy conversion technologies
Learning Outcomes
By the end of this course, you will be able to:
- Set up and run sophisticated fuel cell simulations in ANSYS Fluent
- Analyze and optimize various fuel cell designs, from single cells to stacks
- Interpret complex CFD results for fuel cell performance improvement
- Apply advanced modeling techniques to cutting-edge fuel cell technologies
Elevate your fuel cell simulation skills with our comprehensive ANSYS Fluent training course. Master the art of fuel cell CFD modeling and contribute to the advancement of clean energy technologies!
Buy Course
Benefits of buying the whole course
- Complete access to chapters Without Price
- Special discount
- Unlimited access to course content
- Free access to all new and updated content
- Access to course forever without any additional payment
* You can select chapters seperately, but you won't benefit from the list above.
* The items that do not have a price cannot be bought separately and are only available when you buy the whole course.
Congratulations
Congratulations! Your purchase was successful.
You can now start learning the course by clicking the button "Start Learning".
Add Payment Method
Please enter your payment method details.