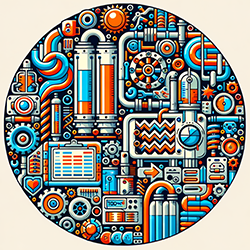
Heat Exchanger, Beginner: CFD Simulation Training Course
Course Price: $1.00 / Month
Dive into the world of heat exchanger design and analysis with our comprehensive ANSYS Fluent CFD Simulation Training course. Perfect for beginners, this hands-on program covers a wide range of heat exchanger types, from chevron plate and spiral designs to shell and tube configurations. Learn to simulate and optimize heat transfer processes using cutting-edge CFD techniques. Master the essentials of ANSYS Fluent while exploring ten diverse heat exchanger categories, including reverse cross flow, finned tube, and planar designs with mixing tabs. Ideal for engineers and students looking to enhance their skills in thermal system analysis and design. Join us to transform your understanding of heat exchangers through the power of computational fluid dynamics.
Finned Tube Heat Exchanger CFD Simulation
Mastering Finned Tube Heat Exchanger CFD Simulation: A Comprehensive Guide for Beginners Welcome to the “Finned Tube Heat Exchanger CFD Simulation” episode of our “Heat Exchanger: BEGINNER” course. This in-depth module introduces learners to the world of Computational Fluid Dynamics (CFD) for analyzing highly efficient Finned Tube Heat Exchangers using ANSYS Fluent. Discover how to simulate and evaluate these crucial heat transfer devices, widely used in HVAC systems, power plants, and automotive radiators. Understanding Finned Tube Heat Exchangers: Fundamentals and Applications Before diving into simulation techniques, let’s explore the core concepts of Finned Tube Heat Exchangers and their significance in modern thermal management. The Advantages of Extended Surface Heat Transfer Discover how Finned Tube Heat Exchangers significantly increase heat transfer surface area, enhancing overall thermal efficiency in various industrial applications. Key Design Features of Finned Tube Heat Exchangers Explore the unique characteristics of these heat exchangers, including fin geometry, spacing, and arrangement, and how they contribute to superior performance across different industries. Introduction to ANSYS Fluent for Finned Tube Heat Exchanger Analysis This section focuses on familiarizing users with the ANSYS Fluent software environment for finned tube heat exchanger simulations: Navigating the ANSYS Fluent Interface for Finned Geometries Gain insights into the specialized tools and features of ANSYS Fluent essential for efficient simulation setup and analysis of Finned Tube Heat Exchangers. Understanding the CFD Workflow for Extended Surface Heat Exchangers Learn the step-by-step process of setting up, running, and analyzing a Finned Tube Heat Exchanger CFD simulation in ANSYS Fluent. Setting Up a Finned Tube Heat Exchanger Model Master the art of creating an accurate simulation environment for Finned Tube Heat Exchanger analysis: Defining Complex Geometry for Finned Tube Configurations Learn techniques for creating a detailed geometry representing a Finned Tube Heat Exchanger, focusing on the critical features that influence performance. Configuring Material Properties and Fluid Domains Explore methods for defining and implementing the properties of working fluids and fin materials in your simulation, considering the unique requirements of extended surface designs. Boundary Conditions for Finned Tube Heat Exchanger Scenarios Dive into the critical settings that ensure realistic representation of heat transfer and fluid flow in finned configurations: Specifying Inlet and Outlet Conditions for Air and Tube-side Fluids Understand how to set up appropriate inlet flow rates, temperatures, and outlet conditions for both air-side and tube-side fluids in a finned tube arrangement. Implementing Wall and Fin Surface Boundary Conditions Learn to define proper boundary conditions for tube surfaces, fin surfaces, and fluid interfaces to capture realistic heat transfer behavior in extended surface geometries. Running CFD Simulations for Finned Tube Heat Exchangers Develop skills to execute and monitor Finned Tube Heat Exchanger CFD simulations: Setting Up Solver Parameters for Complex Fin Geometries Master the configuration of solver settings, including turbulence models suitable for capturing flow patterns around finned surfaces. Managing Simulation Progress and Ensuring Convergence Learn techniques for tracking simulation progress, identifying potential issues, and ensuring solution stability in complex finned geometries. Analyzing Flow Patterns and Heat Transfer Performance Develop expertise in extracting meaningful insights from your Finned Tube Heat Exchanger simulations: Visualizing Airflow Structures and Temperature Distributions Master techniques for creating insightful visualizations of velocity fields and temperature contours to understand the behavior of Finned Tube Heat Exchangers. Interpreting Heat Transfer Coefficients and Pressure Drop Characteristics Learn to analyze key performance metrics, including local and overall heat transfer coefficients and pressure drop, crucial for assessing the efficiency of finned designs. Comparative Analysis: Fin Geometry and Arrangement Optimization Explore the performance differences between various fin designs and configurations: Evaluating the Impact of Fin Spacing on Heat Transfer Gain insights into how fin spacing affects heat transfer rates and airflow patterns in Finned Tube Heat Exchangers. Assessing the Influence of Fin Shape on Overall Performance Learn to analyze the effects of different fin shapes (e.g., plain, wavy, louvered) on heat exchanger efficiency and pressure drop. Practical Applications and Design Optimization Connect simulation insights to real-world heat exchanger applications and design improvements: Applying CFD Insights to Finned Tube Heat Exchanger Design Explore how the complex flow patterns and heat transfer characteristics observed in CFD simulations can inform design decisions and performance enhancements. Optimizing Fin Geometry for Specific Industrial Applications Learn to use simulation results to optimize fin designs for various scenarios, balancing heat transfer efficiency with manufacturing considerations and pressure drop constraints. Why This Module is Essential for Thermal Engineers and HVAC Professionals This comprehensive module offers an in-depth exploration of CFD techniques for Finned Tube Heat Exchanger analysis. By completing this simulation course, you’ll gain valuable insights into: Advanced application of ANSYS Fluent for simulating extended surface heat exchanger designs Essential CFD techniques for capturing complex flow phenomena and heat transfer mechanisms in finned geometries Practical applications of CFD analysis in optimizing Finned Tube Heat Exchangers for various industries By the end of this episode, you’ll have developed advanced skills in: Setting up and running detailed Finned Tube Heat Exchanger simulations using ANSYS Fluent Interpreting complex simulation results to assess and improve heat exchanger performance Applying sophisticated CFD insights to enhance the design and efficiency of Finned Tube Heat Exchangers This knowledge forms a robust foundation for thermal engineers, HVAC professionals, and researchers looking to leverage advanced computational methods in heat exchanger design and analysis, providing a pathway to innovation in thermal system engineering. Join us on this exciting journey into the world of Finned Tube Heat Exchanger CFD simulation, and elevate your skills in advanced thermal system design and optimization using cutting-edge computational tools!
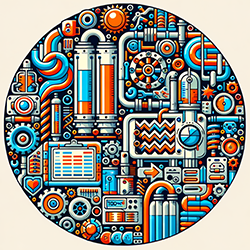
Heat Exchanger, Beginner: CFD Simulation Training Course
Course Price: $1.00 / Month
Dive into the world of heat exchanger design and analysis with our comprehensive ANSYS Fluent CFD Simulation Training course. Perfect for beginners, this hands-on program covers a wide range of heat exchanger types, from chevron plate and spiral designs to shell and tube configurations. Learn to simulate and optimize heat transfer processes using cutting-edge CFD techniques. Master the essentials of ANSYS Fluent while exploring ten diverse heat exchanger categories, including reverse cross flow, finned tube, and planar designs with mixing tabs. Ideal for engineers and students looking to enhance their skills in thermal system analysis and design. Join us to transform your understanding of heat exchangers through the power of computational fluid dynamics.
Finned Tube Heat Exchanger CFD Simulation
Mastering Finned Tube Heat Exchanger CFD Simulation: A Comprehensive Guide for Beginners Welcome to the “Finned Tube Heat Exchanger CFD Simulation” episode of our “Heat Exchanger: BEGINNER” course. This in-depth module introduces learners to the world of Computational Fluid Dynamics (CFD) for analyzing highly efficient Finned Tube Heat Exchangers using ANSYS Fluent. Discover how to simulate and evaluate these crucial heat transfer devices, widely used in HVAC systems, power plants, and automotive radiators. Understanding Finned Tube Heat Exchangers: Fundamentals and Applications Before diving into simulation techniques, let’s explore the core concepts of Finned Tube Heat Exchangers and their significance in modern thermal management. The Advantages of Extended Surface Heat Transfer Discover how Finned Tube Heat Exchangers significantly increase heat transfer surface area, enhancing overall thermal efficiency in various industrial applications. Key Design Features of Finned Tube Heat Exchangers Explore the unique characteristics of these heat exchangers, including fin geometry, spacing, and arrangement, and how they contribute to superior performance across different industries. Introduction to ANSYS Fluent for Finned Tube Heat Exchanger Analysis This section focuses on familiarizing users with the ANSYS Fluent software environment for finned tube heat exchanger simulations: Navigating the ANSYS Fluent Interface for Finned Geometries Gain insights into the specialized tools and features of ANSYS Fluent essential for efficient simulation setup and analysis of Finned Tube Heat Exchangers. Understanding the CFD Workflow for Extended Surface Heat Exchangers Learn the step-by-step process of setting up, running, and analyzing a Finned Tube Heat Exchanger CFD simulation in ANSYS Fluent. Setting Up a Finned Tube Heat Exchanger Model Master the art of creating an accurate simulation environment for Finned Tube Heat Exchanger analysis: Defining Complex Geometry for Finned Tube Configurations Learn techniques for creating a detailed geometry representing a Finned Tube Heat Exchanger, focusing on the critical features that influence performance. Configuring Material Properties and Fluid Domains Explore methods for defining and implementing the properties of working fluids and fin materials in your simulation, considering the unique requirements of extended surface designs. Boundary Conditions for Finned Tube Heat Exchanger Scenarios Dive into the critical settings that ensure realistic representation of heat transfer and fluid flow in finned configurations: Specifying Inlet and Outlet Conditions for Air and Tube-side Fluids Understand how to set up appropriate inlet flow rates, temperatures, and outlet conditions for both air-side and tube-side fluids in a finned tube arrangement. Implementing Wall and Fin Surface Boundary Conditions Learn to define proper boundary conditions for tube surfaces, fin surfaces, and fluid interfaces to capture realistic heat transfer behavior in extended surface geometries. Running CFD Simulations for Finned Tube Heat Exchangers Develop skills to execute and monitor Finned Tube Heat Exchanger CFD simulations: Setting Up Solver Parameters for Complex Fin Geometries Master the configuration of solver settings, including turbulence models suitable for capturing flow patterns around finned surfaces. Managing Simulation Progress and Ensuring Convergence Learn techniques for tracking simulation progress, identifying potential issues, and ensuring solution stability in complex finned geometries. Analyzing Flow Patterns and Heat Transfer Performance Develop expertise in extracting meaningful insights from your Finned Tube Heat Exchanger simulations: Visualizing Airflow Structures and Temperature Distributions Master techniques for creating insightful visualizations of velocity fields and temperature contours to understand the behavior of Finned Tube Heat Exchangers. Interpreting Heat Transfer Coefficients and Pressure Drop Characteristics Learn to analyze key performance metrics, including local and overall heat transfer coefficients and pressure drop, crucial for assessing the efficiency of finned designs. Comparative Analysis: Fin Geometry and Arrangement Optimization Explore the performance differences between various fin designs and configurations: Evaluating the Impact of Fin Spacing on Heat Transfer Gain insights into how fin spacing affects heat transfer rates and airflow patterns in Finned Tube Heat Exchangers. Assessing the Influence of Fin Shape on Overall Performance Learn to analyze the effects of different fin shapes (e.g., plain, wavy, louvered) on heat exchanger efficiency and pressure drop. Practical Applications and Design Optimization Connect simulation insights to real-world heat exchanger applications and design improvements: Applying CFD Insights to Finned Tube Heat Exchanger Design Explore how the complex flow patterns and heat transfer characteristics observed in CFD simulations can inform design decisions and performance enhancements. Optimizing Fin Geometry for Specific Industrial Applications Learn to use simulation results to optimize fin designs for various scenarios, balancing heat transfer efficiency with manufacturing considerations and pressure drop constraints. Why This Module is Essential for Thermal Engineers and HVAC Professionals This comprehensive module offers an in-depth exploration of CFD techniques for Finned Tube Heat Exchanger analysis. By completing this simulation course, you’ll gain valuable insights into: Advanced application of ANSYS Fluent for simulating extended surface heat exchanger designs Essential CFD techniques for capturing complex flow phenomena and heat transfer mechanisms in finned geometries Practical applications of CFD analysis in optimizing Finned Tube Heat Exchangers for various industries By the end of this episode, you’ll have developed advanced skills in: Setting up and running detailed Finned Tube Heat Exchanger simulations using ANSYS Fluent Interpreting complex simulation results to assess and improve heat exchanger performance Applying sophisticated CFD insights to enhance the design and efficiency of Finned Tube Heat Exchangers This knowledge forms a robust foundation for thermal engineers, HVAC professionals, and researchers looking to leverage advanced computational methods in heat exchanger design and analysis, providing a pathway to innovation in thermal system engineering. Join us on this exciting journey into the world of Finned Tube Heat Exchanger CFD simulation, and elevate your skills in advanced thermal system design and optimization using cutting-edge computational tools!
-
Section 1
Plate Heat Exchanger
-
Mastering Plate Heat Exchanger CFD Simulation: A Comprehensive Guide for Beginners Welcome to the “Plate Heat Exchanger CFD Simulation” episode of our “Heat Exchanger: BEGINNER” course. This in-depth module introduces thermal engineers and students to the powerful world of Computational Fluid Dynamics (CFD) for analyzing plate heat exchangers using ANSYS Fluent. Learn how to simulate and optimize these versatile heat transfer devices, essential for various industries including food processing, pharmaceuticals, HVAC, and chemical engineering. Understanding Plate Heat Exchangers: Fundamentals and Applications Before diving into simulation techniques, let’s explore the core concepts of plate heat exchangers and their significance in industrial applications. The Role of Plate Heat Exchangers in Modern Industry Discover how plate heat exchangers revolutionize thermal management across diverse sectors, offering compact design, high efficiency, and easy maintenance. Key Design Features and Heat Transfer Mechanisms Explore the unique characteristics of plate heat exchangers, including flow channel geometry and heat transfer enhancement techniques. Introduction to ANSYS Fluent for Plate Heat Exchanger Analysis This section focuses on familiarizing beginners with the ANSYS Fluent software environment for heat exchanger simulations: Navigating the ANSYS Fluent Interface Gain insights into the basic layout and functionality of ANSYS Fluent, essential for efficient simulation setup and analysis of plate heat exchangers. Understanding the CFD Workflow for Heat Exchanger Simulations Learn the step-by-step process of setting up, running, and analyzing a plate heat exchanger CFD simulation in ANSYS Fluent. Setting Up a Basic Plate Heat Exchanger Model Master the art of creating a simple simulation environment for plate heat exchanger analysis: Defining Geometry and Mesh for Plate Heat Exchanger Simulations Learn techniques for creating an accurate geometry representing a plate heat exchanger, along with appropriate meshing strategies for precise flow and heat transfer analysis. Configuring Material Properties and Fluid Domains Explore methods for defining and implementing the properties of working fluids and solid materials in your plate heat exchanger simulation. Boundary Conditions for Plate Heat Exchanger Scenarios Dive into the critical settings that ensure realistic representation of heat transfer and fluid flow in plate heat exchangers: Specifying Inlet and Outlet Conditions Understand how to set up appropriate inlet flow rates, temperatures, and outlet conditions that accurately represent various operational scenarios. Implementing Wall and Interface Boundary Conditions Learn to define proper boundary conditions for plate surfaces and fluid-solid interfaces to capture realistic heat transfer behavior. Running CFD Simulations for Plate Heat Exchangers Develop skills to execute and monitor your plate heat exchanger CFD simulations: Setting Up Solver Parameters for Heat Transfer Simulations Master the basics of configuring solver settings, including turbulence models and convergence criteria, suitable for plate heat exchanger simulations. Managing Steady-State and Transient Simulations Learn techniques for running both steady-state and time-dependent simulations to analyze various operational conditions. Analyzing Flow Patterns and Heat Transfer Performance Develop expertise in extracting meaningful insights from your plate heat exchanger simulations: Visualizing Complex Flow Patterns and Temperature Distributions Master techniques for creating insightful visualizations of velocity fields, pressure distributions, and temperature contours to understand heat exchanger behavior. Interpreting Pressure Drop and Heat Transfer Coefficients Learn to analyze key performance metrics, including pressure drop and heat transfer coefficients, crucial for assessing and optimizing plate heat exchanger designs. Advanced Simulation Techniques for Plate Heat Exchangers Explore more sophisticated aspects of plate heat exchanger modeling: Investigating the Impact of Chevron Angle and Plate Spacing Gain insights into how geometric parameters like chevron angle and plate spacing affect heat exchanger performance through parametric studies. Simulating Multi-Phase Flows in Plate Heat Exchangers Learn introductory methods for modeling multi-phase flows, expanding your simulation capabilities to more complex heat exchanger scenarios. Practical Applications and Design Optimization Connect simulation insights to real-world heat exchanger design challenges: Applying CFD Insights to Plate Heat Exchanger Design and Optimization Explore how the flow patterns and heat transfer characteristics observed in CFD simulations can inform design decisions and performance improvements. Comparing Performance Metrics for Different Plate Designs Learn to conduct comparative analyses of various plate configurations to identify optimal designs for specific applications. Why This Module is Essential for Beginner Thermal Engineers This beginner-level module offers an introduction to the powerful world of CFD in plate heat exchanger analysis. By completing this simulation course, you’ll gain valuable insights into: Basic application of ANSYS Fluent for simulating plate heat exchangers Essential CFD techniques for capturing complex flow and heat transfer phenomena Practical applications of CFD analysis in thermal system design and optimization By the end of this episode, you’ll have developed foundational skills in: Setting up and running plate heat exchanger simulations using ANSYS Fluent Interpreting simulation results to assess heat exchanger performance Applying CFD insights to enhance understanding of plate heat exchanger behavior and inform design decisions This knowledge forms a solid foundation for thermal engineers looking to integrate advanced computational methods into their heat exchanger design and analysis toolkit, providing a springboard for more advanced studies in thermal system engineering and CFD modeling. Join us on this exciting journey into the world of plate heat exchanger CFD simulation, and take your first steps towards becoming a proficient thermal engineer equipped with cutting-edge computational tools for innovative heat transfer solutions!
Episode 1 15m 24s Free Episode
-
-
Section 2
Chevron Plate Heat Exchanger
-
Mastering Chevron Plate Heat Exchanger CFD Simulation: A Beginner's Guide Welcome to the “Chevron Plate Heat Exchanger CFD Simulation” episode of our “Heat Exchanger: BEGINNER” course. This comprehensive module introduces novices to the world of Computational Fluid Dynamics (CFD) for analyzing Chevron Plate Heat Exchangers using ANSYS Fluent. Learn the basics of simulating these efficient and compact heat transfer devices, essential in industries ranging from food processing to HVAC systems. Understanding Chevron Plate Heat Exchangers: Fundamentals and Applications Before diving into simulation techniques, let’s explore the core concepts of Chevron Plate Heat Exchangers and their significance in industrial applications. The Role of Chevron Plate Heat Exchangers in Modern Industry Discover how these compact yet powerful devices revolutionize heat transfer across diverse sectors, offering high efficiency and versatility. Key Design Features of Chevron Plate Heat Exchangers Explore the unique characteristics of Chevron Plate Heat Exchangers, including their distinctive geometry and enhanced heat transfer capabilities. Introduction to ANSYS Fluent for Heat Exchanger Analysis This section focuses on familiarizing beginners with the ANSYS Fluent software environment: Navigating the ANSYS Fluent Interface Gain insights into the basic layout and functionality of ANSYS Fluent, essential for efficient simulation setup and analysis of Chevron Plate Heat Exchangers. Understanding the CFD Workflow for Heat Exchanger Simulations Learn the step-by-step process of setting up, running, and analyzing a Chevron Plate Heat Exchanger CFD simulation in ANSYS Fluent. Setting Up a Basic Chevron Plate Heat Exchanger Model Master the art of creating a simple simulation environment for Chevron Plate Heat Exchanger analysis: Defining Geometry for Chevron Plate Heat Exchanger Simulations Learn techniques for creating a basic geometry representing a Chevron Plate Heat Exchanger, focusing on the essential features for beginner-level simulations. Configuring Material Properties and Fluid Domains Explore methods for defining and implementing the properties of working fluids in your Chevron Plate Heat Exchanger simulation. Boundary Conditions for Chevron Plate Heat Exchanger Scenarios Dive into the critical settings that ensure realistic representation of heat transfer and fluid flow in Chevron Plate Heat Exchangers: Specifying Inlet and Outlet Conditions Understand how to set up appropriate inlet flow rates, temperatures, and outlet conditions for a basic Chevron Plate Heat Exchanger simulation. Implementing Wall Boundary Conditions Learn to define proper boundary conditions for plate surfaces to capture realistic heat transfer behavior in a simplified model. Running Your First CFD Simulation for Chevron Plate Heat Exchangers Develop skills to execute and monitor your first Chevron Plate Heat Exchanger CFD simulation: Setting Up Basic Solver Parameters Master the fundamentals of configuring solver settings, including simple turbulence models and convergence criteria, suitable for beginner-level Chevron Plate Heat Exchanger simulations. Monitoring Simulation Progress Learn techniques for tracking simulation progress and identifying basic issues during the solving process. Analyzing Basic Flow Patterns and Heat Transfer Performance Develop expertise in extracting fundamental insights from your Chevron Plate Heat Exchanger simulations: Visualizing Simple Flow Patterns and Temperature Distributions Master techniques for creating basic visualizations of velocity fields and temperature contours to understand Chevron Plate Heat Exchanger behavior. Interpreting Fundamental Pressure Drop Results Learn to analyze basic pressure drop characteristics, crucial for assessing Chevron Plate Heat Exchanger performance at a beginner level. Introduction to Turbulent Flow in ANSYS Fluent Explore the basics of turbulent flow modeling in the context of Chevron Plate Heat Exchangers: Understanding the Concept of Turbulence in Heat Exchangers Gain insights into how turbulence affects heat transfer in Chevron Plate Heat Exchangers and its importance in CFD simulations. Basic Techniques for Implementing Simple Turbulence Models Learn introductory methods for selecting and applying basic turbulence models in your Chevron Plate Heat Exchanger simulations. Practical Applications and Future Learning Paths Connect simulation insights to real-world heat exchanger applications and future learning opportunities: Applying Basic CFD Insights to Chevron Plate Heat Exchanger Understanding Explore how the fundamental flow patterns and heat transfer characteristics observed in CFD simulations can enhance your understanding of Chevron Plate Heat Exchangers. Identifying Next Steps in Heat Exchanger CFD Simulation Gain awareness of more advanced topics in heat exchanger simulation and potential paths for further learning and skill development. Why This Module is Essential for Beginner Thermal Engineers This beginner-level module offers an introduction to the world of CFD in Chevron Plate Heat Exchanger analysis. By completing this simulation course, you’ll gain valuable insights into: Basic application of ANSYS Fluent for simulating Chevron Plate Heat Exchangers Fundamental CFD techniques for capturing flow and heat transfer phenomena Practical applications of CFD analysis in thermal system design By the end of this episode, you’ll have developed foundational skills in: Setting up and running basic Chevron Plate Heat Exchanger simulations using ANSYS Fluent Interpreting simple simulation results to assess heat exchanger performance Applying fundamental CFD insights to enhance understanding of Chevron Plate Heat Exchanger behavior This knowledge forms a solid foundation for thermal engineers and students looking to start their journey in computational heat transfer analysis, providing a springboard for more advanced studies in thermal system engineering and CFD modeling. Join us on this exciting introductory journey into the world of Chevron Plate Heat Exchanger CFD simulation, and take your first steps towards becoming a proficient thermal engineer equipped with essential computational tools for innovative heat transfer solutions!
Episode 1 24m 28s
-
-
Section 3
Mixing Tab in Planar Heat Exchanger
-
Mastering Planar Heat Exchanger with Mixing Tabs CFD Simulation: A Beginner's Guide Welcome to the “Planar Heat Exchanger with Mixing Tabs CFD Simulation” episode of our “Heat Exchanger: BEGINNER” course. This comprehensive module introduces novices to the world of Computational Fluid Dynamics (CFD) for analyzing innovative Planar Heat Exchangers with Mixing Tabs using ANSYS Fluent. Learn how to simulate and evaluate these advanced heat transfer devices, essential for applications in electronics cooling, automotive thermal management, and compact HVAC systems. Understanding Planar Heat Exchangers with Mixing Tabs: Fundamentals and Applications Before diving into simulation techniques, let’s explore the core concepts of Planar Heat Exchangers with Mixing Tabs and their significance in modern thermal management. The Role of Mixing Tabs in Enhancing Heat Transfer Discover how mixing tabs revolutionize heat exchanger performance by increasing turbulence and generating secondary flows, leading to improved heat transfer rates and reduced fouling. Key Design Features of Planar Heat Exchangers with Mixing Tabs Explore the unique characteristics of these advanced heat exchangers, including their compact form factor and innovative tab configurations. Introduction to ANSYS Fluent for Advanced Heat Exchanger Analysis This section focuses on familiarizing beginners with the ANSYS Fluent software environment for simulating complex heat exchanger designs: Navigating the ANSYS Fluent Interface for Planar Heat Exchanger Simulations Gain insights into the basic layout and functionality of ANSYS Fluent, essential for efficient simulation setup and analysis of Planar Heat Exchangers with Mixing Tabs. Understanding the CFD Workflow for Advanced Heat Exchanger Simulations Learn the step-by-step process of setting up, running, and analyzing a Planar Heat Exchanger with Mixing Tabs CFD simulation in ANSYS Fluent. Setting Up the Case Study: Planar Heat Exchanger with Mixing Tabs Master the art of creating a simulation environment for this advanced heat exchanger design: Defining Geometry for the Planar Heat Exchanger with Mixing Tabs Learn techniques for creating a representative geometry of a Planar Heat Exchanger with Mixing Tabs, focusing on the essential features for beginner-level simulations. Configuring Material Properties and Fluid Domains Explore methods for defining and implementing the properties of working fluids and solid materials in your simulation. Boundary Conditions for Planar Heat Exchanger with Mixing Tabs Dive into the critical settings that ensure realistic representation of heat transfer and fluid flow in this advanced design: Specifying Inlet and Outlet Conditions Understand how to set up appropriate inlet flow rates, temperatures, and outlet conditions for the case study simulation. Implementing Wall and Interface Boundary Conditions Learn to define proper boundary conditions for heat exchanger surfaces and mixing tabs to capture realistic heat transfer and flow behavior. Running CFD Simulations for Planar Heat Exchangers with Mixing Tabs Develop skills to execute and monitor your CFD simulation: Setting Up Solver Parameters for Complex Flow Patterns Master the basics of configuring solver settings, including turbulence models suitable for capturing the flow structures generated by mixing tabs. Managing Simulation Progress and Ensuring Convergence Learn techniques for tracking simulation progress and identifying potential issues during the solving process. Analyzing Flow Patterns and Heat Transfer Performance Develop expertise in extracting meaningful insights from your simulations: Visualizing Complex Flow Structures and Temperature Distributions Master techniques for creating insightful visualizations of velocity fields, turbulence patterns, and temperature contours to understand the impact of mixing tabs. Interpreting Heat Transfer Coefficients and Pressure Drop Learn to analyze key performance metrics, including local and overall heat transfer coefficients and pressure drop, crucial for assessing the effectiveness of mixing tabs. Comparative Analysis: Standard vs. Mixing Tab Design Explore the performance differences between standard planar heat exchangers and those with mixing tabs: Evaluating Heat Transfer Enhancement Gain insights into how mixing tabs improve heat transfer rates compared to standard planar designs. Assessing the Trade-off: Improved Heat Transfer vs. Increased Pressure Drop Learn to analyze the balance between enhanced heat transfer and the associated increase in pressure drop due to mixing tabs. Practical Applications and Design Considerations Connect simulation insights to real-world heat exchanger applications: Applying CFD Insights to Planar Heat Exchanger Design Optimization Explore how the flow patterns and heat transfer characteristics observed in CFD simulations can inform design decisions and performance improvements. Understanding Limitations and Future Research Directions Gain awareness of the simplifications in this introductory case study and potential areas for more advanced analyses in future studies. Why This Module is Essential for Beginner Thermal Engineers This beginner-level module offers an introduction to the world of CFD in advanced heat exchanger analysis. By completing this simulation course, you’ll gain valuable insights into: Basic application of ANSYS Fluent for simulating Planar Heat Exchangers with Mixing Tabs Essential CFD techniques for capturing complex flow and heat transfer phenomena Practical applications of CFD analysis in modern thermal system design and optimization By the end of this episode, you’ll have developed foundational skills in: Setting up and running simulations of advanced heat exchanger designs using ANSYS Fluent Interpreting simulation results to assess the impact of mixing tabs on heat exchanger performance Applying CFD insights to enhance understanding of innovative heat transfer solutions This knowledge forms a solid foundation for thermal engineers looking to explore advanced heat exchanger designs, providing a springboard for more in-depth studies in thermal system engineering and CFD modeling. Join us on this exciting journey into the world of Planar Heat Exchangers with Mixing Tabs CFD simulation, and take your first steps towards becoming a proficient thermal engineer equipped with cutting-edge computational tools for innovative heat transfer solutions!
Episode 1 12m 55s
-
-
Section 4
Reverse Cross Flow Plate Heat Exchanger
-
Mastering Reverse Cross Flow Plate Heat Exchanger CFD Simulation: A Beginner's Guide Welcome to the “Reverse Cross Flow Plate Heat Exchanger CFD Simulation” episode of our “Heat Exchanger: BEGINNER” course. This comprehensive module introduces novices to the world of Computational Fluid Dynamics (CFD) for analyzing Reverse Cross Flow Plate Heat Exchangers using ANSYS Fluent. Learn how to simulate and evaluate these highly efficient heat transfer devices, essential for applications in HVAC systems and industrial process cooling. Understanding Reverse Cross Flow Plate Heat Exchangers: Fundamentals and Applications Before diving into simulation techniques, let’s explore the core concepts of Reverse Cross Flow Plate Heat Exchangers and their significance in modern thermal management. The Advantages of Reverse Cross Flow Configuration Discover how Reverse Cross Flow Plate Heat Exchangers offer high thermal efficiency and compact design, making them crucial in various industrial applications. Key Design Features of Reverse Cross Flow Plate Heat Exchangers Explore the unique characteristics of these heat exchangers, including their plate arrangement and flow patterns that contribute to their superior performance. Introduction to ANSYS Fluent for Heat Exchanger Analysis This section focuses on familiarizing beginners with the ANSYS Fluent software environment for heat exchanger simulations: Navigating the ANSYS Fluent Interface Gain insights into the basic layout and functionality of ANSYS Fluent, essential for efficient simulation setup and analysis of Reverse Cross Flow Plate Heat Exchangers. Understanding the CFD Workflow for Heat Exchanger Simulations Learn the step-by-step process of setting up, running, and analyzing a Reverse Cross Flow Plate Heat Exchanger CFD simulation in ANSYS Fluent. Setting Up a Basic Reverse Cross Flow Plate Heat Exchanger Model Master the art of creating a simple simulation environment for Reverse Cross Flow Plate Heat Exchanger analysis: Defining Geometry for Cross Flow Configurations Learn techniques for creating a basic geometry representing a Reverse Cross Flow Plate Heat Exchanger, focusing on the essential features for beginner-level simulations. Configuring Material Properties and Fluid Domains Explore methods for defining and implementing the properties of working fluids and plate materials in your simulation. Boundary Conditions for Reverse Cross Flow Plate Heat Exchanger Scenarios Dive into the critical settings that ensure realistic representation of heat transfer and fluid flow in Reverse Cross Flow configurations: Specifying Inlet and Outlet Conditions Understand how to set up appropriate inlet flow rates, temperatures, and outlet conditions for both fluid streams in a Reverse Cross Flow arrangement. Implementing Wall and Interface Boundary Conditions Learn to define proper boundary conditions for plate surfaces and fluid interfaces to capture realistic heat transfer behavior. Running CFD Simulations for Reverse Cross Flow Plate Heat Exchangers Develop skills to execute and monitor your Reverse Cross Flow Plate Heat Exchanger CFD simulations: Setting Up Solver Parameters for Cross Flow Simulations Master the basics of configuring solver settings, including convergence criteria and solution methods suitable for cross flow heat exchanger simulations. Managing Simulation Progress and Ensuring Stability Learn techniques for tracking simulation progress and identifying potential issues during the solving process. Analyzing Flow Patterns and Heat Transfer Performance Develop expertise in extracting meaningful insights from your Reverse Cross Flow Plate Heat Exchanger simulations: Visualizing Flow and Temperature Distributions Master techniques for creating insightful visualizations of velocity fields and temperature contours to understand the behavior of Reverse Cross Flow Plate Heat Exchangers. Interpreting Heat Transfer Coefficients and Effectiveness Learn to analyze key performance metrics, including local and overall heat transfer coefficients and heat exchanger effectiveness, crucial for assessing Reverse Cross Flow designs. Comparative Analysis: Co-Current vs. Counter-Current Flow Explore the performance differences between co-current and counter-current flow arrangements in Reverse Cross Flow Plate Heat Exchangers: Evaluating Temperature Profiles in Different Flow Arrangements Gain insights into how flow direction impacts temperature distribution and overall heat transfer efficiency. Assessing Heat Transfer Effectiveness in Co-Current and Counter-Current Configurations Learn to compare and analyze the effectiveness of different flow arrangements in Reverse Cross Flow Plate Heat Exchangers. Practical Applications and Future Learning Paths Connect simulation insights to real-world heat exchanger applications and future learning opportunities: Applying CFD Insights to Reverse Cross Flow Plate Heat Exchanger Design Explore how the flow patterns and heat transfer characteristics observed in CFD simulations can inform design decisions and performance improvements. Identifying Next Steps in Heat Exchanger CFD Simulation Gain awareness of more advanced topics in heat exchanger simulation and potential paths for further learning and skill development. Why This Module is Essential for Beginner Thermal Engineers This beginner-level module offers an introduction to the world of CFD in Reverse Cross Flow Plate Heat Exchanger analysis. By completing this simulation course, you’ll gain valuable insights into: Basic application of ANSYS Fluent for simulating Reverse Cross Flow Plate Heat Exchangers Essential CFD techniques for capturing flow and heat transfer phenomena in cross flow configurations Practical applications of CFD analysis in thermal system design and optimization By the end of this episode, you’ll have developed foundational skills in: Setting up and running basic Reverse Cross Flow Plate Heat Exchanger simulations using ANSYS Fluent Interpreting simulation results to assess heat exchanger performance in different flow arrangements Applying fundamental CFD insights to enhance understanding of Reverse Cross Flow Plate Heat Exchanger behavior This knowledge forms a solid foundation for thermal engineers and students looking to start their journey in computational heat transfer analysis, providing a springboard for more advanced studies in thermal system engineering and CFD modeling. Join us on this exciting introductory journey into the world of Reverse Cross Flow Plate Heat Exchanger CFD simulation, and take your first steps towards becoming a proficient thermal engineer equipped with essential computational tools for innovative heat transfer solutions!
Episode 1 15m 16s
-
-
Section 5
Double Pipe Counter Flow Heat Exchanger
-
Mastering Double Pipe Counter Flow Heat Exchanger CFD Simulation: A Beginner's Guide Welcome to the “Double Pipe Counter Flow Heat Exchanger CFD Simulation” episode of our “Heat Exchanger: BEGINNER” course. This comprehensive module introduces novices to the world of Computational Fluid Dynamics (CFD) for analyzing Double Pipe Counter Flow Heat Exchangers using ANSYS Fluent. Learn how to simulate and evaluate these fundamental heat transfer devices, essential for applications ranging from laboratory setups to industrial processes. Understanding Double Pipe Counter Flow Heat Exchangers: Fundamentals and Applications Before diving into simulation techniques, let’s explore the core concepts of Double Pipe Counter Flow Heat Exchangers and their significance in thermal management. The Advantages of Counter Flow Configuration Discover how the counter flow arrangement in double pipe heat exchangers maximizes temperature difference and enhances heat transfer efficiency across various industries. Key Design Features of Double Pipe Heat Exchangers Explore the unique characteristics of these heat exchangers, including their concentric pipe structure and flow patterns that contribute to their effectiveness and reliability. Introduction to ANSYS Fluent for Heat Exchanger Analysis This section focuses on familiarizing beginners with the ANSYS Fluent software environment for heat exchanger simulations: Navigating the ANSYS Fluent Interface Gain insights into the basic layout and functionality of ANSYS Fluent, essential for efficient simulation setup and analysis of Double Pipe Counter Flow Heat Exchangers. Understanding the CFD Workflow for Heat Exchanger Simulations Learn the step-by-step process of setting up, running, and analyzing a Double Pipe Counter Flow Heat Exchanger CFD simulation in ANSYS Fluent. Setting Up a Basic Double Pipe Counter Flow Heat Exchanger Model Master the art of creating a simple simulation environment for Double Pipe Counter Flow Heat Exchanger analysis: Defining Geometry for Concentric Pipe Configurations Learn techniques for creating a basic geometry representing a Double Pipe Counter Flow Heat Exchanger, focusing on the essential features for beginner-level simulations. Configuring Material Properties and Fluid Domains Explore methods for defining and implementing the properties of working fluids and pipe materials in your simulation. Boundary Conditions for Double Pipe Counter Flow Heat Exchanger Scenarios Dive into the critical settings that ensure realistic representation of heat transfer and fluid flow in counter flow configurations: Specifying Inlet and Outlet Conditions Understand how to set up appropriate inlet flow rates, temperatures, and outlet conditions for both fluid streams in a counter flow arrangement. Implementing Wall and Interface Boundary Conditions Learn to define proper boundary conditions for pipe surfaces and fluid interfaces to capture realistic heat transfer behavior. Running CFD Simulations for Double Pipe Counter Flow Heat Exchangers Develop skills to execute and monitor your Double Pipe Counter Flow Heat Exchanger CFD simulations: Setting Up Solver Parameters for Steady-State Simulations Master the basics of configuring solver settings, including convergence criteria and solution methods suitable for double pipe heat exchanger simulations. Managing Simulation Progress and Ensuring Stability Learn techniques for tracking simulation progress and identifying potential issues during the solving process. Analyzing Flow Patterns and Heat Transfer Performance Develop expertise in extracting meaningful insights from your Double Pipe Counter Flow Heat Exchanger simulations: Visualizing Temperature Distributions and Velocity Profiles Master techniques for creating insightful visualizations of temperature contours and velocity fields to understand the behavior of Double Pipe Counter Flow Heat Exchangers. Interpreting Heat Transfer Coefficients and Overall Heat Transfer Rates Learn to analyze key performance metrics, including local and overall heat transfer coefficients and heat transfer rates, crucial for assessing Double Pipe Counter Flow designs. Investigating the Impact of Design Parameters Explore how various factors affect the performance of Double Pipe Counter Flow Heat Exchangers: Evaluating the Effects of Flow Rates and Fluid Properties Gain insights into how changes in fluid velocity and thermal properties impact heat exchanger efficiency. Assessing the Influence of Pipe Materials and Dimensions Learn to analyze how different pipe materials and geometric configurations affect heat transfer performance in Double Pipe Counter Flow Heat Exchangers. Practical Applications and Performance Evaluation Connect simulation insights to real-world heat exchanger applications and performance assessment: Applying CFD Insights to Double Pipe Heat Exchanger Design Explore how the temperature profiles and heat transfer characteristics observed in CFD simulations can inform design decisions and performance improvements. Evaluating Key Performance Metrics for Double Pipe Counter Flow Heat Exchangers Learn to calculate and interpret essential performance indicators such as effectiveness and overall heat transfer coefficient using simulation results. Why This Module is Essential for Beginner Thermal Engineers This beginner-level module offers an introduction to the world of CFD in Double Pipe Counter Flow Heat Exchanger analysis. By completing this simulation course, you’ll gain valuable insights into: Basic application of ANSYS Fluent for simulating Double Pipe Counter Flow Heat Exchangers Essential CFD techniques for capturing flow and heat transfer phenomena in concentric pipe configurations Practical applications of CFD analysis in thermal system design and optimization By the end of this episode, you’ll have developed foundational skills in: Setting up and running basic Double Pipe Counter Flow Heat Exchanger simulations using ANSYS Fluent Interpreting simulation results to assess heat exchanger performance and efficiency Applying fundamental CFD insights to enhance understanding of Double Pipe Counter Flow Heat Exchanger behavior This knowledge forms a solid foundation for thermal engineers, process designers, and students looking to start their journey in computational heat transfer analysis, providing a springboard for more advanced studies in thermal system engineering and CFD modeling. Join us on this exciting introductory journey into the world of Double Pipe Counter Flow Heat Exchanger CFD simulation, and take your first steps towards becoming a proficient thermal engineer equipped with essential computational tools for innovative heat transfer solutions!
Episode 1 13m 42s
-
-
Section 6
Shell and Helical Tube Heat Exchanger
-
Mastering Shell and Helical Tube Heat Exchanger CFD Simulation: A Comprehensive Guide Welcome to the “Shell and Helical Tube Heat Exchanger CFD Simulation” episode of our “Heat Exchanger: BEGINNER” course. This in-depth module introduces learners to the world of Computational Fluid Dynamics (CFD) for analyzing innovative Shell and Helical Tube Heat Exchangers using ANSYS Fluent. Discover how to simulate and evaluate these advanced heat transfer devices, crucial for applications in petrochemical processing, power generation, and cryogenic systems. Understanding Shell and Helical Tube Heat Exchangers: Fundamentals and Applications Before diving into simulation techniques, let’s explore the core concepts of Shell and Helical Tube Heat Exchangers and their significance in modern thermal management. The Advantages of Helical Tube Configuration Discover how Shell and Helical Tube Heat Exchangers combine the robustness of shell-and-tube designs with enhanced efficiency, offering improved heat transfer rates and compact design for high-pressure applications. Key Design Features of Shell and Helical Tube Heat Exchangers Explore the unique characteristics of these heat exchangers, including their helical flow paths and how they contribute to superior performance in various industries. Introduction to ANSYS Fluent for Advanced Heat Exchanger Analysis This section focuses on familiarizing users with the ANSYS Fluent software environment for complex heat exchanger simulations: Navigating the ANSYS Fluent Interface for Helical Geometries Gain insights into the specialized tools and features of ANSYS Fluent essential for efficient simulation setup and analysis of Shell and Helical Tube Heat Exchangers. Understanding the CFD Workflow for Complex Heat Exchanger Simulations Learn the step-by-step process of setting up, running, and analyzing a Shell and Helical Tube Heat Exchanger CFD simulation in ANSYS Fluent. Setting Up a Shell and Helical Tube Heat Exchanger Model Master the art of creating an accurate simulation environment for Shell and Helical Tube Heat Exchanger analysis: Defining Complex Geometry for Helical Tube Configurations Learn advanced techniques for creating a detailed geometry representing a Shell and Helical Tube Heat Exchanger, focusing on the critical features that influence performance. Configuring Material Properties and Fluid Domains Explore methods for defining and implementing the properties of working fluids and materials in your simulation, considering the unique requirements of helical designs. Boundary Conditions for Shell and Helical Tube Heat Exchanger Scenarios Dive into the critical settings that ensure realistic representation of heat transfer and fluid flow in helical configurations: Specifying Inlet and Outlet Conditions for Helical Paths Understand how to set up appropriate inlet flow rates, temperatures, and outlet conditions for both shell-side and tube-side fluids in a helical arrangement. Implementing Wall and Interface Boundary Conditions Learn to define proper boundary conditions for helical tube surfaces and fluid interfaces to capture realistic heat transfer behavior in curved geometries. Running Advanced CFD Simulations for Shell and Helical Tube Heat Exchangers Develop skills to execute and monitor complex Shell and Helical Tube Heat Exchanger CFD simulations: Setting Up Solver Parameters for Curved Flow Simulations Master the configuration of solver settings, including advanced turbulence models suitable for capturing Dean vortices and other phenomena specific to helical flows. Managing Simulation Progress and Ensuring Convergence Learn techniques for tracking simulation progress, identifying potential issues, and ensuring solution stability in complex 3D geometries. Analyzing Complex Flow Patterns and Heat Transfer Performance Develop expertise in extracting meaningful insights from your Shell and Helical Tube Heat Exchanger simulations: Visualizing 3D Flow Structures and Temperature Distributions Master advanced techniques for creating insightful visualizations of velocity fields, Dean vortices, and temperature contours to understand the behavior of Shell and Helical Tube Heat Exchangers. Interpreting Heat Transfer Coefficients and Pressure Drop Characteristics Learn to analyze key performance metrics, including local and overall heat transfer coefficients and pressure drop, crucial for assessing the efficiency of helical designs. Comparative Analysis: Helical vs. Traditional Shell-and-Tube Designs Explore the performance differences between helical and conventional shell-and-tube heat exchangers: Evaluating Heat Transfer Enhancement in Helical Configurations Gain insights into how helical designs improve heat transfer rates compared to traditional straight-tube arrangements. Assessing the Impact of Coil Parameters on Exchanger Performance Learn to analyze the effects of coil pitch, curvature, and other geometric factors on overall heat exchanger efficiency. Practical Applications and Design Optimization Connect simulation insights to real-world heat exchanger applications and design improvements: Applying CFD Insights to Shell and Helical Tube Heat Exchanger Design Explore how the complex flow patterns and heat transfer characteristics observed in CFD simulations can inform design decisions and performance enhancements. Optimizing Helical Tube Geometry for Specific Industrial Applications Learn to use simulation results to optimize helical tube designs for various industrial scenarios, balancing heat transfer efficiency with pressure drop considerations. Why This Module is Essential for Thermal Engineers and Designers This comprehensive module offers an in-depth exploration of CFD techniques for Shell and Helical Tube Heat Exchanger analysis. By completing this simulation course, you’ll gain valuable insights into: Advanced application of ANSYS Fluent for simulating complex helical heat exchanger designs Essential CFD techniques for capturing intricate flow phenomena and heat transfer mechanisms in curved geometries Practical applications of CFD analysis in optimizing innovative heat exchanger designs for various industries By the end of this episode, you’ll have developed advanced skills in: Setting up and running detailed Shell and Helical Tube Heat Exchanger simulations using ANSYS Fluent Interpreting complex simulation results to assess and improve heat exchanger performance Applying sophisticated CFD insights to enhance the design and efficiency of Shell and Helical Tube Heat Exchangers This knowledge forms a robust foundation for thermal engineers, process designers, and researchers looking to leverage advanced computational methods in heat exchanger design and analysis, providing a pathway to innovation in thermal system engineering. Join us on this exciting journey into the world of Shell and Helical Tube Heat Exchanger CFD simulation, and elevate your skills in advanced thermal system design and optimization using cutting-edge computational tools!
Episode 1 16m 30s
-
-
Section 7
Spiral Baffle in Shell and Tube Heat Exchanger
-
Mastering Shell and Tube Heat Exchanger with Spiral Baffle CFD Simulation: A Beginner's Guide Welcome to the “Shell and Tube Heat Exchanger with Spiral Baffle CFD Simulation” episode of our “Heat Exchanger: BEGINNER” course. This comprehensive module introduces novices to the world of Computational Fluid Dynamics (CFD) for analyzing innovative Shell and Tube Heat Exchangers with Spiral Baffles using ANSYS Fluent. Learn how to simulate and evaluate these advanced heat transfer devices, essential for applications in petrochemical processing, power generation, and HVAC systems. Understanding Shell and Tube Heat Exchangers with Spiral Baffles: Fundamentals and Applications Before diving into simulation techniques, let’s explore the core concepts of Shell and Tube Heat Exchangers with Spiral Baffles and their significance in modern thermal management. The Advantages of Spiral Baffle Configuration Discover how spiral baffles enhance heat transfer rates, reduce fouling, and improve overall efficiency compared to traditional segmental baffle designs. Key Design Features of Shell and Tube Heat Exchangers with Spiral Baffles Explore the unique characteristics of these heat exchangers, including their helical flow paths and how they contribute to superior performance in various industries. Introduction to ANSYS Fluent for Advanced Heat Exchanger Analysis This section focuses on familiarizing beginners with the ANSYS Fluent software environment for complex heat exchanger simulations: Navigating the ANSYS Fluent Interface for Spiral Baffle Geometries Gain insights into the basic layout and functionality of ANSYS Fluent, essential for efficient simulation setup and analysis of Shell and Tube Heat Exchangers with Spiral Baffles. Understanding the CFD Workflow for Complex Heat Exchanger Simulations Learn the step-by-step process of setting up, running, and analyzing a Shell and Tube Heat Exchanger with Spiral Baffles CFD simulation in ANSYS Fluent. Setting Up a Shell and Tube Heat Exchanger Model with Spiral Baffles Master the art of creating a simulation environment for this advanced heat exchanger design: Defining Geometry for Spiral Baffle Configurations Learn techniques for creating a representative geometry of a Shell and Tube Heat Exchanger with Spiral Baffles, focusing on the essential features for beginner-level simulations. Configuring Material Properties and Fluid Domains Explore methods for defining and implementing the properties of working fluids and materials in your simulation, considering the unique requirements of spiral baffle designs. Boundary Conditions for Shell and Tube Heat Exchangers with Spiral Baffles Dive into the critical settings that ensure realistic representation of heat transfer and fluid flow in spiral baffle configurations: Specifying Inlet and Outlet Conditions Understand how to set up appropriate inlet flow rates, temperatures, and outlet conditions for both shell-side and tube-side fluids in a spiral baffle arrangement. Implementing Wall and Interface Boundary Conditions Learn to define proper boundary conditions for heat exchanger surfaces and fluid interfaces to capture realistic heat transfer behavior in spiral baffle geometries. Running CFD Simulations for Shell and Tube Heat Exchangers with Spiral Baffles Develop skills to execute and monitor your CFD simulations: Setting Up Solver Parameters for Helical Flow Patterns Master the basics of configuring solver settings, including turbulence models suitable for capturing the complex flow structures generated by spiral baffles. Managing Simulation Progress and Ensuring Convergence Learn techniques for tracking simulation progress and identifying potential issues during the solving process. Analyzing Flow Patterns and Heat Transfer Performance Develop expertise in extracting meaningful insights from your simulations: Visualizing Complex Flow Structures and Temperature Distributions Master techniques for creating insightful visualizations of velocity fields, helical flow patterns, and temperature contours to understand the impact of spiral baffles. Interpreting Heat Transfer Coefficients and Pressure Drop Learn to analyze key performance metrics, including local and overall heat transfer coefficients and pressure drop, crucial for assessing the effectiveness of spiral baffle designs. Comparative Analysis: Spiral vs. Segmental Baffle Designs Explore the performance differences between spiral and traditional segmental baffle configurations: Evaluating Heat Transfer Enhancement with Spiral Baffles Gain insights into how spiral baffles improve heat transfer rates compared to conventional segmental baffle designs. Assessing Pressure Drop and Fouling Reduction Learn to analyze the balance between enhanced heat transfer, pressure drop characteristics, and reduced fouling potential in spiral baffle configurations. Practical Applications and Design Considerations Connect simulation insights to real-world heat exchanger applications: Applying CFD Insights to Shell and Tube Heat Exchanger Design Optimization Explore how the flow patterns and heat transfer characteristics observed in CFD simulations can inform design decisions and performance improvements for spiral baffle heat exchangers. Understanding Vibration Reduction and Maintenance Benefits Gain awareness of the additional advantages of spiral baffle designs, including reduced vibration and potential maintenance benefits. Why This Module is Essential for Beginner Thermal Engineers This beginner-level module offers an introduction to the world of CFD in advanced heat exchanger analysis. By completing this simulation course, you’ll gain valuable insights into: Basic application of ANSYS Fluent for simulating Shell and Tube Heat Exchangers with Spiral Baffles Essential CFD techniques for capturing complex flow and heat transfer phenomena in advanced baffle designs Practical applications of CFD analysis in modern thermal system design and optimization By the end of this episode, you’ll have developed foundational skills in: Setting up and running simulations of advanced heat exchanger designs using ANSYS Fluent Interpreting simulation results to assess the impact of spiral baffles on heat exchanger performance Applying CFD insights to enhance understanding of innovative heat transfer solutions This knowledge forms a solid foundation for thermal engineers looking to explore advanced heat exchanger designs, providing a springboard for more in-depth studies in thermal system engineering and CFD modeling. Join us on this exciting journey into the world of Shell and Tube Heat Exchangers with Spiral Baffles CFD simulation, and take your first steps towards becoming a proficient thermal engineer equipped with cutting-edge computational tools for innovative heat transfer solutions!
Episode 1 15m 40s
-
-
Section 8
Vertical Shell and Spiral Tube Heat Exchanger
-
Mastering Heat Transfer in Vertical Shell and Spiral Tube Heat Exchanger CFD Simulation: A Beginner's Guide Welcome to the “Heat Transfer in Vertical Shell and Spiral Tube Heat Exchanger CFD Simulation” episode of our “Heat Exchanger: BEGINNER” course. This comprehensive module introduces novices to the world of Computational Fluid Dynamics (CFD) for analyzing innovative Vertical Shell and Spiral Tube Heat Exchangers using ANSYS Fluent. Learn how to simulate and evaluate these advanced heat transfer devices, essential for applications in chemical processing, oil and gas industries, and power generation systems. Understanding Vertical Shell and Spiral Tube Heat Exchangers: Fundamentals and Applications Before diving into simulation techniques, let’s explore the core concepts of Vertical Shell and Spiral Tube Heat Exchangers and their significance in modern thermal management. The Advantages of Vertical Shell and Spiral Tube Configuration Discover how Vertical Shell and Spiral Tube Heat Exchangers offer improved performance in a compact vertical arrangement, making them ideal for space-constrained applications requiring high heat transfer rates. Key Design Features of Vertical Shell and Spiral Tube Heat Exchangers Explore the unique characteristics of these heat exchangers, including their vertical orientation and spiral tube geometry that contribute to their superior performance in various industries. Introduction to ANSYS Fluent for Vertical Heat Exchanger Analysis This section focuses on familiarizing beginners with the ANSYS Fluent software environment for vertical heat exchanger simulations: Navigating the ANSYS Fluent Interface for Vertical and Spiral Geometries Gain insights into the basic layout and functionality of ANSYS Fluent, essential for efficient simulation setup and analysis of Vertical Shell and Spiral Tube Heat Exchangers. Understanding the CFD Workflow for Vertical Heat Exchanger Simulations Learn the step-by-step process of setting up, running, and analyzing a Vertical Shell and Spiral Tube Heat Exchanger CFD simulation in ANSYS Fluent. Setting Up a Basic Vertical Shell and Spiral Tube Heat Exchanger Model Master the art of creating a simple simulation environment for Vertical Shell and Spiral Tube Heat Exchanger analysis: Defining Geometry for Vertical and Spiral Configurations Learn techniques for creating a basic geometry representing a Vertical Shell and Spiral Tube Heat Exchanger, focusing on the essential features for beginner-level simulations. Configuring Material Properties and Fluid Domains Explore methods for defining and implementing the properties of working fluids and materials in your simulation, considering the unique requirements of vertical and spiral designs. Boundary Conditions for Vertical Shell and Spiral Tube Heat Exchanger Scenarios Dive into the critical settings that ensure realistic representation of heat transfer and fluid flow in vertical and spiral configurations: Specifying Inlet and Outlet Conditions Understand how to set up appropriate inlet flow rates, temperatures, and outlet conditions for both shell-side and tube-side fluids in a vertical spiral arrangement. Implementing Wall and Interface Boundary Conditions Learn to define proper boundary conditions for heat exchanger surfaces and fluid interfaces to capture realistic heat transfer behavior in vertical spiral geometries. Running Basic CFD Simulations for Vertical Shell and Spiral Tube Heat Exchangers Develop skills to execute and monitor your Vertical Shell and Spiral Tube Heat Exchanger CFD simulations: Setting Up Solver Parameters for Vertical and Spiral Flow Patterns Master the basics of configuring solver settings, including simple turbulence models suitable for capturing the flow structures in vertical and spiral configurations. Managing Simulation Progress and Ensuring Stability Learn techniques for tracking simulation progress and identifying potential issues during the solving process for vertical heat exchanger models. Analyzing Flow Patterns and Heat Transfer Performance Develop expertise in extracting meaningful insights from your Vertical Shell and Spiral Tube Heat Exchanger simulations: Visualizing Flow Structures and Temperature Distributions Master techniques for creating insightful visualizations of velocity fields and temperature contours to understand the behavior of Vertical Shell and Spiral Tube Heat Exchangers. Interpreting Heat Transfer Coefficients and Overall Thermal Performance Learn to analyze key performance metrics, including heat transfer coefficients and overall thermal efficiency, crucial for assessing Vertical Shell and Spiral Tube designs. Comparative Analysis: Vertical Spiral vs. Conventional Designs Explore the performance differences between vertical spiral and traditional shell-and-tube heat exchangers: Evaluating Heat Transfer Enhancement in Vertical Spiral Configurations Gain insights into how vertical spiral designs improve heat transfer rates compared to conventional shell-and-tube arrangements. Assessing the Impact of Spiral Geometry on Exchanger Performance Learn to analyze the effects of spiral pitch and tube diameter on overall heat exchanger efficiency in vertical configurations. Practical Applications and Future Learning Paths Connect simulation insights to real-world heat exchanger applications and future learning opportunities: Applying CFD Insights to Vertical Shell and Spiral Tube Heat Exchanger Design Explore how the flow patterns and heat transfer characteristics observed in CFD simulations can inform design decisions and performance improvements for vertical spiral heat exchangers. Identifying Next Steps in Advanced Heat Exchanger CFD Simulation Gain awareness of more complex topics in heat exchanger simulation and potential paths for further learning and skill development. Why This Module is Essential for Beginner Thermal Engineers This beginner-level module offers an introduction to the world of CFD in Vertical Shell and Spiral Tube Heat Exchanger analysis. By completing this simulation course, you’ll gain valuable insights into: Basic application of ANSYS Fluent for simulating Vertical Shell and Spiral Tube Heat Exchangers Essential CFD techniques for capturing flow and heat transfer phenomena in vertical and spiral configurations Practical applications of CFD analysis in thermal system design and optimization By the end of this episode, you’ll have developed foundational skills in: Setting up and running basic Vertical Shell and Spiral Tube Heat Exchanger simulations using ANSYS Fluent Interpreting simulation results to assess heat exchanger performance in vertical spiral arrangements Applying fundamental CFD insights to enhance understanding of Vertical Shell and Spiral Tube Heat Exchanger behavior This knowledge forms a solid foundation for thermal engineers and students looking to start their journey in computational heat transfer analysis, providing a springboard for more advanced studies in thermal system engineering and CFD modeling. Join us on this exciting introductory journey into the world of Vertical Shell and Spiral Tube Heat Exchanger CFD simulation, and take your first steps towards becoming a proficient thermal engineer equipped with essential computational tools for innovative heat transfer solutions!
Episode 1 13m 27s
-
-
Section 9
Spiral Heat Exchanger
-
Mastering Spiral Heat Exchanger CFD Simulation: A Beginner's Guide Welcome to the “Spiral Heat Exchanger CFD Simulation” episode of our “Heat Exchanger: BEGINNER” course. This comprehensive module introduces novices to the world of Computational Fluid Dynamics (CFD) for analyzing innovative Spiral Heat Exchangers using ANSYS Fluent. Learn how to simulate and evaluate these compact and efficient heat transfer devices, essential for applications ranging from petrochemical processing to food manufacturing. Understanding Spiral Heat Exchangers: Fundamentals and Applications Before diving into simulation techniques, let’s explore the core concepts of Spiral Heat Exchangers and their significance in modern thermal management. The Advantages of Spiral Configuration Discover how Spiral Heat Exchangers offer space-saving design, self-cleaning properties, and superior handling of viscous fluids, making them crucial in various industrial applications. Key Design Features of Spiral Heat Exchangers Explore the unique characteristics of these heat exchangers, including their spiral channels and counter-current flow arrangements that contribute to their high efficiency. Introduction to ANSYS Fluent for Spiral Heat Exchanger Analysis This section focuses on familiarizing beginners with the ANSYS Fluent software environment for spiral heat exchanger simulations: Navigating the ANSYS Fluent Interface for Spiral Geometries Gain insights into the basic layout and functionality of ANSYS Fluent, essential for efficient simulation setup and analysis of Spiral Heat Exchangers. Understanding the CFD Workflow for Spiral Heat Exchanger Simulations Learn the step-by-step process of setting up, running, and analyzing a Spiral Heat Exchanger CFD simulation in ANSYS Fluent. Setting Up a Basic Spiral Heat Exchanger Model Master the art of creating a simple simulation environment for Spiral Heat Exchanger analysis: Defining Geometry for Spiral Configurations Learn techniques for creating a basic geometry representing a Spiral Heat Exchanger, focusing on the essential features for beginner-level simulations. Configuring Material Properties and Fluid Domains Explore methods for defining and implementing the properties of working fluids and materials in your simulation, considering the unique requirements of spiral designs. Boundary Conditions for Spiral Heat Exchanger Scenarios Dive into the critical settings that ensure realistic representation of heat transfer and fluid flow in spiral configurations: Specifying Inlet and Outlet Conditions for Spiral Channels Understand how to set up appropriate inlet flow rates, temperatures, and outlet conditions for both fluid streams in a spiral arrangement. Implementing Wall and Interface Boundary Conditions Learn to define proper boundary conditions for spiral surfaces and fluid interfaces to capture realistic heat transfer behavior in curved geometries. Running CFD Simulations for Spiral Heat Exchangers Develop skills to execute and monitor your Spiral Heat Exchanger CFD simulations: Setting Up Solver Parameters for Curved Flow Simulations Master the basics of configuring solver settings, including convergence criteria and solution methods suitable for spiral heat exchanger simulations. Managing Simulation Progress and Ensuring Stability Learn techniques for tracking simulation progress and identifying potential issues during the solving process. Analyzing Flow Patterns and Heat Transfer Performance Develop expertise in extracting meaningful insights from your Spiral Heat Exchanger simulations: Visualizing Complex Flow Structures and Temperature Distributions Master techniques for creating insightful visualizations of velocity fields and temperature contours to understand the behavior of Spiral Heat Exchangers. Interpreting Heat Transfer Coefficients and Pressure Drop Learn to analyze key performance metrics, including local and overall heat transfer coefficients and pressure drop characteristics, crucial for assessing Spiral Heat Exchanger designs. Comparative Analysis: Spiral vs. Conventional Heat Exchanger Designs Explore the performance differences between spiral and traditional heat exchanger configurations: Evaluating Space Efficiency and Heat Transfer Enhancement Gain insights into how spiral designs optimize space utilization and improve heat transfer rates compared to conventional heat exchangers. Assessing Self-Cleaning Properties and Fouling Resistance Learn to analyze the unique advantages of spiral configurations in reducing fouling and maintaining performance over time. Practical Applications and Future Learning Paths Connect simulation insights to real-world heat exchanger applications and future learning opportunities: Applying CFD Insights to Spiral Heat Exchanger Design Explore how the flow patterns and heat transfer characteristics observed in CFD simulations can inform design decisions and performance improvements for Spiral Heat Exchangers. Identifying Advanced Topics in Spiral Heat Exchanger Analysis Gain awareness of more complex aspects of spiral heat exchanger simulation and potential paths for further learning and skill development. Why This Module is Essential for Beginner Thermal Engineers This beginner-level module offers an introduction to the world of CFD in Spiral Heat Exchanger analysis. By completing this simulation course, you’ll gain valuable insights into: Basic application of ANSYS Fluent for simulating Spiral Heat Exchangers Essential CFD techniques for capturing flow and heat transfer phenomena in curved geometries Practical applications of CFD analysis in innovative thermal system design and optimization By the end of this episode, you’ll have developed foundational skills in: Setting up and running basic Spiral Heat Exchanger simulations using ANSYS Fluent Interpreting simulation results to assess heat exchanger performance in spiral configurations Applying fundamental CFD insights to enhance understanding of Spiral Heat Exchanger behavior This knowledge forms a solid foundation for thermal engineers and students looking to start their journey in computational heat transfer analysis, providing a springboard for more advanced studies in thermal system engineering and CFD modeling. Join us on this exciting introductory journey into the world of Spiral Heat Exchanger CFD simulation, and take your first steps towards becoming a proficient thermal engineer equipped with essential computational tools for innovative heat transfer solutions!
Episode 1 18m 22s
-
-
Section 10
Finned Tube Heat Exchanger
-
Mastering Finned Tube Heat Exchanger CFD Simulation: A Comprehensive Guide for Beginners Welcome to the “Finned Tube Heat Exchanger CFD Simulation” episode of our “Heat Exchanger: BEGINNER” course. This in-depth module introduces learners to the world of Computational Fluid Dynamics (CFD) for analyzing highly efficient Finned Tube Heat Exchangers using ANSYS Fluent. Discover how to simulate and evaluate these crucial heat transfer devices, widely used in HVAC systems, power plants, and automotive radiators. Understanding Finned Tube Heat Exchangers: Fundamentals and Applications Before diving into simulation techniques, let’s explore the core concepts of Finned Tube Heat Exchangers and their significance in modern thermal management. The Advantages of Extended Surface Heat Transfer Discover how Finned Tube Heat Exchangers significantly increase heat transfer surface area, enhancing overall thermal efficiency in various industrial applications. Key Design Features of Finned Tube Heat Exchangers Explore the unique characteristics of these heat exchangers, including fin geometry, spacing, and arrangement, and how they contribute to superior performance across different industries. Introduction to ANSYS Fluent for Finned Tube Heat Exchanger Analysis This section focuses on familiarizing users with the ANSYS Fluent software environment for finned tube heat exchanger simulations: Navigating the ANSYS Fluent Interface for Finned Geometries Gain insights into the specialized tools and features of ANSYS Fluent essential for efficient simulation setup and analysis of Finned Tube Heat Exchangers. Understanding the CFD Workflow for Extended Surface Heat Exchangers Learn the step-by-step process of setting up, running, and analyzing a Finned Tube Heat Exchanger CFD simulation in ANSYS Fluent. Setting Up a Finned Tube Heat Exchanger Model Master the art of creating an accurate simulation environment for Finned Tube Heat Exchanger analysis: Defining Complex Geometry for Finned Tube Configurations Learn techniques for creating a detailed geometry representing a Finned Tube Heat Exchanger, focusing on the critical features that influence performance. Configuring Material Properties and Fluid Domains Explore methods for defining and implementing the properties of working fluids and fin materials in your simulation, considering the unique requirements of extended surface designs. Boundary Conditions for Finned Tube Heat Exchanger Scenarios Dive into the critical settings that ensure realistic representation of heat transfer and fluid flow in finned configurations: Specifying Inlet and Outlet Conditions for Air and Tube-side Fluids Understand how to set up appropriate inlet flow rates, temperatures, and outlet conditions for both air-side and tube-side fluids in a finned tube arrangement. Implementing Wall and Fin Surface Boundary Conditions Learn to define proper boundary conditions for tube surfaces, fin surfaces, and fluid interfaces to capture realistic heat transfer behavior in extended surface geometries. Running CFD Simulations for Finned Tube Heat Exchangers Develop skills to execute and monitor Finned Tube Heat Exchanger CFD simulations: Setting Up Solver Parameters for Complex Fin Geometries Master the configuration of solver settings, including turbulence models suitable for capturing flow patterns around finned surfaces. Managing Simulation Progress and Ensuring Convergence Learn techniques for tracking simulation progress, identifying potential issues, and ensuring solution stability in complex finned geometries. Analyzing Flow Patterns and Heat Transfer Performance Develop expertise in extracting meaningful insights from your Finned Tube Heat Exchanger simulations: Visualizing Airflow Structures and Temperature Distributions Master techniques for creating insightful visualizations of velocity fields and temperature contours to understand the behavior of Finned Tube Heat Exchangers. Interpreting Heat Transfer Coefficients and Pressure Drop Characteristics Learn to analyze key performance metrics, including local and overall heat transfer coefficients and pressure drop, crucial for assessing the efficiency of finned designs. Comparative Analysis: Fin Geometry and Arrangement Optimization Explore the performance differences between various fin designs and configurations: Evaluating the Impact of Fin Spacing on Heat Transfer Gain insights into how fin spacing affects heat transfer rates and airflow patterns in Finned Tube Heat Exchangers. Assessing the Influence of Fin Shape on Overall Performance Learn to analyze the effects of different fin shapes (e.g., plain, wavy, louvered) on heat exchanger efficiency and pressure drop. Practical Applications and Design Optimization Connect simulation insights to real-world heat exchanger applications and design improvements: Applying CFD Insights to Finned Tube Heat Exchanger Design Explore how the complex flow patterns and heat transfer characteristics observed in CFD simulations can inform design decisions and performance enhancements. Optimizing Fin Geometry for Specific Industrial Applications Learn to use simulation results to optimize fin designs for various scenarios, balancing heat transfer efficiency with manufacturing considerations and pressure drop constraints. Why This Module is Essential for Thermal Engineers and HVAC Professionals This comprehensive module offers an in-depth exploration of CFD techniques for Finned Tube Heat Exchanger analysis. By completing this simulation course, you’ll gain valuable insights into: Advanced application of ANSYS Fluent for simulating extended surface heat exchanger designs Essential CFD techniques for capturing complex flow phenomena and heat transfer mechanisms in finned geometries Practical applications of CFD analysis in optimizing Finned Tube Heat Exchangers for various industries By the end of this episode, you’ll have developed advanced skills in: Setting up and running detailed Finned Tube Heat Exchanger simulations using ANSYS Fluent Interpreting complex simulation results to assess and improve heat exchanger performance Applying sophisticated CFD insights to enhance the design and efficiency of Finned Tube Heat Exchangers This knowledge forms a robust foundation for thermal engineers, HVAC professionals, and researchers looking to leverage advanced computational methods in heat exchanger design and analysis, providing a pathway to innovation in thermal system engineering. Join us on this exciting journey into the world of Finned Tube Heat Exchanger CFD simulation, and elevate your skills in advanced thermal system design and optimization using cutting-edge computational tools!
Episode 1 12m 3s
-
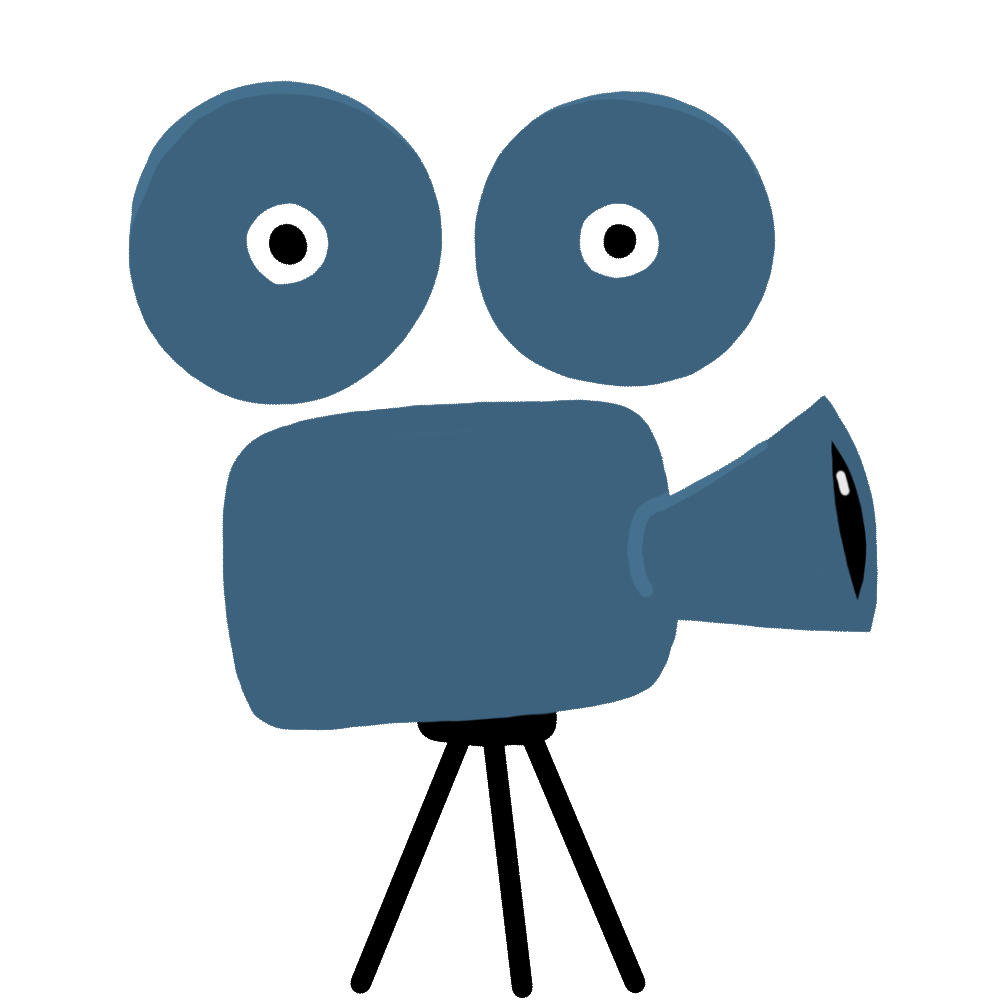
Course In Progress
Course still in development. Check back often for updates.
HEAT EXCHANGER: BEGINNER - Master CFD Simulations with ANSYS Fluent
Embark on an exciting journey into the world of Computational Fluid Dynamics (CFD) for heat exchangers with our comprehensive “HEAT EXCHANGER: BEGINNER” course. This training program is meticulously designed to introduce newcomers to the power of ANSYS Fluent in simulating and analyzing various types of heat exchangers.
Through a series of 10 carefully crafted modules, you’ll gain hands-on experience in modeling real-world heat transfer scenarios, setting a solid foundation for your career in thermal system design and analysis. Whether you’re an engineering student, a recent graduate, or a professional looking to expand your skillset, this course will equip you with the essential tools to excel in heat exchanger CFD simulations.
Course Highlights: Bridging Theory and Practice
Our HEAT EXCHANGER: BEGINNER course stands out with its focus on practical, industry-relevant simulations:
Tailored for ANSYS Fluent Beginners
Start your CFD journey with confidence:
- Step-by-step guidance through ANSYS Fluent interface and workflow
- Clear explanations of CFD principles for heat transfer applications
- Gradual progression from basic to complex heat exchanger models
Diverse Heat Exchanger Types
Explore a wide range of heat exchanger designs:
- Plate heat exchangers (Chevron, Reverse Cross Flow, Standard)
- Shell and tube configurations (with Spiral Baffle, Helical Tube)
- Specialized designs (Spiral, Finned Tube, Planar with Mixing Tabs)
Course Modules: Comprehensive Heat Exchanger Analysis
Our program covers 10 key areas of heat exchanger simulation:
1. Chevron Plate Heat Exchanger Simulation
Master the basics of plate heat exchanger modeling:
- Set up geometry and mesh for chevron plates
- Analyze fluid flow and heat transfer in corrugated channels
- Optimize plate design for enhanced thermal performance
2. Reverse Cross Flow Plate Heat Exchanger Analysis
Explore complex flow patterns in plate heat exchangers:
- Model counter-current and cross-flow regions
- Evaluate temperature distribution and heat transfer efficiency
- Optimize flow arrangement for maximum thermal performance
Advanced Heat Exchanger Designs
Dive deeper into specialized heat exchanger configurations:
3. Spiral Heat Exchanger CFD Modeling
Simulate compact and efficient heat transfer systems:
- Create geometry and mesh for spiral flow paths
- Analyze fluid dynamics in curved channels
- Evaluate heat transfer performance in spiral configurations
4. Shell and Tube Heat Exchanger with Spiral Baffle Design
Master industrial-scale heat exchanger simulations:
- Model complex geometries with spiral baffles
- Analyze flow distribution and pressure drop
- Optimize baffle design for improved heat transfer
Enhanced Surface Heat Exchangers
Explore techniques to boost heat transfer efficiency:
5. Finned Tube Heat Exchanger Performance Evaluation
Simulate extended surface heat transfer:
- Model fin geometry and tube arrangement
- Analyze air-side heat transfer and pressure drop
- Optimize fin design for maximum thermal performance
6. Standard Plate Heat Exchanger Simulation Techniques
Master fundamental plate heat exchanger modeling:
- Set up fluid domains and boundary conditions
- Analyze temperature and velocity profiles
- Evaluate overall heat transfer coefficient and effectiveness
Innovative Heat Exchanger Configurations
Tackle unique and challenging heat exchanger designs:
7. Shell and Helical Tube Heat Exchanger Analysis
Simulate advanced tubular heat exchangers:
- Model helical tube geometry within a shell
- Analyze flow patterns and heat transfer in helical paths
- Evaluate the impact of tube pitch on thermal performance
8. Planar Heat Exchanger with Mixing Tabs Analysis
Explore passive heat transfer enhancement techniques:
- Model planar channels with mixing tabs
- Analyze vortex generation and fluid mixing
- Optimize tab design for improved heat transfer
Fundamental Heat Exchanger Types
Master simulations of classic heat exchanger designs:
9. Double Pipe Counter Flow Heat Exchanger Modeling
Simulate basic counter-flow arrangements:
- Set up concentric pipe geometry and mesh
- Analyze temperature profiles and heat transfer rates
- Evaluate the impact of flow rates on exchanger performance
10. Vertical Shell and Spiral Tube Heat Exchanger Simulation
Combine multiple heat exchanger concepts:
- Model vertical shell with internal spiral tubing
- Analyze natural convection effects in the shell side
- Optimize tube spiraling for enhanced heat transfer
Why Choose Our HEAT EXCHANGER: BEGINNER Course?
This course offers unparalleled advantages for those starting their journey in heat exchanger CFD:
- Comprehensive coverage of 10 diverse heat exchanger types
- Hands-on experience with industry-standard ANSYS Fluent software
- Real-world applications directly relevant to thermal system design
- Structured learning path from basic to advanced heat exchanger models
By enrolling in our course, you’ll:
- Gain practical skills in setting up and running CFD simulations for heat exchangers
- Develop a deep understanding of heat transfer principles and their application in CFD
- Learn to interpret and analyze simulation results for heat exchanger optimization
- Build confidence in applying CFD techniques to real-world thermal system problems
Start your journey into the fascinating world of heat exchanger CFD today and transform the way you approach thermal system design and analysis!
Subscribe
Benefits of subscribing to the course
- Complete access to All chapters
- Special discount
- Free access to all new and updated content
- Cancel subscription anytime
* You will have access to the course only until your subscription ends; after that, your subscription will be automatically renewed unless you cancel it.
Congratulations
Congratulations! You have successfully subscribed to the course.
You can now start learning the course by clicking the button "Start Learning".
You can manage your subscription like canceling or upgrading the subscription, adding or changing the payment method, etc by clicking the button "Manage Subscriptions".
Add Payment Method
Please enter your payment method details.