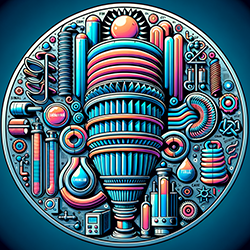
Heat Exchanger, Intermediate: CFD Simulation Training Course
Course Price: $3.00 / Month
Elevate your thermal engineering expertise with our intermediate-level “Heat Exchanger CFD Simulation” course, featuring 10 comprehensive ANSYS Fluent projects that cover diverse heat transfer applications. From analyzing triple and plate heat exchangers to simulating advanced designs with phase change materials (PCM), baffles, and nanofluids, this hands-on course builds practical simulation skills for complex thermal systems. You’ll master conjugate heat transfer modeling, explore performance optimization through geometric variations like helical fins and baffle cuts, and learn specialized techniques for renewable energy applications with solar heat exchanger simulations. Each carefully structured project combines theoretical foundations with step-by-step implementation in ANSYS Fluent (and CFX), ensuring you develop both the conceptual understanding and software proficiency needed to confidently tackle real-world thermal management challenges across multiple industries.
Solar Heat Exchanger: CFD Simulation by ANSYS Fluent
Solar Heat Exchanger CFD Simulation: Radiation and Thermal Performance Analysis A comprehensive computational fluid dynamics investigation of a specialized solar heat exchanger design featuring an absorber plate, internal flow barriers, and dual-medium heat transfer. This simulation captures the complex interplay between solar radiation, conduction, and convection mechanisms to demonstrate the thermal performance characteristics of this renewable energy system. Solar Heat Exchanger Design and Operating Principles This simulation examines a specialized heat exchanger designed to capture and transfer solar thermal energy to a working fluid. The system incorporates an innovative dual-medium approach with an air gap and absorber plate to maximize solar energy capture and transfer to the water flow through strategic internal flow barriers. System Configuration Primary Components: Solar absorber plate exposed to radiation Air gap between front plate and absorber Water flow channel with internal flow barriers Strategic internal walls for flow path extension Heat Transfer Pathway: Solar radiation absorption at absorber plate Air gap heating through radiation and convection Conduction through absorber plate Convective transfer to water flow Geometric Specifications Flow Path Design: Extended water flow route via internal barriers Absorber Orientation: Positioned for maximum solar radiation capture Internal Barriers: Multiple rows of flow obstacles for extended fluid residence time Air Gap Configuration: Optimized spacing for thermal performance Computational Approach and Radiation Modeling Mesh Characteristics Grid Type: Unstructured mesh generated in ANSYS Meshing Cell Count: 304,200 elements Resolution Focus: Enhanced density near absorber plate and internal barriers Quality Parameters: Optimized for complex geometry with multiple domains Radiation Modeling Strategy Primary Model: Discrete Ordinates (DO) radiation model Model Capabilities: Handles scattering media Accounts for semi-transparent boundaries Manages specular surfaces Supports wavelength-dependent transmission Solar Loading: Solar Ray Tracing model implementation Solar Parameters: Direct solar radiation: 1150 W/m² Diffuse solar radiation: 80 W/m² Incidence angle: Perpendicular to absorber plane Operating Conditions Water Flow: 4 m/s inlet velocity at 30°C Outlet Condition: Atmospheric pressure Air Gap: Natural convection and radiation heat transfer Thermal Boundaries: Solar radiation on absorber surface Results and Performance Analysis Thermal Characteristics Temperature Distribution: Visualization of thermal gradients throughout the system Heat Transfer Pathways: Identification of primary energy transfer routes Absorber Performance: Temperature profile across the solar collector surface Water Temperature Gain: Progressive heating along the extended flow path Flow Behavior Velocity Patterns: Analysis of flow development around internal barriers Pressure Distribution: Characterization of pressure drop across the exchanger Recirculation Zones: Identification of potential thermal mixing regions Barrier Effectiveness: Assessment of flow path extension and residence time Radiation Effects Absorption Patterns: Distribution of captured solar energy across absorber Air Gap Thermal Gradient: Temperature stratification in the front air layer Direct vs. Diffuse Contribution: Relative impact of radiation components Thermal Losses: Evaluation of energy not transferred to working fluid Performance Metrics Overall Efficiency: Ratio of captured energy to incident solar radiation Temperature Rise: Quantification of water temperature increase Heat Transfer Rate: Total thermal energy transferred to water flow Pressure Drop: Hydraulic resistance through the extended flow path Engineering Insights Design Optimization: Guidance for barrier placement and configuration Performance Enhancement: Strategies for improving solar absorption and transfer Operational Parameters: Effects of flow rate on thermal efficiency System Scalability: Considerations for larger implementation This detailed CFD simulation provides valuable insights into the thermal-hydraulic behavior of this specialized solar heat exchanger design. The results demonstrate the effectiveness of combining strategic flow path extension with optimized solar absorption to achieve efficient thermal energy capture and transfer. The comprehensive radiation modeling approach ensures accurate representation of the complex heat transfer mechanisms involved in solar thermal systems, providing reliable guidance for design optimization and performance prediction in renewable energy applications.
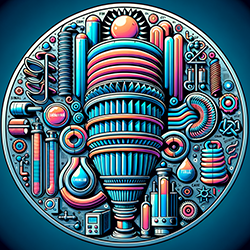
Heat Exchanger, Intermediate: CFD Simulation Training Course
Course Price: $3.00 / Month
Elevate your thermal engineering expertise with our intermediate-level “Heat Exchanger CFD Simulation” course, featuring 10 comprehensive ANSYS Fluent projects that cover diverse heat transfer applications. From analyzing triple and plate heat exchangers to simulating advanced designs with phase change materials (PCM), baffles, and nanofluids, this hands-on course builds practical simulation skills for complex thermal systems. You’ll master conjugate heat transfer modeling, explore performance optimization through geometric variations like helical fins and baffle cuts, and learn specialized techniques for renewable energy applications with solar heat exchanger simulations. Each carefully structured project combines theoretical foundations with step-by-step implementation in ANSYS Fluent (and CFX), ensuring you develop both the conceptual understanding and software proficiency needed to confidently tackle real-world thermal management challenges across multiple industries.
Solar Heat Exchanger: CFD Simulation by ANSYS Fluent
Solar Heat Exchanger CFD Simulation: Radiation and Thermal Performance Analysis A comprehensive computational fluid dynamics investigation of a specialized solar heat exchanger design featuring an absorber plate, internal flow barriers, and dual-medium heat transfer. This simulation captures the complex interplay between solar radiation, conduction, and convection mechanisms to demonstrate the thermal performance characteristics of this renewable energy system. Solar Heat Exchanger Design and Operating Principles This simulation examines a specialized heat exchanger designed to capture and transfer solar thermal energy to a working fluid. The system incorporates an innovative dual-medium approach with an air gap and absorber plate to maximize solar energy capture and transfer to the water flow through strategic internal flow barriers. System Configuration Primary Components: Solar absorber plate exposed to radiation Air gap between front plate and absorber Water flow channel with internal flow barriers Strategic internal walls for flow path extension Heat Transfer Pathway: Solar radiation absorption at absorber plate Air gap heating through radiation and convection Conduction through absorber plate Convective transfer to water flow Geometric Specifications Flow Path Design: Extended water flow route via internal barriers Absorber Orientation: Positioned for maximum solar radiation capture Internal Barriers: Multiple rows of flow obstacles for extended fluid residence time Air Gap Configuration: Optimized spacing for thermal performance Computational Approach and Radiation Modeling Mesh Characteristics Grid Type: Unstructured mesh generated in ANSYS Meshing Cell Count: 304,200 elements Resolution Focus: Enhanced density near absorber plate and internal barriers Quality Parameters: Optimized for complex geometry with multiple domains Radiation Modeling Strategy Primary Model: Discrete Ordinates (DO) radiation model Model Capabilities: Handles scattering media Accounts for semi-transparent boundaries Manages specular surfaces Supports wavelength-dependent transmission Solar Loading: Solar Ray Tracing model implementation Solar Parameters: Direct solar radiation: 1150 W/m² Diffuse solar radiation: 80 W/m² Incidence angle: Perpendicular to absorber plane Operating Conditions Water Flow: 4 m/s inlet velocity at 30°C Outlet Condition: Atmospheric pressure Air Gap: Natural convection and radiation heat transfer Thermal Boundaries: Solar radiation on absorber surface Results and Performance Analysis Thermal Characteristics Temperature Distribution: Visualization of thermal gradients throughout the system Heat Transfer Pathways: Identification of primary energy transfer routes Absorber Performance: Temperature profile across the solar collector surface Water Temperature Gain: Progressive heating along the extended flow path Flow Behavior Velocity Patterns: Analysis of flow development around internal barriers Pressure Distribution: Characterization of pressure drop across the exchanger Recirculation Zones: Identification of potential thermal mixing regions Barrier Effectiveness: Assessment of flow path extension and residence time Radiation Effects Absorption Patterns: Distribution of captured solar energy across absorber Air Gap Thermal Gradient: Temperature stratification in the front air layer Direct vs. Diffuse Contribution: Relative impact of radiation components Thermal Losses: Evaluation of energy not transferred to working fluid Performance Metrics Overall Efficiency: Ratio of captured energy to incident solar radiation Temperature Rise: Quantification of water temperature increase Heat Transfer Rate: Total thermal energy transferred to water flow Pressure Drop: Hydraulic resistance through the extended flow path Engineering Insights Design Optimization: Guidance for barrier placement and configuration Performance Enhancement: Strategies for improving solar absorption and transfer Operational Parameters: Effects of flow rate on thermal efficiency System Scalability: Considerations for larger implementation This detailed CFD simulation provides valuable insights into the thermal-hydraulic behavior of this specialized solar heat exchanger design. The results demonstrate the effectiveness of combining strategic flow path extension with optimized solar absorption to achieve efficient thermal energy capture and transfer. The comprehensive radiation modeling approach ensures accurate representation of the complex heat transfer mechanisms involved in solar thermal systems, providing reliable guidance for design optimization and performance prediction in renewable energy applications.
-
Section 1
Traditional Heat Exchanger Configurations
-
Triple Heat Exchanger, CFD Simulation Ansys Fluent Training An in-depth computational fluid dynamics analysis of a triple concentric tube heat exchanger, exploring the complex thermal interactions between three fluid streams flowing through concentrically arranged pipes. This project demonstrates complete simulation workflow from geometry creation through results interpretation, providing valuable insights into advanced heat exchanger performance. Project Overview This simulation investigates a triple concentric tube heat exchanger (TCTHE), an enhanced design that improves upon traditional double-pipe configurations by adding an intermediate tube. The model features three distinct flow channels with different temperature fluids, creating multiple heat transfer interfaces within a compact arrangement. Key Simulation Parameters Geometry: Three-dimensional concentric tubes modeled in ANSYS DesignModeler Mesh: 1.96 million elements generated using ANSYS Meshing Flow Conditions: Laminar flow regime for all domains Thermal Conditions: Temperature differentials between all three fluid streams Methodology and Approach Geometric Configuration The heat exchanger consists of three concentrically arranged tubes creating separate flow paths: Inner tube: Water at 280K with 0.1 kg/s mass flow rate Middle annulus: Water at 330K with 0.05 kg/s mass flow rate Outer annulus: Water at 290K with 0.05 m/s inlet velocity Simulation Setup Laminar flow model implementation Energy equation activation for thermal analysis Appropriate boundary conditions at inlets, outlets, and walls Interface definitions for thermal interactions between domains Solution Strategy Sequential solving of flow and energy equations Convergence monitoring for momentum and thermal residuals Post-processing of temperature fields and heat transfer metrics Results and Analysis Temperature Distribution The simulation reveals comprehensive temperature patterns showing: Gradual cooling of the middle hot stream along the exchanger length Simultaneous heating of both inner and outer fluid streams Complex thermal gradients at the interfaces between domains Heat Transfer Performance Quantification of heat exchange between each pair of fluid streams Analysis of local and overall heat transfer coefficients Effectiveness evaluation compared to conventional designs Engineering Insights Demonstration of the TCTHE’s ability to facilitate simultaneous heat exchange between multiple fluid streams Identification of thermal performance characteristics specific to triple concentric arrangements Practical considerations for design optimization and operational parameters Learning Outcomes This project provides practical experience in: Modeling complex multi-domain heat exchanger geometries Configuring multi-stream heat transfer simulations Analyzing thermal interactions between multiple fluid domains Evaluating performance metrics for advanced heat exchanger designs The simulation techniques demonstrated are applicable to various thermal management challenges across process industries, HVAC systems, and energy recovery applications.
Episode 1 12m 18s -
Plate Heat Exchanger CFD Simulation by ANSYS Fluent Training A comprehensive computational fluid dynamics analysis of a 4-layer plate heat exchanger design, demonstrating the thermal-hydraulic performance characteristics and heat transfer mechanisms between alternating hot and cold fluid channels. This simulation provides valuable insights into plate heat exchanger behavior through detailed visualization of temperature distributions, flow patterns, and quantitative performance metrics. Project Overview This simulation investigates a 4-layer plate heat exchanger configuration with alternating hot and cold water channels. The model captures the complex fluid flow and heat transfer phenomena occurring within the compact plate arrangement, demonstrating how thermal energy is effectively transferred between the fluid streams through the separating plates. Key Simulation Parameters Configuration: 4-layer plate heat exchanger with alternating hot and cold channels Hot Fluid: Water at 286.2K with 0.0045 kg/s mass flow rate Cold Fluid: Water at 276.5K with 0.00361 kg/s mass flow rate Mesh: Unstructured grid with approximately 2,273,000 elements Methodology and Approach Geometric Configuration The heat exchanger consists of four parallel flow channels arranged in alternating hot and cold layers: Layers 1 and 3: Cold fluid channels (heating process) Layers 2 and 4: Hot fluid channels (cooling process) Defined inlet and outlet regions for each fluid stream Solid plates separating fluid channels (not explicitly mentioned but implied) Simulation Setup Solver Configuration: Pressure-based, steady-state simulation Turbulence Model: Standard k-epsilon with standard wall functions Energy Equation: Enabled for heat transfer analysis Discretization Schemes: Momentum: Second-order upwind Energy: Second-order upwind Turbulence parameters: First-order upwind Solution Algorithm: SIMPLE pressure-velocity coupling Boundary Conditions Hot Inlet: 286.2K at 0.0045 kg/s with 2% turbulence intensity Cold Inlet: 276.5K at 0.00361 kg/s with 2% turbulence intensity Hydraulic Diameter: 0.003m for both inlets Initialization Parameters: Zero gauge pressure, specified velocity components and turbulence parameters Results and Analysis Temperature Distribution The simulation reveals the thermal behavior across all four layers: Progressive temperature change along the flow path in each channel Hot fluid cooling from 286.2K to 281.213K Cold fluid heating from 276.5K to 282.725K Temperature convergence at exits (~282K for both streams) Flow Characteristics Detailed velocity contours showing flow distribution within each layer Streamline visualizations demonstrating flow patterns and potential recirculation zones Impact of plate geometry on local flow behavior Heat Transfer Performance Quantified heat transfer rate from hot fluid: 93.8503W Quantified heat absorption by cold fluid: 93.9754W Energy balance verification with less than 0.2% discrepancy Thermal effectiveness assessment based on inlet-outlet temperature differences Engineering Insights The simulation demonstrates several key aspects of plate heat exchanger performance: Effective thermal energy transfer between alternating fluid streams Nearly identical exit temperatures despite different inlet conditions Balanced heat transfer rates confirming simulation accuracy Influence of flow distribution on local heat transfer effectiveness This analysis provides valuable information for design optimization, performance prediction, and operational parameter selection for plate heat exchangers in various industrial applications including HVAC systems, food processing, and chemical industries.
Episode 2 15m 24s
-
-
Section 2
Advanced Shell and Tube Designs
-
Baffle Cut Effect on Shell and Tube Heat Exchanger Efficiency, Conjugated Heat Transfer A detailed computational fluid dynamics investigation into the influence of baffle configuration on shell and tube heat exchanger performance, with specific focus on conjugated heat transfer effects. This study examines the complex relationship between thermal enhancement and hydraulic penalties associated with baffle implementation, providing valuable design insights for optimizing heat exchanger efficiency. Heat Exchanger Configuration and Design Parameters This simulation explores a shell and tube heat exchanger featuring aluminum baffles with a 36% cut ratio. The model incorporates conjugated heat transfer to accurately capture the thermal interaction between fluid domains and solid baffle structures, demonstrating how baffle thermal conductivity contributes to overall heat transfer enhancement. Geometric Specifications Shell Dimensions: 600mm length, 90mm diameter Tube Arrangement: 7 tubes in triangular pattern, 20mm outer diameter Tube Spacing: 30mm center-to-center distance Baffle Configuration: 6 baffles with 4mm thickness Baffle Spacing: 86mm center-to-center distance Baffle Cut Ratio: 36% of shell diameter Simulation Setup Mesh: Unstructured grid with 1,953,754 elements Near-Wall Treatment: Boundary layer mesh for appropriate y+ values Flow Conditions: Water at 300K entering shell side at 0.5 kg/m³ Thermal Boundary: Constant tube wall temperature of 450K Methodology and Physical Models Material Properties Working Fluid: Water with temperature-dependent properties Property Definition: Piecewise-linear functions for density, viscosity, specific heat, and thermal conductivity Baffle Material: Aluminum with high thermal conductivity Numerical Approach Solver Type: Pressure-based, steady-state simulation Turbulence Model: Realizable k-ε with standard wall functions Solution Algorithm: SIMPLE pressure-velocity coupling Discretization: First-order upwind schemes for momentum, energy, and turbulence parameters Initialization: Standard method with -0.7 m/s inlet velocity Boundary Conditions Shell Inlet: Mass flow inlet at 300K Shell Outlet: Zero gauge pressure outlet Shell Wall: Adiabatic condition (zero heat flux) Tube Walls: Constant temperature at 450K Baffles: Solid aluminum with conjugated heat transfer Results and Performance Analysis Thermal Performance Exit Temperature: Shell-side fluid heated to approximately 360K Temperature Rise: 60K increase from inlet to outlet Heat Transfer Enhancement: Accelerated temperature diffusion due to baffle thermal conductivity Heat Transfer Coefficient: Convergence demonstrated with increasing iterations Flow Characteristics Flow Pattern: Complex cross-flow arrangement induced by baffles Pressure Drop: Approximately 1 kPa across the heat exchanger Velocity Distribution: Increased local velocities in baffle-restricted regions Conjugated Heat Transfer Effects Baffle Thermal Contribution: Enhanced temperature distribution through conductive heat paths Thermal Gradients: Visualization of temperature fields across fluid and solid domains Heat Transfer Mechanism: Combined convective and conductive pathways through strategic baffle placement Engineering Implications Performance Trade-offs: Balance between thermal enhancement and hydraulic penalties Design Optimization: Insights into optimal baffle cut ratio and spacing Efficiency Considerations: Improved understanding of how baffle configuration affects overall heat exchanger performance This comprehensive simulation demonstrates the significant impact of baffle design parameters on shell and tube heat exchanger efficiency, providing valuable guidance for thermal system designers seeking to optimize heat transfer performance while managing pressure drop constraints.
Episode 1 19m 51s -
Shell and Tube Heat Exchanger with Baffle Cut and Mixture Nano Fluid by ANSYS Fluent A sophisticated computational fluid dynamics investigation exploring the combined effects of baffle configuration and nanofluid application on shell and tube heat exchanger performance. This simulation demonstrates how thermal enhancement strategies can be synergistically implemented to achieve superior heat transfer characteristics while maintaining acceptable hydraulic performance. Nanofluid Enhancement in Heat Exchanger Applications This simulation examines a shell and tube heat exchanger incorporating two advanced heat transfer enhancement techniques: strategic baffle placement and Al₂O₃-water nanofluid as the working medium. The study demonstrates how nanofluids can significantly improve thermal performance through increased effective thermal conductivity, while baffles create beneficial flow patterns that further enhance heat transfer capabilities. Performance Enhancement Mechanisms Nanofluid Benefits: Increased thermal conductivity without significant viscosity penalties Baffle Configuration: Improved shell-side flow distribution and extended flow path Combined Effects: Synergistic enhancement through complementary thermal improvement strategies Geometric Configuration and Model Parameters Heat Exchanger Specifications Shell Dimensions: 1m diameter, 4.5m length Shell-Side Fluid: Al₂O₃-water nanofluid (cold stream) Tube-Side Fluid: Water (hot stream) Baffle Arrangement: 4 baffles with 0.7m length Tube Configuration: 0.15m diameter tubes with 3m active length Connection Nozzles: 0.15m shell-side, 0.3m tube-side Computational Domain Mesh Structure: 450,980 elements generated in ANSYS Meshing Domain Regions: Shell-side flow path with baffles, tube-side flow path, solid tube walls Interface Definitions: Fluid-solid interfaces for conjugated heat transfer Simulation Methodology and Approach Multiphase Modeling Strategy Model Selection: Mixture model for nanofluid simulation Phase Definition: Water as continuous phase, Al₂O₃ particles as dispersed phase Interaction Mechanisms: Interphase drag, particle distribution, and thermal effects Numerical Methods Solver Configuration: Pressure-based coupled solver Discretization: Second-order schemes for improved accuracy Turbulence Model: k-ε model with standard wall functions Solution Process: Steady-state simulation with appropriate convergence criteria Material Properties Nanoparticles: Al₂O₃ with 40 W/m·K thermal conductivity, 3970 kg/m³ density Base Fluid: Water with standard thermophysical properties Effective Properties: Calculated based on mixture theory and particle concentration Temperature Dependence: Constant properties assumed for this simulation Results and Performance Analysis Thermal Performance Characteristics Temperature Distribution: Visualized through contours showing thermal gradients Heat Transfer Enhancement: Quantification of improvement over conventional fluids Nanofluid Effectiveness: Analysis of thermal conductivity enhancement contribution Flow Pattern Visualization Streamline Analysis: Path lines demonstrating complex flow patterns induced by baffles Recirculation Zones: Identification of mixing regions promoting heat transfer Velocity Distribution: Examination of flow acceleration in baffle-restricted areas Engineering Implications Design Considerations: Guidance for optimal baffle placement with nanofluids Performance Optimization: Balance between thermal enhancement and pumping power Practical Implementation: Insights into nanofluid concentration effects and stability requirements This comprehensive simulation provides valuable insights into the combined thermal enhancement potential of baffles and nanofluids in shell and tube heat exchangers. The results demonstrate how strategic integration of multiple enhancement techniques can achieve superior thermal performance beyond what either approach could accomplish independently, offering promising directions for heat exchanger design optimization in various industrial applications.
Episode 2 15m 40s
-
-
Section 3
Phase Change Material Applications
-
PCM in Shell and Tube Finned Heat Exchanger Simulation A comprehensive computational fluid dynamics investigation of thermal energy storage using phase change materials (PCMs) within a finned shell and tube heat exchanger configuration. This simulation captures the complex transient behavior of PCM melting processes, demonstrating the effectiveness of latent heat storage systems for thermal management applications. Thermal Energy Storage with Phase Change Materials This simulation explores the dynamic thermal behavior of a shell and tube heat exchanger incorporating phase change materials as the storage medium. The study focuses on capturing the complex phase transformation process and associated heat transfer mechanisms that make PCMs valuable for thermal energy storage applications. PCM Operating Principles Energy Storage Mechanism: Latent heat absorption during solid-to-liquid phase transition Energy Release Process: Heat dissipation during liquid-to-solid phase change Application Versatility: Thermal regulation in both heating and cooling systems Diurnal Cycle Utilization: Heat absorption during daytime and release during nighttime Geometric Configuration and System Design Heat Exchanger Architecture Shell Design: Cylindrical tank containing uniformly distributed PCM Heat Transfer Elements: Copper tube with winding path through PCM medium Enhancement Features: Cross-shaped copper fins along tube pathway Material Selection: Copper components for high thermal conductivity Tube Specifications: 0.001m wall thickness for efficient heat transfer Computational Domain Mesh Characteristics: Unstructured grid with 2,448,380 elements Domain Regions: PCM volume, copper tube, copper fins, fluid flow path Boundary Definition: Interfaces between different materials and phases Simulation Methodology and Physical Models Phase Change Modeling Approach Model Selection: Solidification and Melting model for phase transition simulation Phase Transition Parameters: Solidus temperature: 314.15K Liquidus temperature: 317.15K Latent heat of fusion: 255,000 J/kg Material Properties PCM Characteristics: Paraffin with following properties: Density: 750 kg/m³ Specific heat capacity: 2000 J/kg·K Thermal conductivity: 0.2 W/m·K Viscosity: 0.008 kg/m·s Heat Transfer Fluid: Water at 325.15K with 1.4973 kg/s mass flow rate Structural Components: Copper tubes and fins with high thermal conductivity Numerical Approach Simulation Type: Transient analysis with 1200-second duration Time Step Configuration: Appropriate stepping for phase change capture Convergence Criteria: Suitable tolerances for energy and phase equations Results and Performance Analysis Thermal Evolution and Phase Transition Temperature Distribution: Visualization of thermal gradients throughout the storage medium Melting Front Progression: Tracking of solid-liquid interface movement over time Liquid Fraction Development: Quantification of PCM melting as a function of time Heat Transfer Effectiveness: Analysis of temperature rise near tube surfaces System Performance Metrics Energy Storage Capacity: Evaluation of total thermal energy absorbed by PCM Charging Rate: Assessment of system response to heat input Thermal Gradients: Identification of temperature distribution patterns Fin Effectiveness: Contribution of extended surfaces to overall heat transfer Engineering Insights Design Optimization: Guidance for fin placement and tube routing Operational Parameters: Influence of flow rate and inlet temperature System Response: Transient behavior during charging cycle Efficiency Considerations: Balance between thermal performance and material usage This detailed simulation provides valuable insights into the dynamic behavior of PCM-based thermal energy storage systems, demonstrating how finned shell and tube configurations can effectively manage the inherent thermal conductivity limitations of phase change materials. The results highlight the potential of such systems for applications requiring efficient thermal energy storage and release cycles, including building climate control, solar thermal systems, and waste heat recovery.
Episode 1 19m 23s -
PCM in Three-Layer Tube Heat Exchanger Simulation A detailed computational fluid dynamics analysis of thermal energy storage using Erythritol phase change material (PCM) in a three-layer tube heat exchanger with copper fins. This simulation captures the complex phase transition dynamics and heat transfer mechanisms over an extended time period, demonstrating the effectiveness of PCM systems for thermal energy management applications. Phase Change Material for Thermal Energy Storage This simulation investigates the thermal behavior and phase transition dynamics of Erythritol PCM embedded in a three-layer tube heat exchanger. The study demonstrates how PCMs can effectively store and release thermal energy through latent heat mechanisms, providing valuable insights into their application for sustainable energy management. PCM Working Principles Energy Storage Mechanism: Latent heat absorption during solid-to-liquid transition Energy Release Process: Heat dissipation during liquid-to-solid transformation Thermal Regulation: Temperature stabilization through phase change properties Diurnal Applications: Solar energy capture during day and release during night Heat Exchanger Design and Configuration System Architecture Exchanger Type: Three-layer tube heat exchanger with enhanced surfaces Material Selection: Copper tubes and fins for superior thermal conductivity PCM Medium: Erythritol as the phase change material in storage layer Heat Transfer Fluid: Liquid silicone circulating through inner tube Enhancement Features: Copper fins for improved thermal conductance Computational Domain Mesh Characteristics: Hybrid structured/unstructured grid with 107,718 elements Domain Components: Inner tube flow path, copper tube walls, fins, PCM region Boundary Interfaces: Coupled wall conditions between different materials Simulation Methodology and Physical Models Phase Change Modeling Approach Model Selection: Solidification and Melting module for phase transition simulation Simulation Duration: Extended 12,000-second analysis to capture complete phase dynamics Time Step Configuration: Appropriate stepping for phase change resolution Material Properties and Parameters PCM Characteristics: Erythritol with defined: Solidus and liquidus temperatures Latent heat of fusion Density, specific heat, and thermal conductivity Heat Transfer Fluid: Liquid silicone at 343.15K with 1 m/s inlet velocity Structural Components: Copper with high thermal conductivity for tubes and fins Boundary Conditions Inlet Conditions: 1 m/s velocity, 343.15K temperature for silicone fluid Outer Walls: Adiabatic condition (zero heat flux) Inner Walls: Automatically coupled thermal interfaces Initial Conditions: Starting temperature and phase distribution Results and Performance Analysis Thermal Evolution and Phase Dynamics Temperature Distribution: Visualization of thermal gradients throughout the PCM medium Phase Front Progression: Tracking of solid-liquid interface movement over time Liquid Fraction Development: Quantification of PCM melting progression Heat Transfer Pathways: Analysis of conduction through fins and convection in liquid regions Performance Characteristics Energy Storage Capacity: Evaluation of thermal energy absorbed as latent heat System Response: Transient behavior during the charging cycle Fin Effectiveness: Impact of extended surfaces on heat transfer enhancement Thermal Penetration: Heat distribution patterns from tube surface into PCM volume Engineering Insights Design Considerations: Optimization guidance for fin geometry and spacing Operational Parameters: Influence of flow rate and inlet temperature System Efficiency: Balance between thermal performance and material utilization Application Potential: Suitability for various thermal management scenarios This comprehensive simulation provides valuable insights into the behavior of PCM-based thermal energy storage systems, highlighting the critical role of enhanced heat transfer surfaces in overcoming the inherent thermal conductivity limitations of phase change materials. The results demonstrate the effectiveness of copper fins in accelerating the charging process and improving overall system performance, offering practical design guidance for thermal energy storage applications ranging from building climate control to industrial waste heat recovery systems.
Episode 2 27m 44s
-
-
Section 4
Advanced Physics and Alternative Methods
-
Plate Heat Exchanger CFD Simulation: Viscous Heating and Conjugated Heat Transfer A comprehensive computational fluid dynamics analysis of a novel plate heat exchanger design incorporating parallel solid plates with corner-mounted flow channels. This simulation captures the complex interplay between convective and conductive heat transfer mechanisms, demonstrating the unique thermal characteristics of this unconventional heat exchanger configuration. Heat Exchanger Configuration and Design Approach This simulation investigates a specialized plate heat exchanger design featuring four solid plates with integrated corner pipes, creating a unique thermal pathway that differs from conventional plate heat exchanger configurations. The study demonstrates how this arrangement facilitates heat transfer through a combination of convection in the fluid channels and conduction through the solid plates. Geometric Specifications Plate Dimensions: 2m × 2m with 0.2m thickness Flow Channels: Four corner-mounted pipes with 0.2m diameter and 1.1m length Material Configuration: Single-part solid construction with integrated flow passages Flow Arrangement: Counter-flow configuration with opposing inlet locations Computational Domain Mesh Structure: Unstructured grid with 2,216,379 elements Domain Components: Solid plates, fluid channels, fluid-solid interfaces Discretization Quality: Refined mesh near fluid-solid boundaries for accurate CHT modeling Simulation Methodology and Physical Models Conjugated Heat Transfer Approach Heat Transfer Mechanisms: Simultaneous modeling of: Convection between fluid and pipe walls Conduction through solid plates Thermal interface coupling between domains Solution Strategy: Pressure-based solver for incompressible flow Analysis Type: Steady-state simulation with coupled energy equation Operating Conditions Working Fluid: Water with temperature-dependent properties Flow Parameters: Equal velocity in all channels Temperature Differential: 20°C and 40°C inlet temperatures in counter-flow arrangement Boundary Conditions: Specified velocity inlets and pressure outlets Simplifications: Negligible gravitational effects Modeling Considerations Viscous Heating: Inclusion of energy dissipation due to fluid friction Turbulence Model: Appropriate model for pipe flow conditions Material Properties: Temperature-dependent thermal properties for water Interface Treatment: Continuous temperature and heat flux at fluid-solid boundaries Results and Performance Analysis Thermal Characteristics Temperature Distribution: Visualization of thermal gradients across solid plates Heat Transfer Pathways: Identification of primary conduction paths between channels Thermal Spreading: Analysis of heat diffusion through solid medium Temperature Profiles: Examination of fluid temperature evolution along flow paths Flow Behavior Pressure Distribution: Characterization of pressure gradients in flow channels Velocity Patterns: Analysis of flow development in pipe sections Turbulence Characteristics: Evaluation of turbulent kinetic energy distribution Viscous Effects: Assessment of viscous heating contribution to thermal performance Performance Metrics Heat Transfer Effectiveness: Evaluation of overall thermal efficiency Temperature Approach: Analysis of terminal temperature differences Pressure Drop: Quantification of hydraulic resistance Flow Distribution: Assessment of flow uniformity across channels Engineering Insights Design Implications: Guidance for optimizing plate thickness and channel placement Performance Enhancement: Strategies for improving thermal effectiveness Material Selection: Impact of solid thermal conductivity on overall performance Operational Considerations: Effects of flow rate on heat transfer characteristics This detailed simulation provides valuable insights into the thermal-hydraulic behavior of this unconventional plate heat exchanger design. The results demonstrate how the combination of strategic channel placement and solid conduction pathways can create effective heat transfer between fluid streams, offering design guidance for specialized heat transfer applications where traditional plate heat exchanger configurations may not be suitable.
Episode 1 13m 37s -
Plate Heat Exchanger CFD Simulation with ANSYS CFX: Conjugated Heat Transfer Analysis A detailed computational fluid dynamics investigation of a specialized plate heat exchanger design featuring solid plates with corner-mounted flow channels. This simulation leverages ANSYS CFX to capture the complex interplay between convective and conductive heat transfer mechanisms, providing insights into thermal performance characteristics under counter-flow operating conditions. Heat Exchanger Configuration and Design Parameters This simulation examines a unique plate heat exchanger configuration consisting of four solid plates with integrated corner pipes, creating a specialized thermal pathway that combines convective heat transfer in fluid channels with conductive heat transfer through solid plates. The 2.5D modeling approach provides comprehensive insights into the thermal-hydraulic behavior of this system. Geometric Specifications Plate Dimensions: 2m × 2m with 0.1m thickness Flow Channels: Four corner-mounted pipes with 0.15m diameter and 1.1m length Material Configuration: Single-part construction with integrated solid and fluid domains Flow Arrangement: Counter-flow configuration with temperature differential of 20°C Computational Domain Mesh Characteristics: Unstructured grid with 5,096,686 elements Near-Wall Treatment: Five inflation layers within pipe regions for boundary layer resolution Domain Integration: Combined solid-fluid mesh with preserved interface continuity Mesh Quality: Enhanced resolution at critical heat transfer interfaces Simulation Methodology and Physical Models Conjugated Heat Transfer Approach Heat Transfer Mechanisms: Simultaneous modeling of: Convective transport between fluid and pipe walls Conductive diffusion through solid plates Thermal coupling at fluid-solid interfaces Energy Formulation: Thermal Energy model for incompressible flow Analysis Type: Steady-state simulation with coupled thermal-fluid solution Numerical Methods and Models Turbulence Model: k-epsilon with Scalable Wall Function Discretization Scheme: High Resolution Advection Scheme for improved accuracy Turbulence Numerics: High Resolution approach for turbulence equations Convergence Criteria: Appropriate residual targets for momentum and energy Operating Conditions Working Fluid: Water with temperature-dependent properties Flow Parameters: Uniform velocity in all channels Temperature Differential: 20°C and 40°C inlet temperatures in opposing flow directions Simplifications: Negligible gravitational effects, steady-state conditions Results and Performance Analysis Thermal Characteristics Temperature Distribution: Visualization of thermal gradients throughout the system Heat Transfer Pathways: Identification of primary conduction routes between channels Thermal Spreading: Analysis of heat diffusion patterns within solid plates Temperature Contours: Clear visualization of isothermal lines across the domain Flow Behavior Pressure Distribution: Characterization of pressure fields in flow channels Velocity Patterns: Analysis of flow development in pipe sections Turbulence Characteristics: Evaluation of turbulent kinetic energy distribution Flow Uniformity: Assessment of flow distribution across parallel channels Performance Metrics Heat Transfer Effectiveness: Evaluation of thermal exchange efficiency Temperature Profiles: Analysis of fluid temperature evolution along flow paths Pressure Drop: Quantification of hydraulic resistance through the system Thermal Gradients: Assessment of temperature differential across solid medium Engineering Insights Design Implications: Guidance for optimizing plate thickness and pipe placement Velocity Effects: Confirmation of flow rate impact on convective heat transfer Heat Path Optimization: Strategies for enhancing conductive pathways System Efficiency: Balance between thermal performance and pressure loss This comprehensive CFD simulation using ANSYS CFX provides valuable insights into the thermal-hydraulic behavior of this specialized plate heat exchanger design. The results demonstrate the effectiveness of the counter-flow arrangement and the significant role of conduction through the solid plates in facilitating heat transfer between the fluid streams. The high-resolution numerical approach with enhanced boundary layer treatment ensures accurate capture of the convective heat transfer processes, providing reliable guidance for design optimization and performance prediction in similar heat exchanger applications.
Episode 2 1h 29m 15s
-
-
Section 5
Specialized Configurations and Applications
-
Shell and Tube Heat Exchanger with Helical Fins and Nanofluid: CFD Analysis A comprehensive computational fluid dynamics investigation of an enhanced shell and tube heat exchanger design featuring helical fins and Al₂O₃-water nanofluid as the working medium. This simulation demonstrates how geometric modifications and advanced working fluids can synergistically improve heat transfer performance in industrial heat exchange applications. Advanced Heat Exchanger Design and Enhancement Strategies This simulation examines a shell and tube heat exchanger incorporating two significant performance enhancement techniques: helical fins in the shell-side flow path and Al₂O₃-water nanofluid as the working medium. The study demonstrates how these modifications work in concert to improve thermal performance through extended flow paths and enhanced thermal properties. Enhancement Mechanisms Helical Fin Benefits: Extended flow path length, increased turbulence, and larger heat transfer surface area Nanofluid Advantages: Improved thermal conductivity without significant viscosity penalties Combined Effect: Synergistic performance enhancement through complementary mechanisms Geometric Configuration and Model Development Heat Exchanger Architecture Basic Type: Shell and tube configuration with tube bundle Enhancement Features: Helical fins installed in shell-side flow path Flow Arrangement: Counter-flow or cross-flow configuration (as specified) Fin Design: Optimized helical geometry for flow guidance and surface area extension Computational Domain Mesh Characteristics: Unstructured grid generated in ANSYS Meshing Domain Components: Shell-side volume with fins, tube bundle, fluid regions Resolution Requirements: Refined mesh near fin surfaces and tube walls Element Quality: Optimized for complex geometry with curved surfaces Simulation Methodology and Nanofluid Modeling Nanofluid Implementation Approach Modeling Strategy: Single-phase effective property method Alternative Approach: Multiphase mixture model (noted as higher computational cost) Property Calculation: Thermophysical properties derived from base fluid and nanoparticle characteristics: Effective density Modified specific heat capacity Enhanced thermal conductivity Adjusted viscosity Physical Models and Numerical Methods Flow Regime: Appropriate turbulence model for complex geometry Heat Transfer: Conjugate modeling of fluid and solid domains Discretization Schemes: Higher-order methods for improved accuracy Solution Strategy: Pressure-based solver with suitable coupling algorithm Operating Conditions Working Fluids: Al₂O₃-water nanofluid and secondary fluid (water or other) Flow Parameters: Specified inlet velocities or mass flow rates Temperature Conditions: Defined inlet temperatures for both streams Boundary Specifications: Wall conditions, inlet/outlet parameters Results and Performance Analysis Thermal Performance Characteristics Temperature Distribution: Visualization of thermal gradients throughout the exchanger Heat Transfer Enhancement: Quantification of improvement over conventional design Nanofluid Effectiveness: Analysis of thermal conductivity enhancement contribution Fin Performance: Evaluation of extended surface contribution to overall heat transfer Flow Behavior and Hydraulic Performance Velocity Patterns: Analysis of flow development and path extension due to fins Pressure Distribution: Characterization of pressure drop across the exchanger Turbulence Effects: Examination of increased mixing due to helical geometry Secondary Flows: Identification of vortex structures enhancing heat transfer Comparative Performance Metrics Heat Transfer Coefficient: Enhancement relative to standard design Pressure Drop Penalty: Assessment of increased pumping power requirements Overall Efficiency: Balance between thermal improvement and hydraulic losses Design Optimization: Insights for fin spacing, height, and pitch optimization Engineering Implications Design Considerations: Guidance for optimal fin configuration with nanofluids Performance Predictions: Expected enhancement for various operating conditions Application Suitability: Identification of ideal implementation scenarios Economic Assessment: Balance between performance gains and manufacturing complexity This detailed CFD simulation provides valuable insights into the combined thermal enhancement potential of helical fins and nanofluids in shell and tube heat exchangers. The results demonstrate how strategic integration of multiple enhancement techniques can achieve superior thermal performance beyond what either approach could accomplish independently, offering promising directions for heat exchanger design optimization in various industrial applications requiring high thermal efficiency.
Episode 1 17m 11s -
Solar Heat Exchanger CFD Simulation: Radiation and Thermal Performance Analysis A comprehensive computational fluid dynamics investigation of a specialized solar heat exchanger design featuring an absorber plate, internal flow barriers, and dual-medium heat transfer. This simulation captures the complex interplay between solar radiation, conduction, and convection mechanisms to demonstrate the thermal performance characteristics of this renewable energy system. Solar Heat Exchanger Design and Operating Principles This simulation examines a specialized heat exchanger designed to capture and transfer solar thermal energy to a working fluid. The system incorporates an innovative dual-medium approach with an air gap and absorber plate to maximize solar energy capture and transfer to the water flow through strategic internal flow barriers. System Configuration Primary Components: Solar absorber plate exposed to radiation Air gap between front plate and absorber Water flow channel with internal flow barriers Strategic internal walls for flow path extension Heat Transfer Pathway: Solar radiation absorption at absorber plate Air gap heating through radiation and convection Conduction through absorber plate Convective transfer to water flow Geometric Specifications Flow Path Design: Extended water flow route via internal barriers Absorber Orientation: Positioned for maximum solar radiation capture Internal Barriers: Multiple rows of flow obstacles for extended fluid residence time Air Gap Configuration: Optimized spacing for thermal performance Computational Approach and Radiation Modeling Mesh Characteristics Grid Type: Unstructured mesh generated in ANSYS Meshing Cell Count: 304,200 elements Resolution Focus: Enhanced density near absorber plate and internal barriers Quality Parameters: Optimized for complex geometry with multiple domains Radiation Modeling Strategy Primary Model: Discrete Ordinates (DO) radiation model Model Capabilities: Handles scattering media Accounts for semi-transparent boundaries Manages specular surfaces Supports wavelength-dependent transmission Solar Loading: Solar Ray Tracing model implementation Solar Parameters: Direct solar radiation: 1150 W/m² Diffuse solar radiation: 80 W/m² Incidence angle: Perpendicular to absorber plane Operating Conditions Water Flow: 4 m/s inlet velocity at 30°C Outlet Condition: Atmospheric pressure Air Gap: Natural convection and radiation heat transfer Thermal Boundaries: Solar radiation on absorber surface Results and Performance Analysis Thermal Characteristics Temperature Distribution: Visualization of thermal gradients throughout the system Heat Transfer Pathways: Identification of primary energy transfer routes Absorber Performance: Temperature profile across the solar collector surface Water Temperature Gain: Progressive heating along the extended flow path Flow Behavior Velocity Patterns: Analysis of flow development around internal barriers Pressure Distribution: Characterization of pressure drop across the exchanger Recirculation Zones: Identification of potential thermal mixing regions Barrier Effectiveness: Assessment of flow path extension and residence time Radiation Effects Absorption Patterns: Distribution of captured solar energy across absorber Air Gap Thermal Gradient: Temperature stratification in the front air layer Direct vs. Diffuse Contribution: Relative impact of radiation components Thermal Losses: Evaluation of energy not transferred to working fluid Performance Metrics Overall Efficiency: Ratio of captured energy to incident solar radiation Temperature Rise: Quantification of water temperature increase Heat Transfer Rate: Total thermal energy transferred to water flow Pressure Drop: Hydraulic resistance through the extended flow path Engineering Insights Design Optimization: Guidance for barrier placement and configuration Performance Enhancement: Strategies for improving solar absorption and transfer Operational Parameters: Effects of flow rate on thermal efficiency System Scalability: Considerations for larger implementation This detailed CFD simulation provides valuable insights into the thermal-hydraulic behavior of this specialized solar heat exchanger design. The results demonstrate the effectiveness of combining strategic flow path extension with optimized solar absorption to achieve efficient thermal energy capture and transfer. The comprehensive radiation modeling approach ensures accurate representation of the complex heat transfer mechanisms involved in solar thermal systems, providing reliable guidance for design optimization and performance prediction in renewable energy applications.
Episode 2 17m 10s
-
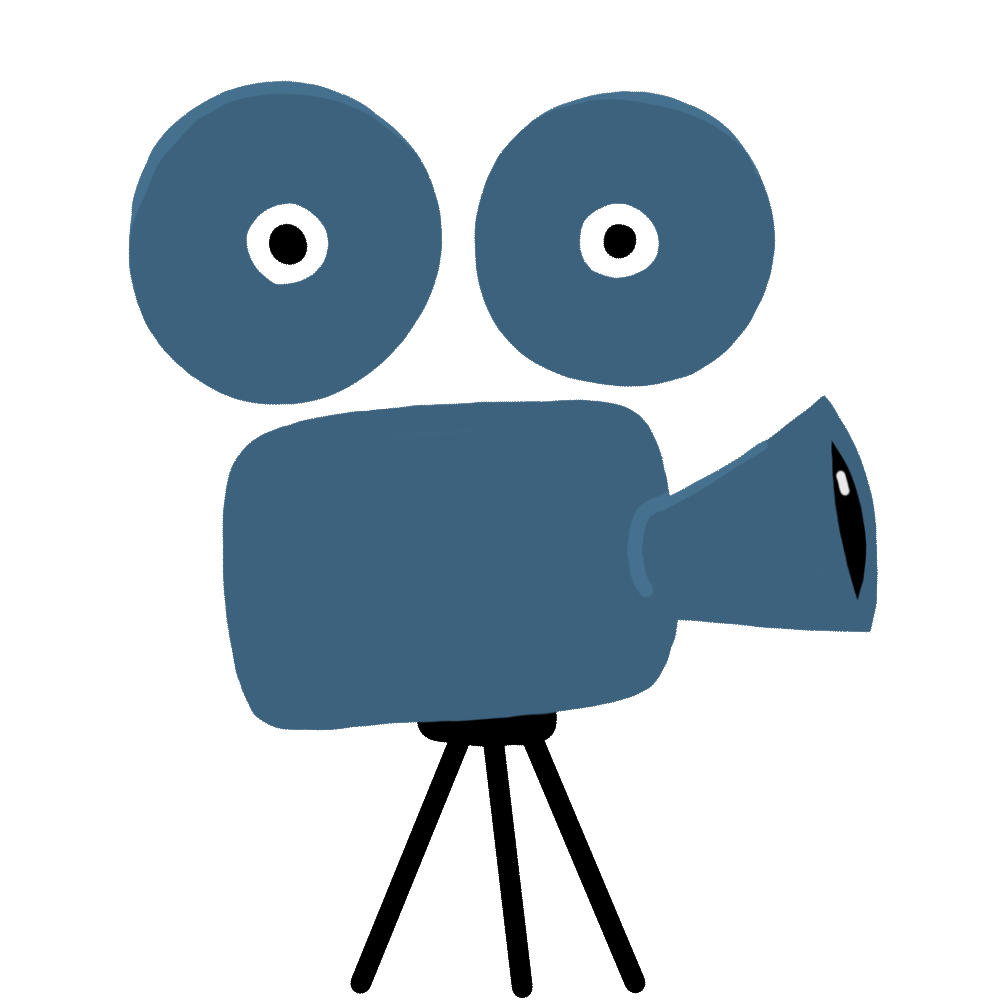
Course In Progress
Course still in development. Check back often for updates.
Master advanced thermal system analysis through 10 comprehensive ANSYS Fluent projects in this intermediate-level course. From conventional designs to cutting-edge configurations with phase change materials and nanofluids, you’ll develop the practical skills to simulate, analyze, and optimize various heat exchanger types for industrial applications.
Course Overview
This specialized training program bridges the gap between basic CFD knowledge and professional-level heat exchanger simulation capabilities. Through carefully structured projects, you’ll progressively build expertise in modeling complex thermal systems, implementing advanced physics models, and extracting meaningful performance data to drive design decisions.
What You’ll Learn
- Comprehensive modeling approaches for shell-and-tube, plate, and specialized heat exchanger geometries
- Advanced physics implementation including conjugate heat transfer, phase change phenomena, and nanofluid behavior
- Performance optimization techniques through parametric studies of baffle configurations, fin designs, and flow arrangements
- Multi-physics simulation methods for solar thermal applications and energy storage systems
- Practical workflow strategies that ensure efficient model setup, solution convergence, and results interpretation
Project Breakdown
Fundamental Configurations
- Triple Heat Exchanger Simulation: Model complex flow distribution and thermal interactions in multi-channel systems
- Plate Heat Exchanger Analysis: Capture chevron plate effects on heat transfer enhancement and pressure drop
- Shell and Tube Configurations: Evaluate baffle cut geometries and their impact on thermal-hydraulic performance
Advanced Materials and Physics
- Phase Change Material (PCM) Implementation: Simulate latent heat storage in finned tube and shell configurations
- Nanofluid Modeling Techniques: Configure mixture models for enhanced thermal conductivity in various heat exchanger designs
- Conjugate Heat Transfer Analysis: Master solid-fluid thermal interaction modeling for accurate temperature distributions
Specialized Applications
- Solar Heat Exchanger Simulation: Implement radiation models and temperature-dependent properties for renewable energy systems
- Helical Fin Optimization: Analyze geometric variations to maximize heat transfer while minimizing pressure penalties
- Alternative Solver Approaches: Compare ANSYS Fluent and CFX methodologies for plate heat exchanger applications
Learning Outcomes
By completing this course, you’ll develop the technical proficiency to:
- Configure appropriate physics models for complex heat transfer phenomena
- Create efficient computational meshes that capture critical flow and thermal features
- Extract and analyze performance metrics including effectiveness, pressure drop, and temperature distributions
- Identify optimization opportunities through parametric studies and design variations
- Apply industry best practices for heat exchanger simulation across multiple sectors
Who Should Enroll
This intermediate course is ideal for thermal engineers, HVAC specialists, process engineers, and CFD analysts seeking specialized expertise in heat exchanger simulation. Basic familiarity with ANSYS Workbench and fundamental fluid mechanics concepts is recommended.
Subscribe
Benefits of subscribing to the course
- Complete access to All chapters
- Special discount
- Free access to all new and updated content
- Cancel subscription anytime
* You will have access to the course only until your subscription ends; after that, your subscription will be automatically renewed unless you cancel it.
Congratulations
Congratulations! You have successfully subscribed to the course.
You can now start learning the course by clicking the button "Start Learning".
You can manage your subscription like canceling or upgrading the subscription, adding or changing the payment method, etc by clicking the button "Manage Subscriptions".
Add Payment Method
Please enter your payment method details.