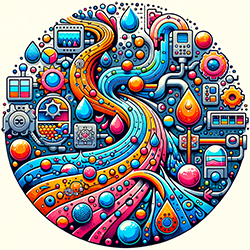
Multi-Phase Flow: ANSYS Fluent CFD Simulation Training Course
Workshop
Price:
$1,120.00
$149.00
Master multi-phase flow simulations with ANSYS Fluent in this comprehensive course. Learn VOF, Eulerian, Mixture, and Wet Steam models through practical examples. From microfluidics to industrial reactors, gain the skills to tackle complex multi-phase scenarios. Suitable for beginners and experienced CFD users alike. Enhance your expertise and unlock new possibilities in fluid dynamics modeling!
Wet Steam for Condensation inside a Steam Ejector CFD Simulation
Wet Steam for Condensation inside a Steam Ejector CFD Simulation Dive into the intricate world of steam dynamics with our comprehensive tutorial on simulating wet steam condensation inside a steam ejector using ANSYS Fluent. This episode, part of our “Multi-Phase: All Levels” course, offers an in-depth exploration of the Wet Steam multiphase model applied to a critical process in industrial fluid mechanics. Understanding Steam Ejectors and Wet Steam Dynamics Steam ejectors play a crucial role in various industrial applications, from vacuum creation to fluid mixing. This tutorial delves into the complexities of steam condensation within ejectors, providing insights into: The fundamental principles of ejector operation The physics of wet steam formation and condensation The importance of accurate modeling in ejector design and optimization Industrial Applications and Significance Discover how understanding wet steam dynamics in ejectors is crucial for: Enhancing vacuum system efficiency in process industries Optimizing steam-driven refrigeration cycles Improving performance in power generation systems Simulation Setup in ANSYS Fluent Follow our detailed guide to set up a robust simulation of wet steam condensation in an ejector: Geometry and Mesh Generation Learn how to: Design an accurate 2D ejector geometry using ANSYS Design Modeler Generate an appropriate structured mesh using ANSYS Meshing Optimize mesh quality for capturing complex flow phenomena Wet Steam Model Configuration Master the setup of the Wet Steam multiphase model to simulate the condensation process: Activating and configuring the non-equilibrium condensation model Setting up transport equations for liquid mass fraction and droplet concentration Implementing the density-based solver for compressible flow analysis Advanced Modeling Techniques Elevate your simulation skills with advanced techniques specific to wet steam and ejector flows: Nucleation and Droplet Growth Modeling Explore the implementation of: Classical non-isothermal nucleation theory Droplet growth and evaporation models Phase change dynamics in rapid steam expansion Compressible Flow and Shock Capturing Learn to accurately simulate: Supersonic flow regions in the ejector Shock formation and interaction with condensation Mixing of primary and secondary flows Result Analysis and Visualization Develop skills in interpreting and visualizing complex multiphase simulation results: Analyzing pressure, velocity, and temperature distributions Observing turbulent kinetic energy patterns Understanding liquid vapor mass production rates Applications in Industrial Process Optimization Understand the real-world impact of your simulations through: Case studies on ejector design optimization Examples of how simulation results inform efficiency improvements Discussions on scaling ejector performance for various industrial applications Future Directions and Research Opportunities Explore potential areas for further research and development: Investigating novel ejector geometries for enhanced performance Studying the effects of different operating conditions on condensation dynamics Developing predictive models for ejector efficiency and reliability By completing this comprehensive tutorial, you’ll gain the skills to simulate complex wet steam condensation processes in ejectors using ANSYS Fluent. Whether you’re a process engineer, CFD specialist, or a student in mechanical engineering, this knowledge will empower you to contribute to cutting-edge developments in steam-driven systems and industrial process optimization. Join us on this exciting journey into the world of advanced fluid dynamics and unlock new possibilities in enhancing ejector performance and efficiency across various industries!
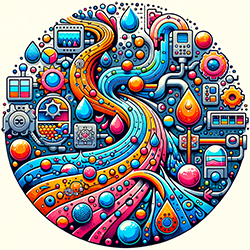
Multi-Phase Flow: ANSYS Fluent CFD Simulation Training Course
Workshop
Price:
$1,120.00
$149.00
Master multi-phase flow simulations with ANSYS Fluent in this comprehensive course. Learn VOF, Eulerian, Mixture, and Wet Steam models through practical examples. From microfluidics to industrial reactors, gain the skills to tackle complex multi-phase scenarios. Suitable for beginners and experienced CFD users alike. Enhance your expertise and unlock new possibilities in fluid dynamics modeling!
Wet Steam for Condensation inside a Steam Ejector CFD Simulation
Wet Steam for Condensation inside a Steam Ejector CFD Simulation Dive into the intricate world of steam dynamics with our comprehensive tutorial on simulating wet steam condensation inside a steam ejector using ANSYS Fluent. This episode, part of our “Multi-Phase: All Levels” course, offers an in-depth exploration of the Wet Steam multiphase model applied to a critical process in industrial fluid mechanics. Understanding Steam Ejectors and Wet Steam Dynamics Steam ejectors play a crucial role in various industrial applications, from vacuum creation to fluid mixing. This tutorial delves into the complexities of steam condensation within ejectors, providing insights into: The fundamental principles of ejector operation The physics of wet steam formation and condensation The importance of accurate modeling in ejector design and optimization Industrial Applications and Significance Discover how understanding wet steam dynamics in ejectors is crucial for: Enhancing vacuum system efficiency in process industries Optimizing steam-driven refrigeration cycles Improving performance in power generation systems Simulation Setup in ANSYS Fluent Follow our detailed guide to set up a robust simulation of wet steam condensation in an ejector: Geometry and Mesh Generation Learn how to: Design an accurate 2D ejector geometry using ANSYS Design Modeler Generate an appropriate structured mesh using ANSYS Meshing Optimize mesh quality for capturing complex flow phenomena Wet Steam Model Configuration Master the setup of the Wet Steam multiphase model to simulate the condensation process: Activating and configuring the non-equilibrium condensation model Setting up transport equations for liquid mass fraction and droplet concentration Implementing the density-based solver for compressible flow analysis Advanced Modeling Techniques Elevate your simulation skills with advanced techniques specific to wet steam and ejector flows: Nucleation and Droplet Growth Modeling Explore the implementation of: Classical non-isothermal nucleation theory Droplet growth and evaporation models Phase change dynamics in rapid steam expansion Compressible Flow and Shock Capturing Learn to accurately simulate: Supersonic flow regions in the ejector Shock formation and interaction with condensation Mixing of primary and secondary flows Result Analysis and Visualization Develop skills in interpreting and visualizing complex multiphase simulation results: Analyzing pressure, velocity, and temperature distributions Observing turbulent kinetic energy patterns Understanding liquid vapor mass production rates Applications in Industrial Process Optimization Understand the real-world impact of your simulations through: Case studies on ejector design optimization Examples of how simulation results inform efficiency improvements Discussions on scaling ejector performance for various industrial applications Future Directions and Research Opportunities Explore potential areas for further research and development: Investigating novel ejector geometries for enhanced performance Studying the effects of different operating conditions on condensation dynamics Developing predictive models for ejector efficiency and reliability By completing this comprehensive tutorial, you’ll gain the skills to simulate complex wet steam condensation processes in ejectors using ANSYS Fluent. Whether you’re a process engineer, CFD specialist, or a student in mechanical engineering, this knowledge will empower you to contribute to cutting-edge developments in steam-driven systems and industrial process optimization. Join us on this exciting journey into the world of advanced fluid dynamics and unlock new possibilities in enhancing ejector performance and efficiency across various industries!
-
Section 1
Multi-Phase Concept
-
Comprehensive Multiphase Flow Concepts in ANSYS Fluent Dive into the world of multiphase flow simulation with our in-depth tutorial on “Comprehensive Multiphase Flow Concepts in ANSYS Fluent.” This episode, the first in our “Multi-Phase: All Levels” course, provides a solid foundation for understanding and simulating complex multiphase phenomena using ANSYS Fluent. Understanding Multiphase Flows Multiphase flows are ubiquitous in nature and industry, involving the interaction of different phases such as gas, liquid, and solid. This tutorial begins with a comprehensive overview of multiphase flows, their classification, and various flow regimes. Classification and Flow Regimes Learn about the different types of multiphase flows, including: Gas-Solid interactions Gas-Liquid systems Liquid-Solid flows Explore various flow regimes such as bubbly, slug, churn, and annular flows, understanding their characteristics and significance in different applications. Multiphase Modeling Approaches Discover the two main approaches to modeling multiphase flows: Eulerian-Lagrangian Eulerian-Eulerian We’ll discuss the strengths and limitations of each approach, helping you choose the most appropriate method for your specific simulation needs. ANSYS Fluent Multiphase Models This tutorial provides an in-depth look at the primary multiphase models available in ANSYS Fluent: Volume of Fluid (VOF) Model Explore the applications and capabilities of the VOF model, ideal for simulating immiscible fluids with clearly defined interfaces. Eulerian Model Learn about the Eulerian model’s strengths in simulating dispersed phases within a continuous medium. Mixture Model Understand the applications of the Mixture model for simulating homogeneous multiphase flows. Choosing the Right Model One of the most crucial aspects of multiphase flow simulation is selecting the appropriate model. We’ll guide you through the decision-making process, considering factors such as: Specific application requirements Computational resources Desired level of detail We’ll also discuss the merits and limitations of each model, ensuring you can make informed choices for your simulations. Practical Applications and Industry Relevance Throughout the tutorial, we’ll highlight real-world applications of these multiphase flow concepts and models, demonstrating their relevance in industries such as: Chemical processing Oil and gas Power generation Environmental engineering By the end of this comprehensive tutorial, you’ll have a solid understanding of multiphase flow concepts and be well-prepared to tackle complex simulations using ANSYS Fluent. Whether you’re an engineer, researcher, or student, this episode provides essential knowledge for mastering multiphase flow simulations. Join us in this exciting journey into the world of multiphase flows and take your CFD skills to the next level!
Episode 1 12m 25s Free Episode
-
-
Section 2
VOF Model Concept
-
VOF Multiphase Model CFD Simulation Concepts in ANSYS Fluent Explore the powerful Volume of Fluid (VOF) multiphase model in this comprehensive tutorial, part of our “Multi-Phase: All Levels” course. This episode provides an in-depth introduction to VOF concepts and their implementation in ANSYS Fluent, equipping you with essential knowledge for advanced multiphase simulations. Understanding the VOF Model The VOF model is a robust tool for simulating immiscible fluids with clearly defined interfaces. We begin with a general introduction to the VOF multiphase model, its applications, and its applicability in various engineering scenarios. VOF Applications and Applicability Discover the wide range of applications where VOF excels, including: Free surface flows Bubble dynamics Liquid-liquid interfaces And more Learn to identify when VOF is the most suitable choice for your multiphase simulation needs. VOF Model Setup in ANSYS Fluent Dive into the practical aspects of setting up VOF simulations in ANSYS Fluent. We’ll guide you through: General Settings and Options Explore the VOF module window and understand the significance of each setting for your simulation. Implicit vs. Explicit Formulations Compare these two formulations, understanding their differences and when to use each for optimal results. Discretization Methods Learn about available discretization methods and how to choose between faster simulations or more accurate results based on your project requirements. Advanced VOF Concepts Take your VOF modeling skills to the next level with these advanced topics: Body Force Formulation Understand how body forces are handled in VOF simulations and their impact on results. Open Channel Boundary Conditions Explore open channel and open channel wave boundary conditions, crucial for many environmental and hydraulic engineering applications. Interface Modeling Techniques Delve into various interface modeling methods, including the Level Set method, to accurately capture fluid interfaces. Surface Tension and Mass Transfer Master the simulation of complex phenomena in VOF models: Surface Tension Modeling Compare Continuum Surface Force and Continuum Surface Stress approaches for modeling surface tension effects. Mass Transfer Mechanisms Learn to simulate evaporation and condensation processes, expanding the capabilities of your VOF simulations. Practical Implementation and Best Practices Throughout the tutorial, we’ll provide practical tips and best practices for implementing VOF models effectively. You’ll gain insights into: Choosing appropriate mesh resolutions Setting up initial conditions Selecting suitable time step sizes Interpreting and validating results By the end of this comprehensive tutorial, you’ll have a solid foundation in VOF multiphase modeling using ANSYS Fluent. Whether you’re simulating droplet formation, wave dynamics, or complex industrial processes, this knowledge will empower you to tackle challenging multiphase flow problems with confidence. Join us in this exciting exploration of VOF modeling and elevate your CFD simulation skills to new heights!
Episode 1 16m 53s Free Episode
-
-
Section 3
Microfluidic Droplet Generator (VOF)
-
VOF: Microfluidic Droplet Generator, ANSYS Fluent Tutorial Dive into the fascinating world of microfluidics with our comprehensive tutorial on simulating a microfluidic droplet generator using ANSYS Fluent. This episode, part of our “Multi-Phase: All Levels” course, offers an in-depth exploration of the Volume of Fluid (VOF) multiphase model applied to a cutting-edge biomedical engineering problem. Understanding Microfluidic Droplet Generators Microfluidic droplet generators play a crucial role in biomedical and bioengineering fields. These devices enable clinicians and scientists to analyze biological entities in vitro, providing valuable insights away from their natural habitat. Our tutorial delves into the intricacies of these devices and their simulation using advanced CFD techniques. Applications in Biomedical Research Discover how microfluidic droplet generators are used to: Separate and isolate biological entities Create controlled microenvironments for analysis Enable precise manipulation of microscale fluid dynamics Learn why accurate simulation of these devices is critical for advancing biomedical research and diagnostics. Simulation Setup in ANSYS Fluent Follow our step-by-step guide to set up a robust simulation of a microfluidic droplet generator: Geometry and Mesh Generation Learn how to: Design the device geometry using ANSYS Design Modeler Generate an appropriate unstructured mesh using ANSYS Meshing Optimize mesh quality for accurate results VOF Model Configuration Master the setup of the VOF multiphase model to simulate the interaction between water and oil phases (or their biological equivalents). We’ll cover: Enabling and configuring surface tension modeling Setting up wall adhesion for accurate droplet formation Utilizing the patching option to optimize computational efficiency Advanced Simulation Techniques Elevate your simulation skills with advanced techniques specific to microfluidic applications: Droplet Generation Control Explore how to manipulate droplet characteristics by adjusting: Inlet flow velocities for different phases Surface tension parameters Channel geometry and dimensions Result Analysis and Validation Learn to: Interpret simulation results effectively Validate your model against experimental data Optimize your simulation for improved accuracy and efficiency Practical Applications and Case Studies Understand the real-world impact of your simulations through: Case studies of biological entity separation Examples of how simulation results inform device design Discussions on scaling simulations for different biological applications Optimization and Parametric Studies Take your understanding further by learning how to: Conduct parametric studies to optimize device performance Investigate the effects of different fluids (e.g., PBS, blood) on droplet formation Explore the impact of channel geometry on droplet characteristics By the end of this comprehensive tutorial, you’ll have the skills to simulate complex microfluidic droplet generators using ANSYS Fluent. Whether you’re a biomedical researcher, a CFD specialist, or an engineering student, this knowledge will empower you to contribute to cutting-edge developments in microfluidics and bioengineering. Join us on this exciting journey into the microscale world of fluid dynamics and unlock new possibilities in biomedical research and device design!
Episode 1 35m 37s
-
-
Section 4
Sub-Oceanic Volcanic Activity (VOF)
-
VOF: Sub-Oceanic Volcanic Activity ANSYS Fluent Training Dive into the depths of oceanic phenomena with our cutting-edge tutorial on simulating sub-oceanic volcanic activity using ANSYS Fluent. This episode, part of our “Multi-Phase: All Levels” course, offers an immersive exploration of the Volume of Fluid (VOF) multiphase model applied to a complex and critical environmental scenario. Understanding Sub-Oceanic Volcanic Activity Sub-oceanic volcanic eruptions play a crucial role in shaping our planet’s oceans and climate. This tutorial delves into the intricacies of these powerful natural phenomena and their far-reaching impacts. Learn how accurate simulation of these events can: Enhance oceanographic research Improve ocean engineering practices Contribute to disaster prevention, particularly tsunami forecasting Advance meteorological and weather forecasting sciences Importance in Environmental Sciences Discover how modeling sub-oceanic volcanic activity provides invaluable data for: Understanding ocean dynamics under extreme conditions Predicting long-term climate patterns Assessing risks to coastal communities and marine ecosystems Simulation Setup in ANSYS Fluent Follow our comprehensive guide to set up a robust simulation of sub-oceanic volcanic activity: Geometry and Mesh Generation Learn the process of: Designing complex underwater topography using ANSYS Design Modeler Generating an appropriate unstructured mesh with ANSYS Meshing Optimizing mesh quality for accurate results in challenging multi-phase scenarios VOF Model Configuration Master the setup of the VOF multiphase model to simulate the interaction between water, lava, and vapor: Enabling and configuring the Open Channel Flow model Setting up the Open Channel Wave boundary submodel for realistic wave simulation Implementing the Fifth Order Stokes Wave Theory for accurate surface wave patterns Advanced Simulation Techniques Elevate your simulation skills with advanced techniques specific to volcanic and oceanic modeling: Mass Transfer Modeling Explore the implementation of evaporation and condensation mass transfer using the Lee model to accurately simulate: Vapor generation due to extreme temperatures during eruptions The impact of vapor on ocean hydrodynamics Wave-Eruption Interaction Analysis Learn to analyze and visualize: The disruption of wave patterns due to volcanic activity The hydrodynamic effects of vapor generation on ocean surface dynamics Result Interpretation and Validation Develop skills in: Interpreting complex multi-phase simulation results Validating your model against known oceanic and volcanic phenomena Optimizing your simulation for improved accuracy and computational efficiency Applications in Environmental Prediction and Protection Understand the real-world impact of your simulations through: Case studies on tsunami prediction and prevention Examples of how simulation results inform ocean engineering practices Discussions on the role of CFD in climate change research and mitigation strategies Future Directions and Research Opportunities Explore potential areas for further research and development: Coupling volcanic simulations with global climate models Investigating long-term effects of sub-oceanic volcanic activity on marine ecosystems Developing early warning systems based on simulation insights By completing this comprehensive tutorial, you’ll gain the skills to simulate complex sub-oceanic volcanic activities using ANSYS Fluent. Whether you’re an environmental scientist, oceanographer, CFD specialist, or engineering student, this knowledge will empower you to contribute to cutting-edge research in oceanography, climate science, and disaster prevention. Join us on this exciting journey into the depths of the ocean and unlock new possibilities in understanding and predicting our planet’s dynamic systems!
Episode 1 49m 41s
-
-
Section 5
Eulerian Model Concept
-
Eulerian Multiphase Model Concepts in ANSYS Fluent Dive into the powerful world of Eulerian multiphase modeling with this comprehensive tutorial, a key component of our “Multi-Phase: All Levels” course. This episode provides an in-depth exploration of Eulerian multiphase concepts and their implementation in ANSYS Fluent, equipping you with essential knowledge for advanced multiphase simulations. Understanding the Eulerian Model The Eulerian model is a versatile tool for simulating complex multiphase flows where phases are treated as interpenetrating continua. We begin with a general introduction to the Eulerian multiphase model, its applications, and its applicability in various engineering scenarios. Applications and Applicability Discover the wide range of applications where the Eulerian model excels, including: Bubble columns Fluidized beds Particle-laden flows And more Learn to identify when the Eulerian approach is the most suitable choice for your multiphase simulation needs. Advanced Eulerian Modeling Techniques Explore cutting-edge features and sub-models available in ANSYS Fluent for Eulerian simulations: Regime Transition Modeling Understand how to model transitions between different flow regimes using advanced sub-models: AIAD (Algebraic Interfacial Area Density) sub-model GENTOP (Generalized Two-Phase Flow) sub-model Boiling Models Delve into the intricacies of simulating boiling phenomena using the RPI (Rensselaer Polytechnic Institute) boiling model. Interfacial Dynamics and Forces Master the simulation of complex interfacial phenomena in Eulerian models: Interfacial Area Modeling Compare Interfacial Area Concentration and Algebraic Interfacial Area approaches for modeling interfacial dynamics. Applicable Forces Learn to incorporate various interphase forces crucial for accurate multiphase simulations: Drag force Lift force Wall lubrication force And other relevant forces Turbulence Modeling in Multiphase Flows Gain insights into modeling turbulence in complex multiphase systems: Turbulent Interaction Models Explore different approaches to turbulence modeling in multiphase flows: Mixture turbulence models Dispersed phase turbulence models Per-phase turbulence models Understand the pros and cons of each approach and learn when to apply them. Euler-Granular Model for Particle-Laden Flows Dive into the specialized Euler-Granular model for simulating flows with solid particles: Granular Temperature Concept Understand the concept of granular temperature and its role in modeling particle-particle interactions. Packed Bed Simulations Learn techniques for simulating packed bed reactors and other systems with high particle concentrations. Practical Implementation and Best Practices Throughout the tutorial, we’ll provide practical tips and best practices for implementing Eulerian models effectively. You’ll gain insights into: Choosing appropriate phase interaction models Setting up initial and boundary conditions Selecting suitable solution methods and convergence criteria Interpreting and validating results By the end of this comprehensive tutorial, you’ll have a solid foundation in Eulerian multiphase modeling using ANSYS Fluent. Whether you’re simulating complex reactor designs, multiphase flows in process equipment, or particle-laden environmental flows, this knowledge will empower you to tackle challenging multiphase flow problems with confidence. Join us in this exciting exploration of Eulerian modeling and elevate your CFD simulation skills to new heights!
Episode 1 30m 45s Free Episode
-
-
Section 6
Unconfined Pool Boiling (Eulerian)
-
Eulerian: Unconfined Pool Boiling ANSYS Fluent Tutorial Dive into the fascinating world of thermal-fluid dynamics with our comprehensive tutorial on simulating unconfined pool boiling using ANSYS Fluent. This episode, part of our “Multi-Phase: All Levels” course, offers an in-depth exploration of the Eulerian multiphase model applied to a critical heat transfer phenomenon. Understanding Pool Boiling Dynamics Pool boiling is a fundamental process in many industrial and engineering applications. This tutorial delves into the intricacies of saturated water pool boiling inside a cylindrical chamber, providing insights into: The definition and types of pool boiling (saturated vs. subcooled) Key concepts such as Onset of Nucleate Boiling (ONB), Departure from Nucleate Boiling (DNB), and Critical Heat Flux (CHF) The importance of pool boiling in academic research and industrial applications Industrial Relevance and Safety Implications Discover how understanding pool boiling is crucial for: Designing efficient heat exchange systems Preventing burnout in industrial equipment Enhancing safety in nuclear reactors and other high-heat applications Simulation Setup in ANSYS Fluent Follow our step-by-step guide to set up a robust simulation of unconfined pool boiling: Geometry and Mesh Generation Learn how to: Design the cylindrical chamber geometry using ANSYS Design Modeler Generate an appropriate structured mesh using ANSYS Meshing Optimize mesh quality for accurate results in complex multiphase scenarios Eulerian Model Configuration Master the setup of the Eulerian multiphase model to simulate the interaction between liquid water and vapor: Enabling and configuring the RPI (Rensselaer Polytechnic Institute) boiling sub-model Setting up various interphase forces including drag, lift, and wall lubrication Implementing wall adhesion for realistic bubble detachment modeling Advanced Boiling Simulation Techniques Elevate your simulation skills with advanced techniques specific to pool boiling: Mass Transfer and Energy Modeling Explore the implementation of: Boiling mass transfer mechanisms Energy equation for temperature distribution calculation Realizable k-epsilon model for turbulence modeling Bubble Dynamics Modeling Learn to accurately simulate: Bubble departure diameter and frequency Nucleation site density Area influence coefficient Quenching model correction using bubble waiting time coefficient Result Analysis and Visualization Develop skills in interpreting and visualizing complex multiphase simulation results: Analyzing vapor volume fraction contours Observing bubble shape changes and mass exchange (condensation) during ascent Understanding the convective motion induced by boiling Applications in Thermal Management and Safety Understand the real-world impact of your simulations through: Case studies on heat exchanger design optimization Examples of how simulation results inform safety protocols in high-heat industries Discussions on the role of CFD in predicting and preventing burnout conditions Future Directions and Research Opportunities Explore potential areas for further research and development: Investigating subcooled boiling scenarios Studying the effects of surface characteristics on boiling performance Developing predictive models for Critical Heat Flux in various geometries By completing this comprehensive tutorial, you’ll gain the skills to simulate complex pool boiling phenomena using ANSYS Fluent. Whether you’re a thermal engineer, CFD specialist, or a student in heat transfer sciences, this knowledge will empower you to contribute to cutting-edge developments in thermal management and safety engineering. Join us on this exciting journey into the world of multiphase heat transfer and unlock new possibilities in understanding and optimizing boiling processes!
Episode 1 1h 12m 9s
-
-
Section 7
Fluidized Bed Bio-Reactor (Eulerian)
-
Eulerian: Fluidized Bed Bio-Reactor ANSYS Fluent Training Dive into the cutting-edge world of biochemical engineering with our comprehensive tutorial on simulating a fluidized bed bio-reactor using ANSYS Fluent. This episode, part of our “Multi-Phase: All Levels” course, offers an in-depth exploration of the Eulerian multiphase model applied to a critical industrial process. Understanding Fluidized Bed Bio-Reactors Fluidized bed bio-reactors (FBRs) are versatile devices crucial in various industries, from biomedical to food processing. This tutorial delves into the intricacies of FBRs, providing insights into: The principle of fluidization and its advantages Applications of FBRs in industrial processes Key components and dynamics of fluidized bed systems Industrial Applications and Advantages Discover how FBRs are revolutionizing various sectors: Enhancing efficiency in biomedical research Improving food processing techniques Advancing chemical and pharmaceutical manufacturing Simulation Setup in ANSYS Fluent Follow our step-by-step guide to set up a robust simulation of a fluidized bed bio-reactor: Geometry and Mesh Generation Learn how to: Design the bio-reactor geometry using ANSYS Design Modeler Generate an appropriate structured mesh using ANSYS Meshing Optimize mesh quality for accurate results in complex multiphase scenarios Eulerian Model Configuration Master the setup of the Eulerian multiphase model to simulate the interaction between air and silicon particles: Activating and configuring the Granular sub-model Setting up phase property models for granular temperature calculation Implementing drag and virtual mass forces between phase pairs Advanced Modeling Techniques Elevate your simulation skills with advanced techniques specific to fluidized bed reactors: Heat Transfer and Energy Modeling Explore the implementation of: Ranz-Marshall model for air-particle heat transfer Energy equation for temperature distribution calculation Standard k-epsilon model for turbulence modeling Particle Dynamics and Interactions Learn to accurately simulate: Particle-particle interactions with restitution coefficients Gravity effects on particle motion Transient behavior of the fluidized bed Result Analysis and Visualization Develop skills in interpreting and visualizing complex multiphase simulation results: Analyzing particle distribution and motion patterns Observing temperature changes within the reactor Understanding the impact of fluidization on reaction kinetics Applications in Bioengineering and Process Optimization Understand the real-world impact of your simulations through: Case studies on bio-reactor design optimization Examples of how simulation results inform process efficiency improvements Discussions on scaling up FBRs for industrial applications Future Directions and Research Opportunities Explore potential areas for further research and development: Investigating the effects of different particle types and sizes Studying the impact of reactor geometry on fluidization efficiency Developing predictive models for bio-reaction rates in FBRs By completing this comprehensive tutorial, you’ll gain the skills to simulate complex fluidized bed bio-reactors using ANSYS Fluent. Whether you’re a bioprocess engineer, CFD specialist, or a student in chemical engineering, this knowledge will empower you to contribute to cutting-edge developments in bioengineering and process optimization. Join us on this exciting journey into the world of fluidized bed technology and unlock new possibilities in enhancing biochemical processes and reactor designs!
Episode 1 48m 27s
-
-
Section 8
Carbonate Cake Filtration (Eulerian)
-
Eulerian: Carbonate Cake Filtration ANSYS Fluent Tutorial Dive into the intricate world of industrial filtration processes with our comprehensive tutorial on simulating carbonate cake filtration using ANSYS Fluent. This episode, part of our “Multi-Phase: All Levels” course, offers an in-depth exploration of the Eulerian multiphase model applied to a critical separation process. Understanding Carbonate Cake Filtration Filtration is a fundamental process in many industries, crucial for separating solids from liquids. This tutorial delves into the complexities of carbonate cake filtration, providing insights into: The principles of physical separation in filtration processes Formation and impact of filter cakes Challenges in maintaining filter efficiency Industrial Applications and Importance Discover how carbonate cake filtration is essential in various sectors: Water treatment and purification Chemical processing industries Environmental remediation efforts Simulation Setup in ANSYS Fluent Follow our detailed guide to set up a robust simulation of carbonate cake filtration: Geometry and Mesh Generation Learn how to: Design the filtration unit geometry using ANSYS Design Modeler Generate an appropriate structured mesh using ANSYS Meshing Optimize mesh quality for accurate results in complex multiphase scenarios Eulerian Model Configuration Master the setup of the Eulerian multiphase model to simulate the interaction between water, carbonate particles, and the carbon filter: Activating and configuring the Granular and Packed Bed sub-models Setting up phase property models for granular temperature calculation Implementing drag, lift, and virtual mass forces between phase pairs Advanced Modeling Techniques Elevate your simulation skills with advanced techniques specific to filtration processes: Heat Transfer and Energy Modeling Explore the implementation of: Ranz-Marshall model for water-filter heat transfer Energy equation for temperature distribution calculation Standard k-epsilon model for turbulence modeling Particle Dynamics and Cake Formation Learn to accurately simulate: Particle-particle and particle-filter interactions Cake layer formation and growth over time Impact of cake formation on filtration efficiency Result Analysis and Visualization Develop skills in interpreting and visualizing complex multiphase simulation results: Analyzing carbonate concentration changes across the filter Observing temperature profiles in the feed water Understanding the dynamics of cake layer formation Applications in Process Optimization Understand the real-world impact of your simulations through: Case studies on filtration unit design optimization Examples of how simulation results inform process efficiency improvements Discussions on scaling up filtration processes for industrial applications Future Directions and Research Opportunities Explore potential areas for further research and development: Investigating the effects of different filter materials and structures Studying the impact of particle size distribution on cake formation Developing predictive models for filter lifespan and maintenance schedules By completing this comprehensive tutorial, you’ll gain the skills to simulate complex carbonate cake filtration processes using ANSYS Fluent. Whether you’re a process engineer, CFD specialist, or a student in chemical engineering, this knowledge will empower you to contribute to cutting-edge developments in separation technologies and process optimization. Join us on this exciting journey into the world of advanced filtration technology and unlock new possibilities in enhancing industrial separation processes and filter designs!
Episode 1 1h 2m 20s
-
-
Section 9
Mixture and Wet Steam Models Concept
-
Mixture and Wet Steam Multiphase Models Concepts in ANSYS Fluent Unlock the power of advanced multiphase modeling with our comprehensive tutorial on Mixture and Wet Steam Multiphase Models in ANSYS Fluent. This episode, part of our “Multi-Phase: All Levels” course, provides an in-depth exploration of these crucial models, equipping you with the knowledge to conduct more accurate and efficient CFD simulations. Understanding Mixture and Wet Steam Models Begin your journey with a thorough introduction to the Mixture and Wet Steam Multiphase models. We’ll explore their fundamental principles, applications, and unique features that make them indispensable tools in the CFD toolkit. Overview of Simulation Techniques Discover the range of simulation techniques and sub-models available in ANSYS Fluent for both Mixture and Wet Steam models. This knowledge will empower you to choose the most appropriate approach for your specific simulation needs. Deep Dive into the Mixture Model The Mixture model is a simplified multiphase model that can handle a wide range of multiphase flows. We’ll explore its intricacies in detail: Governing Equations and Assumptions Understand the mathematical foundation of the Mixture model, including its governing equations and the assumptions that underpin its effectiveness. Applications and Limitations Learn about the diverse applications of the Mixture model, from in-homogeneous to homogeneous flows. We’ll also discuss its limitations to help you make informed decisions about when to use this model. Advanced Concepts: Drift and Slip Velocities Delve into the concepts of drift and slip velocities, crucial for accurately modeling relative motion between phases in the Mixture model. Cavitation Modeling Explore how the Mixture model can be extended to simulate cavitation phenomena, a critical aspect in many engineering applications. Exploring the Wet Steam Model The Wet Steam model is specialized for simulating two-phase flows involving water and steam. We’ll cover its unique features and applications: Model Assumptions and Restrictions Understand the specific assumptions and restrictions of the Wet Steam model to ensure its appropriate application in your simulations. Steam Ejector Applications Learn how to apply the Wet Steam model to simulate steam ejectors, a common application in various industries. Practical Implementation and Best Practices Throughout the tutorial, we’ll provide valuable insights on: Selecting the appropriate model for your specific multiphase flow problem Setting up simulations correctly in ANSYS Fluent Interpreting results and ensuring simulation accuracy Troubleshooting common issues in Mixture and Wet Steam model simulations Comparative Analysis We’ll conclude with a comparative analysis of the Mixture and Wet Steam models, highlighting their strengths, weaknesses, and ideal use cases. This comparison will help you make informed decisions when choosing between these models for your CFD projects. By the end of this comprehensive tutorial, you’ll have a solid understanding of both the Mixture and Wet Steam Multiphase Models in ANSYS Fluent. Whether you’re simulating complex industrial processes, designing new equipment, or conducting academic research, this knowledge will elevate your CFD simulation capabilities to new heights. Join us on this exciting journey into advanced multiphase modeling and transform your approach to CFD simulations!
Episode 1 8m 57s Free Episode
-
-
Section 10
Boat Propeller Cavitation (Mixture)
-
Boat Propeller Cavitation CFD Simulation
Mixture: Boat Propeller Cavitation CFD Simulation Tutorial Dive into the fascinating world of marine engineering with our comprehensive tutorial on simulating boat propeller cavitation using ANSYS Fluent. This episode, part of our “Multi-Phase: All Levels” course, offers an in-depth exploration of the Mixture multiphase model applied to a critical phenomenon in propeller design and performance. Understanding Propeller Cavitation Cavitation is a complex phenomenon that significantly impacts the performance and longevity of boat propellers. This tutorial delves into the intricacies of cavitation, providing insights into: The physics behind cavitation formation Impact of cavitation on propeller efficiency and wear Challenges in propeller design to mitigate cavitation effects Engineering Implications and Importance Discover how understanding and controlling cavitation is crucial for: Optimizing propeller performance and efficiency Reducing wear and extending propeller lifespan Minimizing noise and vibration in marine vessels Simulation Setup in ANSYS Fluent Follow our detailed guide to set up a robust simulation of propeller cavitation: Geometry and Mesh Generation Learn how to: Design complex propeller geometry using ANSYS Design Modeler Generate an appropriate unstructured mesh using ANSYS Meshing Optimize mesh quality for accurate results in rotating fluid domains Mixture Model Configuration Master the setup of the Mixture multiphase model to simulate the interaction between water and vapor: Activating and configuring the Schnerr-Sauer cavitation model Setting appropriate vaporization pressure limits Implementing mesh motion for propeller rotation Advanced Modeling Techniques Elevate your simulation skills with advanced techniques specific to propeller cavitation: Turbulence Modeling and Transient Analysis Explore the implementation of: SST k-omega model for accurate external flow simulation Transient analysis for capturing time-dependent cavitation dynamics Mesh motion techniques for realistic propeller rotation Cavitation Dynamics and Bubble Formation Learn to accurately simulate: Pressure distribution around propeller blades Cavitation inception and growth Super cavitation phenomena at high rotational speeds Result Analysis and Visualization Develop skills in interpreting and visualizing complex multiphase simulation results: Analyzing vapor volume fraction on propeller surfaces Observing pressure distributions leading to cavitation Understanding the impact of rotational speed on cavitation extent Applications in Marine Engineering and Design Understand the real-world impact of your simulations through: Case studies on propeller design optimization Examples of how simulation results inform cavitation mitigation strategies Discussions on balancing performance and cavitation reduction in propeller design Future Directions and Research Opportunities Explore potential areas for further research and development: Investigating novel blade geometries for cavitation reduction Studying the effects of different materials on cavitation resistance Developing predictive models for propeller lifespan under cavitation conditions By completing this comprehensive tutorial, you’ll gain the skills to simulate complex propeller cavitation using ANSYS Fluent. Whether you’re a marine engineer, CFD specialist, or a student in naval architecture, this knowledge will empower you to contribute to cutting-edge developments in propeller design and marine propulsion systems. Join us on this exciting journey into the world of advanced marine engineering and unlock new possibilities in enhancing propeller performance and longevity!
Episode 1 Coming Soon
-
-
Section 11
Steam Ejector Condensation (Wet Steam)
-
Wet Steam for Condensation inside a Steam Ejector CFD Simulation Dive into the intricate world of steam dynamics with our comprehensive tutorial on simulating wet steam condensation inside a steam ejector using ANSYS Fluent. This episode, part of our “Multi-Phase: All Levels” course, offers an in-depth exploration of the Wet Steam multiphase model applied to a critical process in industrial fluid mechanics. Understanding Steam Ejectors and Wet Steam Dynamics Steam ejectors play a crucial role in various industrial applications, from vacuum creation to fluid mixing. This tutorial delves into the complexities of steam condensation within ejectors, providing insights into: The fundamental principles of ejector operation The physics of wet steam formation and condensation The importance of accurate modeling in ejector design and optimization Industrial Applications and Significance Discover how understanding wet steam dynamics in ejectors is crucial for: Enhancing vacuum system efficiency in process industries Optimizing steam-driven refrigeration cycles Improving performance in power generation systems Simulation Setup in ANSYS Fluent Follow our detailed guide to set up a robust simulation of wet steam condensation in an ejector: Geometry and Mesh Generation Learn how to: Design an accurate 2D ejector geometry using ANSYS Design Modeler Generate an appropriate structured mesh using ANSYS Meshing Optimize mesh quality for capturing complex flow phenomena Wet Steam Model Configuration Master the setup of the Wet Steam multiphase model to simulate the condensation process: Activating and configuring the non-equilibrium condensation model Setting up transport equations for liquid mass fraction and droplet concentration Implementing the density-based solver for compressible flow analysis Advanced Modeling Techniques Elevate your simulation skills with advanced techniques specific to wet steam and ejector flows: Nucleation and Droplet Growth Modeling Explore the implementation of: Classical non-isothermal nucleation theory Droplet growth and evaporation models Phase change dynamics in rapid steam expansion Compressible Flow and Shock Capturing Learn to accurately simulate: Supersonic flow regions in the ejector Shock formation and interaction with condensation Mixing of primary and secondary flows Result Analysis and Visualization Develop skills in interpreting and visualizing complex multiphase simulation results: Analyzing pressure, velocity, and temperature distributions Observing turbulent kinetic energy patterns Understanding liquid vapor mass production rates Applications in Industrial Process Optimization Understand the real-world impact of your simulations through: Case studies on ejector design optimization Examples of how simulation results inform efficiency improvements Discussions on scaling ejector performance for various industrial applications Future Directions and Research Opportunities Explore potential areas for further research and development: Investigating novel ejector geometries for enhanced performance Studying the effects of different operating conditions on condensation dynamics Developing predictive models for ejector efficiency and reliability By completing this comprehensive tutorial, you’ll gain the skills to simulate complex wet steam condensation processes in ejectors using ANSYS Fluent. Whether you’re a process engineer, CFD specialist, or a student in mechanical engineering, this knowledge will empower you to contribute to cutting-edge developments in steam-driven systems and industrial process optimization. Join us on this exciting journey into the world of advanced fluid dynamics and unlock new possibilities in enhancing ejector performance and efficiency across various industries!
Episode 1 40m
-
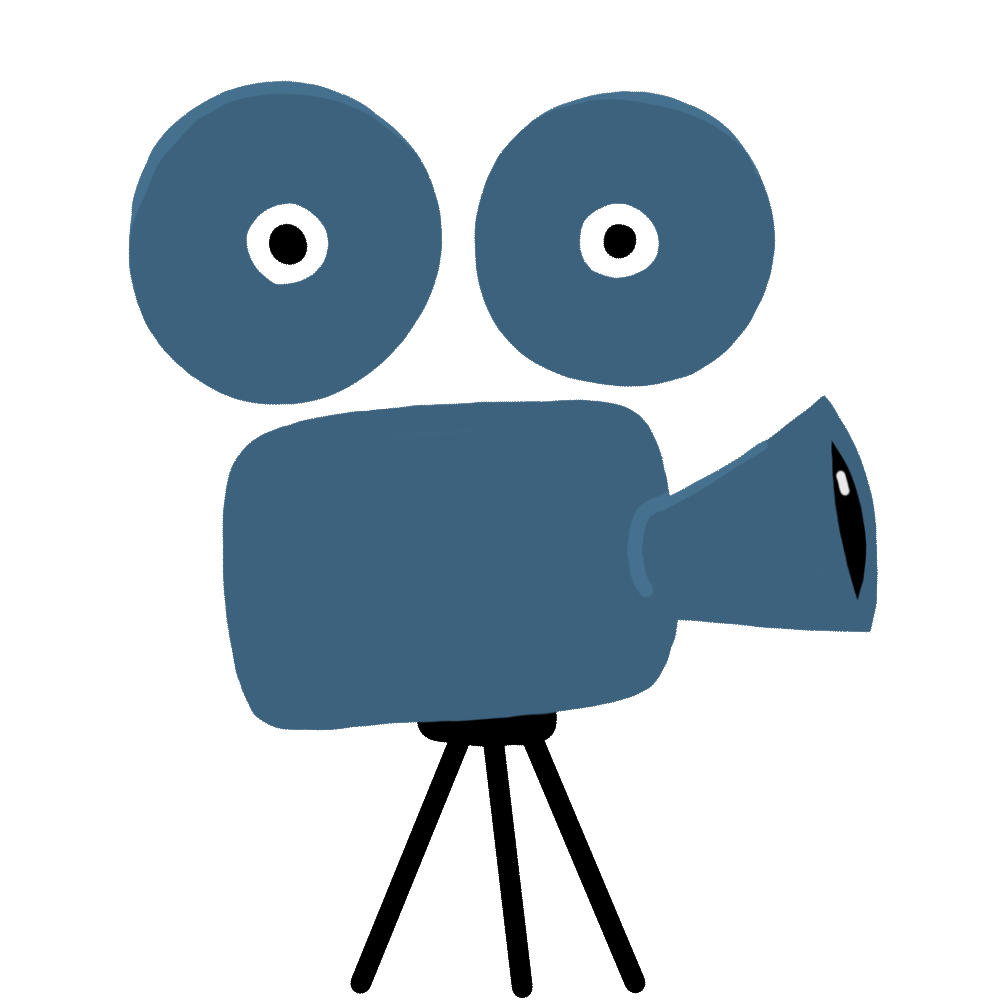
Course In Progress
Course still in development. Check back often for updates.
Introduction to Multiphase Flows and Their Applications
Welcome to the first chapter of our comprehensive “Multi-Phase: All Levels” course. In this foundational episode, we delve into the fascinating world of multiphase flows, providing you with a solid understanding of their fundamental concepts and diverse applications in real-world scenarios.
Understanding Multiphase Flows
Multiphase flows involve the simultaneous presence of two or more phases - liquid, gas, and solid - within a single system. These complex flow phenomena are ubiquitous in nature and industry, making their accurate modeling crucial for various engineering applications.
Classification and Flow Regimes
We’ll explore the different classifications of multiphase flows and the various flow regimes they can exhibit. Understanding these classifications is essential for selecting the appropriate modeling approach for your specific application.
Modeling Approaches: Eulerian-Lagrangian vs. Eulerian-Eulerian
Learn the differences between Eulerian-Lagrangian and Eulerian-Eulerian approaches, and when to apply each in your simulations. This knowledge will help you make informed decisions when tackling complex multiphase flow problems.
Introduction to Multiphase Models in ANSYS Fluent
ANSYS Fluent offers a range of powerful models for simulating multiphase flows. We’ll provide an overview of the following key models:
- Volume of Fluid (VOF) Model
- Eulerian Model
- Mixture Model
- Wet Steam Model
For each model, we’ll discuss its principles, applications, and strengths, giving you a comprehensive understanding of when and how to use them effectively.
Choosing the Right Model
We’ll guide you through the decision-making process for selecting the most appropriate model for your specific multiphase flow problem. This crucial skill will help you optimize your simulation strategy and achieve accurate results.
Real-World Applications
To reinforce your understanding, we’ll present various real-life and industrial examples of multiphase flows. These practical illustrations will demonstrate the importance of multiphase flow modeling in fields such as:
- Chemical processing
- Oil and gas industry
- Power generation
- Environmental engineering
- Biomedical applications
By the end of this introductory chapter, you’ll have a solid foundation in multiphase flow concepts and be well-prepared to dive into the specific modeling techniques covered in subsequent chapters. Whether you’re a beginner or an experienced CFD user, this episode will equip you with the knowledge to tackle complex multiphase flow simulations with confidence.
Buy Course
Benefits of buying the whole course
- Complete access to chapters Without Price
- Special discount
- Unlimited access to course content
- Free access to all new and updated content
- Access to course forever without any additional payment
* You can select chapters seperately, but you won't benefit from the list above.
* The items that do not have a price cannot be bought separately and are only available when you buy the whole course.
Congratulations
Congratulations! Your purchase was successful.
You can now start learning the course by clicking the button "Start Learning".
Add Payment Method
Please enter your payment method details.