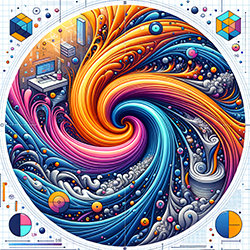
Multi-Phase Flow, Beginner: CFD Simulation Training Course
Course Price: $1.00 / Month
Dive into the world of multiphase flow simulation with this comprehensive ANSYS Fluent course designed for beginners. Master the fundamentals of Volume of Fluid (VOF), Eulerian, and Mixture models through hands-on tutorials covering a diverse range of applications. From shower drains to fuel injectors, learn to simulate complex multiphase phenomena using industry-standard CFD tools. This subscription-based course offers a structured approach to building your multiphase modeling skills, equipping you with practical knowledge for real-world engineering challenges.
Fuel Injector Three-Phase Flow CFD Simulation
Mastering Fuel Injection Dynamics: Three-Phase Flow CFD Simulation Using Mixture Multiphase Model Welcome to the “Fuel Injector Three-Phase Flow CFD Simulation” episode of our “MULTI-PHASE Flow: BEGINNER” course. This comprehensive module introduces you to the intricate world of fuel injection systems, a critical component in automotive and aerospace engineering. Learn how to leverage the Mixture multiphase model in ANSYS Fluent to simulate and analyze complex three-phase flows in fuel injectors, providing essential skills for engineers in automotive, aerospace, and combustion engineering sectors. Understanding the Mixture Multiphase Model in Fuel Injection Systems Before diving into the simulation specifics, let’s explore the fundamental concepts of the Mixture approach in the context of fuel injector flow dynamics. Principles of Mixture Modeling for Liquid-Gas-Vapor Interactions Discover how the Mixture model accurately represents phase interactions, slip velocities, and mass transfer between liquid fuel, air, and fuel vapor phases in high-pressure injection systems. Applications of Three-Phase Flow Simulations in Engine Technology Learn about the diverse applications of Mixture multiphase modeling in fuel injection systems, from automotive engines to aerospace propulsion systems. Exploring the Pre-configured Fuel Injector Geometry This section focuses on familiarizing yourself with the simulation environment: Anatomy of a Fuel Injector Model Gain insights into the key features of the pre-configured geometry representing a real-world fuel injector system, including internal passages and nozzle design. Mesh Characteristics for Accurate Phase Interaction Capture Understand the crucial aspects of the mesh that enable precise simulation of fluid behavior and phase coupling within the complex injector geometry. Implementing Boundary Conditions for Realistic Fuel Injection Scenarios Master the art of defining realistic conditions for your three-phase fuel injector simulation: Setting Up Fuel Inlet and Air Intake Parameters Learn to configure appropriate flow rates, pressures, and phase fractions for fuel inlet and air intake, mimicking real-world injection processes. Defining Nozzle Outlet and Ambient Conditions Explore techniques for accurately representing nozzle exit conditions and implementing appropriate ambient parameters for spray formation. Fine-tuning Mixture Model Parameters for Precise Phase Coupling Dive deep into the critical settings that ensure accurate capture of liquid-gas-vapor interactions and momentum transfer in high-pressure flows: Selecting Optimal Slip Velocity and Mass Transfer Models Understand how to choose and configure the right models for accurate representation of phase interactions and fuel vaporization in injection systems. Implementing Turbulence and Cavitation Effects Learn to incorporate crucial physical phenomena such as turbulence modulation and cavitation inception that govern multiphase behavior in fuel injectors. Analyzing Flow Patterns and Spray Characteristics Develop skills to interpret the complex behavior of three-phase flows within the fuel injector system: Visualizing Phase Distribution and Velocity Profiles Master techniques for creating and interpreting contours and vector plots that reveal the spatial distribution and movement of liquid fuel, air, and fuel vapor through the injector and nozzle. Quantifying Spray Penetration and Droplet Formation Learn methods to assess and analyze key parameters such as spray cone angle, droplet size distribution, and vapor phase concentration in the near-nozzle region. Investigating Effects of Operating Conditions on Injector Performance Explore how various factors impact the behavior of fuel sprays in injection systems: Impact of Injection Pressure on Spray Atomization Discover how changes in fuel injection pressure affect the fluid dynamics and spray characteristics crucial for efficient combustion. Influence of Nozzle Geometry on Flow Patterns Learn to use CFD results to evaluate how different nozzle designs affect the overall spray formation and fuel distribution patterns. Interpreting Steady-State Simulation Results for Comprehensive Performance Analysis Develop expertise in extracting meaningful insights from your equilibrium simulations: Analyzing Fuel-Air Mixing and Vapor Distribution Master techniques for processing and interpreting CFD data to assess the effectiveness of fuel atomization and vapor formation for various engine operating conditions. Identifying Optimization Opportunities for Injector Design Learn to pinpoint crucial areas in the simulation that reveal potential improvements in injector geometry for enhanced performance and efficiency. Practical Applications and Industry Relevance Connect simulation insights to real-world engineering challenges: Optimizing Fuel Injection Systems for Improved Engine Efficiency Explore how CFD simulations can inform the design and improvement of fuel injectors for better fuel economy and reduced emissions in automotive and aerospace applications. Enhancing Combustion Stability through Precise Fuel Delivery Understand how the principles learned in this module can contribute to the development of more stable and efficient combustion processes in various engine types. Why This Module is Essential for Beginner Multiphase Flow Engineers This beginner-level module offers a practical introduction to advanced CFD techniques in fuel injector system simulation. By completing this simulation, you’ll gain valuable insights into: Fundamental principles of the Mixture approach and its application in modeling complex three-phase flows in high-pressure fuel injection systems Essential CFD techniques for simulating liquid-gas-vapor interactions, phase coupling, and momentum transfer in automotive and aerospace applications Practical applications of Mixture CFD analysis in engine technology, combustion engineering, and propulsion system design By the end of this episode, you’ll have developed crucial skills in: Setting up and running three-phase fuel injector simulations using the Mixture multiphase model in ANSYS Fluent Interpreting steady-state simulation results to assess flow patterns, phase distributions, and spray formation characteristics Applying CFD insights to enhance understanding and design in applications involving multiphase flows in fuel injection systems This knowledge forms a solid foundation for engineers and researchers looking to specialize in engine technology and multiphase flow analysis, providing a springboard for advanced studies in fluid dynamics, combustion processes, and innovative fuel injection technologies. Join us on this exciting journey into the world of fuel injector three-phase flow CFD simulation, and take your first steps towards becoming an expert in multiphase dynamics modeling for critical automotive and aerospace applications!
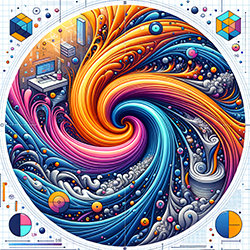
Multi-Phase Flow, Beginner: CFD Simulation Training Course
Course Price: $1.00 / Month
Dive into the world of multiphase flow simulation with this comprehensive ANSYS Fluent course designed for beginners. Master the fundamentals of Volume of Fluid (VOF), Eulerian, and Mixture models through hands-on tutorials covering a diverse range of applications. From shower drains to fuel injectors, learn to simulate complex multiphase phenomena using industry-standard CFD tools. This subscription-based course offers a structured approach to building your multiphase modeling skills, equipping you with practical knowledge for real-world engineering challenges.
Fuel Injector Three-Phase Flow CFD Simulation
Mastering Fuel Injection Dynamics: Three-Phase Flow CFD Simulation Using Mixture Multiphase Model Welcome to the “Fuel Injector Three-Phase Flow CFD Simulation” episode of our “MULTI-PHASE Flow: BEGINNER” course. This comprehensive module introduces you to the intricate world of fuel injection systems, a critical component in automotive and aerospace engineering. Learn how to leverage the Mixture multiphase model in ANSYS Fluent to simulate and analyze complex three-phase flows in fuel injectors, providing essential skills for engineers in automotive, aerospace, and combustion engineering sectors. Understanding the Mixture Multiphase Model in Fuel Injection Systems Before diving into the simulation specifics, let’s explore the fundamental concepts of the Mixture approach in the context of fuel injector flow dynamics. Principles of Mixture Modeling for Liquid-Gas-Vapor Interactions Discover how the Mixture model accurately represents phase interactions, slip velocities, and mass transfer between liquid fuel, air, and fuel vapor phases in high-pressure injection systems. Applications of Three-Phase Flow Simulations in Engine Technology Learn about the diverse applications of Mixture multiphase modeling in fuel injection systems, from automotive engines to aerospace propulsion systems. Exploring the Pre-configured Fuel Injector Geometry This section focuses on familiarizing yourself with the simulation environment: Anatomy of a Fuel Injector Model Gain insights into the key features of the pre-configured geometry representing a real-world fuel injector system, including internal passages and nozzle design. Mesh Characteristics for Accurate Phase Interaction Capture Understand the crucial aspects of the mesh that enable precise simulation of fluid behavior and phase coupling within the complex injector geometry. Implementing Boundary Conditions for Realistic Fuel Injection Scenarios Master the art of defining realistic conditions for your three-phase fuel injector simulation: Setting Up Fuel Inlet and Air Intake Parameters Learn to configure appropriate flow rates, pressures, and phase fractions for fuel inlet and air intake, mimicking real-world injection processes. Defining Nozzle Outlet and Ambient Conditions Explore techniques for accurately representing nozzle exit conditions and implementing appropriate ambient parameters for spray formation. Fine-tuning Mixture Model Parameters for Precise Phase Coupling Dive deep into the critical settings that ensure accurate capture of liquid-gas-vapor interactions and momentum transfer in high-pressure flows: Selecting Optimal Slip Velocity and Mass Transfer Models Understand how to choose and configure the right models for accurate representation of phase interactions and fuel vaporization in injection systems. Implementing Turbulence and Cavitation Effects Learn to incorporate crucial physical phenomena such as turbulence modulation and cavitation inception that govern multiphase behavior in fuel injectors. Analyzing Flow Patterns and Spray Characteristics Develop skills to interpret the complex behavior of three-phase flows within the fuel injector system: Visualizing Phase Distribution and Velocity Profiles Master techniques for creating and interpreting contours and vector plots that reveal the spatial distribution and movement of liquid fuel, air, and fuel vapor through the injector and nozzle. Quantifying Spray Penetration and Droplet Formation Learn methods to assess and analyze key parameters such as spray cone angle, droplet size distribution, and vapor phase concentration in the near-nozzle region. Investigating Effects of Operating Conditions on Injector Performance Explore how various factors impact the behavior of fuel sprays in injection systems: Impact of Injection Pressure on Spray Atomization Discover how changes in fuel injection pressure affect the fluid dynamics and spray characteristics crucial for efficient combustion. Influence of Nozzle Geometry on Flow Patterns Learn to use CFD results to evaluate how different nozzle designs affect the overall spray formation and fuel distribution patterns. Interpreting Steady-State Simulation Results for Comprehensive Performance Analysis Develop expertise in extracting meaningful insights from your equilibrium simulations: Analyzing Fuel-Air Mixing and Vapor Distribution Master techniques for processing and interpreting CFD data to assess the effectiveness of fuel atomization and vapor formation for various engine operating conditions. Identifying Optimization Opportunities for Injector Design Learn to pinpoint crucial areas in the simulation that reveal potential improvements in injector geometry for enhanced performance and efficiency. Practical Applications and Industry Relevance Connect simulation insights to real-world engineering challenges: Optimizing Fuel Injection Systems for Improved Engine Efficiency Explore how CFD simulations can inform the design and improvement of fuel injectors for better fuel economy and reduced emissions in automotive and aerospace applications. Enhancing Combustion Stability through Precise Fuel Delivery Understand how the principles learned in this module can contribute to the development of more stable and efficient combustion processes in various engine types. Why This Module is Essential for Beginner Multiphase Flow Engineers This beginner-level module offers a practical introduction to advanced CFD techniques in fuel injector system simulation. By completing this simulation, you’ll gain valuable insights into: Fundamental principles of the Mixture approach and its application in modeling complex three-phase flows in high-pressure fuel injection systems Essential CFD techniques for simulating liquid-gas-vapor interactions, phase coupling, and momentum transfer in automotive and aerospace applications Practical applications of Mixture CFD analysis in engine technology, combustion engineering, and propulsion system design By the end of this episode, you’ll have developed crucial skills in: Setting up and running three-phase fuel injector simulations using the Mixture multiphase model in ANSYS Fluent Interpreting steady-state simulation results to assess flow patterns, phase distributions, and spray formation characteristics Applying CFD insights to enhance understanding and design in applications involving multiphase flows in fuel injection systems This knowledge forms a solid foundation for engineers and researchers looking to specialize in engine technology and multiphase flow analysis, providing a springboard for advanced studies in fluid dynamics, combustion processes, and innovative fuel injection technologies. Join us on this exciting journey into the world of fuel injector three-phase flow CFD simulation, and take your first steps towards becoming an expert in multiphase dynamics modeling for critical automotive and aerospace applications!
-
Section 1
Shower Drain (VOF)
-
Mastering Multiphase Flow: Shower Channel Drain CFD Simulation Using VOF Method Welcome to the “Shower Channel Drain CFD Simulation” episode of our “MULTI-PHASE Flow: BEGINNER” course. This comprehensive module introduces you to the fascinating world of dynamic multiphase flow modeling using the Volume of Fluid (VOF) method in ANSYS Fluent. Dive into the intricacies of time-dependent free surface flow analysis through a practical household application, and learn how to simulate and optimize drainage systems with powerful CFD techniques. Understanding the Volume of Fluid (VOF) Model Before delving into the simulation specifics, let’s explore the fundamental concepts of the VOF method. Principles of VOF in Multiphase Flow Modeling Discover how the VOF method accurately tracks and simulates the dynamic interface between different fluid phases, such as water and air. Applications of VOF in Engineering and Household Systems Learn about the diverse applications of VOF modeling, from industrial processes to everyday scenarios like shower drains. Setting Up the Pre-configured Shower Drain Geometry This section focuses on preparing your simulation environment: Importing and Refining the Drain Model Gain insights into efficiently setting up the shower drain geometry in ANSYS Fluent for transient analysis. Mesh Generation Strategies for Free Surface Flows Understand the crucial aspects of creating an appropriate mesh that captures both the drain structure and the dynamic fluid interface. Implementing Time-Dependent Boundary Conditions Master the art of defining realistic, time-varying conditions for your simulation: Configuring Water Inlet Flow Rates Learn to set up time-dependent water inflow conditions that mimic real shower usage patterns. Defining Air-Water Interface Parameters Explore techniques for accurately representing the initial and evolving air-water interface in the drain channel. Configuring VOF Parameters and Time-Stepping Dive deep into the critical settings that ensure accurate phase tracking over time: Selecting Appropriate VOF Scheme and Settings Understand how to choose and configure the right VOF parameters for optimal simulation accuracy and stability. Time-Stepping Strategies for Transient Simulations Learn to balance computational efficiency with solution accuracy through proper time-step selection and adaptive time-stepping techniques. Analyzing Evolving Water Flow Patterns and Air Entrainment Develop skills to interpret the dynamic behavior of multiphase flows: Visualizing Phase Distribution Over Time Master techniques for creating and interpreting time-dependent phase contours and volume fraction animations. Quantifying Air Entrainment in the Drain Flow Learn methods to assess and analyze the amount of air captured in the water flow, a critical factor in drain performance. Investigating Temporal Effects on Drainage Efficiency Explore how time-dependent factors influence drain performance: Impact of Varying Flow Rates on Drain Capacity Discover how changes in water inflow over time affect the drain’s ability to efficiently remove water. Channel Design Optimization for Transient Flows Learn to use CFD results to evaluate and improve drain channel geometry for better performance under varying flow conditions. Interpreting Transient Simulation Results Develop expertise in extracting meaningful insights from your time-dependent simulations: Analyzing Time-Series Data for Performance Metrics Master techniques for processing and interpreting time-varying CFD data to assess overall drain efficiency. Identifying Critical Time Points in Drain Operation Learn to pinpoint crucial moments in the simulation that reveal potential issues or opportunities for design improvement. Practical Applications and Industry Relevance Connect simulation insights to real-world engineering challenges: Optimizing Residential and Commercial Drainage Systems Explore how CFD simulations can inform the design and improvement of various drainage applications beyond shower drains. Scaling VOF Simulations for Larger Water Management Projects Understand how the principles learned in this module can be applied to larger-scale water flow and management scenarios. Why This Module is Essential for Beginner Multiphase Flow Engineers This beginner-level module offers a practical introduction to advanced CFD techniques in multiphase flow analysis. By completing this simulation, you’ll gain valuable insights into: Fundamental principles of the Volume of Fluid method and its application in tracking time-varying fluid interfaces Essential CFD techniques for modeling complex, time-dependent free surface flows Practical applications of multiphase CFD analysis in everyday engineering challenges By the end of this episode, you’ll have developed crucial skills in: Setting up and running transient multiphase simulations using the VOF method in ANSYS Fluent Interpreting time-dependent simulation results to assess and optimize drainage system performance Applying CFD insights to enhance the efficiency of free surface flow systems in various engineering applications This knowledge forms a solid foundation for engineers looking to specialize in multiphase flow analysis, providing a springboard for advanced studies in fluid dynamics, drainage system design, and innovative water management solutions. Join us on this exciting journey into the world of shower channel drain CFD simulation, and take your first steps towards becoming an expert in dynamic multiphase flow modeling for real-world engineering applications!
Episode 1 18m 43s Free Episode
-
-
Section 2
Gas Sweetening (VOF)
-
Mastering Gas Sweetening Hydrodynamics: Advanced CFD Simulation Using VOF Method Welcome to the “Gas Sweetening Hydrodynamic CFD Simulation” episode of our “MULTI-PHASE Flow: BEGINNER” course. This comprehensive module introduces you to the intricate world of industrial process simulation, focusing on the critical application of gas sweetening in the oil and gas industry. Learn how to leverage the Volume of Fluid (VOF) method in ANSYS Fluent to simulate and optimize complex gas-liquid interactions in vertical columns. Understanding the Volume of Fluid (VOF) Model in Gas Sweetening Before diving into the simulation specifics, let’s explore the fundamental concepts of VOF in the context of gas sweetening. Principles of VOF for Gas-Liquid Interactions Discover how the VOF method accurately captures the dynamic interface between gas and liquid phases in a sweetening column. Applications of VOF in Oil and Gas Processing Learn about the diverse applications of VOF modeling in the petroleum industry, from gas sweetening to other separation processes. Exploring the Pre-configured Gas Sweetening Unit Geometry This section focuses on familiarizing yourself with the simulation environment: Anatomy of a Gas Sweetening Column Gain insights into the key components and design features of a typical gas sweetening unit represented in the ANSYS Fluent model. Mesh Characteristics for Multiphase Flow in Vertical Columns Understand the crucial aspects of the pre-configured mesh that enable accurate simulation of gas-liquid flow patterns. Implementing Boundary and Operating Conditions for Gas-Liquid Contacting Master the art of defining realistic conditions for your gas sweetening simulation: Setting Up Gas and Liquid Inlet Parameters Learn to configure appropriate flow rates, compositions, and properties for the incoming gas and liquid absorbent streams. Defining Column Pressure and Temperature Conditions Explore techniques for accurately representing the operating conditions within the sweetening column. Configuring VOF Parameters for Accurate Interface Capture Dive deep into the critical settings that ensure precise tracking of gas-liquid interfaces: Selecting Optimal VOF Scheme for Gas Sweetening Understand how to choose and configure the right VOF parameters for stable and accurate multiphase simulations in vertical columns. Surface Tension and Wall Adhesion Settings Learn to incorporate surface tension effects and wall interactions crucial for modeling falling liquid films and rising gas bubbles. Analyzing Hydrodynamic Behavior of Falling Liquid Films and Rising Gas Bubbles Develop skills to interpret the complex flow patterns in gas sweetening columns: Visualizing Phase Distribution and Flow Patterns Master techniques for creating and interpreting contours and vector plots that reveal the intricate gas-liquid flow structures. Quantifying Liquid Holdup and Gas Bubble Characteristics Learn methods to assess and analyze key hydrodynamic parameters that influence mass transfer efficiency. Investigating Effects of Operating Conditions on Sweetening Efficiency Explore how various factors impact the performance of gas sweetening processes: Impact of Gas and Liquid Flow Rates on Column Hydrodynamics Discover how changes in input flow rates affect the gas-liquid contacting patterns and overall column efficiency. Column Design Optimization for Enhanced Mass Transfer Learn to use CFD results to evaluate and improve column internals for better gas-liquid interaction and separation performance. Interpreting Transient Simulation Results for Process Understanding Develop expertise in extracting meaningful insights from your multiphase simulations: Analyzing Time-Dependent Flow Behavior Master techniques for processing and interpreting transient CFD data to assess the dynamic nature of gas-liquid interactions. Correlating Hydrodynamics with Mass Transfer Efficiency Learn to link hydrodynamic simulation results with potential mass transfer performance, bridging CFD with process engineering. Practical Applications and Industry Relevance Connect simulation insights to real-world engineering challenges: Optimizing Industrial Gas Sweetening Units Explore how CFD simulations can inform the design and improvement of full-scale gas sweetening facilities in the oil and gas industry. Extending VOF Techniques to Other Separation Processes Understand how the principles learned in this module can be applied to various multiphase separation processes in chemical and petrochemical industries. Why This Module is Essential for Beginner Multiphase Flow Engineers This beginner-level module offers a practical introduction to advanced CFD techniques in industrial process simulation. By completing this simulation, you’ll gain valuable insights into: Fundamental principles of the Volume of Fluid method and its application in modeling complex gas-liquid interactions Essential CFD techniques for simulating multiphase flows in vertical process equipment Practical applications of multiphase CFD analysis in critical oil and gas industry processes By the end of this episode, you’ll have developed crucial skills in: Setting up and running gas sweetening hydrodynamic simulations using the VOF method in ANSYS Fluent Interpreting simulation results to assess and optimize column performance and efficiency Applying CFD insights to enhance the design and operation of gas-liquid contacting equipment in various industrial applications This knowledge forms a solid foundation for engineers looking to specialize in multiphase flow analysis in the process industry, providing a springboard for advanced studies in process equipment design, separation technology, and innovative gas treatment solutions. Join us on this exciting journey into the world of gas sweetening hydrodynamic CFD simulation, and take your first steps towards becoming an expert in multiphase flow modeling for critical industrial processes!
Episode 1 16m 6s
-
-
Section 3
Droplet Dynamics (VOF)
-
Mastering Droplet Dynamics: Falling Droplet CFD Simulation Using VOF Method Welcome to the “Falling Droplet CFD Simulation” episode of our “MULTI-PHASE Flow: BEGINNER” course. This comprehensive module introduces you to the captivating world of fluid dynamics, focusing on the behavior of falling water droplets in air. Learn how to leverage the Volume of Fluid (VOF) method in ANSYS Fluent to simulate and analyze complex droplet phenomena, providing a perfect foundation for multiphase flow modeling. Understanding the Volume of Fluid (VOF) Model for Droplet Simulation Before diving into the simulation specifics, let’s explore the fundamental concepts of VOF in the context of droplet dynamics. Principles of VOF for Liquid-Gas Interfaces Discover how the VOF method accurately captures the dynamic interface between a water droplet and the surrounding air. Applications of Droplet Simulations in Engineering Learn about the diverse applications of droplet modeling, from spray systems and inkjet printing to rainfall analysis and beyond. Exploring the Pre-configured Axisymmetric Droplet Geometry This section focuses on familiarizing yourself with the simulation environment: Anatomy of the Axisymmetric Droplet Model Gain insights into the key features of the pre-configured geometry representing the droplet and surrounding air domain. Mesh Characteristics for Accurate Droplet Interface Capture Understand the crucial aspects of the mesh that enable precise simulation of droplet deformation and movement. Implementing Boundary Conditions and Initial Setup for Droplet Simulation Master the art of defining realistic conditions for your falling droplet simulation: Setting Up Initial Droplet Parameters Learn to configure appropriate size, shape, and initial velocity for the water droplet at the start of the simulation. Defining Air Domain and Boundary Conditions Explore techniques for accurately representing the surrounding air and implementing appropriate boundary conditions for the simulation domain. Configuring VOF Parameters for Precise Interface Tracking Dive deep into the critical settings that ensure accurate capture of droplet behavior: Selecting Optimal VOF Scheme for Droplet Dynamics Understand how to choose and configure the right VOF parameters for stable and accurate interface tracking during droplet fall. Implementing Surface Tension and Gravitational Effects Learn to incorporate crucial physical phenomena such as surface tension and gravity that govern droplet behavior. Analyzing Droplet Deformation, Oscillation, and Potential Breakup Develop skills to interpret the complex behavior of falling droplets: Visualizing Droplet Shape Evolution Master techniques for creating and interpreting time-dependent contours and animations that reveal droplet deformation and oscillation. Quantifying Droplet Deformation Metrics Learn methods to assess and analyze key parameters such as aspect ratio and oscillation frequency during droplet fall. Investigating Effects of Physical Parameters on Droplet Dynamics Explore how various factors impact the behavior of falling droplets: Impact of Surface Tension on Droplet Stability Discover how changes in surface tension affect the droplet’s ability to maintain its shape or break up during free fall. Air Resistance and Its Influence on Droplet Terminal Velocity Learn to use CFD results to evaluate the effects of air drag on droplet motion and equilibrium velocity. Interpreting Transient Simulation Results for Comprehensive Droplet Behavior Analysis Develop expertise in extracting meaningful insights from your time-dependent simulations: Analyzing Time-Series Data of Droplet Properties Master techniques for processing and interpreting transient CFD data to assess the evolution of droplet characteristics over time. Identifying Critical Stages in Droplet Fall Learn to pinpoint crucial moments in the simulation that reveal important physical phenomena or potential breakup events. Practical Applications and Research Relevance Connect simulation insights to real-world engineering and scientific challenges: Optimizing Spray Systems and Atomization Processes Explore how droplet CFD simulations can inform the design and improvement of industrial spray and atomization technologies. Advancing Meteorological and Climate Models Understand how the principles learned in this module can contribute to more accurate rainfall and cloud formation predictions in atmospheric science. Why This Module is Essential for Beginner Multiphase Flow Engineers This beginner-level module offers a practical introduction to advanced CFD techniques in droplet dynamics simulation. By completing this simulation, you’ll gain valuable insights into: Fundamental principles of the Volume of Fluid method and its application in modeling liquid-gas interfaces Essential CFD techniques for simulating surface tension-dominated flows and interfacial dynamics Practical applications of droplet CFD analysis in various engineering and scientific fields By the end of this episode, you’ll have developed crucial skills in: Setting up and running falling droplet simulations using the VOF method in ANSYS Fluent Interpreting simulation results to assess droplet behavior, deformation, and stability Applying CFD insights to enhance understanding and design in applications involving droplet dynamics This knowledge forms a solid foundation for engineers and researchers looking to specialize in multiphase flow analysis, providing a springboard for advanced studies in fluid dynamics, spray technology, and innovative applications in fields ranging from manufacturing to environmental science. Join us on this exciting journey into the world of falling droplet CFD simulation, and take your first steps towards becoming an expert in multiphase flow modeling for a wide range of scientific and engineering applications!
Episode 1 13m 3s
-
-
Section 4
Ogee Spillway (VOF)
-
Mastering Hydraulic Engineering: Ogee Spillway CFD Simulation Using VOF Method Welcome to the “Ogee Spillway CFD Simulation” episode of our “MULTI-PHASE Flow: BEGINNER” course. This comprehensive module introduces you to the dynamic world of hydraulic engineering, focusing on the complex behavior of water flow over an Ogee spillway. Learn how to leverage the Volume of Fluid (VOF) method in ANSYS Fluent to simulate and analyze critical hydraulic structures, providing essential skills for civil and hydraulic engineers. Understanding the Volume of Fluid (VOF) Model in Hydraulic Engineering Before diving into the simulation specifics, let’s explore the fundamental concepts of VOF in the context of spillway dynamics. Principles of VOF for Free-Surface Flows Discover how the VOF method accurately captures the dynamic interface between water and air in spillway simulations. Applications of VOF in Dam Design and Flood Control Learn about the diverse applications of VOF modeling in hydraulic engineering, from spillway design to flood management systems. Exploring the Pre-configured Ogee Spillway Geometry This section focuses on familiarizing yourself with the simulation environment: Anatomy of an Ogee Spillway Gain insights into the key components and design features of a typical Ogee spillway represented in the ANSYS Fluent model. Mesh Characteristics for Accurate Free-Surface Flow Simulation Understand the crucial aspects of the pre-configured mesh that enable precise simulation of water flow over the spillway. Implementing Time-Dependent Boundary Conditions for Spillway Flow Master the art of defining realistic conditions for your Ogee spillway simulation: Setting Up Water Inlet Parameters Learn to configure appropriate flow rates and water levels that mimic real-world spillway operating conditions. Defining Air-Water Interface and Outlet Conditions Explore techniques for accurately representing the initial and evolving air-water interface, as well as downstream conditions. Configuring VOF Parameters and Time-Stepping for Dynamic Flow Analysis Dive deep into the critical settings that ensure accurate interface tracking over time: Selecting Optimal VOF Scheme for Spillway Flows Understand how to choose and configure the right VOF parameters for stable and accurate free-surface simulations. Time-Stepping Strategies for Transient Hydraulic Simulations Learn to balance computational efficiency with solution accuracy through proper time-step selection and adaptive time-stepping techniques. Analyzing Evolving Water Flow Patterns and Hydraulic Parameters Develop skills to interpret the complex behavior of water flow over spillways: Visualizing Flow Profiles and Velocity Distributions Master techniques for creating and interpreting time-dependent contours and vector plots that reveal the intricate flow structures. Quantifying Pressure Distributions and Hydrodynamic Forces Learn methods to assess and analyze key hydraulic parameters that influence spillway performance and structural design. Investigating Temporal Effects on Spillway Hydraulic Performance Explore how time-dependent factors impact spillway behavior: Impact of Varying Flow Rates on Spillway Efficiency Discover how changes in water inflow over time affect the spillway’s capacity and flow characteristics. Spillway Design Optimization for Dynamic Flow Conditions Learn to use CFD results to evaluate and improve spillway geometry for better performance under varying hydraulic loads. Interpreting Transient Simulation Results for Comprehensive Spillway Analysis Develop expertise in extracting meaningful insights from your time-dependent simulations: Analyzing Time-Series Data for Key Performance Metrics Master techniques for processing and interpreting time-varying CFD data to assess overall spillway efficiency and behavior. Identifying Critical Flow Regimes and Hydraulic Phenomena Learn to pinpoint crucial moments in the simulation that reveal important hydraulic events or potential design issues. Practical Applications and Engineering Relevance Connect simulation insights to real-world engineering challenges: Optimizing Dam Safety and Flood Control Systems Explore how CFD simulations can inform the design and improvement of large-scale hydraulic structures for enhanced safety and performance. Scaling VOF Simulations for Comprehensive Watershed Management Understand how the principles learned in this module can be applied to larger-scale water management and flood control projects. Why This Module is Essential for Beginner Multiphase Flow Engineers This beginner-level module offers a practical introduction to advanced CFD techniques in hydraulic engineering. By completing this simulation, you’ll gain valuable insights into: Fundamental principles of the Volume of Fluid method and its application in modeling free-surface flows Essential CFD techniques for simulating complex, time-dependent hydraulic structures Practical applications of multiphase CFD analysis in critical civil engineering projects By the end of this episode, you’ll have developed crucial skills in: Setting up and running transient Ogee spillway simulations using the VOF method in ANSYS Fluent Interpreting time-dependent simulation results to assess and optimize spillway performance Applying CFD insights to enhance the design and operation of hydraulic structures in various engineering applications This knowledge forms a solid foundation for engineers looking to specialize in hydraulic engineering and multiphase flow analysis, providing a springboard for advanced studies in dam design, flood control, and innovative water management solutions. Join us on this exciting journey into the world of Ogee spillway CFD simulation, and take your first steps towards becoming an expert in dynamic hydraulic modeling for critical infrastructure projects!
Episode 1 12m 40s
-
-
Section 5
Injector (VOF)
-
Mastering Fuel Injector Dynamics: Advanced CFD Simulation Using VOF Multiphase Model Welcome to the “Injector CFD Simulation” episode of our “MULTI-PHASE Flow: BEGINNER” course. This comprehensive module introduces you to the intricate world of multi-phase flows within fuel injectors, a critical component in various combustion systems. Learn how to leverage the Volume of Fluid (VOF) multiphase model in ANSYS Fluent to simulate and analyze complex fluid interactions, providing essential skills for engineers in automotive, aerospace, and energy sectors. Understanding the Volume of Fluid (VOF) Model for Injector Simulation Before diving into the simulation specifics, let’s explore the fundamental concepts of VOF in the context of fuel injection dynamics. Principles of VOF for Liquid-Gas Interfaces in Confined Geometries Discover how the VOF method accurately captures the dynamic interface between liquid fuel and gas phases within an injector’s complex geometry. Applications of Injector Simulations in Engineering Learn about the diverse applications of injector modeling, from automotive fuel systems to aerospace propulsion and industrial combustion processes. Exploring the Pre-configured Injector Geometry This section focuses on familiarizing yourself with the simulation environment: Anatomy of a Fuel Injector Model Gain insights into the key features of the pre-configured geometry representing a real-world fuel injector design. Mesh Characteristics for Accurate Interface Capture in Injectors Understand the crucial aspects of the mesh that enable precise simulation of fluid behavior within the intricate injector passages. Implementing Boundary Conditions for Realistic Injector Operation Master the art of defining realistic conditions for your fuel injector simulation: Setting Up Fuel Inlet Parameters Learn to configure appropriate pressure, velocity, and fluid properties for the liquid fuel at the injector inlet. Defining Gas Phase and Wall Conditions Explore techniques for accurately representing the gas phase environment and implementing appropriate wall boundary conditions within the injector. Fine-tuning VOF Parameters for Precise Interface Tracking Dive deep into the critical settings that ensure accurate capture of liquid-gas interface behavior: Selecting Optimal VOF Scheme for Injector Flows Understand how to choose and configure the right VOF parameters for stable and accurate interface tracking within the complex injector geometry. Implementing Surface Tension and Turbulence Effects Learn to incorporate crucial physical phenomena such as surface tension and turbulence that govern fluid behavior in injectors. Analyzing Volume Fraction Distribution and Flow Patterns Develop skills to interpret the complex behavior of multi-phase flows within injectors: Visualizing Phase Distribution in Injector Passages Master techniques for creating and interpreting contours and animations that reveal the spatial distribution of liquid fuel and gas phases. Quantifying Flow Characteristics and Spray Formation Learn methods to assess and analyze key parameters such as velocity profiles, pressure distributions, and initial spray characteristics at the nozzle exit. Investigating Effects of Injector Design and Operating Conditions Explore how various factors impact the performance of fuel injectors: Impact of Injection Pressure on Flow Behavior Discover how changes in injection pressure affect the fluid dynamics and phase distribution within the injector. Nozzle Geometry Optimization for Enhanced Performance Learn to use CFD results to evaluate and improve nozzle design for better atomization and spray characteristics. Interpreting Simulation Results for Comprehensive Injector Performance Analysis Develop expertise in extracting meaningful insights from your steady-state simulations: Analyzing Key Performance Metrics Master techniques for processing and interpreting CFD data to assess injector efficiency, flow uniformity, and potential cavitation risks. Correlating Simulation Results with Real-World Injector Behavior Learn to relate CFD insights to practical injector performance characteristics and potential design improvements. Practical Applications and Industry Relevance Connect simulation insights to real-world engineering challenges: Optimizing Fuel Injection Systems for Improved Engine Performance Explore how injector CFD simulations can inform the design and improvement of fuel systems in automotive and aerospace applications. Advancing Clean Combustion Technologies Understand how the principles learned in this module can contribute to the development of more efficient and cleaner-burning injection systems. Why This Module is Essential for Beginner Multiphase Flow Engineers This beginner-level module offers a practical introduction to advanced CFD techniques in fuel injector simulation. By completing this simulation, you’ll gain valuable insights into: Fundamental principles of the Volume of Fluid method and its application in modeling complex multi-phase flows in confined geometries Essential CFD techniques for simulating liquid-gas interactions and interface dynamics in high-pressure injection systems Practical applications of injector CFD analysis in various engineering fields, including automotive, aerospace, and energy sectors By the end of this episode, you’ll have developed crucial skills in: Setting up and running fuel injector simulations using the VOF multiphase model in ANSYS Fluent Interpreting simulation results to assess injector performance, flow characteristics, and phase distribution Applying CFD insights to enhance understanding and design in applications involving multi-phase flows in complex geometries This knowledge forms a solid foundation for engineers and researchers looking to specialize in multi-phase flow analysis, providing a springboard for advanced studies in combustion systems, spray dynamics, and innovative fuel injection technologies. Join us on this exciting journey into the world of fuel injector CFD simulation, and take your first steps towards becoming an expert in multi-phase flow modeling for critical engineering applications!
Episode 1 13m 34s
-
-
Section 6
Tank Filling (VOF)
-
Mastering Multi-Fluid Dynamics: 3-Phase Tank Filling CFD Simulation Using VOF Model Welcome to the “3-phase Tank Filling CFD Simulation” episode of our “MULTI-PHASE Flow: BEGINNER” course. This comprehensive module introduces you to the intricate world of multi-fluid interactions within storage tanks, a critical aspect of various industrial processes. Learn how to leverage the Volume of Fluid (VOF) multiphase model in ANSYS Fluent to simulate and analyze complex three-phase flows, providing essential skills for engineers in chemical processing, oil and gas, and environmental sectors. Understanding the Volume of Fluid (VOF) Model for Multi-Fluid Simulations Before diving into the simulation specifics, let’s explore the fundamental concepts of VOF in the context of tank filling dynamics. Principles of VOF for Multiple Immiscible Fluids Discover how the VOF method accurately captures the dynamic interfaces between three distinct phases (e.g., water, oil, and air) during tank filling. Applications of Multi-Fluid Tank Simulations in Industry Learn about the diverse applications of three-phase flow modeling, from oil storage tanks to chemical reactors and wastewater treatment facilities. Exploring the Pre-configured Tank Geometry This section focuses on familiarizing yourself with the simulation environment: Anatomy of a Multi-Fluid Storage Tank Model Gain insights into the key features of the pre-configured geometry representing a real-world storage vessel suitable for multi-fluid operations. Mesh Characteristics for Accurate Interface Capture in Tanks Understand the crucial aspects of the mesh that enable precise simulation of fluid behavior and interface dynamics within the tank. Implementing Boundary Conditions for Realistic Tank Filling Scenarios Master the art of defining realistic conditions for your three-phase tank filling simulation: Setting Up Fluid Inlet Parameters Learn to configure appropriate flow rates, velocities, and fluid properties for multiple inlets, mimicking real-world filling processes. Defining Tank Wall and Outlet Conditions Explore techniques for accurately representing tank boundaries and implementing appropriate outlet conditions for displaced fluids. Fine-tuning VOF Parameters for Precise Multi-Interface Tracking Dive deep into the critical settings that ensure accurate capture of multiple fluid interfaces: Selecting Optimal VOF Scheme for Multi-Fluid Flows Understand how to choose and configure the right VOF parameters for stable and accurate interface tracking between three distinct phases. Implementing Surface Tension and Gravity Effects Learn to incorporate crucial physical phenomena such as interfacial tension and gravitational stratification that govern multi-fluid behavior in tanks. Analyzing Fluid Interface Evolution and Volume Fraction Distributions Develop skills to interpret the complex behavior of multi-phase flows within storage tanks: Visualizing Phase Distribution and Interface Dynamics Master techniques for creating and interpreting time-dependent contours and animations that reveal the spatial distribution and movement of multiple fluids. Quantifying Fluid Stratification and Mixing Phenomena Learn methods to assess and analyze key parameters such as phase volume fractions, interface positions, and potential mixing or separation zones. Investigating Effects of Operating Conditions on Filling Patterns Explore how various factors impact the behavior of fluids during tank filling: Impact of Inlet Flow Rates on Fluid Displacement Discover how changes in inlet conditions affect the fluid dynamics and interface evolution within the tank. Tank Geometry Optimization for Desired Stratification Learn to use CFD results to evaluate and improve tank design for better fluid separation or mixing, depending on the application requirements. Interpreting Transient Simulation Results for Comprehensive Process Understanding Develop expertise in extracting meaningful insights from your time-dependent simulations: Analyzing Time-Series Data of Fluid Behaviors Master techniques for processing and interpreting transient CFD data to assess the dynamic nature of multi-fluid interactions throughout the filling process. Identifying Critical Stages in Tank Filling Operations Learn to pinpoint crucial moments in the simulation that reveal important phenomena or potential operational issues. Practical Applications and Industry Relevance Connect simulation insights to real-world engineering challenges: Optimizing Storage Tank Designs for Multi-Fluid Handling Explore how CFD simulations can inform the design and improvement of storage facilities in various industries, from petrochemical to environmental engineering. Enhancing Separation Processes in Multi-Phase Systems Understand how the principles learned in this module can contribute to the development of more efficient fluid separation and handling techniques in industrial processes. Why This Module is Essential for Beginner Multiphase Flow Engineers This beginner-level module offers a practical introduction to advanced CFD techniques in multi-fluid tank filling simulation. By completing this simulation, you’ll gain valuable insights into: Fundamental principles of the Volume of Fluid method and its application in modeling complex three-phase flows in storage tanks Essential CFD techniques for simulating gravity-driven flows, buoyancy effects, and interface dynamics in multi-fluid systems Practical applications of multi-phase CFD analysis in various industrial sectors, including chemical processing, oil and gas, and environmental engineering By the end of this episode, you’ll have developed crucial skills in: Setting up and running three-phase tank filling simulations using the VOF multiphase model in ANSYS Fluent Interpreting transient simulation results to assess fluid displacement, interface dynamics, and potential mixing or separation issues Applying CFD insights to enhance understanding and design in applications involving multi-fluid storage and handling operations This knowledge forms a solid foundation for engineers and researchers looking to specialize in multi-phase flow analysis, providing a springboard for advanced studies in fluid dynamics, process engineering, and innovative multi-fluid handling technologies. Join us on this exciting journey into the world of 3-phase tank filling CFD simulation, and take your first steps towards becoming an expert in multi-fluid dynamics modeling for critical industrial applications!
Episode 1 27m 24s
-
-
Section 7
Fluid Flow in Moving Cylinder (EULERIAN)
-
Mastering Complex Multiphase Dynamics: Eulerian Two-Phase Flow in a Moving Wall Cylinder CFD Simulation Welcome to the “Eulerian Two Phase Flow in a Moving Wall Cylinder CFD Simulation” episode of our “MULTI-PHASE Flow: BEGINNER” course. This comprehensive module introduces you to the intricate world of fluid-fluid interactions in dynamic systems, a critical aspect of various industrial processes. Learn how to leverage the Eulerian multiphase model in ANSYS Fluent to simulate and analyze complex two-phase flows, providing essential skills for engineers in chemical processing, oil and gas, and energy sectors. Understanding the Eulerian Multiphase Model for Immiscible Fluid Interactions Before diving into the simulation specifics, let’s explore the fundamental concepts of the Eulerian approach in the context of two-phase flow dynamics. Principles of Eulerian Modeling for Continuous Fluid Phases Discover how the Eulerian model treats both phases as interpenetrating continua, allowing for accurate representation of phase interactions and momentum transfer. Applications of Two-Phase Flow Simulations in Industry Learn about the diverse applications of Eulerian multiphase modeling, from liquid-liquid extraction processes to oil-water separators and multiphase reactors. Exploring the Pre-configured Cylindrical Geometry with Moving Wall This section focuses on familiarizing yourself with the simulation environment: Anatomy of a Cylindrical Reactor Model with Dynamic Boundary Gain insights into the key features of the pre-configured geometry representing a real-world cylindrical system with a moving wall. Mesh Characteristics for Accurate Phase Interaction Capture Understand the crucial aspects of the mesh that enable precise simulation of fluid behavior and phase coupling within the dynamic cylinder. Implementing Boundary Conditions for Realistic Two-Phase Flow Scenarios Master the art of defining realistic conditions for your two-phase flow simulation in a moving boundary system: Setting Up Fluid Inlet and Outlet Parameters Learn to configure appropriate flow rates, velocities, and phase fractions for inlets and outlets, mimicking real-world multiphase processes. Defining Moving Wall and Stationary Boundary Conditions Explore techniques for accurately representing the moving cylindrical wall and implementing appropriate conditions for other boundaries. Configuring Eulerian Model Parameters for Precise Phase Coupling Dive deep into the critical settings that ensure accurate capture of phase interactions and momentum transfer: Selecting Optimal Drag Models for Immiscible Fluids Understand how to choose and configure the right drag models for accurate representation of interfacial forces between the two phases. Implementing Turbulence and Phase Coupling Effects Learn to incorporate crucial physical phenomena such as turbulence modulation and momentum exchange that govern multiphase behavior in dynamic systems. Analyzing Phase Distribution and Flow Field Characteristics Develop skills to interpret the complex behavior of two-phase flows within the moving wall cylinder: Visualizing Phase Fractions and Velocity Profiles Master techniques for creating and interpreting contours and vector plots that reveal the spatial distribution and movement of both fluid phases. Quantifying Mixing Patterns and Phase Segregation Learn methods to assess and analyze key parameters such as phase volume fractions, interfacial area density, and mixing indices. Investigating Effects of Operating Conditions on Two-Phase Interactions Explore how various factors impact the behavior of fluids in the dynamic cylindrical system: Impact of Wall Motion on Phase Distribution Discover how changes in wall velocity and motion patterns affect the fluid dynamics and phase interactions within the cylinder. Influence of Fluid Properties on Mixing and Separation Learn to use CFD results to evaluate how different fluid combinations and properties affect the overall multiphase behavior and process efficiency. Interpreting Steady-State Simulation Results for Comprehensive Process Understanding Develop expertise in extracting meaningful insights from your equilibrium simulations: Analyzing Global and Local Phase Characteristics Master techniques for processing and interpreting CFD data to assess overall phase distribution and local flow phenomena at equilibrium conditions. Identifying Critical Zones for Process Optimization Learn to pinpoint crucial areas in the simulation that reveal important mixing, separation, or potential operational issues. Practical Applications and Industry Relevance Connect simulation insights to real-world engineering challenges: Optimizing Multiphase Reactors and Extraction Processes Explore how CFD simulations can inform the design and improvement of industrial equipment involving immiscible fluid interactions. Enhancing Oil-Water Separation Techniques Understand how the principles learned in this module can contribute to the development of more efficient separation processes in the oil and gas industry. Why This Module is Essential for Beginner Multiphase Flow Engineers This beginner-level module offers a practical introduction to advanced CFD techniques in Eulerian multiphase flow simulation. By completing this simulation, you’ll gain valuable insights into: Fundamental principles of the Eulerian approach and its application in modeling complex two-phase flows in dynamic systems Essential CFD techniques for simulating immiscible fluid interactions, phase coupling, and momentum transfer in systems with moving boundaries Practical applications of Eulerian CFD analysis in various industrial sectors, including chemical processing, oil and gas, and energy engineering By the end of this episode, you’ll have developed crucial skills in: Setting up and running two-phase flow simulations using the Eulerian multiphase model in ANSYS Fluent Interpreting steady-state simulation results to assess phase distribution, interfacial momentum exchange, and flow field characteristics Applying CFD insights to enhance understanding and design in applications involving multiphase flows in dynamic systems This knowledge forms a solid foundation for engineers and researchers looking to specialize in multiphase flow analysis, providing a springboard for advanced studies in fluid dynamics, process engineering, and innovative multiphase handling technologies. Join us on this exciting journey into the world of Eulerian two-phase flow CFD simulation in a moving wall cylinder, and take your first steps towards becoming an expert in complex multiphase dynamics modeling for critical industrial applications!
Episode 1 13m 31s
-
-
Section 8
Fluid Flow in Convergent-Divergent Channel (EULERIAN)
-
Mastering Complex Multiphase Dynamics: Eulerian Two-Phase Flow in a Convergent-Divergent Channel CFD Simulation Welcome to the “Eulerian Two Phase Flow within a Convergent-Divergent Channel CFD Simulation” episode of our “MULTI-PHASE Flow: BEGINNER” course. This comprehensive module introduces you to the intricate world of fluid-fluid interactions in geometrically complex systems, a critical aspect of various industrial processes. Learn how to leverage the Eulerian multiphase model in ANSYS Fluent to simulate and analyze complex two-phase flows, providing essential skills for engineers in chemical processing, oil and gas, power generation, and aerospace sectors. Understanding the Eulerian Multiphase Model in Complex Geometries Before diving into the simulation specifics, let’s explore the fundamental concepts of the Eulerian approach in the context of convergent-divergent channel flow dynamics. Principles of Eulerian Modeling for Varying Flow Conditions Discover how the Eulerian model accurately represents phase interactions and momentum transfer in channels with changing cross-sections. Applications of Two-Phase Flow Simulations in Industrial Systems Learn about the diverse applications of Eulerian multiphase modeling in complex geometries, from nozzles and diffusers to heat exchangers and reactors. Exploring the Pre-configured Convergent-Divergent Channel Geometry This section focuses on familiarizing yourself with the simulation environment: Anatomy of a Convergent-Divergent Channel Model Gain insights into the key features of the pre-configured geometry representing a real-world flow system with varying cross-sectional areas. Mesh Characteristics for Accurate Phase Interaction Capture Understand the crucial aspects of the mesh that enable precise simulation of fluid behavior and phase coupling within the complex channel geometry. Implementing Boundary Conditions for Realistic Two-Phase Flow Scenarios Master the art of defining realistic conditions for your two-phase flow simulation in a convergent-divergent channel: Setting Up Fluid Inlet and Outlet Parameters Learn to configure appropriate flow rates, velocities, and phase fractions for inlets and outlets, mimicking real-world multiphase processes in varying geometries. Defining Wall Boundary Conditions and Roughness Effects Explore techniques for accurately representing channel walls and implementing appropriate conditions that affect flow behavior and phase interactions. Fine-tuning Eulerian Model Parameters for Precise Phase Coupling Dive deep into the critical settings that ensure accurate capture of phase interactions and momentum transfer in complex flow conditions: Selecting Optimal Drag and Lift Models for Immiscible Fluids Understand how to choose and configure the right interfacial force models for accurate representation of phase interactions in varying flow regimes. Implementing Turbulence Modulation and Phase Coupling Effects Learn to incorporate crucial physical phenomena such as turbulence modulation and momentum exchange that govern multiphase behavior in convergent-divergent flows. Analyzing Phase Distribution and Flow Field Characteristics Develop skills to interpret the complex behavior of two-phase flows within the convergent-divergent channel: Visualizing Phase Fractions and Velocity Profiles Along the Channel Master techniques for creating and interpreting contours and vector plots that reveal the spatial distribution and movement of both fluid phases through varying cross-sections. Quantifying Pressure Drops and Phase Separation Tendencies Learn methods to assess and analyze key parameters such as pressure gradients, phase volume fractions, and potential flow regime transitions along the channel. Investigating Effects of Channel Geometry on Two-Phase Interactions Explore how various factors impact the behavior of fluids in the convergent-divergent system: Impact of Area Changes on Phase Distribution and Velocities Discover how changes in channel cross-section affect the fluid dynamics and phase interactions within the convergent and divergent sections. Influence of Channel Angle on Flow Patterns and Separation Learn to use CFD results to evaluate how different convergent-divergent angles affect the overall multiphase behavior and potential phase separation. Interpreting Steady-State Simulation Results for Comprehensive Process Understanding Develop expertise in extracting meaningful insights from your equilibrium simulations: Analyzing Flow Regime Transitions Along the Channel Master techniques for processing and interpreting CFD data to identify potential changes in flow patterns and phase distributions at different channel sections. Identifying Critical Zones for Process Optimization Learn to pinpoint crucial areas in the simulation that reveal important phase interaction phenomena or potential operational issues. Practical Applications and Industry Relevance Connect simulation insights to real-world engineering challenges: Optimizing Multiphase Flow Systems in Complex Geometries Explore how CFD simulations can inform the design and improvement of industrial equipment involving immiscible fluid interactions in varying flow conditions. Enhancing Heat Transfer in Two-Phase Systems Understand how the principles learned in this module can contribute to the development of more efficient heat exchangers and thermal management systems. Why This Module is Essential for Beginner Multiphase Flow Engineers This beginner-level module offers a practical introduction to advanced CFD techniques in Eulerian multiphase flow simulation within complex geometries. By completing this simulation, you’ll gain valuable insights into: Fundamental principles of the Eulerian approach and its application in modeling complex two-phase flows in convergent-divergent channels Essential CFD techniques for simulating immiscible fluid interactions, phase coupling, and momentum transfer in varying flow conditions Practical applications of Eulerian CFD analysis in various industrial sectors, including chemical processing, oil and gas, power generation, and aerospace engineering By the end of this episode, you’ll have developed crucial skills in: Setting up and running two-phase flow simulations in complex geometries using the Eulerian multiphase model in ANSYS Fluent Interpreting steady-state simulation results to assess phase distribution, flow patterns, and potential flow regime transitions in convergent-divergent channels Applying CFD insights to enhance understanding and design in applications involving multiphase flows in geometrically complex systems This knowledge forms a solid foundation for engineers and researchers looking to specialize in multiphase flow analysis, providing a springboard for advanced studies in fluid dynamics, process engineering, and innovative multiphase handling technologies in complex geometries. Join us on this exciting journey into the world of Eulerian two-phase flow CFD simulation in a convergent-divergent channel, and take your first steps towards becoming an expert in complex multiphase dynamics modeling for critical industrial applications!
Episode 1 15m 7s
-
-
Section 9
Firehose (EULERIAN)
-
Mastering Firefighting Equipment Dynamics: Firehose CFD Simulation Using Eulerian Multiphase Approach Welcome to the “Firehose CFD Simulation” episode of our “MULTI-PHASE Flow: BEGINNER” course. This comprehensive module introduces you to the intricate world of water and air interactions within firefighting equipment, a critical aspect of emergency response system design. Learn how to leverage the Eulerian multiphase model in ANSYS Fluent to simulate and analyze complex two-phase flows in firehose systems, providing essential skills for engineers in fire safety, emergency response equipment design, and hydraulic systems. Understanding the Eulerian Multiphase Model in Firehose Systems Before diving into the simulation specifics, let’s explore the fundamental concepts of the Eulerian approach in the context of firehose flow dynamics. Principles of Eulerian Modeling for Water-Air Interactions Discover how the Eulerian model accurately represents phase interactions and momentum transfer in high-pressure water jets with air entrainment. Applications of Firehose Simulations in Safety Engineering Learn about the diverse applications of Eulerian multiphase modeling in firefighting equipment, from nozzle design to water jet optimization for various emergency scenarios. Exploring the Pre-configured Firehose Geometry This section focuses on familiarizing yourself with the simulation environment: Anatomy of a Firehose Model Gain insights into the key features of the pre-configured geometry representing a real-world firehose system, including hose and nozzle components. Mesh Characteristics for Accurate Phase Interaction Capture Understand the crucial aspects of the mesh that enable precise simulation of fluid behavior and phase coupling within the firehose and nozzle. Implementing Boundary Conditions for Realistic Firehose Operation Master the art of defining realistic conditions for your firehose simulation: Setting Up Water Inlet and Air Entrainment Parameters Learn to configure appropriate flow rates, pressures, and phase fractions for water inlet and air entrainment, mimicking real-world firehose operations. Defining Nozzle Outlet and Ambient Conditions Explore techniques for accurately representing nozzle exit conditions and implementing appropriate ambient air parameters for jet formation. Fine-tuning Eulerian Model Parameters for Precise Phase Coupling Dive deep into the critical settings that ensure accurate capture of water-air interactions and momentum transfer in high-pressure flows: Selecting Optimal Drag and Turbulence Models Understand how to choose and configure the right interfacial force and turbulence models for accurate representation of phase interactions in firehose systems. Implementing Droplet Breakup and Coalescence Effects Learn to incorporate crucial physical phenomena such as droplet formation and air bubble dynamics that govern multiphase behavior in water jets. Analyzing Flow Patterns and Jet Characteristics Develop skills to interpret the complex behavior of two-phase flows within the firehose system: Visualizing Velocity Profiles and Phase Distribution Master techniques for creating and interpreting contours and vector plots that reveal the spatial distribution and movement of water and air phases through the hose and nozzle. Quantifying Pressure Distribution and Jet Formation Learn methods to assess and analyze key parameters such as pressure gradients, water jet velocity, and spray pattern characteristics at the nozzle exit. Investigating Effects of Operating Conditions on Firehose Performance Explore how various factors impact the behavior of water jets in firefighting applications: Impact of Inlet Pressure on Jet Reach and Dispersion Discover how changes in water inlet pressure affect the fluid dynamics and jet characteristics crucial for firefighting effectiveness. Influence of Nozzle Design on Spray Patterns Learn to use CFD results to evaluate how different nozzle geometries affect the overall jet formation and water dispersion patterns. Interpreting Steady-State Simulation Results for Comprehensive Performance Analysis Develop expertise in extracting meaningful insights from your equilibrium simulations: Analyzing Jet Penetration and Coverage Area Master techniques for processing and interpreting CFD data to assess the effectiveness of water jet reach and coverage for various firefighting scenarios. Identifying Optimization Opportunities for Firehose Systems Learn to pinpoint crucial areas in the simulation that reveal potential improvements in firehose and nozzle design for enhanced performance. Practical Applications and Safety Relevance Connect simulation insights to real-world firefighting challenges: Optimizing Firefighting Equipment for Various Emergency Scenarios Explore how CFD simulations can inform the design and improvement of firehose systems for different types of fires and environmental conditions. Enhancing Firefighter Safety through Equipment Design Understand how the principles learned in this module can contribute to the development of more efficient and safer firefighting equipment. Why This Module is Essential for Beginner Multiphase Flow Engineers This beginner-level module offers a practical introduction to advanced CFD techniques in firehose system simulation. By completing this simulation, you’ll gain valuable insights into: Fundamental principles of the Eulerian approach and its application in modeling complex two-phase flows in high-pressure water jet systems Essential CFD techniques for simulating water-air interactions, phase coupling, and momentum transfer in firefighting equipment Practical applications of Eulerian CFD analysis in fire safety engineering, emergency response equipment design, and hydraulic systems optimization By the end of this episode, you’ll have developed crucial skills in: Setting up and running firehose simulations using the Eulerian multiphase model in ANSYS Fluent Interpreting steady-state simulation results to assess flow patterns, pressure distribution, and water jet formation characteristics Applying CFD insights to enhance understanding and design in applications involving multiphase flows in firefighting equipment This knowledge forms a solid foundation for engineers and researchers looking to specialize in safety equipment design and multiphase flow analysis, providing a springboard for advanced studies in fluid dynamics, emergency response systems, and innovative firefighting technologies. Join us on this exciting journey into the world of firehose CFD simulation, and take your first steps towards becoming an expert in multiphase dynamics modeling for critical safety applications!
Episode 1 11m 33s
-
-
Section 10
Fuel Injector 3-Phase (MIXTURE)
-
Mastering Fuel Injection Dynamics: Three-Phase Flow CFD Simulation Using Mixture Multiphase Model Welcome to the “Fuel Injector Three-Phase Flow CFD Simulation” episode of our “MULTI-PHASE Flow: BEGINNER” course. This comprehensive module introduces you to the intricate world of fuel injection systems, a critical component in automotive and aerospace engineering. Learn how to leverage the Mixture multiphase model in ANSYS Fluent to simulate and analyze complex three-phase flows in fuel injectors, providing essential skills for engineers in automotive, aerospace, and combustion engineering sectors. Understanding the Mixture Multiphase Model in Fuel Injection Systems Before diving into the simulation specifics, let’s explore the fundamental concepts of the Mixture approach in the context of fuel injector flow dynamics. Principles of Mixture Modeling for Liquid-Gas-Vapor Interactions Discover how the Mixture model accurately represents phase interactions, slip velocities, and mass transfer between liquid fuel, air, and fuel vapor phases in high-pressure injection systems. Applications of Three-Phase Flow Simulations in Engine Technology Learn about the diverse applications of Mixture multiphase modeling in fuel injection systems, from automotive engines to aerospace propulsion systems. Exploring the Pre-configured Fuel Injector Geometry This section focuses on familiarizing yourself with the simulation environment: Anatomy of a Fuel Injector Model Gain insights into the key features of the pre-configured geometry representing a real-world fuel injector system, including internal passages and nozzle design. Mesh Characteristics for Accurate Phase Interaction Capture Understand the crucial aspects of the mesh that enable precise simulation of fluid behavior and phase coupling within the complex injector geometry. Implementing Boundary Conditions for Realistic Fuel Injection Scenarios Master the art of defining realistic conditions for your three-phase fuel injector simulation: Setting Up Fuel Inlet and Air Intake Parameters Learn to configure appropriate flow rates, pressures, and phase fractions for fuel inlet and air intake, mimicking real-world injection processes. Defining Nozzle Outlet and Ambient Conditions Explore techniques for accurately representing nozzle exit conditions and implementing appropriate ambient parameters for spray formation. Fine-tuning Mixture Model Parameters for Precise Phase Coupling Dive deep into the critical settings that ensure accurate capture of liquid-gas-vapor interactions and momentum transfer in high-pressure flows: Selecting Optimal Slip Velocity and Mass Transfer Models Understand how to choose and configure the right models for accurate representation of phase interactions and fuel vaporization in injection systems. Implementing Turbulence and Cavitation Effects Learn to incorporate crucial physical phenomena such as turbulence modulation and cavitation inception that govern multiphase behavior in fuel injectors. Analyzing Flow Patterns and Spray Characteristics Develop skills to interpret the complex behavior of three-phase flows within the fuel injector system: Visualizing Phase Distribution and Velocity Profiles Master techniques for creating and interpreting contours and vector plots that reveal the spatial distribution and movement of liquid fuel, air, and fuel vapor through the injector and nozzle. Quantifying Spray Penetration and Droplet Formation Learn methods to assess and analyze key parameters such as spray cone angle, droplet size distribution, and vapor phase concentration in the near-nozzle region. Investigating Effects of Operating Conditions on Injector Performance Explore how various factors impact the behavior of fuel sprays in injection systems: Impact of Injection Pressure on Spray Atomization Discover how changes in fuel injection pressure affect the fluid dynamics and spray characteristics crucial for efficient combustion. Influence of Nozzle Geometry on Flow Patterns Learn to use CFD results to evaluate how different nozzle designs affect the overall spray formation and fuel distribution patterns. Interpreting Steady-State Simulation Results for Comprehensive Performance Analysis Develop expertise in extracting meaningful insights from your equilibrium simulations: Analyzing Fuel-Air Mixing and Vapor Distribution Master techniques for processing and interpreting CFD data to assess the effectiveness of fuel atomization and vapor formation for various engine operating conditions. Identifying Optimization Opportunities for Injector Design Learn to pinpoint crucial areas in the simulation that reveal potential improvements in injector geometry for enhanced performance and efficiency. Practical Applications and Industry Relevance Connect simulation insights to real-world engineering challenges: Optimizing Fuel Injection Systems for Improved Engine Efficiency Explore how CFD simulations can inform the design and improvement of fuel injectors for better fuel economy and reduced emissions in automotive and aerospace applications. Enhancing Combustion Stability through Precise Fuel Delivery Understand how the principles learned in this module can contribute to the development of more stable and efficient combustion processes in various engine types. Why This Module is Essential for Beginner Multiphase Flow Engineers This beginner-level module offers a practical introduction to advanced CFD techniques in fuel injector system simulation. By completing this simulation, you’ll gain valuable insights into: Fundamental principles of the Mixture approach and its application in modeling complex three-phase flows in high-pressure fuel injection systems Essential CFD techniques for simulating liquid-gas-vapor interactions, phase coupling, and momentum transfer in automotive and aerospace applications Practical applications of Mixture CFD analysis in engine technology, combustion engineering, and propulsion system design By the end of this episode, you’ll have developed crucial skills in: Setting up and running three-phase fuel injector simulations using the Mixture multiphase model in ANSYS Fluent Interpreting steady-state simulation results to assess flow patterns, phase distributions, and spray formation characteristics Applying CFD insights to enhance understanding and design in applications involving multiphase flows in fuel injection systems This knowledge forms a solid foundation for engineers and researchers looking to specialize in engine technology and multiphase flow analysis, providing a springboard for advanced studies in fluid dynamics, combustion processes, and innovative fuel injection technologies. Join us on this exciting journey into the world of fuel injector three-phase flow CFD simulation, and take your first steps towards becoming an expert in multiphase dynamics modeling for critical automotive and aerospace applications!
Episode 1 15m 4s
-
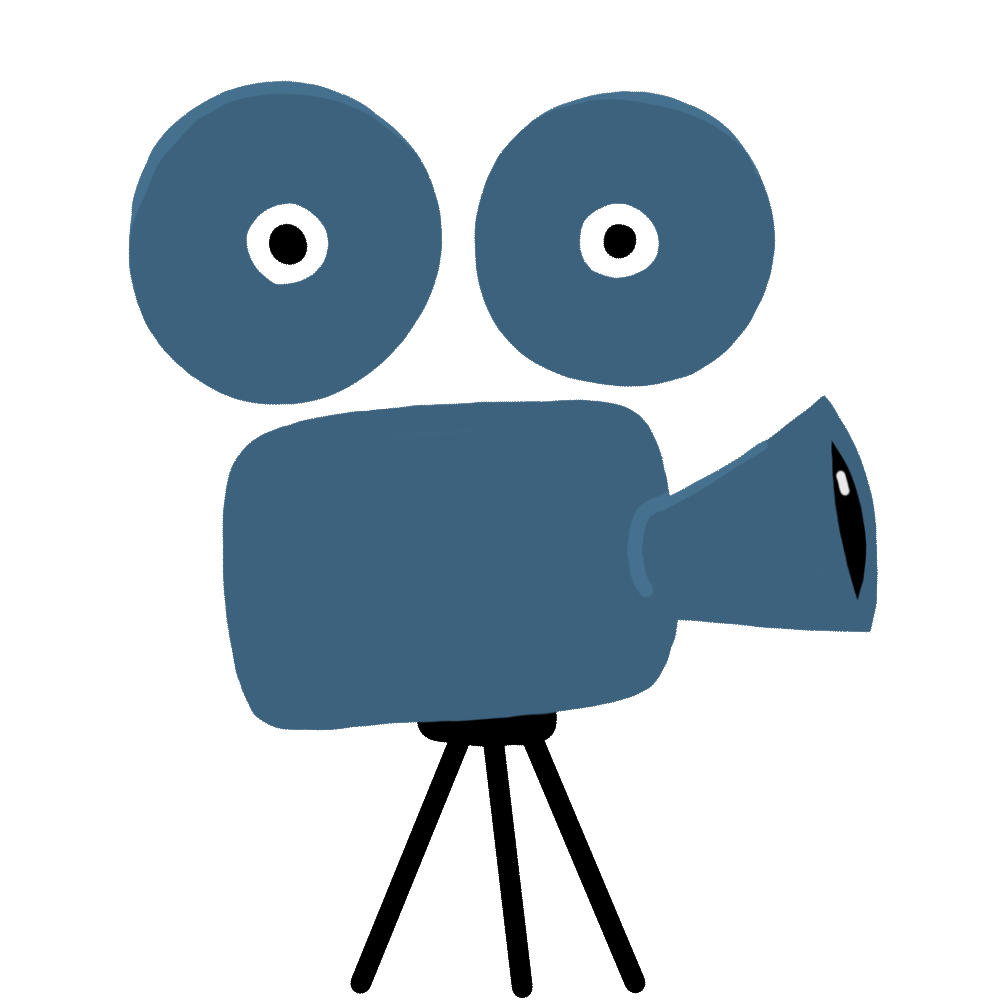
Course In Progress
Course still in development. Check back often for updates.
MULTI-PHASE Flow: BEGINNER - Master CFD Fundamentals with ANSYS Fluent
Embark on your journey into the fascinating world of multiphase Computational Fluid Dynamics (CFD) with our comprehensive “MULTI-PHASE Flow: BEGINNER” course. Designed specifically for newcomers to CFD, this program offers a solid foundation in simulating complex fluid interactions using ANSYS Fluent, an industry-leading software tool.
Through a series of carefully crafted tutorials, you’ll gain hands-on experience with the three primary multiphase models: Volume of Fluid (VOF), Eulerian, and Mixture. This course bridges the gap between theoretical knowledge and practical application, providing you with the skills to tackle real-world engineering challenges involving multiple fluid phases.
Course Structure: Exploring Multiphase CFD Models
Our MULTI-PHASE Flow: BEGINNER course is structured to provide a progressive learning path, introducing you to each multiphase model through practical, real-world examples.
1. Volume of Fluid (VOF) Model
Dive into free surface flows and multi-fluid interactions:
- Simulating shower drain dynamics
- Analyzing droplet behavior and fluid interfaces
- Exploring applications in gas sweetening processes
2. Eulerian Model
Master two-phase flow simulations in various geometries:
- Modeling fluid interactions in complex flow patterns
- Analyzing phase distribution and momentum transfer
- Investigating industrial applications of two-phase flows
3. Mixture Model
Explore advanced multiphase scenarios:
- Simulating three-phase flow in a fuel injector
- Understanding the principles of the mixture model approach
- Analyzing phase interactions in complex engineering systems
Key Features of Our Course
Our MULTI-PHASE Flow: BEGINNER course offers unique advantages for aspiring CFD practitioners:
Hands-on Learning with ANSYS Fluent
Gain practical experience with industry-standard software:
- Step-by-step guidance through simulation setup and execution
- Interactive tutorials for each multiphase model
- Real-time problem-solving and result interpretation
Progressive Learning Path
Tailored for beginners, our course ensures steady skill development:
- Gradual introduction to multiphase CFD concepts
- Increasing complexity of simulations as you progress
- Continuous reinforcement of fundamental principles
Real-World Engineering Applications
Apply your skills to practical scenarios across various industries:
Industrial Process Simulations
Tackle multiphase challenges in manufacturing and chemical processing:
- Gas-liquid interactions in absorption columns
- Particle-fluid dynamics in separation processes
- Multiphase heat transfer in industrial equipment
Environmental and Energy Applications
Explore multiphase CFD in sustainable technologies:
- Simulating oil-water separators for environmental protection
- Analyzing multiphase flows in renewable energy systems
- Modeling atmospheric dispersion of pollutants
Learning Outcomes and Skill Development
By completing our MULTI-PHASE Flow: BEGINNER course, you’ll gain:
Proficiency in Multiphase CFD Techniques
Master the fundamentals of multiphase simulations:
- Setting up and running multiphase models in ANSYS Fluent
- Selecting appropriate models for different multiphase scenarios
- Interpreting and analyzing multiphase CFD results
Problem-Solving Skills for Complex Fluid Flows
Develop the ability to tackle real-world engineering challenges:
- Applying multiphase CFD techniques to various industries
- Optimizing designs involving multiple fluid phases
- Troubleshooting common issues in multiphase simulations
Why Choose Our MULTI-PHASE Flow: BEGINNER Course?
This course offers unparalleled advantages for those starting their journey in multiphase CFD:
- Comprehensive coverage of major multiphase models (VOF, Eulerian, Mixture)
- 10 detailed tutorials spanning diverse engineering applications
- Subscription-based access for continuous learning and skill improvement
- Foundational knowledge applicable across various industries
By enrolling in our MULTI-PHASE Flow: BEGINNER course, you’ll:
- Gain a solid foundation in multiphase CFD simulation techniques
- Develop practical skills directly applicable to engineering challenges
- Enhance your career prospects in CFD-related fields
- Build confidence in tackling complex fluid flow problems
Join us today and take your first steps towards becoming a proficient multiphase CFD practitioner, opening doors to exciting opportunities in engineering and research!
Subscribe
Benefits of subscribing to the course
- Complete access to All chapters
- Special discount
- Free access to all new and updated content
- Cancel subscription anytime
* You will have access to the course only until your subscription ends; after that, your subscription will be automatically renewed unless you cancel it.
Congratulations
Congratulations! You have successfully subscribed to the course.
You can now start learning the course by clicking the button "Start Learning".
You can manage your subscription like canceling or upgrading the subscription, adding or changing the payment method, etc by clicking the button "Manage Subscriptions".
Add Payment Method
Please enter your payment method details.