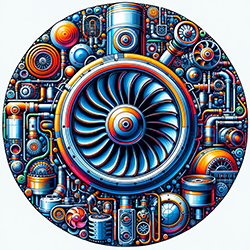
Turbomachinery: ANSYS Fluent CFD Simulation Training Course
Workshop
Price:
$480.00
$149.00
The “Turbomachinery: All Levels” CFD simulation training course is a comprehensive program designed to transform you into a Turbomachinery CFD Simulation expert. This course covers essential concepts and advanced techniques for simulating various turbomachinery systems using ANSYS Fluent. Through five detailed video lessons and a final project, you’ll master frame motion techniques (including Single Reference Frame and Multiple Reference Frame models), mesh motion techniques, and their applications in simulating mixers, wind turbines, and other rotating machinery. You’ll learn to analyze flow fields, extract graphical data, and calculate critical parameters such as lift, drag forces, and power generation. By the end of this course, you’ll have the skills to perform high-fidelity turbomachinery simulations, making you proficient in using ANSYS Fluent for complex rotating system analyses in fields like chemical engineering, mechanical engineering, and renewable energy.
HAWT and VAWT Comparison CFD Simulation
Master Wind Turbine CFD: HAWT vs VAWT Simulation Techniques Dive into the cutting-edge world of wind turbine simulation with our comprehensive tutorial on “HAWT and VAWT Comparison, (Mesh Motion and MRF)”. This pivotal episode in our “Turbomachinery: All Levels” course offers an in-depth exploration of advanced CFD techniques for modeling both Horizontal Axis Wind Turbines (HAWT) and Vertical Axis Wind Turbines (VAWT). Advanced Turbomachinery Simulation: Comparing HAWT and VAWT Unlock the secrets of efficient wind energy harvesting through sophisticated Computational Fluid Dynamics (CFD) simulations. This tutorial provides a detailed comparison of modeling techniques for two distinct wind turbine designs, offering invaluable insights into their unique fluid dynamics. Key Learning Objectives Master advanced CFD techniques for simulating HAWT and VAWT Understand the critical differences in modeling approaches for various turbine designs Develop proficiency in both Mesh Motion and Multiple Reference Frame (MRF) methods Analyze and interpret complex aerodynamic data for wind turbine optimization Comprehensive Simulation Methodologies Learn to set up and execute professional-grade CFD simulations for both HAWT and VAWT, covering all aspects from geometry creation to result analysis. 1. VAWT Simulation: Mesh Motion Technique - Implementing dynamic mesh motion for accurate VAWT modeling - Setting up transient analysis to capture time-dependent phenomena - Configuring interface boundaries between rotating and stationary zones 2. HAWT Simulation: Frame Motion (MRF) Approach - Applying the Multiple Reference Frame technique for HAWT analysis - Configuring steady-state simulations for efficient computation - Understanding the trade-offs between computational speed and temporal accuracy 3. Advanced Performance Analysis - Extracting crucial performance metrics: lift, drag, and moment coefficients - Analyzing power output and efficiency for both turbine types - Comparing the aerodynamic characteristics of HAWT and VAWT designs Real-World Applications and Industry Relevance This tutorial is essential for professionals and researchers in: Renewable energy engineering Wind turbine design and optimization Aerodynamics and fluid dynamics research Sustainable energy systems development Key Simulation Outcomes and Insights 1. Comparative Analysis of HAWT and VAWT - Understand the unique flow patterns around different turbine designs - Evaluate the strengths and limitations of each turbine type 2. Method Selection and Application - Learn when to apply Mesh Motion vs. Frame Motion techniques - Understand the implications of each method on simulation accuracy and computational cost 3. Performance Optimization Strategies - Gain insights into optimizing blade designs for improved efficiency - Understand how different wind conditions affect turbine performance Elevate Your Wind Energy Engineering Skills By completing this advanced tutorial, you’ll gain: Expertise in simulating both HAWT and VAWT using state-of-the-art CFD techniques Proficiency in selecting and applying appropriate simulation methods for different turbine types Deep understanding of the aerodynamic principles governing wind turbine performance Skills to optimize wind turbine designs for enhanced energy harvesting Who Should Take This Advanced Tutorial Wind energy engineers and researchers CFD specialists focusing on renewable energy applications Graduate students in mechanical or aerospace engineering R&D professionals in sustainable energy technologies Don’t miss this opportunity to significantly advance your wind turbine simulation skills and gain a comprehensive understanding of both HAWT and VAWT dynamics. Enroll now in our “Turbomachinery: All Levels” course and master the art of wind turbine CFD simulation using advanced techniques in ANSYS Fluent!
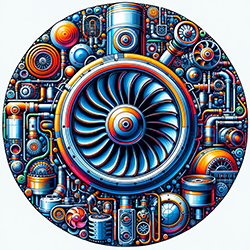
Turbomachinery: ANSYS Fluent CFD Simulation Training Course
Workshop
Price:
$480.00
$149.00
The “Turbomachinery: All Levels” CFD simulation training course is a comprehensive program designed to transform you into a Turbomachinery CFD Simulation expert. This course covers essential concepts and advanced techniques for simulating various turbomachinery systems using ANSYS Fluent. Through five detailed video lessons and a final project, you’ll master frame motion techniques (including Single Reference Frame and Multiple Reference Frame models), mesh motion techniques, and their applications in simulating mixers, wind turbines, and other rotating machinery. You’ll learn to analyze flow fields, extract graphical data, and calculate critical parameters such as lift, drag forces, and power generation. By the end of this course, you’ll have the skills to perform high-fidelity turbomachinery simulations, making you proficient in using ANSYS Fluent for complex rotating system analyses in fields like chemical engineering, mechanical engineering, and renewable energy.
HAWT and VAWT Comparison CFD Simulation
Master Wind Turbine CFD: HAWT vs VAWT Simulation Techniques Dive into the cutting-edge world of wind turbine simulation with our comprehensive tutorial on “HAWT and VAWT Comparison, (Mesh Motion and MRF)”. This pivotal episode in our “Turbomachinery: All Levels” course offers an in-depth exploration of advanced CFD techniques for modeling both Horizontal Axis Wind Turbines (HAWT) and Vertical Axis Wind Turbines (VAWT). Advanced Turbomachinery Simulation: Comparing HAWT and VAWT Unlock the secrets of efficient wind energy harvesting through sophisticated Computational Fluid Dynamics (CFD) simulations. This tutorial provides a detailed comparison of modeling techniques for two distinct wind turbine designs, offering invaluable insights into their unique fluid dynamics. Key Learning Objectives Master advanced CFD techniques for simulating HAWT and VAWT Understand the critical differences in modeling approaches for various turbine designs Develop proficiency in both Mesh Motion and Multiple Reference Frame (MRF) methods Analyze and interpret complex aerodynamic data for wind turbine optimization Comprehensive Simulation Methodologies Learn to set up and execute professional-grade CFD simulations for both HAWT and VAWT, covering all aspects from geometry creation to result analysis. 1. VAWT Simulation: Mesh Motion Technique - Implementing dynamic mesh motion for accurate VAWT modeling - Setting up transient analysis to capture time-dependent phenomena - Configuring interface boundaries between rotating and stationary zones 2. HAWT Simulation: Frame Motion (MRF) Approach - Applying the Multiple Reference Frame technique for HAWT analysis - Configuring steady-state simulations for efficient computation - Understanding the trade-offs between computational speed and temporal accuracy 3. Advanced Performance Analysis - Extracting crucial performance metrics: lift, drag, and moment coefficients - Analyzing power output and efficiency for both turbine types - Comparing the aerodynamic characteristics of HAWT and VAWT designs Real-World Applications and Industry Relevance This tutorial is essential for professionals and researchers in: Renewable energy engineering Wind turbine design and optimization Aerodynamics and fluid dynamics research Sustainable energy systems development Key Simulation Outcomes and Insights 1. Comparative Analysis of HAWT and VAWT - Understand the unique flow patterns around different turbine designs - Evaluate the strengths and limitations of each turbine type 2. Method Selection and Application - Learn when to apply Mesh Motion vs. Frame Motion techniques - Understand the implications of each method on simulation accuracy and computational cost 3. Performance Optimization Strategies - Gain insights into optimizing blade designs for improved efficiency - Understand how different wind conditions affect turbine performance Elevate Your Wind Energy Engineering Skills By completing this advanced tutorial, you’ll gain: Expertise in simulating both HAWT and VAWT using state-of-the-art CFD techniques Proficiency in selecting and applying appropriate simulation methods for different turbine types Deep understanding of the aerodynamic principles governing wind turbine performance Skills to optimize wind turbine designs for enhanced energy harvesting Who Should Take This Advanced Tutorial Wind energy engineers and researchers CFD specialists focusing on renewable energy applications Graduate students in mechanical or aerospace engineering R&D professionals in sustainable energy technologies Don’t miss this opportunity to significantly advance your wind turbine simulation skills and gain a comprehensive understanding of both HAWT and VAWT dynamics. Enroll now in our “Turbomachinery: All Levels” course and master the art of wind turbine CFD simulation using advanced techniques in ANSYS Fluent!
-
Section 1
Concept
-
Mastering Turbomachinery Concepts with ANSYS Fluent: Foundation for CFD Simulation Embark on your journey to become a turbomachinery CFD expert with our comprehensive introductory episode, “Turbomachinery Concepts, ANSYS Fluent”. This foundational module sets the stage for advanced simulations in our “Turbomachinery: All Levels” course, providing you with essential knowledge and techniques used in industry-leading CFD software. Unveiling the World of Turbomachinery Dive deep into the fascinating realm of rotating machinery and fluid dynamics. This episode lays the groundwork for understanding complex turbomachinery systems and their simulation techniques. Key Learning Objectives Grasp fundamental concepts of turbomachinery and rotating frames Understand various simulation techniques available in ANSYS Fluent Compare and contrast different modeling approaches for rotating systems Comprehensive Overview of Simulation Techniques Gain insights into the cutting-edge methods used for turbomachinery simulation in ANSYS Fluent. This episode covers: 1. Frame Motion Techniques - Introduction to the Frame Motion concept - Detailed exploration of Single Reference Frame (SRF) model - In-depth look at Multiple Reference Frame (MRF) approach 2. Mesh Motion Techniques - Understanding the principles of Mesh Motion - Focused study on Sliding Mesh Motion and its applications 3. Comparative Analysis - Critical comparison between Frame Motion and Mesh Motion techniques - Guidance on selecting the appropriate method for specific turbomachinery problems Practical Applications and Industry Relevance This episode is crucial for professionals and students in: Aerospace engineering Power generation systems Turbomachinery design and optimization Advanced CFD analysis Why This Episode is Essential Foundation for Advanced Simulations - Build a solid understanding of core concepts - Prepare for complex turbomachinery simulations in later episodes Industry-Aligned Knowledge - Learn techniques used in real-world engineering applications - Gain insights into best practices in turbomachinery CFD Enhanced Problem-Solving Skills - Develop critical thinking for selecting appropriate simulation methods - Understand the strengths and limitations of different approaches Start Your Journey to Turbomachinery Mastery This episode is your gateway to becoming proficient in turbomachinery CFD simulation. By completing this module, you’ll: Gain confidence in fundamental turbomachinery concepts Understand the range of simulation techniques available in ANSYS Fluent Be prepared for more advanced topics in subsequent episodes Who Should Watch This Episode? Engineering students focusing on fluid dynamics or rotary machinery CFD professionals looking to specialize in turbomachinery Mechanical and aerospace engineers seeking to enhance their simulation skills Researchers in fields related to rotating machinery and fluid dynamics Don’t miss this crucial first step in your turbomachinery CFD journey. Enroll now in our “Turbomachinery: All Levels” course and start with this foundational episode to set yourself up for success in the exciting world of turbomachinery simulation!
Episode 1 12m 6s Free Episode
-
-
Section 2
Single Reference Frames (SRF)
-
Master Mixing Tank Simulation: SRF Method in ANSYS Fluent Dive deep into advanced turbomachinery simulation with our comprehensive tutorial on “SRF Method, Mixing Tank CFD Simulation by ANSYS Fluent”. This crucial episode in our “Turbomachinery: All Levels” course offers hands-on experience in applying the Single Reference Frame (SRF) method to a real-world mixing tank scenario. Practical Application of SRF in Mixing Tank Analysis Experience the power of Computational Fluid Dynamics (CFD) in analyzing complex fluid behaviors within a rotating system. This tutorial provides a step-by-step guide to simulating a closed mixing tank using ANSYS Fluent, a leading industry software for CFD analysis. Key Learning Objectives Master the application of the Single Reference Frame (SRF) method Understand fluid dynamics in rotating systems Gain proficiency in ANSYS Fluent for turbomachinery simulations Analyze and interpret critical flow parameters in mixing tanks Comprehensive Simulation Setup and Methodology Learn to set up and execute a professional-grade CFD simulation for a mixing tank, covering all aspects from geometry creation to result analysis. 1. Geometry and Mesh Generation - Creating 3D models using ANSYS Design Modeler - Implementing effective meshing strategies with ANSYS Meshing - Optimizing mesh quality for accurate results (278,775 unstructured elements) 2. ANSYS Fluent Configuration - Configuring the SRF method for rotational movement simulation - Setting up steady-state analysis with k-ε turbulence model - Defining boundary conditions for a 500 rpm impeller rotation 3. Advanced Analysis Techniques - Extracting and interpreting pressure, velocity, and turbulent intensity contours - Analyzing vortex formation and fluid behavior in rotating systems - Understanding the impact of impeller rotation on fluid dynamics Real-World Applications and Industry Relevance This tutorial is invaluable for professionals and researchers in: Chemical process engineering Mixing and blending technology Wastewater treatment systems Food and beverage industry Key Simulation Outcomes and Insights 1. Pressure Distribution Analysis - Observe pressure variations from tank center to walls - Understand pressure effects on mixing efficiency 2. Velocity Profile Examination - Analyze flow speed patterns across the tank - Correlate velocity distributions with mixing effectiveness 3. Turbulence Intensity Evaluation - Visualize turbulence patterns throughout the mixing tank - Assess the impact of turbulence on mixing performance Elevate Your Turbomachinery Simulation Skills By completing this tutorial, you’ll gain: Practical experience in applying SRF method to real-world problems Proficiency in setting up complex CFD simulations in ANSYS Fluent Skills in analyzing and interpreting fluid dynamics in rotating systems Insights into optimizing mixing tank designs for various applications Who Should Take This Tutorial Process engineers working with mixing and blending equipment CFD specialists focusing on rotating machinery Graduate students in chemical or mechanical engineering R&D professionals in fluid dynamics and mixing technology Don’t miss this opportunity to enhance your CFD simulation skills and deepen your understanding of turbomachinery applications. Enroll now in our “Turbomachinery: All Levels” course and master the art of mixing tank simulation using the SRF method in ANSYS Fluent!
Episode 1 16m 11s
-
-
Section 3
Multiple Reference Frames (MRF)
-
Advanced Mixing Tank CFD: Mastering the MRF Method in ANSYS Fluent Elevate your turbomachinery simulation skills with our in-depth tutorial on “MRF Method, Mixing Tank CFD Simulation by ANSYS Fluent”. This essential episode in our “Turbomachinery: All Levels” course offers a comprehensive guide to applying the Multiple Reference Frame (MRF) method in complex mixing tank scenarios. Cutting-Edge Simulation Techniques for Rotating Machinery Delve into the world of advanced Computational Fluid Dynamics (CFD) as we explore the intricacies of simulating a mixing tank using the MRF method. This tutorial provides a step-by-step approach to modeling complex fluid behaviors in rotating systems using ANSYS Fluent, an industry-leading CFD software. Key Learning Objectives Master the application of the Multiple Reference Frame (MRF) method Understand fluid dynamics in multi-zone rotating systems Develop proficiency in ANSYS Fluent for advanced turbomachinery simulations Analyze and interpret critical flow parameters in complex mixing scenarios Comprehensive Simulation Workflow and Methodology Learn to set up and execute a professional-grade CFD simulation for a mixing tank, covering all aspects from geometry creation to result interpretation. 1. Advanced Geometry and Mesh Generation - Creating detailed 3D models using ANSYS Design Modeler - Implementing sophisticated meshing strategies with ANSYS Meshing - Optimizing mesh quality for high-fidelity results (229,177 unstructured elements) 2. ANSYS Fluent Setup for MRF Simulation - Configuring multiple zones for the MRF method - Setting up steady-state analysis with k-ε turbulence model - Defining boundary conditions for a 500 rpm impeller rotation in a stationary tank 3. Advanced Analysis and Visualization Techniques - Extracting and interpreting pressure, velocity, and turbulent intensity contours - Analyzing vortex formation and fluid behavior in multi-zone systems - Understanding the impact of impeller rotation on fluid dynamics across different zones Real-World Applications and Industry Relevance This tutorial is crucial for professionals and researchers in: Chemical and process engineering Pharmaceutical mixing processes Food and beverage industry Wastewater treatment and environmental engineering Key Simulation Outcomes and Insights 1. Pressure Distribution Analysis - Observe pressure variations around the impeller - Understand pressure effects on mixing efficiency in different zones 2. Velocity Profile Examination - Analyze flow speed patterns, particularly behind the impeller - Correlate velocity distributions with mixing effectiveness in rotating and stationary zones 3. Turbulence Intensity Evaluation - Visualize turbulence patterns throughout the mixing tank, especially near the impeller - Assess the impact of turbulence on mixing performance in different regions 4. Vector Flow Analysis - Examine water flow vectors around the impeller - Understand vortex formation and its impact on mixing efficiency Enhance Your Turbomachinery Simulation Expertise By completing this tutorial, you’ll gain: Advanced skills in applying the MRF method to complex rotating machinery problems Proficiency in setting up and analyzing multi-zone CFD simulations in ANSYS Fluent Deep understanding of fluid dynamics in mixing tanks with rotating impellers Insights into optimizing mixing processes for various industrial applications Who Should Take This Tutorial Process engineers specializing in mixing and blending technologies CFD specialists focusing on complex rotating machinery Graduate students in chemical, mechanical, or environmental engineering R&D professionals in fluid dynamics and industrial mixing processes Don’t miss this opportunity to advance your CFD simulation skills and gain a deeper understanding of complex turbomachinery applications. Enroll now in our “Turbomachinery: All Levels” course and master the art of mixing tank simulation using the MRF method in ANSYS Fluent!
Episode 1 43m 21s
-
-
Section 4
Mesh Motion (Moving Mesh)
-
Master Dynamic Mixing Tank Simulation: Mesh Motion Method in ANSYS Fluent Unlock the power of advanced turbomachinery simulation with our comprehensive tutorial on “Mesh Motion Method, Mixing Tank CFD Simulation ANSYS Fluent”. This pivotal episode in our “Turbomachinery: All Levels” course offers an in-depth exploration of dynamic fluid behavior modeling using the sophisticated Mesh Motion technique. Cutting-Edge Dynamic Simulation for Rotating Systems Immerse yourself in the world of high-fidelity Computational Fluid Dynamics (CFD) as we delve into the intricacies of simulating a mixing tank using the Mesh Motion method. This tutorial provides a detailed, step-by-step approach to modeling complex, time-dependent fluid behaviors in rotating systems using ANSYS Fluent, a leading industry-standard CFD software. Key Learning Objectives Master the application of the Mesh Motion method for dynamic simulations Understand transient fluid dynamics in multi-zone rotating systems Develop advanced proficiency in ANSYS Fluent for complex turbomachinery simulations Analyze and interpret time-dependent flow parameters in mixing scenarios Comprehensive Simulation Setup and Methodology Learn to configure and execute a professional-grade, time-dependent CFD simulation for a mixing tank, covering all aspects from geometry creation to transient result analysis. 1. Advanced 3D Geometry and Mesh Generation - Creating detailed 3D models optimized for dynamic simulation using ANSYS Design Modeler - Implementing sophisticated meshing strategies with ANSYS Meshing for moving parts - Optimizing mesh quality for high-fidelity, time-accurate results (209,328 unstructured elements) 2. ANSYS Fluent Configuration for Mesh Motion Simulation - Setting up multiple zones with interfaces for the Mesh Motion method - Configuring unsteady analysis with the k-ε turbulence model - Defining dynamic boundary conditions for a 500 rpm impeller rotation 3. Advanced Transient Analysis Techniques - Extracting and interpreting time-dependent pressure, velocity, and turbulent intensity contours - Analyzing dynamic vortex formation and fluid behavior in rotating systems - Understanding the temporal evolution of mixing processes Real-World Applications and Industry Relevance This tutorial is essential for professionals and researchers in: Chemical process engineering and design Pharmaceutical mixing and blending processes Food and beverage industry innovations Advanced wastewater treatment systems Key Simulation Outcomes and Dynamic Insights 1. Time-Dependent Pressure Distribution Analysis - Observe dynamic pressure variations around the rotating impeller - Understand the transient effects of pressure on mixing efficiency 2. Velocity Profile Evolution - Analyze time-varying flow speed patterns, particularly in the wake of the impeller - Correlate dynamic velocity distributions with mixing effectiveness 3. Turbulence Intensity Fluctuations - Visualize the temporal evolution of turbulence patterns throughout the mixing tank - Assess the impact of time-varying turbulence on overall mixing performance Elevate Your Turbomachinery Simulation Expertise By completing this advanced tutorial, you’ll gain: Cutting-edge skills in applying the Mesh Motion method to complex, time-dependent rotating machinery problems Proficiency in setting up and analyzing dynamic, multi-zone CFD simulations in ANSYS Fluent Deep understanding of transient fluid dynamics in mixing tanks with rotating impellers Insights into optimizing mixing processes for various industrial applications using time-accurate simulations Who Should Take This Advanced Tutorial Senior process engineers specializing in complex mixing technologies CFD specialists focusing on dynamic simulations of rotating machinery Doctoral students in chemical, mechanical, or process engineering R&D professionals in advanced fluid dynamics and industrial mixing processes Seize this opportunity to significantly advance your CFD simulation skills and gain a profound understanding of dynamic turbomachinery applications. Enroll now in our “Turbomachinery: All Levels” course and master the art of time-dependent mixing tank simulation using the Mesh Motion method in ANSYS Fluent!
Episode 1 19m 12s
-
-
Section 5
Mesh Motion Vs. MRF
-
Master Wind Turbine CFD: HAWT vs VAWT Simulation Techniques Dive into the cutting-edge world of wind turbine simulation with our comprehensive tutorial on “HAWT and VAWT Comparison, (Mesh Motion and MRF)”. This pivotal episode in our “Turbomachinery: All Levels” course offers an in-depth exploration of advanced CFD techniques for modeling both Horizontal Axis Wind Turbines (HAWT) and Vertical Axis Wind Turbines (VAWT). Advanced Turbomachinery Simulation: Comparing HAWT and VAWT Unlock the secrets of efficient wind energy harvesting through sophisticated Computational Fluid Dynamics (CFD) simulations. This tutorial provides a detailed comparison of modeling techniques for two distinct wind turbine designs, offering invaluable insights into their unique fluid dynamics. Key Learning Objectives Master advanced CFD techniques for simulating HAWT and VAWT Understand the critical differences in modeling approaches for various turbine designs Develop proficiency in both Mesh Motion and Multiple Reference Frame (MRF) methods Analyze and interpret complex aerodynamic data for wind turbine optimization Comprehensive Simulation Methodologies Learn to set up and execute professional-grade CFD simulations for both HAWT and VAWT, covering all aspects from geometry creation to result analysis. 1. VAWT Simulation: Mesh Motion Technique - Implementing dynamic mesh motion for accurate VAWT modeling - Setting up transient analysis to capture time-dependent phenomena - Configuring interface boundaries between rotating and stationary zones 2. HAWT Simulation: Frame Motion (MRF) Approach - Applying the Multiple Reference Frame technique for HAWT analysis - Configuring steady-state simulations for efficient computation - Understanding the trade-offs between computational speed and temporal accuracy 3. Advanced Performance Analysis - Extracting crucial performance metrics: lift, drag, and moment coefficients - Analyzing power output and efficiency for both turbine types - Comparing the aerodynamic characteristics of HAWT and VAWT designs Real-World Applications and Industry Relevance This tutorial is essential for professionals and researchers in: Renewable energy engineering Wind turbine design and optimization Aerodynamics and fluid dynamics research Sustainable energy systems development Key Simulation Outcomes and Insights 1. Comparative Analysis of HAWT and VAWT - Understand the unique flow patterns around different turbine designs - Evaluate the strengths and limitations of each turbine type 2. Method Selection and Application - Learn when to apply Mesh Motion vs. Frame Motion techniques - Understand the implications of each method on simulation accuracy and computational cost 3. Performance Optimization Strategies - Gain insights into optimizing blade designs for improved efficiency - Understand how different wind conditions affect turbine performance Elevate Your Wind Energy Engineering Skills By completing this advanced tutorial, you’ll gain: Expertise in simulating both HAWT and VAWT using state-of-the-art CFD techniques Proficiency in selecting and applying appropriate simulation methods for different turbine types Deep understanding of the aerodynamic principles governing wind turbine performance Skills to optimize wind turbine designs for enhanced energy harvesting Who Should Take This Advanced Tutorial Wind energy engineers and researchers CFD specialists focusing on renewable energy applications Graduate students in mechanical or aerospace engineering R&D professionals in sustainable energy technologies Don’t miss this opportunity to significantly advance your wind turbine simulation skills and gain a comprehensive understanding of both HAWT and VAWT dynamics. Enroll now in our “Turbomachinery: All Levels” course and master the art of wind turbine CFD simulation using advanced techniques in ANSYS Fluent!
Episode 1 25m 43s
-
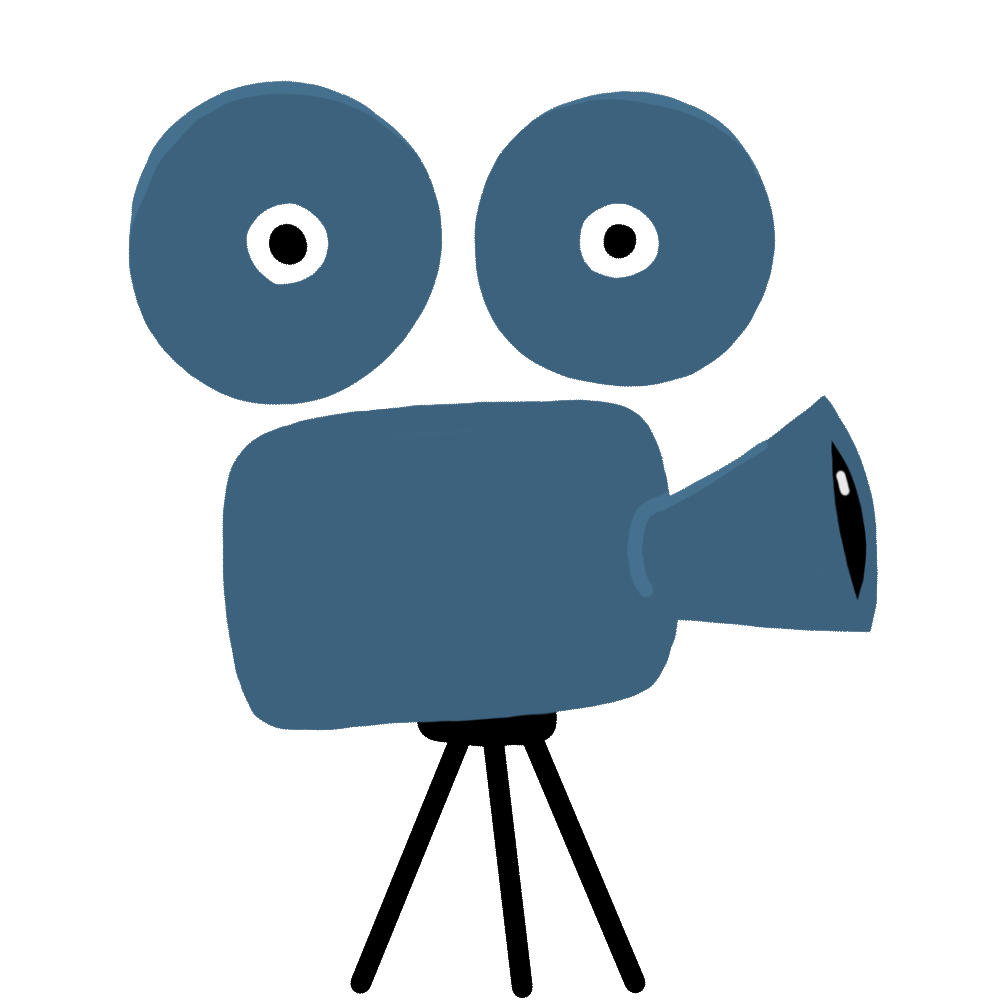
Course In Progress
Course still in development. Check back often for updates.
Master Turbomachinery CFD Simulation: Comprehensive ANSYS Fluent Training
Elevate your engineering skills with our “Turbomachinery: All Levels” course, designed to transform you into a Turbomachinery CFD Simulation expert. This comprehensive program covers everything from basic principles to advanced techniques in simulating rotating machinery using ANSYS Fluent.
Course Overview: Unlocking the Power of Turbomachinery Simulation
Turbomachinery is at the heart of many engineering applications, from power generation to aerospace. This course provides in-depth knowledge on simulating these complex systems, focusing on energy transfer between rotors and fluids.
Key Learning Objectives
- Master various turbomachinery simulation techniques in ANSYS Fluent
- Understand and apply Frame Motion and Mesh Motion models
- Analyze flow fields, forces, and energy transfer in rotating systems
- Develop skills to design and optimize turbomachines using CFD
Course Structure: From Fundamentals to Advanced Applications
Our carefully structured curriculum ensures a progressive learning experience, covering all aspects of turbomachinery simulation.
Lesson 1: Foundations of Turbomachinery Simulation
- Introduction to rotating frames and simulation techniques - Detailed exploration of Frame Motion and Mesh Motion models - Comparative analysis of different simulation approaches
Lesson 2: Single Reference Frame (SRF) Model
- Practical application of SRF in mixer flow field analysis - Essential setup and settings for accurate simulations - Techniques for extracting and interpreting graphical data
Lesson 3: Multiple Reference Frame (MRF) Model
- Advanced geometry creation and mesh generation for MRF - Utilizing the "Form part" option for complex geometries - In-depth data analysis and visualization techniques
Lesson 4: Mesh Motion Model
- Mastering mesh generation for dynamic simulations - Understanding and implementing interfaces in rotating systems - Best practices for time step selection in transient analyses
Lesson 5: Real-World Applications
- Simulating Horizontal Axis Wind Turbines (HAWT) using MRF - Analyzing Vertical Axis Wind Turbines (VAWT) with Mesh Motion - Generating comprehensive reports on lift, drag, and power output
Why Choose Our Turbomachinery Course?
Practical, Hands-On Learning
- Step-by-step tutorials using real-world examples - Focus on industry-relevant skills and techniques
Comprehensive Coverage
- From basic concepts to advanced simulation strategies - Applicable to various turbomachinery types: turbines, compressors, fans, and more
Expert Instruction
- Learn from experienced CFD professionals - Gain insights into industry best practices and common pitfalls
Who Should Enroll?
This course is ideal for:
- Mechanical and aerospace engineers
- CFD specialists and researchers
- Graduate students in engineering disciplines
- Professionals in power generation and HVAC industries
Course Outcomes and Career Benefits
Upon completion, you’ll be able to:
- Conduct high-fidelity turbomachinery simulations using ANSYS Fluent
- Optimize designs for various rotating machinery applications
- Analyze and interpret complex CFD results for turbomachinery
- Apply your skills to real-world engineering challenges in multiple industries
Become a Turbomachinery CFD Expert Today!
Enroll now in our “Turbomachinery: All Levels” course and take your engineering career to new heights. With our comprehensive training, you’ll gain the skills and confidence to tackle complex turbomachinery simulations and stand out in the competitive field of CFD analysis.
Don’t miss this opportunity to transform your career. Join us and master the art and science of turbomachinery simulation with ANSYS Fluent!
Buy Course
Benefits of buying the whole course
- Complete access to chapters Without Price
- Special discount
- Unlimited access to course content
- Free access to all new and updated content
- Access to course forever without any additional payment
* You can select chapters seperately, but you won't benefit from the list above.
* The items that do not have a price cannot be bought separately and are only available when you buy the whole course.
Congratulations
Congratulations! Your purchase was successful.
You can now start learning the course by clicking the button "Start Learning".
Add Payment Method
Please enter your payment method details.