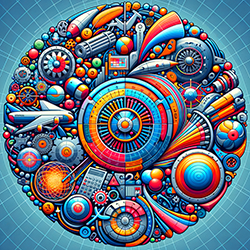
Mechanical, Advanced: CFD Simulation Training Course
Course Price: $6.00 / Month
Master advanced CFD techniques with ANSYS Fluent in this comprehensive course designed for experienced users. Explore complex Multiphysics simulations crucial to mechanical engineering, including multiphase flows, moving boundaries, porous media, discrete particle modeling, and compressible flows. Through ten carefully crafted modules, you’ll tackle real-world challenges such as Eulerian two-phase flows, pigging operations, fuel injection, turbomachinery, and supersonic nozzles. Enhance your ability to simulate, analyze, and optimize sophisticated fluid systems, elevating your expertise in computational fluid dynamics for cutting-edge mechanical engineering applications.
By enrolling in this course, you will also gain access to the following courses for free:
Supersonic Nozzle Flow Separation and Shock Wave CFD Simulation
Mastering Supersonic Nozzle Dynamics: Advanced CFD Simulation for Mechanical Engineers Welcome to the “Supersonic Nozzle Flow Separation and Shock Wave CFD Simulation” episode of our “MECHANICAL Engineers: ADVANCED” course. This comprehensive module delves into the complex world of supersonic nozzle flow, focusing on the intricate phenomena of flow separation and shock wave formation using cutting-edge CFD techniques. Compressible Flow Modeling in Supersonic Regimes Before diving into the simulation specifics, we’ll explore the fundamental concepts of compressible flow modeling in supersonic conditions. Governing Equations for High-Speed Flows Discover advanced techniques for implementing and solving the governing equations of compressible flow in supersonic regimes using ANSYS Fluent. Turbulence Modeling for Supersonic Flows Learn to select and implement appropriate turbulence models for accurate simulation of high-speed flows in supersonic nozzles, considering shock-turbulence interactions. Shock Wave Formation and Propagation Analysis This section focuses on the critical aspects of shock wave dynamics within supersonic nozzles: Normal Shock Wave Capture Techniques Master the process of simulating and analyzing normal shock waves in supersonic nozzles, including their formation and propagation. Oblique Shock Wave Modeling in Overexpanded Nozzles Gain skills in investigating oblique shock wave structures and their interaction with nozzle walls under various operating conditions. Boundary Layer Separation in Adverse Pressure Gradients Dive deep into the mechanisms of flow separation in supersonic nozzles: Boundary Layer Behavior in Supersonic Flows Learn to model and analyze boundary layer development and behavior in high-speed nozzle flows, including the effects of compressibility. Separation Point Prediction Methods Explore techniques to accurately predict and analyze flow separation points in supersonic nozzles under various pressure ratios. Nozzle Performance Analysis Under Various Operating Conditions In this section, we’ll delve into the detailed performance characteristics of supersonic nozzles: Thrust Coefficient Calculation Techniques Master the process of computing and interpreting thrust coefficients for supersonic nozzles under design and off-design conditions. Nozzle Efficiency Evaluation Methods Develop strategies to assess and optimize nozzle efficiency, considering factors such as flow separation and shock wave losses. Mach Number Distribution Along the Nozzle Explore the critical Mach number variations within supersonic nozzles: Subsonic-to-Supersonic Transition Analysis Learn to simulate and visualize the transition from subsonic to supersonic flow in converging-diverging nozzles. Mach Number Contour Interpretation Discover techniques to generate and analyze Mach number contours, providing insights into flow acceleration and shock formation. Pressure and Temperature Variations Across Shocks Examine the thermodynamic changes associated with shock waves: Pressure Jump Conditions Across Shocks Explore methods for quantifying and visualizing pressure discontinuities across normal and oblique shock waves in nozzle flows. Temperature Rise Prediction in Shock Regions Learn to predict and analyze temperature increases due to shock compression, crucial for material selection and thermal management in nozzle design. Impact of Back Pressure on Nozzle Flow Characteristics Analyze the effects of varying exit conditions on nozzle performance: Flow Adaptation to Changing Back Pressures Develop skills in simulating nozzle flow behavior under varying back pressure conditions, from overexpanded to underexpanded regimes. Hysteresis Effects in Nozzle Flow Patterns Explore the phenomena of flow pattern hysteresis in supersonic nozzles as back pressure is varied, and its implications for nozzle operation. Practical Applications and Industry Relevance Connect simulation insights to real-world engineering challenges: Rocket Engine Nozzle Optimization Explore how CFD simulations of supersonic nozzles contribute to the design and optimization of rocket propulsion systems. Supersonic Wind Tunnel Design Discover the relevance of this technology in developing efficient supersonic wind tunnels for aerospace testing and research. Advanced Result Interpretation and Performance Analysis Elevate your CFD skills with sophisticated data analysis techniques: Shock Structure Visualization Methods Learn advanced techniques for visualizing complex shock structures in supersonic nozzles, including shock diamonds and interaction patterns. Parametric Studies for Nozzle Shape Optimization Develop strategies to conduct parametric studies for optimizing nozzle contours to enhance performance across a range of operating conditions. Why This Module is Essential for Advanced Mechanical Engineers This advanced module offers a deep dive into the sophisticated world of supersonic nozzle dynamics using state-of-the-art CFD techniques. By mastering this simulation, you’ll gain invaluable insights into: Advanced CFD methods for modeling complex compressible flows and shock phenomena in supersonic nozzles The intricate relationships between nozzle geometry, operating conditions, and flow separation characteristics Practical applications of CFD in aerospace propulsion, rocket engine design, and high-speed aerodynamics By the end of this episode, you’ll have enhanced your skills in: Modeling and analyzing advanced supersonic nozzle scenarios in ANSYS Fluent Interpreting complex CFD results to optimize nozzle designs for various aerospace and propulsion applications Applying cutting-edge fluid dynamics concepts to real-world engineering challenges in high-speed flow systems This knowledge will elevate your capabilities as a mechanical engineer, enabling you to contribute to innovative solutions in fields where understanding and optimizing supersonic nozzle performance is critical. Join us on this advanced journey into the world of supersonic nozzle CFD simulation, and position yourself at the forefront of mechanical engineering technology in propulsion system design and high-speed aerodynamics!
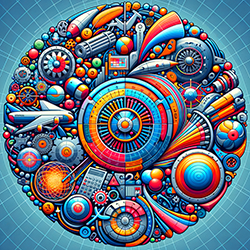
Mechanical, Advanced: CFD Simulation Training Course
Course Price: $6.00 / Month
Master advanced CFD techniques with ANSYS Fluent in this comprehensive course designed for experienced users. Explore complex Multiphysics simulations crucial to mechanical engineering, including multiphase flows, moving boundaries, porous media, discrete particle modeling, and compressible flows. Through ten carefully crafted modules, you’ll tackle real-world challenges such as Eulerian two-phase flows, pigging operations, fuel injection, turbomachinery, and supersonic nozzles. Enhance your ability to simulate, analyze, and optimize sophisticated fluid systems, elevating your expertise in computational fluid dynamics for cutting-edge mechanical engineering applications.
Supersonic Nozzle Flow Separation and Shock Wave CFD Simulation
Mastering Supersonic Nozzle Dynamics: Advanced CFD Simulation for Mechanical Engineers Welcome to the “Supersonic Nozzle Flow Separation and Shock Wave CFD Simulation” episode of our “MECHANICAL Engineers: ADVANCED” course. This comprehensive module delves into the complex world of supersonic nozzle flow, focusing on the intricate phenomena of flow separation and shock wave formation using cutting-edge CFD techniques. Compressible Flow Modeling in Supersonic Regimes Before diving into the simulation specifics, we’ll explore the fundamental concepts of compressible flow modeling in supersonic conditions. Governing Equations for High-Speed Flows Discover advanced techniques for implementing and solving the governing equations of compressible flow in supersonic regimes using ANSYS Fluent. Turbulence Modeling for Supersonic Flows Learn to select and implement appropriate turbulence models for accurate simulation of high-speed flows in supersonic nozzles, considering shock-turbulence interactions. Shock Wave Formation and Propagation Analysis This section focuses on the critical aspects of shock wave dynamics within supersonic nozzles: Normal Shock Wave Capture Techniques Master the process of simulating and analyzing normal shock waves in supersonic nozzles, including their formation and propagation. Oblique Shock Wave Modeling in Overexpanded Nozzles Gain skills in investigating oblique shock wave structures and their interaction with nozzle walls under various operating conditions. Boundary Layer Separation in Adverse Pressure Gradients Dive deep into the mechanisms of flow separation in supersonic nozzles: Boundary Layer Behavior in Supersonic Flows Learn to model and analyze boundary layer development and behavior in high-speed nozzle flows, including the effects of compressibility. Separation Point Prediction Methods Explore techniques to accurately predict and analyze flow separation points in supersonic nozzles under various pressure ratios. Nozzle Performance Analysis Under Various Operating Conditions In this section, we’ll delve into the detailed performance characteristics of supersonic nozzles: Thrust Coefficient Calculation Techniques Master the process of computing and interpreting thrust coefficients for supersonic nozzles under design and off-design conditions. Nozzle Efficiency Evaluation Methods Develop strategies to assess and optimize nozzle efficiency, considering factors such as flow separation and shock wave losses. Mach Number Distribution Along the Nozzle Explore the critical Mach number variations within supersonic nozzles: Subsonic-to-Supersonic Transition Analysis Learn to simulate and visualize the transition from subsonic to supersonic flow in converging-diverging nozzles. Mach Number Contour Interpretation Discover techniques to generate and analyze Mach number contours, providing insights into flow acceleration and shock formation. Pressure and Temperature Variations Across Shocks Examine the thermodynamic changes associated with shock waves: Pressure Jump Conditions Across Shocks Explore methods for quantifying and visualizing pressure discontinuities across normal and oblique shock waves in nozzle flows. Temperature Rise Prediction in Shock Regions Learn to predict and analyze temperature increases due to shock compression, crucial for material selection and thermal management in nozzle design. Impact of Back Pressure on Nozzle Flow Characteristics Analyze the effects of varying exit conditions on nozzle performance: Flow Adaptation to Changing Back Pressures Develop skills in simulating nozzle flow behavior under varying back pressure conditions, from overexpanded to underexpanded regimes. Hysteresis Effects in Nozzle Flow Patterns Explore the phenomena of flow pattern hysteresis in supersonic nozzles as back pressure is varied, and its implications for nozzle operation. Practical Applications and Industry Relevance Connect simulation insights to real-world engineering challenges: Rocket Engine Nozzle Optimization Explore how CFD simulations of supersonic nozzles contribute to the design and optimization of rocket propulsion systems. Supersonic Wind Tunnel Design Discover the relevance of this technology in developing efficient supersonic wind tunnels for aerospace testing and research. Advanced Result Interpretation and Performance Analysis Elevate your CFD skills with sophisticated data analysis techniques: Shock Structure Visualization Methods Learn advanced techniques for visualizing complex shock structures in supersonic nozzles, including shock diamonds and interaction patterns. Parametric Studies for Nozzle Shape Optimization Develop strategies to conduct parametric studies for optimizing nozzle contours to enhance performance across a range of operating conditions. Why This Module is Essential for Advanced Mechanical Engineers This advanced module offers a deep dive into the sophisticated world of supersonic nozzle dynamics using state-of-the-art CFD techniques. By mastering this simulation, you’ll gain invaluable insights into: Advanced CFD methods for modeling complex compressible flows and shock phenomena in supersonic nozzles The intricate relationships between nozzle geometry, operating conditions, and flow separation characteristics Practical applications of CFD in aerospace propulsion, rocket engine design, and high-speed aerodynamics By the end of this episode, you’ll have enhanced your skills in: Modeling and analyzing advanced supersonic nozzle scenarios in ANSYS Fluent Interpreting complex CFD results to optimize nozzle designs for various aerospace and propulsion applications Applying cutting-edge fluid dynamics concepts to real-world engineering challenges in high-speed flow systems This knowledge will elevate your capabilities as a mechanical engineer, enabling you to contribute to innovative solutions in fields where understanding and optimizing supersonic nozzle performance is critical. Join us on this advanced journey into the world of supersonic nozzle CFD simulation, and position yourself at the forefront of mechanical engineering technology in propulsion system design and high-speed aerodynamics!
-
Section 1
Porosity
-
Mastering Porous Media Flow Dynamics: Advanced CFD Simulation Techniques for Mechanical Engineers Welcome to the “Flow Behavior Passing Through a Porous Medium CFD Simulation” episode of our “MECHANICAL Engineers: ADVANCED” course. This comprehensive module delves into the intricate world of fluid dynamics within porous structures, using ANSYS Fluent to explore complex flow phenomena crucial for numerous mechanical engineering applications. Advanced Porous Media Modeling in ANSYS Fluent Before diving into the simulation, we’ll explore the fundamental concepts and implementation techniques for porous media in CFD. Porosity and Permeability Parameter Setup Discover how to accurately define and implement porosity and permeability parameters in ANSYS Fluent for various porous materials. Inertial Resistance Factor Calibration Learn advanced techniques for calibrating inertial resistance factors to match experimental data and improve simulation accuracy. Darcy's Law and Its Extensions in CFD Applications This section focuses on the theoretical foundations of porous media flow and their numerical representation: Implementing Darcy's Law in ANSYS Fluent Master methods for incorporating Darcy’s law into your CFD simulations for low Reynolds number flows through porous media. Forchheimer's Extension for High-Velocity Flows Gain skills in applying Forchheimer’s extension to account for inertial effects in high-velocity porous media flows. Pressure Drop Analysis in Porous Structures Dive deep into the critical relationship between flow rates and pressure gradients: Pressure Gradient Visualization Techniques Learn to simulate and visualize pressure gradients across complex porous geometries using advanced post-processing tools. Optimizing Porous Media Design for Pressure Drop Reduction Explore strategies to optimize porous structure designs to minimize pressure drop while maintaining desired flow characteristics. Velocity Distribution in and Around Porous Regions Examine the intricate flow patterns within porous media: Velocity Profile Analysis Techniques Develop skills in simulating and interpreting velocity profiles within porous structures and in transition regions. Boundary Layer Effects in Porous Media Learn techniques to analyze boundary layer development and its impact on overall flow behavior in porous systems. Multiphase Flow Simulation in Porous Media In this section, we’ll delve into the complexities of simulating multiple fluid phases within porous structures: Two-Phase Flow Modeling in Porous Media Master the process of setting up and simulating two-phase flows (e.g., oil-water) in porous media using ANSYS Fluent. Capillary Pressure Effects in Multiphase Porous Flow Develop methods to incorporate and analyze capillary pressure effects in multiphase porous media simulations. Practical Applications and Industry Relevance Connect simulation insights to real-world engineering challenges: Filtration System Design Optimization Explore how porous media simulations can improve the efficiency and performance of industrial filtration systems. Oil and Gas Reservoir Engineering Discover the relevance of this technology in predicting and optimizing oil and gas extraction from porous reservoirs. Advanced Result Interpretation and Performance Analysis Elevate your CFD skills with sophisticated data analysis techniques: Porous Media Performance Metrics Calculation Learn to compute and interpret key performance indicators such as effective permeability and tortuosity from simulation results. Sensitivity Analysis for Porous Media Parameters Develop strategies to conduct sensitivity analyses to understand the impact of various porous media parameters on flow behavior. Why This Module is Crucial for Advanced Mechanical Engineers This advanced module offers a deep dive into the sophisticated world of porous media flow dynamics using ANSYS Fluent. By mastering this simulation, you’ll gain invaluable insights into: Advanced CFD techniques for modeling complex flow phenomena in porous structures The intricate relationships between porous media properties and fluid flow behavior Practical applications of CFD in diverse fields such as environmental engineering, energy systems, and biomedical device design By the end of this episode, you’ll have enhanced your skills in: Modeling and analyzing advanced porous media flow scenarios in ANSYS Fluent Interpreting complex CFD results to optimize porous system designs for various applications Applying cutting-edge fluid dynamics concepts to real-world engineering challenges involving porous materials This knowledge will elevate your capabilities as a mechanical engineer, enabling you to contribute to innovative solutions in fields where understanding and controlling flow through porous structures is critical. Join us on this advanced journey into the world of porous media flow CFD simulation with ANSYS Fluent, and position yourself at the forefront of mechanical engineering technology!
Episode 1 13m 39s Free Episode -
This advanced-level episode explores the intricate world of porous media flow simulation, focusing on a perforated plate within a 3D channel using Computational Fluid Dynamics (CFD). Participants will delve into the complexities of modeling fluid flow through porous materials, a crucial aspect in various mechanical engineering applications. Key topics: Introduction to porous media flow and its significance in mechanical engineering Overview of perforated plate applications in industry (e.g., heat exchangers, filters, acoustic panels) Setting up the 3D channel geometry with an embedded perforated plate in CFD software Defining porous zone parameters and properties for the perforated plate Implementing appropriate turbulence models for porous media flow Configuring boundary conditions for the 3D channel with porous zone Running the simulation and ensuring convergence Analyzing flow patterns and pressure drop across the perforated plate Visualizing velocity and pressure fields in the 3D channel Interpreting the impact of the porous zone on overall flow characteristics By completing this episode, participants will gain advanced knowledge in simulating fluid flow through porous materials using CFD techniques. This understanding is essential for designing and optimizing various mechanical systems involving perforated or porous elements. Participants will enhance their skills in advanced CFD modeling, enabling them to tackle complex flow problems in their mechanical engineering projects and research related to porous media applications.
Episode 2 10m 47s
-
-
Section 2
Tank Charge-Discharge
-
Mastering Rotating Tank Dynamics: Advanced CFD Simulation of Water Discharge Phenomena Welcome to the “Water Discharge of a Rotating Tank CFD Simulation” episode of our “MECHANICAL Engineers: ADVANCED” course. This comprehensive module delves into the complex world of fluid dynamics in rotating systems, using ANSYS Fluent to explore the intricate behavior of water discharge from a rotating tank, a critical phenomenon in various mechanical engineering applications. Multiphase Flow Modeling in Rotating Systems Before diving into the simulation specifics, we’ll explore the fundamental concepts of multiphase flow modeling in the context of rotating tanks. Air-Water Interface Capture Techniques Discover advanced methods for accurately modeling and tracking the air-water interface in a rotating environment using ANSYS Fluent. Volume of Fluid (VOF) Method Implementation Learn to implement and optimize the VOF method for precise free surface tracking in rotating tank simulations. Rotating Reference Frame: Setup and Analysis This section focuses on the critical aspect of implementing a rotating reference frame in CFD simulations: Rotating Domain Configuration in ANSYS Fluent Master the process of setting up and configuring rotating fluid domains to accurately represent tank rotation. Centrifugal and Coriolis Effects Analysis Gain skills in analyzing and interpreting the impact of centrifugal and Coriolis forces on fluid behavior within the rotating tank. Free Surface Flow Dynamics in Rotating Tanks Dive deep into the complexities of free surface behavior under rotational forces: Vortex Formation and Evolution Learn to simulate and visualize vortex formation processes and their influence on tank discharge characteristics. Surface Wave Patterns and Instabilities Explore techniques to analyze surface wave patterns and potential instabilities in rotating free surface flows. Transient Analysis of the Discharge Process Examine the time-dependent nature of water discharge from rotating tanks: Time-Step Selection and Convergence Strategies Develop skills in choosing appropriate time-steps and ensuring solution convergence for transient rotating tank simulations. Discharge Rate Variation Over Time Learn methods to quantify and interpret the changing discharge rate as the tank empties, considering rotational effects. Velocity and Pressure Distribution Analysis In this section, we’ll delve into the detailed flow field characteristics within the rotating tank: 3D Velocity Field Visualization Techniques Master the process of visualizing and interpreting complex 3D velocity fields in rotating tank systems using ANSYS Fluent. Pressure Gradient Analysis in Rotating Frames Develop methods to analyze pressure distributions and gradients unique to rotating fluid systems. Rotational Speed Effects on Discharge Behavior Explore the critical relationship between tank rotation speed and discharge characteristics: Parametric Studies of Rotational Speed Learn to conduct and interpret parametric studies to understand how varying rotational speeds affect discharge behavior. Optimal Speed Determination for Efficient Discharge Discover techniques to determine optimal rotational speeds for maximizing discharge efficiency in various applications. Practical Applications and Industry Relevance Connect simulation insights to real-world engineering challenges: Fluid Machinery Design Optimization Explore how rotating tank discharge simulations can improve the design of centrifugal pumps, mixers, and other fluid machinery. Process Equipment Enhancement Discover the relevance of this technology in optimizing process equipment such as centrifuges and rotary filters. Advanced Result Interpretation and Performance Analysis Elevate your CFD skills with sophisticated data analysis techniques: Discharge Efficiency Metrics Calculation Learn to compute and interpret key performance indicators such as discharge coefficient and flow uniformity from simulation results. Transient Data Post-Processing Strategies Develop strategies for effective post-processing and visualization of time-dependent data from rotating tank simulations. Why This Module is Essential for Advanced Mechanical Engineers This advanced module offers a deep dive into the sophisticated world of rotating fluid systems using ANSYS Fluent. By mastering this simulation, you’ll gain invaluable insights into: Advanced CFD techniques for modeling complex multiphase flows in rotating environments The intricate relationships between rotational speed, tank geometry, and discharge behavior Practical applications of CFD in fluid machinery design, process equipment optimization, and hydraulic systems analysis By the end of this episode, you’ll have enhanced your skills in: Modeling and analyzing advanced rotating tank scenarios in ANSYS Fluent Interpreting complex CFD results to optimize rotating system designs for various applications Applying cutting-edge fluid dynamics concepts to real-world engineering challenges involving rotating fluids This knowledge will elevate your capabilities as a mechanical engineer, enabling you to contribute to innovative solutions in fields where understanding and controlling fluid behavior in rotating systems is critical. Join us on this advanced journey into the world of rotating tank CFD simulation with ANSYS Fluent, and position yourself at the forefront of mechanical engineering technology in fluid dynamics and multiphase flow analysis!
Episode 1 30m
-
-
Section 3
Pigging
-
Mastering Pipeline Pigging Dynamics: Advanced CFD Simulation for Oil and Gas Engineers Welcome to the “Pigging Oil Flow in a Pipeline CFD Simulation” episode of our “MECHANICAL Engineers: ADVANCED” course. This comprehensive module delves into the complex world of multiphase flow dynamics during pipeline pigging operations, using ANSYS Fluent to explore the intricate behavior of oil, gas, and potential debris in the presence of a stationary pig. Multiphase Flow Modeling in Pigging Operations Before diving into the simulation specifics, we’ll explore the fundamental concepts of multiphase flow modeling in the context of pipeline pigging. Oil-Gas-Debris Interaction Modeling Discover advanced methods for accurately modeling the interaction between oil, gas, and potential debris within the pipeline during pigging operations. Volume of Fluid (VOF) Method for Pigging Scenarios Learn to implement and optimize the VOF method for precise multiphase flow tracking in pigging simulations. Phase Distribution Analysis in Pigged Pipelines This section focuses on the critical aspect of phase distribution in the presence of a pig: Liquid Holdup Prediction Techniques Master the process of predicting and analyzing liquid holdup around the pig using ANSYS Fluent. Gas Pocket Formation and Evolution Gain skills in simulating and interpreting gas pocket formation and its impact on pigging efficiency. Pressure Drop Analysis in Pigged Sections Dive deep into the complexities of pressure gradients in pigged pipelines: Local Pressure Drop Calculation Methods Learn to simulate and quantify local pressure drops caused by the presence of a pig in the pipeline. Pressure Recovery Analysis Explore techniques to analyze pressure recovery downstream of the pig and its implications for overall pipeline hydraulics. Flow Pattern Visualization Around Pipeline Pigs Examine the intricate flow patterns that develop around pipeline pigs: Streamline and Pathline Visualization Techniques Develop skills in creating and interpreting streamline and pathline visualizations to understand complex flow patterns around pigs. Vortex Formation and Shedding Analysis Learn methods to identify and analyze vortex formation and shedding phenomena induced by the pig’s presence. Fluid Property Effects on Pigging Dynamics In this section, we’ll delve into how varying fluid properties influence multiphase flow behavior during pigging: Viscosity Impact on Pig-Induced Flow Patterns Master the process of simulating and analyzing how fluid viscosity affects flow behavior around the pig. Density Variation Effects on Phase Distribution Develop methods to study how density differences between phases influence their distribution in pigged sections. Practical Applications and Industry Relevance Connect simulation insights to real-world engineering challenges in the oil and gas industry: Pig Design Optimization Strategies Explore how CFD simulations can inform and improve pig design for enhanced cleaning efficiency and reduced pressure drop. Pipeline Maintenance Planning Discover the relevance of this technology in optimizing pipeline maintenance schedules and procedures. Advanced Result Interpretation and Performance Analysis Elevate your CFD skills with sophisticated data analysis techniques: Pigging Efficiency Metrics Calculation Learn to compute and interpret key performance indicators such as cleaning efficiency and pressure loss factor from simulation results. Parametric Studies for Pig Design Optimization Develop strategies for conducting parametric studies to optimize pig geometry and material properties for various pipeline conditions. Why This Module is Essential for Advanced Mechanical Engineers in Oil and Gas This advanced module offers a deep dive into the sophisticated world of pipeline pigging operations using ANSYS Fluent. By mastering this simulation, you’ll gain invaluable insights into: Advanced CFD techniques for modeling complex multiphase flows in pigged pipelines The intricate relationships between pig design, fluid properties, and flow behavior Practical applications of CFD in pipeline maintenance, cleaning efficiency optimization, and hydraulic performance analysis By the end of this episode, you’ll have enhanced your skills in: Modeling and analyzing advanced pigging scenarios in ANSYS Fluent Interpreting complex CFD results to optimize pig designs and pigging operations Applying cutting-edge fluid dynamics concepts to real-world engineering challenges in pipeline maintenance This knowledge will elevate your capabilities as a mechanical engineer in the oil and gas industry, enabling you to contribute to innovative solutions in pipeline operations, maintenance, and efficiency improvement. Join us on this advanced journey into the world of pipeline pigging CFD simulation with ANSYS Fluent, and position yourself at the forefront of mechanical engineering technology in the oil and gas sector!
Episode 1 18m 17s
-
-
Section 4
Eulerian Flow in Mechanical Devices
-
Mastering Eulerian Two-Phase Flow Dynamics: Advanced CFD Simulation in Moving Wall Cylinders Welcome to the “Eulerian Two Phase Flow in a Moving Wall Cylinder CFD Simulation” episode of our “MECHANICAL Engineers: ADVANCED” course. This comprehensive module delves into the intricate world of multiphase flows, using ANSYS Fluent to explore complex fluid dynamics in systems with moving boundaries, a critical phenomenon in various mechanical engineering applications. Eulerian-Eulerian Approach: Fundamentals and Implementation Before diving into the simulation specifics, we’ll explore the core concepts of the Eulerian-Eulerian framework for multiphase modeling. Continuum Representation of Distinct Phases Discover advanced techniques for modeling two fluid phases as interpenetrating continua within a shared computational domain. Governing Equations for Eulerian Multiphase Flow Learn to implement and interpret the complex system of equations governing Eulerian two-phase flows in ANSYS Fluent. Phase Interaction Dynamics in Cylindrical Geometries This section focuses on the critical aspects of inter-phase interactions in a cylindrical domain: Momentum Exchange and Interfacial Force Modeling Master the process of simulating momentum transfer and interfacial forces between phases in Eulerian frameworks. Mass and Heat Transfer Between Phases Gain skills in incorporating and analyzing mass and heat transfer phenomena in two-phase Eulerian simulations. Moving Boundary Conditions: Implementation and Effects Dive deep into the complexities of simulating systems with moving walls: Moving Mesh Techniques for Rotating Cylinders Learn to implement and optimize moving mesh methods to accurately represent rotating or stirred vessel scenarios. Impact of Wall Motion on Phase Distribution Explore techniques to analyze how cylinder wall motion influences the spatial distribution of different phases. Advanced Turbulence Modeling in Eulerian Multiphase Flows Examine the challenges and solutions for turbulence modeling in multiphase systems: Multiphase Turbulence Model Selection Develop skills in choosing and implementing appropriate turbulence models for Eulerian two-phase flows. Turbulence-Induced Phase Interaction Analysis Learn methods to quantify and interpret the effects of turbulence on phase interaction and mixing efficiency. Phase Distribution and Mixing Pattern Analysis In this section, we’ll delve into the spatial and temporal evolution of phase fractions: Transient Phase Distribution Visualization Techniques Master the process of visualizing and interpreting time-dependent phase distribution patterns in moving wall cylinders. Mixing Efficiency Quantification Methods Develop strategies to quantify and optimize mixing efficiency in two-phase systems with moving boundaries. Practical Applications and Industry Relevance Connect simulation insights to real-world engineering challenges: Chemical Reactor Design Optimization Explore how Eulerian two-phase flow simulations can improve the design and performance of stirred chemical reactors. Oil and Gas Separation Process Enhancement Discover the relevance of this technology in optimizing separation processes in the oil and gas industry. Advanced Result Interpretation and Performance Analysis Elevate your CFD skills with sophisticated data analysis techniques: Phase Interaction Metrics Calculation Learn to compute and interpret key performance indicators such as interfacial area concentration and mass transfer coefficients from simulation results. Parametric Studies for Moving Wall Effects Develop strategies to conduct parametric studies to understand the impact of wall motion parameters on two-phase flow behavior. Why This Module is Crucial for Advanced Mechanical Engineers This advanced module offers a deep dive into the sophisticated world of Eulerian two-phase flow dynamics using ANSYS Fluent. By mastering this simulation, you’ll gain invaluable insights into: Advanced CFD techniques for modeling complex multiphase phenomena in systems with moving boundaries The intricate relationships between wall motion, phase distribution, and mixing efficiency Practical applications of CFD in process equipment design, chemical engineering, and multiphase flow systems By the end of this episode, you’ll have enhanced your skills in: Modeling and analyzing advanced Eulerian two-phase flow scenarios in ANSYS Fluent Interpreting complex CFD results to optimize multiphase system designs for various industrial applications Applying cutting-edge fluid dynamics concepts to real-world engineering challenges involving moving boundaries and multiple phases This knowledge will elevate your capabilities as a mechanical engineer, enabling you to contribute to innovative solutions in fields where understanding and controlling multiphase flows in dynamic systems is critical. Join us on this advanced journey into the world of Eulerian two-phase flow CFD simulation with ANSYS Fluent, and position yourself at the forefront of mechanical engineering technology in multiphase flow analysis and process equipment design!
Episode 1 13m 31s -
This advanced-level episode delves into the complex world of Eulerian multiphase flow simulation within a convergent-divergent channel using ANSYS Fluent. Participants will explore the intricacies of two-phase flow behavior in a mechanical device commonly encountered in various engineering applications. Key topics: Introduction to Eulerian multiphase flow modeling and its relevance in mechanical engineering Overview of convergent-divergent channel geometry and its applications Setting up the two-phase flow simulation in ANSYS Fluent Defining fluid properties and interfacial physics for the two phases Configuring appropriate turbulence models for multiphase flow Implementing boundary conditions specific to the convergent-divergent channel Running the simulation and monitoring convergence Analyzing phase distribution and flow patterns within the channel Interpreting velocity and pressure fields for both phases By completing this episode, participants will gain advanced knowledge in simulating complex multiphase flows using the Eulerian approach. This understanding is crucial for analyzing and optimizing various mechanical devices involving two-phase flow, such as nozzles, diffusers, and separators. Participants will enhance their skills in advanced CFD techniques, enabling them to tackle challenging multiphase flow problems in their mechanical engineering projects and research.
Episode 2 15m 7s
-
-
Section 5
DPM (Discrete Phase Model)
-
Mastering Gravity-Driven Particle Separation: Advanced CFD Simulation for Mechanical Engineers Welcome to the “Particle Trapper by Gravity CFD Simulation” episode of our “MECHANICAL Engineers: ADVANCED” course. This comprehensive module delves into the intricate world of particle-fluid interactions, using ANSYS Fluent to explore the complex dynamics of gravity-driven particle separation, a critical process in numerous mechanical engineering applications. Discrete Phase Model (DPM) Setup and Implementation Before diving into the simulation specifics, we’ll explore the fundamental concepts and setup procedures for the Discrete Phase Model in ANSYS Fluent. Particle Injection Configuration Techniques Discover advanced methods for defining and implementing particle injection points and properties in DPM simulations. Particle Tracking and Fate Determination Strategies Learn to configure and optimize particle tracking algorithms and fate determination criteria for accurate separation analysis. Gravity-Driven Separation Dynamics This section focuses on the critical aspects of particle behavior under gravitational influence: Particle Trajectory Analysis in Gravitational Fields Master the process of simulating and analyzing particle trajectories in gravity-driven separation devices using ANSYS Fluent. Influence of Particle Properties on Separation Efficiency Gain skills in investigating how particle size, density, and shape affect separation performance in gravity-based systems. Particle-Fluid Coupling: Two-Way Interaction Modeling Dive deep into the complexities of two-way coupling between discrete particles and the continuous fluid phase: Momentum Exchange Modeling Techniques Learn to implement and analyze momentum transfer mechanisms between particles and the surrounding fluid. Particle-Induced Turbulence Effects Explore techniques to quantify and interpret the impact of particles on fluid turbulence and overall flow patterns. Trapping Efficiency Evaluation and Optimization Examine the effectiveness of gravity-based particle trapping mechanisms: Separation Efficiency Calculation Methods Develop skills in computing and interpreting separation efficiency metrics for particles of various sizes and densities. Design Parameter Optimization for Enhanced Trapping Learn methods to optimize trap geometry and operating conditions for improved particle separation performance. Flow Field Analysis in Particle-Laden Flows In this section, we’ll delve into the impact of particle presence on fluid dynamics: Velocity Field Visualization in Multiphase Flows Master the process of visualizing and interpreting complex velocity fields in particle-laden flows using ANSYS Fluent. Pressure Distribution Analysis in Separation Devices Develop strategies to analyze pressure distributions and their influence on particle separation dynamics. Practical Applications and Industry Relevance Connect simulation insights to real-world engineering challenges: Cyclone Separator Design Optimization Explore how DPM simulations can improve the efficiency and performance of cyclone separators in industrial applications. Dust Collection System Enhancement Discover the relevance of this technology in optimizing dust collection systems for various industrial processes. Advanced Result Interpretation and Performance Analysis Elevate your CFD skills with sophisticated data analysis techniques: Particle Residence Time Distribution Analysis Learn to compute and interpret particle residence time distributions to evaluate separator performance. Parametric Studies for Trapper Design Optimization Develop strategies to conduct parametric studies for optimizing trapper design under various operating conditions. Why This Module is Essential for Advanced Mechanical Engineers This advanced module offers a deep dive into the sophisticated world of gravity-driven particle separation using ANSYS Fluent’s Discrete Phase Model. By mastering this simulation, you’ll gain invaluable insights into: Advanced CFD techniques for modeling complex particle-fluid interactions in separation devices The intricate relationships between particle properties, fluid dynamics, and separation efficiency Practical applications of CFD in particulate matter control, process equipment design, and environmental engineering By the end of this episode, you’ll have enhanced your skills in: Modeling and analyzing advanced particle separation scenarios in ANSYS Fluent Interpreting complex CFD results to optimize gravity-based separator designs for various industrial applications Applying cutting-edge multiphase flow concepts to real-world engineering challenges involving particle transport and separation This knowledge will elevate your capabilities as a mechanical engineer, enabling you to contribute to innovative solutions in fields where understanding and controlling particle behavior is critical, such as air pollution control, mineral processing, and wastewater treatment. Join us on this advanced journey into the world of gravity-driven particle separation CFD simulation with ANSYS Fluent, and position yourself at the forefront of mechanical engineering technology in multiphase flow analysis and separation process optimization!
Episode 1 21m 57s -
This advanced-level episode delves into the intricate world of spray systems simulation using the Discrete Phase Model (DPM) in Computational Fluid Dynamics (CFD). Participants will explore the complexities of modeling color spraying on a wall with conical injection, a process commonly encountered in various mechanical engineering applications. Key topics: Introduction to Discrete Phase Model (DPM) and its relevance in mechanical engineering Overview of spray systems and conical injection applications in industry Configuring DPM parameters for color particles and conical injection Defining injection properties, including spray angle, velocity, and particle size distribution Implementing appropriate turbulence models for spray dynamics Setting up wall interaction models for particle deposition and film formation Running the simulation and monitoring particle trajectories Analyzing spray pattern and coating uniformity on the wall Visualizing particle dispersion and air flow interactions Interpreting results and their implications for spray system design By completing this episode, participants will gain advanced knowledge in simulating complex spray systems using the Discrete Phase Model. This understanding is crucial for analyzing and optimizing various mechanical systems involving particle injection, such as paint booths, fuel injectors, and agricultural sprayers. Participants will enhance their skills in advanced CFD techniques, enabling them to tackle challenging multiphase flow problems in their mechanical engineering projects and research related to spray applications.
Episode 2 31m 40s
-
-
Section 6
Injector
-
Mastering Three-Phase Flow Dynamics in Fuel Injectors: Advanced CFD Simulation for Mechanical Engineers Welcome to the “Fuel Injector Three Phase Flow CFD Simulation” episode of our “MECHANICAL Engineers: ADVANCED” course. This comprehensive module delves into the complex world of multiphase flow dynamics within fuel injectors, using ANSYS Fluent to explore the intricate behavior of liquid fuel, vapor, and air interactions, a critical phenomenon in combustion system engineering. Three-Phase Flow Modeling in Fuel Injectors Before diving into the simulation specifics, we’ll explore the fundamental concepts of three-phase flow modeling in the context of fuel injection systems. Liquid Fuel, Vapor, and Air Interaction Modeling Discover advanced methods for accurately modeling the complex interactions between liquid fuel, vapor, and air within the confined geometry of a fuel injector. Phase Transition Dynamics in High-Pressure Environments Learn to implement and analyze phase transition phenomena occurring in the high-pressure conditions typical of fuel injection systems. Volume of Fluid (VOF) Method Implementation This section focuses on the critical aspect of interface tracking in multiphase flows: VOF Setup for Multiple Fluid Interfaces Master the process of setting up and optimizing the VOF method for tracking multiple fluid interfaces in fuel injector simulations. Interface Reconstruction Techniques Gain skills in implementing and fine-tuning interface reconstruction algorithms for improved accuracy in multiphase simulations. Fluid Property Effects on Injection Dynamics Dive deep into the impact of fluid properties on multiphase flow behavior: Viscosity and Surface Tension Influence Analysis Learn to simulate and quantify the effects of fluid viscosity and surface tension on spray formation and injector performance. Fuel Composition Impact on Flow Characteristics Explore techniques to analyze how variations in fuel composition affect the overall flow behavior within the injector. Nozzle Flow Characteristics in Multiphase Environments Examine the intricate flow patterns and phase distributions within fuel injector nozzles: Cavitation Inception and Development Modeling Develop skills in simulating and interpreting cavitation phenomena in fuel injector nozzles using ANSYS Fluent. Spray Atomization Process Analysis Learn methods to model and analyze the initial stages of spray atomization as fuel exits the injector nozzle. Pressure and Velocity Field Analysis in Fuel Injectors In this section, we’ll delve into the detailed flow field characteristics within the fuel injector: High-Pressure Zone Identification Techniques Master the process of identifying and analyzing high-pressure zones within the injector that influence fuel atomization. Velocity Profile Optimization for Efficient Injection Develop methods to study and optimize velocity profiles for improved fuel injection efficiency and spray characteristics. Practical Applications and Industry Relevance Connect simulation insights to real-world engineering challenges in combustion systems: Injector Design Optimization Strategies Explore how CFD simulations can inform and improve fuel injector design for enhanced combustion efficiency and reduced emissions. Engine Performance Enhancement Discover the relevance of this technology in optimizing overall engine performance through improved fuel injection processes. Advanced Result Interpretation and Performance Analysis Elevate your CFD skills with sophisticated data analysis techniques: Injection Quality Metrics Calculation Learn to compute and interpret key performance indicators such as spray cone angle, penetration depth, and droplet size distribution from simulation results. Parametric Studies for Nozzle Geometry Optimization Develop strategies for conducting parametric studies to optimize nozzle geometry for various engine operating conditions. Why This Module is Essential for Advanced Mechanical Engineers in Combustion Systems This advanced module offers a deep dive into the sophisticated world of three-phase flow dynamics in fuel injectors using ANSYS Fluent. By mastering this simulation, you’ll gain invaluable insights into: Advanced CFD techniques for modeling complex multiphase phenomena in high-pressure injection systems The intricate relationships between injector geometry, fluid properties, and spray characteristics Practical applications of CFD in engine design, combustion optimization, and emission reduction strategies By the end of this episode, you’ll have enhanced your skills in: Modeling and analyzing advanced fuel injector scenarios in ANSYS Fluent Interpreting complex CFD results to optimize injector designs for various engine types and operating conditions Applying cutting-edge fluid dynamics concepts to real-world engineering challenges in combustion systems This knowledge will elevate your capabilities as a mechanical engineer in the automotive and combustion engineering fields, enabling you to contribute to innovative solutions in engine development, fuel efficiency improvement, and emission control. Join us on this advanced journey into the world of fuel injector CFD simulation with ANSYS Fluent, and position yourself at the forefront of mechanical engineering technology in combustion system design and optimization!
Episode 1 15m 4s -
This advanced-level episode explores the complex world of multi-phase flow simulation within an injector using Computational Fluid Dynamics (CFD). Participants will delve into the intricacies of modeling fluid behavior in injectors, a critical component in various mechanical engineering applications. Key topics: Introduction to multi-phase flow modeling in injectors and its significance in mechanical engineering Overview of injector applications in industry (e.g., fuel injection systems, spray cooling, chemical processing) Configuring multi-phase flow models for the injector simulation Defining fluid properties and interfacial physics for the different phases Implementing appropriate turbulence models for multi-phase flow in injectors Setting up boundary conditions specific to injector operation Configuring droplet breakup and coalescence models Running the simulation and monitoring convergence Analyzing flow patterns, pressure distribution, and phase interactions within the injector Visualizing velocity fields, droplet size distribution, and spray characteristics Interpreting results to evaluate injector performance and efficiency By completing this episode, participants will gain advanced knowledge in simulating complex multi-phase flows within injectors using CFD techniques. This understanding is essential for analyzing and optimizing various mechanical systems involving injection processes, such as internal combustion engines, gas turbines, and industrial spraying systems. Participants will enhance their skills in advanced CFD modeling, enabling them to tackle challenging multi-phase flow problems in their mechanical engineering projects and research related to injector applications.
Episode 2 13m 34s
-
-
Section 7
Blower
-
Mastering Centrifugal Blower Dynamics: Advanced CFD Simulation for Mechanical Engineers Welcome to the “Centrifugal Blower CFD Simulation” episode of our “MECHANICAL Engineers: ADVANCED” course. This comprehensive module delves into the complex world of centrifugal blower design and analysis, using ANSYS Fluent and the Multiple Reference Frame (MRF) approach to explore the intricate fluid dynamics within these critical mechanical systems. Multiple Reference Frame (MRF) Modeling: Foundations and Implementation Before diving into the simulation specifics, we’ll explore the core concepts of the MRF approach for modeling rotating machinery. Rotating and Stationary Zone Definition Discover advanced techniques for defining and implementing rotating impeller and stationary volute zones in ANSYS Fluent. Interface Treatment Between Rotating and Stationary Domains Learn to implement and optimize interface conditions for seamless flow transition between rotating and stationary components. Flow Field Analysis in Centrifugal Blowers This section focuses on the critical aspects of flow behavior within the blower: Impeller Flow Patterns and Vortex Formation Master the process of simulating and analyzing complex flow patterns and vortex structures within the rotating impeller. Volute Flow Characteristics and Pressure Recovery Gain skills in investigating flow behavior and pressure recovery mechanisms within the blower volute. Performance Characteristics Evaluation Dive deep into the methods for assessing and optimizing blower performance: Pressure Rise and Flow Rate Relationship Analysis Learn to simulate and interpret the fundamental pressure-flow characteristics of centrifugal blowers. Efficiency Calculation and Optimization Techniques Explore methods to compute blower efficiency and develop strategies for performance optimization. Impeller and Volute Flow Interaction Examine the crucial interplay between impeller and volute flows: Blade Pass Frequency Effects Simulation Develop skills in modeling and analyzing the dynamic effects of blade passage on volute flow. Tongue Region Flow Analysis Learn techniques to investigate the complex flow behavior near the volute tongue and its impact on overall performance. Velocity and Pressure Distribution Analysis In this section, we’ll delve into the detailed flow field characteristics within the blower: 3D Velocity Field Visualization Techniques Master the process of visualizing and interpreting complex 3D velocity fields in centrifugal blowers using ANSYS Fluent. Pressure Contour Analysis for Performance Evaluation Develop methods to analyze pressure distributions and their influence on blower performance and efficiency. Impact of Rotational Speed on Blower Performance Explore the critical relationship between impeller speed and blower characteristics: Scaling Laws and Similarity Principles Learn to apply and validate scaling laws for predicting blower performance at different operating speeds. Off-Design Performance Prediction Discover techniques to simulate and analyze blower behavior under various rotational speeds and flow conditions. Practical Applications and Industry Relevance Connect simulation insights to real-world engineering challenges: HVAC System Design Optimization Explore how centrifugal blower CFD simulations can improve the design and efficiency of HVAC systems. Industrial Ventilation Solutions Discover the relevance of this technology in optimizing industrial ventilation and dust collection systems. Advanced Result Interpretation and Performance Analysis Elevate your CFD skills with sophisticated data analysis techniques: Performance Curve Generation and Interpretation Learn to generate and interpret comprehensive performance curves from CFD results for various operating conditions. Parametric Studies for Design Optimization Develop strategies to conduct parametric studies for optimizing impeller and volute geometries to enhance overall blower performance. Why This Module is Essential for Advanced Mechanical Engineers This advanced module offers a deep dive into the sophisticated world of centrifugal blower dynamics using ANSYS Fluent. By mastering this simulation, you’ll gain invaluable insights into: Advanced CFD techniques for modeling complex rotating machinery using the MRF approach The intricate relationships between blower geometry, operating conditions, and performance characteristics Practical applications of CFD in HVAC, industrial ventilation, and process industry equipment design By the end of this episode, you’ll have enhanced your skills in: Modeling and analyzing advanced centrifugal blower scenarios in ANSYS Fluent Interpreting complex CFD results to optimize blower designs for various industrial applications Applying cutting-edge fluid dynamics concepts to real-world engineering challenges in fluid handling systems This knowledge will elevate your capabilities as a mechanical engineer, enabling you to contribute to innovative solutions in fields where understanding and optimizing centrifugal blower performance is critical. Join us on this advanced journey into the world of centrifugal blower CFD simulation with ANSYS Fluent, and position yourself at the forefront of mechanical engineering technology in fluid handling system design and optimization!
Episode 1 17m 27s
-
-
Section 8
Compressor
-
Mastering Centrifugal Compressor Dynamics: Advanced CFD Simulation for Mechanical Engineers Welcome to the “Centrifugal Compressor CFD Simulation” episode of our “MECHANICAL Engineers: ADVANCED” course. This comprehensive module delves into the complex world of centrifugal compressor design and analysis, using ANSYS Fluent to explore the intricate aerodynamics within these critical turbomachinery components. Compressible Flow Modeling in Rotating Machinery Before diving into the simulation specifics, we’ll explore the fundamental concepts of compressible flow modeling in the context of centrifugal compressors. Governing Equations for Compressible Flows Discover advanced techniques for implementing and solving the governing equations of compressible flow in ANSYS Fluent. Turbulence Modeling for High-Speed Rotating Flows Learn to select and implement appropriate turbulence models for accurate simulation of high-speed flows in centrifugal compressors. Impeller and Diffuser Flow Analysis This section focuses on the critical aspects of flow behavior within the compressor’s key components: Impeller Passage Flow Characteristics Master the process of simulating and analyzing complex flow patterns within the rotating impeller passages, including secondary flows and tip clearance effects. Diffuser Performance and Pressure Recovery Gain skills in investigating flow behavior and pressure recovery mechanisms within the compressor diffuser, both vaned and vaneless designs. Pressure Ratio and Efficiency Calculations Dive deep into the methods for assessing and optimizing compressor performance: Total-to-Total Pressure Ratio Computation Learn to simulate and interpret the fundamental pressure ratio characteristics of centrifugal compressors across various operating conditions. Isentropic Efficiency Evaluation Techniques Explore methods to compute compressor efficiency and develop strategies for performance optimization, considering both aerodynamic and thermodynamic aspects. Rotating Reference Frame Implementation Examine the crucial aspects of modeling rotating machinery in CFD: Multiple Reference Frame (MRF) Approach Develop skills in implementing the MRF method for steady-state analysis of centrifugal compressors, including interface treatment between rotating and stationary domains. Sliding Mesh Technique for Transient Analysis Learn techniques to set up and execute transient simulations using the sliding mesh approach for capturing time-dependent phenomena in compressor operation. Pressure and Temperature Distribution Analysis In this section, we’ll delve into the detailed thermodynamic field characteristics within the compressor: 3D Pressure Field Visualization Techniques Master the process of visualizing and interpreting complex 3D pressure fields in centrifugal compressors using ANSYS Fluent, including shock wave identification in transonic designs. Temperature Contour Analysis for Performance Evaluation Develop methods to analyze temperature distributions and their influence on compressor performance, efficiency, and material considerations. Impact of Rotational Speed on Compressor Performance Explore the critical relationship between impeller speed and compressor characteristics: Compressor Map Generation and Analysis Learn to generate and interpret compressor maps, including surge and choke limits, for various rotational speeds. Mach Number Effects on Flow Behavior Discover techniques to simulate and analyze compressor behavior under subsonic, transonic, and supersonic flow regimes at different operating speeds. Velocity Profiles and Secondary Flows Examine the intricate flow structures within the compressor: Blade-to-Blade Flow Visualization Explore methods for visualizing and analyzing flow patterns on blade-to-blade surfaces, including potential flow separation and wake formation. Tip Clearance Flow Analysis Learn to simulate and quantify the effects of tip clearance flows on compressor performance and efficiency. Practical Applications and Industry Relevance Connect simulation insights to real-world engineering challenges: Aerospace Propulsion System Design Explore how centrifugal compressor CFD simulations contribute to the design and optimization of aircraft engines and auxiliary power units. Industrial Process Compressor Optimization Discover the relevance of this technology in enhancing the performance of compressors used in various industrial processes, including oil and gas, petrochemical, and refrigeration applications. Advanced Result Interpretation and Performance Analysis Elevate your CFD skills with sophisticated data analysis techniques: Surge Margin Prediction and Stability Analysis Learn to predict surge margins and analyze compressor stability using CFD results, crucial for safe and efficient operation. Parametric Studies for Design Optimization Develop strategies to conduct parametric studies for optimizing impeller and diffuser geometries to enhance overall compressor performance across the operating range. Why This Module is Essential for Advanced Mechanical Engineers This advanced module offers a deep dive into the sophisticated world of centrifugal compressor dynamics using ANSYS Fluent. By mastering this simulation, you’ll gain invaluable insights into: Advanced CFD techniques for modeling complex compressible flows in high-speed rotating machinery The intricate relationships between compressor geometry, operating conditions, and performance characteristics Practical applications of CFD in aerospace, turbomachinery, and industrial process equipment design By the end of this episode, you’ll have enhanced your skills in: Modeling and analyzing advanced centrifugal compressor scenarios in ANSYS Fluent Interpreting complex CFD results to optimize compressor designs for various industrial and aerospace applications Applying cutting-edge fluid dynamics concepts to real-world engineering challenges in turbomachinery This knowledge will elevate your capabilities as a mechanical engineer, enabling you to contribute to innovative solutions in fields where understanding and optimizing centrifugal compressor performance is critical. Join us on this advanced journey into the world of centrifugal compressor CFD simulation with ANSYS Fluent, and position yourself at the forefront of mechanical engineering technology in turbomachinery design and optimization!
Episode 1 18m 49s -
This advanced-level episode delves into the complex world of multistage compressor simulation using Computational Fluid Dynamics (CFD). Participants will explore the intricacies of modeling fluid flow through a compressor with two rotor and two stator rows, a critical component in various mechanical engineering applications. Key topics: Introduction to multistage compressor modeling and its significance in mechanical engineering Overview of compressor applications in industry (e.g., gas turbines, HVAC systems, process industries) Configuring the CFD simulation for the multistage compressor Implementing appropriate turbulence models for compressor flow Setting up rotating reference frames for the rotor stages Defining interface conditions between rotor and stator domains Configuring boundary conditions specific to compressor operation Running the simulation and monitoring convergence Analyzing flow patterns, pressure ratios, and temperature changes across stages Visualizing velocity fields, pressure distributions, and streamlines By completing this episode, participants will gain advanced knowledge in simulating complex multistage compressor flows using CFD techniques. This understanding is crucial for analyzing and optimizing various mechanical systems involving compression processes, such as gas turbine engines, industrial air compressors, and refrigeration systems. Participants will enhance their skills in advanced CFD modeling, enabling them to tackle challenging turbomachinery problems in their mechanical engineering projects and research related to compressor applications.
Episode 2 14m 43s
-
-
Section 9
Venturi
-
Mastering Venturi-Induced Air Suction: Advanced CFD Simulation for Mechanical Engineers Welcome to the “Venturi VOF Multi-Phase Flow in a Tube for Air Suction CFD Simulation” episode of our “MECHANICAL Engineers: ADVANCED” course. This comprehensive module delves into the complex world of Venturi flow dynamics for air suction, utilizing ANSYS Fluent and the Volume of Fluid (VOF) multi-phase approach to explore the intricate fluid behavior within these critical mechanical systems. Volume of Fluid (VOF) Multi-Phase Flow Modeling Before diving into the simulation specifics, we’ll explore the fundamental concepts of VOF modeling in the context of Venturi-induced air suction. VOF Method Principles and Implementation Discover advanced techniques for implementing the VOF method to accurately capture the interface between primary and secondary fluids in Venturi tubes. Phase Interaction Setup in ANSYS Fluent Learn to define and optimize phase interactions, including surface tension and interface momentum exchange, for realistic multi-phase flow simulation. Pressure Drop and Velocity Profile Analysis This section focuses on the critical aspects of flow behavior within the Venturi tube: Bernoulli's Principle Application in Venturi Flows Master the process of simulating and analyzing pressure and velocity relationships in Venturi tubes, validating Bernoulli’s principle in practice. Velocity Profile Evolution Through Venturi Sections Gain skills in investigating flow acceleration and deceleration patterns through the converging, throat, and diverging sections of the Venturi. Air Entrainment and Suction Effects Dive deep into the mechanisms of air suction in Venturi systems: Secondary Flow Induction Simulation Learn to model and quantify the air entrainment process at the suction port of the Venturi tube. Suction Efficiency Calculation Techniques Explore methods to compute and optimize the suction efficiency of Venturi systems under various operating conditions. Flow Behavior Analysis at Critical Venturi Sections In this section, we’ll delve into the detailed flow characteristics at key points within the Venturi tube: Throat Section Flow Dynamics Master the process of visualizing and interpreting complex flow patterns at the Venturi throat, including potential cavitation inception. Diffuser Section Recovery Analysis Develop methods to analyze pressure recovery and flow expansion in the diffuser section, crucial for overall Venturi performance. Impact of Operating Conditions on Suction Performance Explore the critical relationship between system parameters and Venturi suction characteristics: Primary Flow Rate Influence on Suction Capacity Learn to simulate and quantify how variations in primary flow rate affect the air suction performance of the Venturi system. Pressure Ratio Effects on Entrainment Efficiency Discover techniques to analyze the impact of inlet-to-outlet pressure ratios on the overall entrainment efficiency of the Venturi. Interaction Between Primary and Secondary Fluids Examine the intricate interplay between the main flow and entrained air: Mixing Zone Characterization Explore methods for visualizing and analyzing the mixing process between primary and secondary fluids downstream of the suction port. Two-Phase Flow Regime Identification Learn to identify and characterize different two-phase flow regimes that may occur within the Venturi system under various operating conditions. Practical Applications and Industry Relevance Connect simulation insights to real-world engineering challenges: Vacuum System Design Optimization Explore how Venturi CFD simulations can improve the design and efficiency of vacuum generation systems in industrial applications. Fluid Handling and Processing Solutions Discover the relevance of this technology in optimizing fluid handling systems, including chemical processing and wastewater treatment applications. Advanced Result Interpretation and Performance Analysis Elevate your CFD skills with sophisticated data analysis techniques: Suction Characteristic Curve Generation Learn to generate and interpret comprehensive suction characteristic curves from CFD results for various Venturi geometries and operating conditions. Parametric Studies for Design Optimization Develop strategies to conduct parametric studies for optimizing Venturi geometry to enhance overall suction performance and efficiency. Why This Module is Essential for Advanced Mechanical Engineers This advanced module offers a deep dive into the sophisticated world of Venturi-induced air suction dynamics using ANSYS Fluent. By mastering this simulation, you’ll gain invaluable insights into: Advanced CFD techniques for modeling complex multi-phase flows in Venturi systems using the VOF approach The intricate relationships between Venturi geometry, operating conditions, and suction performance characteristics Practical applications of CFD in vacuum technology, fluid handling systems, and process industry equipment design By the end of this episode, you’ll have enhanced your skills in: Modeling and analyzing advanced Venturi-based air suction scenarios in ANSYS Fluent Interpreting complex CFD results to optimize Venturi designs for various industrial applications Applying cutting-edge fluid dynamics concepts to real-world engineering challenges in multi-phase flow systems This knowledge will elevate your capabilities as a mechanical engineer, enabling you to contribute to innovative solutions in fields where understanding and optimizing Venturi-based air suction systems is critical. Join us on this advanced journey into the world of Venturi VOF multi-phase flow CFD simulation with ANSYS Fluent, and position yourself at the forefront of mechanical engineering technology in fluid handling system design and optimization!
Episode 1 15m 16s -
This advanced-level episode explores the detailed simulation of a venturimeter with a manometer using Computational Fluid Dynamics (CFD) in Ansys Fluent. Participants will delve into the intricacies of modeling fluid flow through a venturi tube and the associated pressure measurements, a fundamental concept with wide-ranging applications in mechanical engineering. Key topics: Introduction to venturimeters and their significance in fluid flow measurement Overview of venturi applications in mechanical engineering (e.g., flow rate measurement, mixing systems, thrust augmentation) Configuring the CFD simulation for the venturimeter and manometer system in Ansys Fluent Implementing appropriate turbulence models for accurate flow prediction Setting up multiphase flow models to simulate the fluid in the manometer Defining boundary conditions for inlet, outlet, and wall surfaces Configuring solution methods and convergence criteria Running the simulation and monitoring solution stability Analyzing pressure distributions and velocity profiles through the venturi Visualizing flow patterns, streamlines, and pressure contours Interpreting results to calculate flow rates and discharge coefficients By completing this episode, participants will gain advanced knowledge in simulating complex flow measurement devices using CFD techniques in Ansys Fluent. This understanding is crucial for analyzing and optimizing various mechanical systems involving flow measurement and control, such as pipeline systems, industrial processes, and aerospace applications. Participants will enhance their skills in advanced CFD modeling, enabling them to tackle challenging fluid dynamics problems in their mechanical engineering projects and research related to flow measurement and venturi applications.
Episode 2 25m 37s
-
-
Section 10
Separation and Shock Wave
-
Mastering Supersonic Nozzle Dynamics: Advanced CFD Simulation for Mechanical Engineers Welcome to the “Supersonic Nozzle Flow Separation and Shock Wave CFD Simulation” episode of our “MECHANICAL Engineers: ADVANCED” course. This comprehensive module delves into the complex world of supersonic nozzle flow, focusing on the intricate phenomena of flow separation and shock wave formation using cutting-edge CFD techniques. Compressible Flow Modeling in Supersonic Regimes Before diving into the simulation specifics, we’ll explore the fundamental concepts of compressible flow modeling in supersonic conditions. Governing Equations for High-Speed Flows Discover advanced techniques for implementing and solving the governing equations of compressible flow in supersonic regimes using ANSYS Fluent. Turbulence Modeling for Supersonic Flows Learn to select and implement appropriate turbulence models for accurate simulation of high-speed flows in supersonic nozzles, considering shock-turbulence interactions. Shock Wave Formation and Propagation Analysis This section focuses on the critical aspects of shock wave dynamics within supersonic nozzles: Normal Shock Wave Capture Techniques Master the process of simulating and analyzing normal shock waves in supersonic nozzles, including their formation and propagation. Oblique Shock Wave Modeling in Overexpanded Nozzles Gain skills in investigating oblique shock wave structures and their interaction with nozzle walls under various operating conditions. Boundary Layer Separation in Adverse Pressure Gradients Dive deep into the mechanisms of flow separation in supersonic nozzles: Boundary Layer Behavior in Supersonic Flows Learn to model and analyze boundary layer development and behavior in high-speed nozzle flows, including the effects of compressibility. Separation Point Prediction Methods Explore techniques to accurately predict and analyze flow separation points in supersonic nozzles under various pressure ratios. Nozzle Performance Analysis Under Various Operating Conditions In this section, we’ll delve into the detailed performance characteristics of supersonic nozzles: Thrust Coefficient Calculation Techniques Master the process of computing and interpreting thrust coefficients for supersonic nozzles under design and off-design conditions. Nozzle Efficiency Evaluation Methods Develop strategies to assess and optimize nozzle efficiency, considering factors such as flow separation and shock wave losses. Mach Number Distribution Along the Nozzle Explore the critical Mach number variations within supersonic nozzles: Subsonic-to-Supersonic Transition Analysis Learn to simulate and visualize the transition from subsonic to supersonic flow in converging-diverging nozzles. Mach Number Contour Interpretation Discover techniques to generate and analyze Mach number contours, providing insights into flow acceleration and shock formation. Pressure and Temperature Variations Across Shocks Examine the thermodynamic changes associated with shock waves: Pressure Jump Conditions Across Shocks Explore methods for quantifying and visualizing pressure discontinuities across normal and oblique shock waves in nozzle flows. Temperature Rise Prediction in Shock Regions Learn to predict and analyze temperature increases due to shock compression, crucial for material selection and thermal management in nozzle design. Impact of Back Pressure on Nozzle Flow Characteristics Analyze the effects of varying exit conditions on nozzle performance: Flow Adaptation to Changing Back Pressures Develop skills in simulating nozzle flow behavior under varying back pressure conditions, from overexpanded to underexpanded regimes. Hysteresis Effects in Nozzle Flow Patterns Explore the phenomena of flow pattern hysteresis in supersonic nozzles as back pressure is varied, and its implications for nozzle operation. Practical Applications and Industry Relevance Connect simulation insights to real-world engineering challenges: Rocket Engine Nozzle Optimization Explore how CFD simulations of supersonic nozzles contribute to the design and optimization of rocket propulsion systems. Supersonic Wind Tunnel Design Discover the relevance of this technology in developing efficient supersonic wind tunnels for aerospace testing and research. Advanced Result Interpretation and Performance Analysis Elevate your CFD skills with sophisticated data analysis techniques: Shock Structure Visualization Methods Learn advanced techniques for visualizing complex shock structures in supersonic nozzles, including shock diamonds and interaction patterns. Parametric Studies for Nozzle Shape Optimization Develop strategies to conduct parametric studies for optimizing nozzle contours to enhance performance across a range of operating conditions. Why This Module is Essential for Advanced Mechanical Engineers This advanced module offers a deep dive into the sophisticated world of supersonic nozzle dynamics using state-of-the-art CFD techniques. By mastering this simulation, you’ll gain invaluable insights into: Advanced CFD methods for modeling complex compressible flows and shock phenomena in supersonic nozzles The intricate relationships between nozzle geometry, operating conditions, and flow separation characteristics Practical applications of CFD in aerospace propulsion, rocket engine design, and high-speed aerodynamics By the end of this episode, you’ll have enhanced your skills in: Modeling and analyzing advanced supersonic nozzle scenarios in ANSYS Fluent Interpreting complex CFD results to optimize nozzle designs for various aerospace and propulsion applications Applying cutting-edge fluid dynamics concepts to real-world engineering challenges in high-speed flow systems This knowledge will elevate your capabilities as a mechanical engineer, enabling you to contribute to innovative solutions in fields where understanding and optimizing supersonic nozzle performance is critical. Join us on this advanced journey into the world of supersonic nozzle CFD simulation, and position yourself at the forefront of mechanical engineering technology in propulsion system design and high-speed aerodynamics!
Episode 1 20m 19s
-
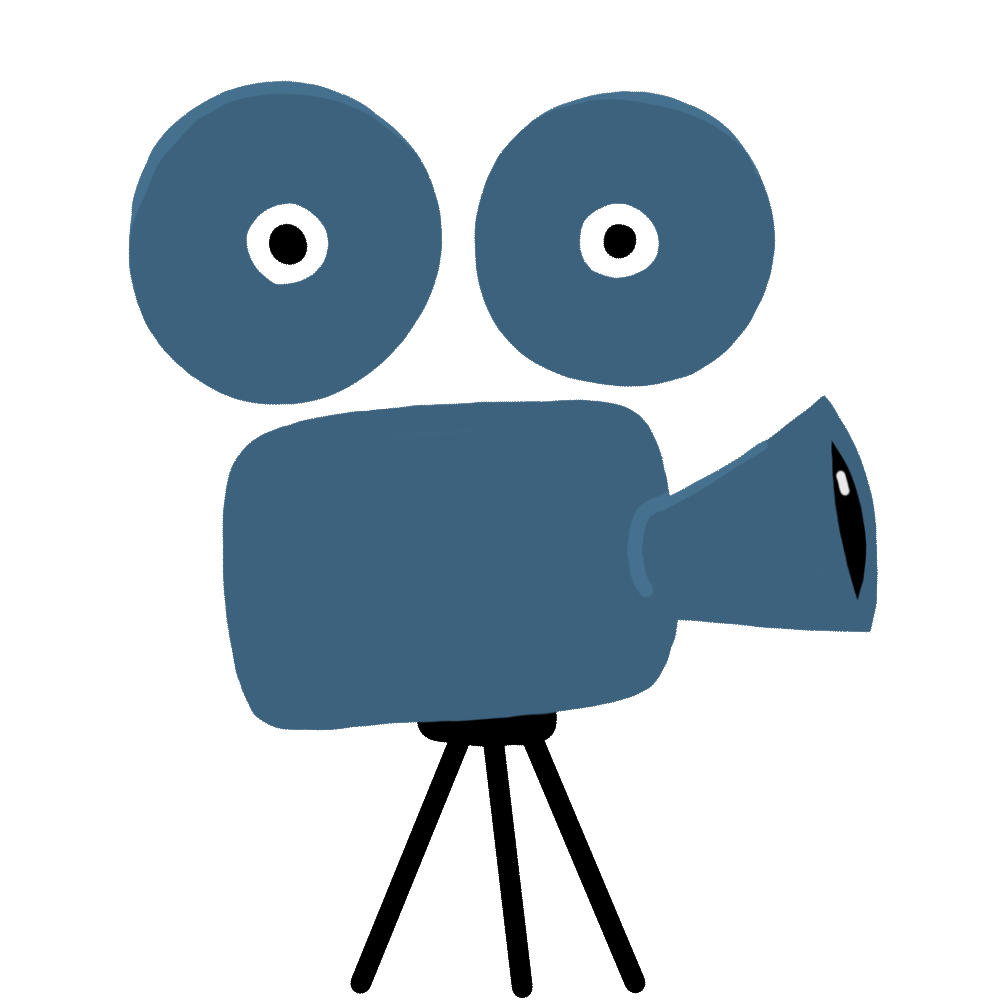
Course In Progress
Course still in development. Check back often for updates.
MECHANICAL Engineers: ADVANCED - Mastering Multiphysics CFD Simulations
Elevate your Computational Fluid Dynamics (CFD) expertise to the highest level with our “Advanced Computational Fluid Dynamics: Multiphysics Simulations in Mechanical Engineering” course. This intensive program is tailored for experienced CFD users ready to tackle the most complex fluid dynamics challenges in modern mechanical engineering.
Leveraging the power of ANSYS Fluent, this course delves deep into advanced multiphysics phenomena, equipping you with cutting-edge skills to innovate and optimize designs across various industries. From aerospace to chemical processing, this course prepares you to lead in the field of advanced CFD applications.
Course Overview: 10 Advanced CFD Modules
Our MECHANICAL Engineers: ADVANCED course comprises ten meticulously crafted modules, each focusing on a critical area of advanced CFD simulation. This comprehensive approach ensures you’re prepared to handle the most challenging fluid dynamics problems in your professional career.
1. Eulerian Two-Phase Flow in Moving Geometries
Master complex multiphase simulations with dynamic boundaries:
- Advanced Eulerian modeling techniques for two-phase flows
- Simulating fluid interactions in moving and deforming geometries
- Applications in automotive and aerospace industries
2. Flow Behavior in Porous Media
Unravel the complexities of fluid transport through porous structures:
- Advanced modeling techniques for porous media flow
- Simulating heat and mass transfer in porous systems
- Applications in filtration, oil and gas recovery, and biomedical engineering
Specialized Industrial Applications
Dive into unique and challenging industrial CFD scenarios:
3. Pipeline Pigging Simulations
Explore advanced techniques for modeling complex pipeline operations:
- Simulating dynamic interactions between pigs and multiphase fluids
- Analyzing cleaning and inspection processes in pipelines
- Optimizing pigging operations for improved efficiency and safety
4. Discrete Phase Modeling (DPM) for Particle Trapping
Master advanced particle dynamics simulations:
- Implementing sophisticated DPM techniques in ANSYS Fluent
- Analyzing particle trajectories and trapping mechanisms
- Applications in air filtration, cyclone separators, and pollution control
Advanced Multiphase Flow Modeling
Tackle the most challenging multiphase flow scenarios:
5. Three-Phase Flow in Fuel Injectors
Simulate complex fuel injection processes:
- Modeling interactions between liquid fuel, air, and fuel vapor
- Analyzing spray formation and atomization processes
- Optimizing injector designs for improved engine performance
6. Rotating Machinery: Centrifugal Blower Analysis
Master advanced turbomachinery simulations:
- Implementing moving reference frame and sliding mesh techniques
- Analyzing flow patterns and performance characteristics in blowers
- Optimizing blade designs for enhanced efficiency
Compressible Flow and Shock Wave Analysis
Dive into high-speed flow simulations and shock wave modeling:
7. Compressible Flow in Centrifugal Compressors
Explore advanced compressible flow modeling in rotating systems:
- Simulating transonic and supersonic flows in compressor stages
- Analyzing shock formation and propagation in impellers
- Optimizing compressor designs for maximum efficiency
8. Multiphase Flow in Venturi Tubes
Master complex multiphase flow simulations in convergent-divergent geometries:
- Modeling gas-liquid flows through Venturi tubes
- Analyzing phase interactions and cavitation phenomena
- Applications in flow measurement and fluid acceleration processes
Dynamic Fluid Behavior and Supersonic Flow
Conclude with cutting-edge simulations in fluid dynamics:
9. Dynamic Fluid Behavior in Rotating Tanks
Simulate complex free surface flows in rotating systems:
- Modeling sloshing and wave formation in rotating containers
- Analyzing fluid-structure interactions in dynamic systems
- Applications in spacecraft fuel tanks and industrial mixing processes
10. Supersonic Nozzle Flow with Shock Waves
Master high-speed flow and shock wave simulations:
- Advanced modeling of supersonic and hypersonic flows
- Analyzing shock wave formation, interaction, and control
- Applications in aerospace propulsion and high-speed aerodynamics
Why Choose Our MECHANICAL Engineers: ADVANCED Course?
This course offers unparalleled advantages for CFD specialists:
- In-depth exploration of 10 advanced multiphysics CFD applications
- Hands-on experience with cutting-edge ANSYS Fluent features
- Real-world, complex engineering scenarios for practical skill development
- Comprehensive training in advanced numerical methods and physics modeling
By enrolling in our MECHANICAL Engineers: ADVANCED course, you’ll:
- Gain mastery over the most challenging fluid dynamics problems
- Develop expertise in advanced multiphase and compressible flow modeling
- Acquire skills to innovate and optimize designs in various industries
- Position yourself as a leader in the field of computational fluid dynamics
Join us to push the boundaries of CFD simulation and become a true expert in advanced computational fluid dynamics for mechanical engineering applications!
Course Price: $3.00 / Month
Master practical CFD simulations using ANSYS Fluent across 10 diverse engineering applications. From heat exchangers to compressible flows, this comprehensive course equips intermediate mechanical engineers with the skills to tackle real-world fluid dynamics challenges. Enhance your simulation expertise and advance your career with hands-on, industry-relevant training.
Course Price: $1.00 / Month
Master the fundamentals of CFD simulation across 10 diverse mechanical engineering applications using ANSYS Fluent. Perfect for beginners, this hands-on course covers fluid dynamics, heat transfer, and aerodynamics through practical, real-world examples.
Subscribe
Benefits of subscribing to the course
- Complete access to All chapters
- Special discount
- Free access to all new and updated content
- Cancel subscription anytime
* You will have access to the course only until your subscription ends; after that, your subscription will be automatically renewed unless you cancel it.
Congratulations
Congratulations! You have successfully subscribed to the course.
You can now start learning the course by clicking the button "Start Learning".
You can manage your subscription like canceling or upgrading the subscription, adding or changing the payment method, etc by clicking the button "Manage Subscriptions".
Add Payment Method
Please enter your payment method details.