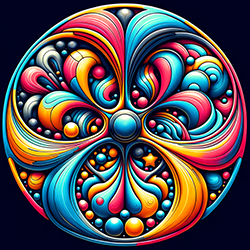
Multi-Phase Flow, Intermediate: CFD Simulation Training Course
Course Price: $3.00 / Month
Enhance your CFD skills with this comprehensive intermediate course on multiphase modeling in ANSYS Fluent. Master the VOF, Eulerian, and Mixture models through practical simulations and real-world applications. Ideal for engineers and researchers looking to advance their multiphase flow simulation capabilities.
By enrolling in this course, you will also gain access to the following courses for free:
Nano Fluid in Heat Source Channel CFD Simulation
Revolutionizing Heat Transfer: Nano Fluid in Heat Source Channel Mixture Multiphase CFD Simulation Welcome to the “Nano Fluid in Heat Source Channel Mixture Multiphase CFD Simulation” episode of our “MULTI-PHASE Flow: INTERMEDIATE” course. This comprehensive module introduces you to the cutting-edge world of nanofluid heat transfer, focusing on the complex dynamics of nanoparticle-enhanced fluids in channels with heat sources. Learn how to leverage the Mixture multiphase model in ANSYS Fluent to simulate and analyze the intricate flow and heat transfer characteristics of nanofluids, providing essential skills for engineers in thermal management, energy systems, and advanced cooling technologies. Understanding Nanofluids and Their Role in Enhanced Heat Transfer Before diving into the simulation specifics, let’s explore the fundamental concepts of nanofluids and their significance in modern heat transfer applications. Principles of Nanofluid Behavior in Heat Transfer Discover how nanofluids, consisting of base fluids with suspended nanoparticles, enhance heat transfer capabilities through unique thermal and flow properties. Applications of Nanofluids in Advanced Cooling Systems Learn about the diverse applications of nanofluids in improving the efficiency of heat exchangers, cooling systems, and thermal management solutions across various industries. Setting Up the Mixture Multiphase Model for Nanofluid Simulation This section focuses on configuring the Mixture model for accurate representation of nanofluid behavior: Defining Base Fluid and Nanoparticle Phases Gain insights into properly setting up the base fluid as the primary continuous phase and nanoparticles as the secondary dispersed phase, including material properties crucial for accurate nanofluid simulation. Configuring Phase Interactions and Mixture Properties Understand the critical aspects of modeling phase interactions and calculating effective properties of the nanofluid mixture based on nanoparticle volume fraction. Implementing the Heat Source Channel Simulation Domain Master the art of creating a representative environment for nanofluid heat transfer simulations: Defining Channel Geometry and Heat Source Integration Learn techniques for implementing a simulation domain that accurately represents a channel with an integrated heat source, including appropriate mesh strategies for capturing complex flow and thermal features. Incorporating Material Properties and Thermal Characteristics Explore methods for defining and implementing the thermal properties of both the base fluid and nanoparticles, crucial for accurate heat transfer modeling. Heat Transfer Modeling in Nanofluid Simulations Dive deep into the critical aspects of modeling heat transfer in nanofluid systems: Implementing Energy Equations for Nanofluid Mixtures Understand how to set up and configure energy equations that accurately capture heat transfer from the source to the nanofluid mixture, accounting for the unique properties of nanofluids. Modeling Enhanced Thermal Conductivity of Nanofluids Learn methods to incorporate the enhanced thermal conductivity of nanofluids into your simulation, a key factor in their improved heat transfer performance. Boundary Conditions and Turbulence Modeling Develop skills to accurately capture the flow and thermal conditions in nanofluid simulations: Specifying Inlet, Outlet, and Wall Conditions Master the techniques for defining appropriate boundary conditions, including inlet flow characteristics, outlet pressure conditions, and wall thermal specifications. Selecting and Configuring Turbulence Models for Nanofluid Flow Learn to choose and set up suitable turbulence models that account for the unique flow characteristics of nanofluids in channels with heat sources. Post-Processing and Performance Evaluation Develop expertise in extracting meaningful insights from your nanofluid heat transfer simulations: Visualizing Temperature Distributions and Velocity Profiles Master techniques for creating insightful visualizations of temperature distributions and velocity profiles throughout the channel, highlighting the enhanced heat transfer capabilities of nanofluids. Analyzing Nanoparticle Concentration Patterns and Heat Transfer Coefficients Learn to quantify and interpret nanoparticle concentration distributions and local heat transfer coefficients, crucial for assessing the performance of nanofluid-based cooling systems. Practical Applications and Engineering Relevance Connect simulation insights to real-world thermal management challenges: Optimizing Cooling System Design with Nanofluids Explore how CFD simulations of nanofluid heat transfer can inform the design of more efficient and compact cooling systems for electronics, power plants, and other high-heat applications. Assessing Nanofluid Performance in Various Heat Exchanger Configurations Understand how the principles learned in this module can contribute to evaluating and enhancing the performance of various heat exchanger designs using nanofluids. Why This Module is Essential for Intermediate Multiphase Flow Engineers This intermediate-level module offers a practical application of advanced CFD techniques in nanofluid heat transfer. By completing this simulation, you’ll gain valuable insights into: Advanced application of the Mixture multiphase model for simulating complex nanofluid behavior in heat transfer scenarios Essential CFD techniques for capturing enhanced thermal conductivity, flow patterns, and heat transfer coefficients in nanofluid systems Practical applications of nanofluid CFD analysis in thermal management, energy efficiency, and advanced cooling technologies By the end of this episode, you’ll have developed crucial skills in: Setting up and running nanofluid heat transfer simulations using ANSYS Fluent Interpreting simulation results to assess nanofluid performance in enhancing heat transfer in channels with heat sources Applying CFD insights to optimize thermal management solutions and cooling system designs This knowledge forms a solid foundation for engineers and researchers looking to specialize in advanced heat transfer technologies and multiphase flow analysis, providing a springboard for innovative cooling solutions and energy-efficient thermal management systems. Join us on this exciting journey into the world of nanofluid heat transfer CFD simulation, and take your next steps towards becoming an expert in multiphase dynamics modeling for cutting-edge thermal management applications!
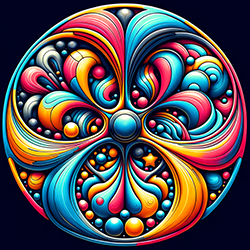
Multi-Phase Flow, Intermediate: CFD Simulation Training Course
Course Price: $3.00 / Month
Enhance your CFD skills with this comprehensive intermediate course on multiphase modeling in ANSYS Fluent. Master the VOF, Eulerian, and Mixture models through practical simulations and real-world applications. Ideal for engineers and researchers looking to advance their multiphase flow simulation capabilities.
Nano Fluid in Heat Source Channel CFD Simulation
Revolutionizing Heat Transfer: Nano Fluid in Heat Source Channel Mixture Multiphase CFD Simulation Welcome to the “Nano Fluid in Heat Source Channel Mixture Multiphase CFD Simulation” episode of our “MULTI-PHASE Flow: INTERMEDIATE” course. This comprehensive module introduces you to the cutting-edge world of nanofluid heat transfer, focusing on the complex dynamics of nanoparticle-enhanced fluids in channels with heat sources. Learn how to leverage the Mixture multiphase model in ANSYS Fluent to simulate and analyze the intricate flow and heat transfer characteristics of nanofluids, providing essential skills for engineers in thermal management, energy systems, and advanced cooling technologies. Understanding Nanofluids and Their Role in Enhanced Heat Transfer Before diving into the simulation specifics, let’s explore the fundamental concepts of nanofluids and their significance in modern heat transfer applications. Principles of Nanofluid Behavior in Heat Transfer Discover how nanofluids, consisting of base fluids with suspended nanoparticles, enhance heat transfer capabilities through unique thermal and flow properties. Applications of Nanofluids in Advanced Cooling Systems Learn about the diverse applications of nanofluids in improving the efficiency of heat exchangers, cooling systems, and thermal management solutions across various industries. Setting Up the Mixture Multiphase Model for Nanofluid Simulation This section focuses on configuring the Mixture model for accurate representation of nanofluid behavior: Defining Base Fluid and Nanoparticle Phases Gain insights into properly setting up the base fluid as the primary continuous phase and nanoparticles as the secondary dispersed phase, including material properties crucial for accurate nanofluid simulation. Configuring Phase Interactions and Mixture Properties Understand the critical aspects of modeling phase interactions and calculating effective properties of the nanofluid mixture based on nanoparticle volume fraction. Implementing the Heat Source Channel Simulation Domain Master the art of creating a representative environment for nanofluid heat transfer simulations: Defining Channel Geometry and Heat Source Integration Learn techniques for implementing a simulation domain that accurately represents a channel with an integrated heat source, including appropriate mesh strategies for capturing complex flow and thermal features. Incorporating Material Properties and Thermal Characteristics Explore methods for defining and implementing the thermal properties of both the base fluid and nanoparticles, crucial for accurate heat transfer modeling. Heat Transfer Modeling in Nanofluid Simulations Dive deep into the critical aspects of modeling heat transfer in nanofluid systems: Implementing Energy Equations for Nanofluid Mixtures Understand how to set up and configure energy equations that accurately capture heat transfer from the source to the nanofluid mixture, accounting for the unique properties of nanofluids. Modeling Enhanced Thermal Conductivity of Nanofluids Learn methods to incorporate the enhanced thermal conductivity of nanofluids into your simulation, a key factor in their improved heat transfer performance. Boundary Conditions and Turbulence Modeling Develop skills to accurately capture the flow and thermal conditions in nanofluid simulations: Specifying Inlet, Outlet, and Wall Conditions Master the techniques for defining appropriate boundary conditions, including inlet flow characteristics, outlet pressure conditions, and wall thermal specifications. Selecting and Configuring Turbulence Models for Nanofluid Flow Learn to choose and set up suitable turbulence models that account for the unique flow characteristics of nanofluids in channels with heat sources. Post-Processing and Performance Evaluation Develop expertise in extracting meaningful insights from your nanofluid heat transfer simulations: Visualizing Temperature Distributions and Velocity Profiles Master techniques for creating insightful visualizations of temperature distributions and velocity profiles throughout the channel, highlighting the enhanced heat transfer capabilities of nanofluids. Analyzing Nanoparticle Concentration Patterns and Heat Transfer Coefficients Learn to quantify and interpret nanoparticle concentration distributions and local heat transfer coefficients, crucial for assessing the performance of nanofluid-based cooling systems. Practical Applications and Engineering Relevance Connect simulation insights to real-world thermal management challenges: Optimizing Cooling System Design with Nanofluids Explore how CFD simulations of nanofluid heat transfer can inform the design of more efficient and compact cooling systems for electronics, power plants, and other high-heat applications. Assessing Nanofluid Performance in Various Heat Exchanger Configurations Understand how the principles learned in this module can contribute to evaluating and enhancing the performance of various heat exchanger designs using nanofluids. Why This Module is Essential for Intermediate Multiphase Flow Engineers This intermediate-level module offers a practical application of advanced CFD techniques in nanofluid heat transfer. By completing this simulation, you’ll gain valuable insights into: Advanced application of the Mixture multiphase model for simulating complex nanofluid behavior in heat transfer scenarios Essential CFD techniques for capturing enhanced thermal conductivity, flow patterns, and heat transfer coefficients in nanofluid systems Practical applications of nanofluid CFD analysis in thermal management, energy efficiency, and advanced cooling technologies By the end of this episode, you’ll have developed crucial skills in: Setting up and running nanofluid heat transfer simulations using ANSYS Fluent Interpreting simulation results to assess nanofluid performance in enhancing heat transfer in channels with heat sources Applying CFD insights to optimize thermal management solutions and cooling system designs This knowledge forms a solid foundation for engineers and researchers looking to specialize in advanced heat transfer technologies and multiphase flow analysis, providing a springboard for innovative cooling solutions and energy-efficient thermal management systems. Join us on this exciting journey into the world of nanofluid heat transfer CFD simulation, and take your next steps towards becoming an expert in multiphase dynamics modeling for cutting-edge thermal management applications!
-
Section 1
Bridge Pillars (VOF)
-
Mastering Bridge Hydraulics: Two-Phase Flow CFD Simulation of Water-Air Interaction Around Bridge Pillars Welcome to the “Bridge Pillars External Two-Phase Flow CFD Simulation” episode of our “MULTI-PHASE Flow: INTERMEDIATE” course. This comprehensive module introduces you to the complex world of river hydraulics and bridge engineering, focusing on the interaction between water flow and bridge pillars. Learn how to leverage the Volume of Fluid (VOF) model in ANSYS Fluent to simulate and analyze free surface flows, providing essential skills for engineers in civil engineering, hydraulics, and environmental sectors. Understanding the Volume of Fluid (VOF) Model in Bridge Hydraulics Before diving into the simulation specifics, let’s explore the fundamental concepts of the VOF approach in the context of river flow dynamics around structures. Principles of VOF Modeling for Free Surface Flows Discover how the VOF model accurately represents the interface between water and air, capturing the complex behavior of river flow around bridge pillars. Applications of Two-Phase Flow Simulations in Hydraulic Engineering Learn about the diverse applications of VOF modeling in bridge design, river engineering, and flood risk assessment. Setting Up the VOF Model for Bridge Pillar Simulation This section focuses on configuring the VOF model for accurate representation of water-air interaction: Defining Primary and Secondary Phases Gain insights into properly setting up water and air as the two phases in your simulation, including material properties and interaction parameters. Configuring Surface Tension and Interface Sharpening Understand the crucial aspects of surface tension modeling and interface capture techniques for realistic free surface representation. Implementing Boundary Conditions for Realistic River Flow Scenarios Master the art of defining realistic conditions for your two-phase bridge pillar simulation: Setting Up Velocity Inlet and Pressure Outlet Learn to configure appropriate inlet velocities and outlet conditions to mimic real-world river flow characteristics. Defining Wall Conditions for Pillars and Riverbed Explore techniques for accurately representing the no-slip conditions on bridge pillars and the riverbed, crucial for capturing flow separation and vortex formation. Turbulence Modeling in Multiphase External Flows Dive deep into the critical settings that ensure accurate capture of turbulent behavior in river flows: Selecting Appropriate Turbulence Models Understand how to choose and configure the right turbulence model, such as k-epsilon or k-omega SST, for external multiphase flows. Adjusting Turbulence Parameters for Free Surface Flows Learn to fine-tune turbulence model parameters to accurately represent the complex interactions at the water-air interface and around bridge pillars. Solution Methods and Convergence Strategies Develop skills to ensure robust and accurate solutions for your bridge pillar simulation: Choosing Discretization Schemes for VOF Simulations Master the selection of appropriate spatial and temporal discretization schemes for capturing sharp interfaces and dynamic flow behavior. Implementing Pressure-Velocity Coupling Algorithms Learn methods to select and configure pressure-velocity coupling algorithms suitable for transient, multiphase simulations. Transient Simulation Setup and Execution Explore the key aspects of time-dependent simulation for capturing dynamic flow phenomena: Determining Appropriate Time Step Sizes Discover how to select time step sizes that balance accuracy and computational efficiency in free surface flow simulations. Configuring Convergence Criteria and Monitoring Learn to set up and monitor convergence criteria to ensure the reliability of your transient simulation results. Post-Processing and Result Interpretation Develop expertise in extracting meaningful insights from your bridge pillar simulations: Visualizing Free Surface and Flow Patterns Master techniques for creating insightful visualizations of the water surface elevation, velocity profiles, and pressure distributions around bridge pillars. Analyzing Vortex Shedding Phenomena Learn to quantify and interpret vortex shedding behavior behind bridge pillars, crucial for assessing structural loads and scour potential. Practical Applications and Engineering Relevance Connect simulation insights to real-world engineering challenges: Assessing Hydraulic Loads on Bridge Structures Explore how CFD simulations can inform the design and risk assessment of bridges under various flow conditions. Evaluating Scour Potential and Mitigation Strategies Understand how the principles learned in this module can contribute to the development of effective scour prevention measures for bridge foundations. Why This Module is Essential for Intermediate Multiphase Flow Engineers This intermediate-level module offers a practical application of advanced CFD techniques in hydraulic engineering. By completing this simulation, you’ll gain valuable insights into: Advanced application of the VOF model for simulating complex free surface flows around structures Essential CFD techniques for capturing water-air interactions, turbulence, and vortex shedding in river systems Practical applications of multiphase CFD analysis in bridge design, river engineering, and flood risk assessment By the end of this episode, you’ll have developed crucial skills in: Setting up and running two-phase flow simulations of bridge pillars using the VOF model in ANSYS Fluent Interpreting transient simulation results to assess flow patterns, free surface behavior, and hydraulic loads on structures Applying CFD insights to enhance understanding and design in applications involving multiphase flows in hydraulic engineering This knowledge forms a solid foundation for engineers and researchers looking to specialize in hydraulic engineering and multiphase flow analysis, providing a springboard for advanced studies in fluid dynamics, structural engineering, and innovative river management technologies. Join us on this exciting journey into the world of bridge pillar two-phase flow CFD simulation, and take your next steps towards becoming an expert in multiphase dynamics modeling for critical civil and environmental engineering applications!
Episode 1 28m 38s Free Episode
-
-
Section 2
Stepped Spillway (VOF)
-
Mastering Hydraulic Structures: Stepped Spillway CFD Simulation Using Volume of Fluid (VOF) Model Welcome to the “Stepped Spillway (Stair Spillway) CFD Simulation” episode of our “MULTI-PHASE Flow: INTERMEDIATE” course. This comprehensive module introduces you to the intricate world of dam engineering and hydraulic structures, focusing on the complex flow dynamics of stepped spillways. Learn how to leverage the Volume of Fluid (VOF) model in ANSYS Fluent to simulate and analyze free-surface flows with significant air entrainment, providing essential skills for engineers in hydraulic engineering, dam design, and water resources management. Understanding the Volume of Fluid (VOF) Model in Stepped Spillway Analysis Before diving into the simulation specifics, let’s explore the fundamental concepts of the VOF approach in the context of stepped spillway hydraulics. Principles of VOF Modeling for Free-Surface Flows with Air Entrainment Discover how the VOF model accurately represents the complex interaction between water and air over stepped spillways, capturing crucial phenomena like air entrainment and energy dissipation. Applications of Stepped Spillway Simulations in Dam Engineering Learn about the diverse applications of VOF modeling in spillway design, energy dissipation assessment, and overall dam safety analysis. Setting Up the VOF Model for Stepped Spillway Simulation This section focuses on configuring the VOF model for accurate representation of water-air interaction in spillways: Defining Primary and Secondary Phases Gain insights into properly setting up water and air as the two phases in your simulation, including material properties and interaction parameters crucial for spillway flow. Configuring Phase Interactions and Surface Tension Effects Understand the critical aspects of modeling phase interactions and surface tension for realistic representation of free-surface flow over steps. Implementing Boundary Conditions for Realistic Spillway Flow Scenarios Master the art of defining realistic conditions for your stepped spillway simulation: Setting Up Velocity or Mass Flow Inlet Learn to configure appropriate inlet conditions to mimic real-world spillway discharge characteristics under various operational scenarios. Defining Wall Conditions for Spillway Steps and Channel Explore techniques for accurately representing the no-slip conditions on spillway steps and channel walls, crucial for capturing flow separation and energy dissipation. Turbulence Modeling in Highly Aerated Flows Dive deep into the critical settings that ensure accurate capture of turbulent behavior in stepped spillway flows: Selecting Appropriate Turbulence Models for Spillway Flows Understand how to choose and configure the right turbulence model, such as k-epsilon or k-omega SST, for highly turbulent, free-surface flows with air entrainment. Implementing Air Entrainment Models Learn to incorporate air entrainment modeling techniques to accurately represent this crucial aspect of stepped spillway performance. Transient Simulation Setup and Solution Strategies Develop skills to ensure robust and accurate solutions for your stepped spillway simulation: Determining Optimal Time Step Sizes Master the selection of appropriate time step sizes to capture rapid flow transitions and potential hydraulic jumps over spillway steps. Implementing Adaptive Time-Stepping Techniques Learn methods to implement adaptive time-stepping for efficiently handling varying flow regimes along the spillway. Post-Processing and Performance Evaluation Explore the key aspects of result interpretation and spillway performance assessment: Visualizing Flow Patterns and Air Entrainment Discover techniques for creating insightful visualizations of water surface profiles, velocity distributions, and air concentration patterns along the spillway. Quantifying Energy Dissipation and Hydraulic Efficiency Learn to calculate and interpret energy dissipation rates and overall hydraulic efficiency of the stepped spillway design. Comparative Analysis and Design Optimization Develop expertise in leveraging simulation results for spillway design improvement: Comparing CFD Results with Empirical Formulas Master techniques for validating your simulation results against established empirical relationships for stepped spillway performance. Identifying Design Optimization Opportunities Learn to use CFD insights to propose and evaluate design modifications for enhanced spillway efficiency and safety. Practical Applications and Engineering Relevance Connect simulation insights to real-world engineering challenges: Assessing Spillway Performance Under Extreme Flow Conditions Explore how CFD simulations can inform the evaluation of spillway behavior during flood events and guide safety assessments. Optimizing Step Geometry for Enhanced Energy Dissipation Understand how the principles learned in this module can contribute to the development of more efficient stepped spillway designs for various dam types. Why This Module is Essential for Intermediate Multiphase Flow Engineers This intermediate-level module offers a practical application of advanced CFD techniques in hydraulic structure design. By completing this simulation, you’ll gain valuable insights into: Advanced application of the VOF model for simulating complex free-surface flows with significant air entrainment Essential CFD techniques for capturing turbulence, energy dissipation, and flow regime transitions in stepped spillways Practical applications of multiphase CFD analysis in dam engineering, spillway design, and hydraulic structure optimization By the end of this episode, you’ll have developed crucial skills in: Setting up and running stepped spillway simulations using the VOF model in ANSYS Fluent Interpreting transient simulation results to assess flow patterns, energy dissipation, and overall spillway performance Applying CFD insights to enhance understanding and design of complex hydraulic structures This knowledge forms a solid foundation for engineers and researchers looking to specialize in hydraulic engineering and multiphase flow analysis, providing a springboard for advanced studies in dam safety, energy dissipation systems, and innovative spillway designs. Join us on this exciting journey into the world of stepped spillway CFD simulation, and take your next steps towards becoming an expert in multiphase dynamics modeling for critical water resources and dam engineering applications!
Episode 1 20m 58s
-
-
Section 3
Waterfall (VOF)
-
Mastering Natural Hydraulics: Waterfall Two-Phase Flow CFD Simulation Using Volume of Fluid (VOF) Model Welcome to the “Waterfall Using Two-Phase Flow CFD Simulation” episode of our “MULTI-PHASE Flow: INTERMEDIATE” course. This comprehensive module introduces you to the fascinating world of natural hydraulics, focusing on the complex flow dynamics of waterfalls. Learn how to leverage the Volume of Fluid (VOF) model in ANSYS Fluent to simulate and analyze free-surface flows with significant air-water interaction, providing essential skills for engineers in environmental engineering, landscape design, and hydropower sectors. Understanding the Volume of Fluid (VOF) Model in Waterfall Analysis Before diving into the simulation specifics, let’s explore the fundamental concepts of the VOF approach in the context of waterfall hydraulics. Principles of VOF Modeling for Free-Surface Waterfall Flows Discover how the VOF model accurately represents the complex interaction between water and air in waterfall scenarios, capturing crucial phenomena like free-surface deformation and air entrainment. Applications of Waterfall Simulations in Environmental and Engineering Fields Learn about the diverse applications of VOF modeling in landscape design, environmental impact assessment, and small-scale hydropower projects. Setting Up the VOF Model for Waterfall Simulation This section focuses on configuring the VOF model for accurate representation of water-air interaction in waterfalls: Defining Primary and Secondary Phases Gain insights into properly setting up water and air as the two phases in your simulation, including material properties and interaction parameters crucial for waterfall flow. Configuring Phase Interactions and Surface Tension Effects Understand the critical aspects of modeling phase interactions and surface tension for realistic representation of free-surface flow in waterfalls. Implementing Boundary Conditions for Realistic Waterfall Scenarios Master the art of defining realistic conditions for your waterfall simulation: Setting Up Velocity Inlet for Water Flow Learn to configure appropriate inlet conditions to mimic real-world waterfall characteristics under various flow rates and geometries. Defining Pressure Outlet and Atmospheric Conditions Explore techniques for accurately representing the air domain and outlet conditions, crucial for capturing the interaction between the falling water and surrounding air. Turbulence Modeling in Highly Aerated Waterfall Flows Dive deep into the critical settings that ensure accurate capture of turbulent behavior in waterfall flows: Selecting Appropriate Turbulence Models for Waterfall Dynamics Understand how to choose and configure the right turbulence model, such as k-epsilon or k-omega SST, for highly turbulent, free-surface flows with significant air entrainment. Implementing Advanced Turbulence Parameters for Plunge Pool Dynamics Learn to fine-tune turbulence model parameters to accurately represent the complex flow patterns and energy dissipation in the plunge pool at the base of the waterfall. Solution Methods and Convergence Strategies for Waterfall Simulations Develop skills to ensure robust and accurate solutions for your waterfall simulation: Choosing Optimal Discretization Schemes Master the selection of appropriate spatial and temporal discretization schemes to capture the dynamic nature of waterfall flows accurately. Implementing Pressure-Velocity Coupling for Free-Surface Flows Learn methods to select and configure pressure-velocity coupling algorithms suitable for the challenging free-surface flow scenario of a waterfall. Post-Processing and Visualization Techniques Explore the key aspects of result interpretation and visualization for waterfall simulations: Creating Compelling Water Surface and Velocity Visualizations Discover techniques for generating visually striking and informative representations of water surface profiles and velocity distributions in your waterfall simulation. Analyzing Air Entrainment Patterns Learn to quantify and visualize air entrainment in the plunge pool, a crucial aspect for understanding energy dissipation in waterfall systems. Advanced Analysis of Plunge Pool Dynamics Develop expertise in analyzing the complex flow patterns at the base of the waterfall: Investigating Turbulence Characteristics in the Plunge Pool Master techniques for analyzing turbulence intensity, vortex formation, and energy dissipation rates in the plunge pool region. Assessing Scour Potential and Sediment Transport Learn to use CFD results to evaluate potential erosion and sediment transport patterns in natural waterfall systems. Practical Applications and Environmental Relevance Connect simulation insights to real-world environmental and engineering challenges: Applying CFD Insights to Landscape Design and Conservation Explore how waterfall simulations can inform landscape architecture decisions and conservation efforts in natural water systems. Evaluating Potential for Small-Scale Hydropower Projects Understand how the principles learned in this module can contribute to the assessment and design of micro-hydropower installations utilizing natural waterfalls. Why This Module is Essential for Intermediate Multiphase Flow Engineers This intermediate-level module offers a practical application of advanced CFD techniques in natural hydraulics. By completing this simulation, you’ll gain valuable insights into: Advanced application of the VOF model for simulating complex free-surface flows with significant air-water interaction Essential CFD techniques for capturing turbulence, air entrainment, and energy dissipation in waterfall systems Practical applications of multiphase CFD analysis in environmental engineering, landscape design, and small-scale hydropower assessment By the end of this episode, you’ll have developed crucial skills in: Setting up and running waterfall simulations using the VOF model in ANSYS Fluent Interpreting simulation results to assess flow patterns, air entrainment, and plunge pool dynamics Applying CFD insights to enhance understanding of natural waterfall systems and their potential engineering applications This knowledge forms a solid foundation for engineers and researchers looking to specialize in environmental fluid dynamics and multiphase flow analysis, providing a springboard for advanced studies in natural hydraulics, eco-hydraulics, and innovative water resource management techniques. Join us on this exciting journey into the world of waterfall CFD simulation, and take your next steps towards becoming an expert in multiphase dynamics modeling for critical environmental and water resource applications!
Episode 1 13m 14s
-
-
Section 4
Pigging (VOF)
-
Mastering Pipeline Maintenance: Pigging Oil Flow CFD Simulation Using Volume of Fluid (VOF) Model Welcome to the “Pigging Oil Flow in a Pipeline CFD Simulation” episode of our “MULTI-PHASE Flow: INTERMEDIATE” course. This comprehensive module introduces you to the intricate world of pipeline maintenance in the oil and gas industry, focusing on the complex process of pipeline pigging. Learn how to leverage the Volume of Fluid (VOF) model in ANSYS Fluent to simulate and analyze multiphase flows with moving objects, providing essential skills for engineers in petroleum engineering, pipeline maintenance, and fluid dynamics sectors. Understanding the Volume of Fluid (VOF) Model in Pipeline Pigging Analysis Before diving into the simulation specifics, let’s explore the fundamental concepts of the VOF approach in the context of pipeline pigging operations. Principles of VOF Modeling for Multiphase Flows with Moving Objects Discover how the VOF model accurately represents the complex interaction between oil, gas, and potentially debris or water in a pipeline, capturing crucial phenomena like phase separation and interface dynamics with a moving pig. Applications of Pipeline Pigging Simulations in Oil and Gas Industry Learn about the diverse applications of VOF modeling in pipeline maintenance, efficiency optimization, and safety assessment in oil and gas transportation systems. Setting Up the VOF Model for Pipeline Pigging Simulation This section focuses on configuring the VOF model for accurate representation of multiphase flow in pipelines: Defining Primary and Secondary Phases Gain insights into properly setting up oil, gas, and potential contaminants as multiple phases in your simulation, including material properties and interaction parameters crucial for pipeline flow. Configuring Phase Interactions and Interface Dynamics Understand the critical aspects of modeling phase interactions and interface behavior for realistic representation of multiphase flow during pigging operations. Implementing Moving Mesh Technique for Pig Motion Master the art of simulating moving objects within fluid domains: Setting Up Dynamic Mesh Zones Learn to configure appropriate mesh motion techniques to accurately represent the pig’s movement through the pipeline. Defining Mesh Update Methods and Parameters Explore techniques for maintaining mesh quality and stability during pig motion, crucial for capturing accurate flow dynamics around the moving object. Boundary Conditions and Fluid-Structure Interaction Dive deep into the critical settings that ensure accurate representation of pipeline flow and pig interaction: Specifying Inlet and Outlet Conditions for Multiphase Flow Understand how to define and configure appropriate boundary conditions for oil and gas phases at pipeline inlets and outlets. Implementing Fluid-Structure Interaction at Pig Surface Learn to set up the interface between the moving pig and surrounding fluids, crucial for capturing the pig’s effect on flow patterns and phase distribution. Turbulence Modeling in Pipeline Pigging Scenarios Develop skills to accurately capture complex flow patterns in pigging operations: Selecting Appropriate Turbulence Models for Multiphase Pipeline Flow Master the selection of suitable turbulence models, such as k-epsilon or k-omega SST, for capturing the complex flow patterns around the moving pig and in its wake. Fine-tuning Turbulence Parameters for Enhanced Accuracy Learn methods to adjust turbulence model parameters to account for the unique flow characteristics induced by the pig’s motion in a confined pipeline environment. Transient Simulation Setup and Solution Strategies Explore the key aspects of time-dependent simulation for capturing dynamic pigging processes: Determining Optimal Time Step Sizes Discover techniques for selecting appropriate time step sizes to capture the rapid flow changes and phase interactions during pig passage. Implementing Adaptive Time-Stepping Techniques Learn to implement adaptive time-stepping methods to efficiently handle varying flow regimes and pig velocities throughout the simulation. Post-Processing and Performance Evaluation Develop expertise in extracting meaningful insights from your pipeline pigging simulations: Visualizing Flow Patterns and Phase Distribution Master techniques for creating insightful visualizations of velocity profiles, pressure distributions, and phase separation patterns during pigging operations. Analyzing Pressure Differentials and Cleaning Efficiency Learn to quantify and interpret pressure drops across the pig, assess potential cleaning efficiency, and evaluate overall pigging performance. Practical Applications and Industrial Relevance Connect simulation insights to real-world engineering challenges: Optimizing Pigging Operations for Enhanced Pipeline Efficiency Explore how CFD simulations can inform the design of pigging schedules, pig geometry, and operational parameters for improved pipeline maintenance. Assessing Safety and Risk Factors in Pigging Processes Understand how the principles learned in this module can contribute to safety assessments and risk mitigation strategies in pipeline operations. Why This Module is Essential for Intermediate Multiphase Flow Engineers This intermediate-level module offers a practical application of advanced CFD techniques in pipeline maintenance. By completing this simulation, you’ll gain valuable insights into: Advanced application of the VOF model for simulating complex multiphase flows with moving objects Essential CFD techniques for capturing turbulence, phase separation, and fluid-structure interaction in pipeline systems Practical applications of multiphase CFD analysis in oil and gas transportation, pipeline maintenance, and efficiency optimization By the end of this episode, you’ll have developed crucial skills in: Setting up and running pipeline pigging simulations using the VOF model and moving mesh techniques in ANSYS Fluent Interpreting transient simulation results to assess flow patterns, pressure differentials, and pigging effectiveness Applying CFD insights to enhance understanding and optimization of pipeline maintenance operations This knowledge forms a solid foundation for engineers and researchers looking to specialize in petroleum engineering and multiphase flow analysis, providing a springboard for advanced studies in pipeline dynamics, maintenance technologies, and innovative oil and gas transportation solutions. Join us on this exciting journey into the world of pipeline pigging CFD simulation, and take your next steps towards becoming an expert in multiphase dynamics modeling for critical oil and gas industry applications!
Episode 1 18m 17s
-
-
Section 5
Open Channel (VOF)
-
Mastering River Hydraulics: Open Channel Two-Phase Flow in Rough Rivers CFD Simulation Welcome to the “Open Channel Two-Phase Flow in Rough Rivers CFD Simulation” episode of our “MULTI-PHASE Flow: INTERMEDIATE” course. This comprehensive module introduces you to the intricate world of river hydraulics, focusing on the complex dynamics of open-channel two-phase flow in rough river beds. Learn how to leverage both the Volume of Fluid (VOF) and Open Channel Flow models in ANSYS Fluent to simulate and analyze multiphase flows in natural river systems, providing essential skills for engineers in hydraulic engineering, environmental science, and water resource management sectors. Understanding the Combined VOF and Open Channel Flow Models in River Analysis Before diving into the simulation specifics, let’s explore the fundamental concepts of this hybrid approach in the context of rough river flow dynamics. Principles of VOF Modeling for Water-Air Interface Capture Discover how the VOF model accurately represents the complex interaction between water and air in open channel flows, capturing crucial phenomena like free surface deformation and potential air entrainment. Advantages of the Open Channel Flow Model for River Hydraulics Learn about the specialized treatment of open channel hydraulics provided by the Open Channel Flow model and its synergy with the VOF approach in representing natural river systems. Setting Up the Hybrid Model for Rough River Simulation This section focuses on configuring the combined VOF and Open Channel Flow models for accurate representation of two-phase flow in rough rivers: Defining Water and Air Phases in the VOF Framework Gain insights into properly setting up water and air as the two phases in your simulation, including material properties and interaction parameters crucial for open channel flow. Configuring Open Channel Parameters for Natural River Systems Understand the critical aspects of setting up the Open Channel Flow model to accurately represent the hydraulic characteristics of rough river beds. Incorporating Rough River Bed Geometry Master the art of representing complex river bed topography in your simulation: Integrating Topographical Data into the CFD Domain Learn techniques for incorporating detailed river bed geometry into your simulation, using topographical survey data or digital elevation models. Implementing Simplified Roughness Models for Efficient Simulation Explore methods for representing bed roughness using simplified models when detailed topographical data is unavailable or computationally prohibitive. Boundary Conditions for Open Channel Two-Phase Flow Dive deep into the critical settings that ensure accurate representation of river flow conditions: Specifying Inlet and Outlet Conditions for River Flow Understand how to define and configure appropriate boundary conditions that satisfy both VOF and Open Channel Flow model requirements at river inlets and outlets. Implementing Wall Conditions for Rough River Beds Learn to set up the interface between the rough river bed and fluid phases, crucial for capturing the effects of bed roughness on flow patterns and turbulence. Turbulence Modeling in Rough Open Channel Flows Develop skills to accurately capture complex flow patterns in natural river systems: Selecting Appropriate Turbulence Models for Open Channel Hydraulics Master the selection of suitable turbulence models, such as k-epsilon or k-omega SST, for capturing the complex flow patterns induced by bed roughness and free surface dynamics. Fine-tuning Turbulence Parameters for Enhanced Accuracy Learn methods to adjust turbulence model parameters to account for the unique flow characteristics of rough open channel flows in natural river systems. Steady-State Simulation Setup and Solution Strategies Explore the key aspects of equilibrium state simulation for capturing stable river flow conditions: Determining Convergence Criteria for Steady-State Analysis Discover techniques for setting appropriate convergence criteria to ensure a stable representation of the water-air interface and flow patterns in the open channel. Implementing Relaxation Factors for Solution Stability Learn to implement relaxation techniques to enhance solution stability and convergence in complex open channel flow simulations. Post-Processing and Performance Evaluation Develop expertise in extracting meaningful insights from your rough river simulations: Visualizing Water Surface Profiles and Velocity Distributions Master techniques for creating insightful visualizations of water surface elevations, velocity profiles, and turbulence characteristics in rough open channel flows. Analyzing the Impact of Bed Roughness on Flow Dynamics Learn to quantify and interpret the effects of bed roughness on water depth, velocity distributions, and turbulence intensity in steady-state open channel configurations. Practical Applications and Environmental Relevance Connect simulation insights to real-world engineering and environmental challenges: Assessing Flood Risk and Inundation Patterns Explore how CFD simulations of rough rivers can inform flood risk assessment and management strategies in natural river systems. Evaluating Sediment Transport and River Morphology Understand how the principles learned in this module can contribute to studies of sediment transport processes and long-term river morphological changes. Why This Module is Essential for Intermediate Multiphase Flow Engineers This intermediate-level module offers a practical application of advanced CFD techniques in river hydraulics. By completing this simulation, you’ll gain valuable insights into: Advanced application of combined VOF and Open Channel Flow models for simulating complex two-phase flows in natural river systems Essential CFD techniques for capturing turbulence, free surface dynamics, and the effects of bed roughness in open channel flows Practical applications of multiphase CFD analysis in river engineering, environmental impact assessment, and water resource management By the end of this episode, you’ll have developed crucial skills in: Setting up and running open channel two-phase flow simulations of rough rivers using ANSYS Fluent Interpreting steady-state simulation results to assess flow patterns, water surface profiles, and the impact of bed roughness on river hydraulics Applying CFD insights to enhance understanding and management of natural river systems This knowledge forms a solid foundation for engineers and researchers looking to specialize in river engineering and multiphase flow analysis, providing a springboard for advanced studies in fluvial hydraulics, eco-hydraulics, and innovative river management technologies. Join us on this exciting journey into the world of open channel two-phase flow CFD simulation in rough rivers, and take your next steps towards becoming an expert in multiphase dynamics modeling for critical environmental and water resource applications!
Episode 1 28m 50s
-
-
Section 6
Tank Discharge (VOF)
-
Mastering Rotating Fluid Dynamics: Water Discharge of a Rotating Tank CFD Simulation Welcome to the “Water Discharge of a Rotating Tank CFD Simulation” episode of our “MULTI-PHASE Flow: INTERMEDIATE” course. This comprehensive module introduces you to the intricate world of rotating fluid systems, focusing on the complex dynamics of water discharge from a rotating tank. Learn how to leverage the Volume of Fluid (VOF) model in ANSYS Fluent to simulate and analyze multiphase flows in rotating reference frames, providing essential skills for engineers in process engineering, fluid machinery design, and industrial fluid dynamics sectors. Understanding the Volume of Fluid (VOF) Model in Rotating Tank Analysis Before diving into the simulation specifics, let’s explore the fundamental concepts of the VOF approach in the context of rotating tank discharge dynamics. Principles of VOF Modeling for Free Surface Capture in Rotating Systems Discover how the VOF model accurately represents the complex interaction between water and air in rotating tanks, capturing crucial phenomena like free surface deformation and centrifugal effects. Applications of Rotating Tank Discharge Simulations in Industry Learn about the diverse applications of VOF modeling in process equipment design, centrifugal separation processes, and fluid handling systems in various industries. Setting Up the VOF Model for Rotating Tank Discharge Simulation This section focuses on configuring the VOF model for accurate representation of two-phase flow in rotating tanks: Defining Water and Air Phases in the VOF Framework Gain insights into properly setting up water and air as the two phases in your simulation, including material properties and interaction parameters crucial for rotating flow systems. Configuring Phase Interactions and Surface Tension Effects Understand the critical aspects of modeling phase interactions and surface tension for realistic representation of free-surface behavior under rotational forces. Implementing Rotating Reference Frame for Tank Motion Master the art of simulating rotating fluid systems: Setting Up the Rotating Reference Frame Learn techniques for implementing a rotating reference frame to accurately capture the effects of tank rotation on fluid motion and discharge characteristics. Handling the Interface Between Rotating and Stationary Domains Explore methods for managing the transition between the rotating tank and the stationary discharge outlet, crucial for accurate flow representation. Modeling the Discharge Outlet and Boundary Conditions Dive deep into the critical settings that ensure accurate representation of the discharge process: Incorporating Discharge Outlet Geometry Understand how to integrate the discharge outlet into your simulation domain, ensuring proper representation of the flow exit point and its interaction with the rotating fluid. Specifying Time-Dependent Boundary Conditions Learn to define and configure appropriate time-varying boundary conditions for the tank walls, free surface, and discharge outlet to capture the dynamic nature of the process. Turbulence Modeling in Rotating Tank Discharge Develop skills to accurately capture complex flow patterns in rotating fluid systems: Selecting Appropriate Turbulence Models for Rotating Flows Master the selection of suitable turbulence models, such as k-epsilon or k-omega SST, for capturing the complex, time-varying flow patterns induced by rotation and discharge. Fine-tuning Turbulence Parameters for Enhanced Accuracy Learn methods to adjust turbulence model parameters to account for the unique flow characteristics of rotating tank systems during discharge. Transient Simulation Setup and Solution Strategies Explore the key aspects of time-dependent simulation for capturing dynamic discharge processes: Determining Optimal Time Step Sizes Discover techniques for selecting appropriate time step sizes to capture the rapid changes in free surface shape and discharge rates throughout the process. Implementing Adaptive Time-Stepping Techniques Learn to implement adaptive time-stepping methods to efficiently handle varying flow regimes during different stages of the discharge process. Post-Processing and Performance Evaluation Develop expertise in extracting meaningful insights from your rotating tank discharge simulations: Visualizing Time-Dependent Flow Patterns and Free Surface Evolution Master techniques for creating insightful animations and time-series visualizations of water surface profiles, velocity distributions, and pressure fields throughout the discharge process. Analyzing the Impact of Rotation Speed on Discharge Characteristics Learn to quantify and interpret the effects of rotation speed on discharge rates, water surface shape, and overall flow characteristics over time. Practical Applications and Industrial Relevance Connect simulation insights to real-world engineering challenges: Optimizing Rotating Equipment Design for Efficient Fluid Handling Explore how CFD simulations of rotating tank discharge can inform the design of centrifugal separators, mixing vessels, and other rotating fluid machinery. Assessing Performance and Safety in Industrial Processes Understand how the principles learned in this module can contribute to performance optimization and safety assessment in various industrial fluid handling processes. Why This Module is Essential for Intermediate Multiphase Flow Engineers This intermediate-level module offers a practical application of advanced CFD techniques in rotating fluid systems. By completing this simulation, you’ll gain valuable insights into: Advanced application of the VOF model for simulating complex two-phase flows in rotating reference frames Essential CFD techniques for capturing turbulence, free surface dynamics, and centrifugal effects in rotating tank systems Practical applications of multiphase CFD analysis in process engineering, equipment design, and industrial fluid dynamics By the end of this episode, you’ll have developed crucial skills in: Setting up and running transient simulations of water discharge from rotating tanks using ANSYS Fluent Interpreting time-dependent simulation results to assess flow patterns, discharge rates, and the impact of rotation on fluid behavior Applying CFD insights to enhance understanding and optimization of rotating fluid machinery and processes This knowledge forms a solid foundation for engineers and researchers looking to specialize in rotating fluid dynamics and multiphase flow analysis, providing a springboard for advanced studies in centrifugal separation technologies, mixing processes, and innovative fluid handling solutions. Join us on this exciting journey into the world of rotating tank discharge CFD simulation, and take your next steps towards becoming an expert in multiphase dynamics modeling for critical industrial and process engineering applications!
Episode 1 30m
-
-
Section 7
Cascade (EULERIAN)
-
Mastering Hydraulic Engineering: Cascade CFD Simulation Using Eulerian Multiphase Flow Model Welcome to the “Cascade CFD Simulation” episode of our “MULTI-PHASE Flow: INTERMEDIATE” course. This comprehensive module introduces you to the intricate world of hydraulic structures, focusing on the complex steady-state dynamics of water and air interaction in cascades. Learn how to leverage the Eulerian multiphase flow model in ANSYS Fluent to simulate and analyze multiphase flows in structured environments, providing essential skills for engineers in hydropower engineering, water feature design, and environmental hydraulics sectors. Understanding the Eulerian Multiphase Model in Cascade Flow Analysis Before diving into the simulation specifics, let’s explore the fundamental concepts of the Eulerian approach in the context of cascade flow dynamics. Principles of Eulerian Modeling for Water-Air Interactions in Cascades Discover how the Eulerian multiphase model accurately represents the complex interaction between water (primary continuous phase) and air (secondary dispersed phase) in cascade environments, capturing crucial phenomena like free surface behavior and air entrainment. Applications of Cascade Simulations in Hydraulic Engineering Learn about the diverse applications of Eulerian modeling in optimizing hydropower systems, designing aesthetic water features, and studying environmental flow structures. Setting Up the Eulerian Multiphase Model for Cascade Simulation This section focuses on configuring the Eulerian model for accurate representation of two-phase flow in cascades: Defining Water and Air Phases in the Eulerian Framework Gain insights into properly setting up water as the primary continuous phase and air as the secondary dispersed phase, including material properties and interaction parameters crucial for accurate cascade flow simulation. Configuring Phase Interactions and Interface Dynamics Understand the critical aspects of modeling phase interactions, including surface tension effects and momentum exchange, for realistic representation of water-air behavior in cascade structures. Implementing the Cascade Simulation Domain Master the art of creating a representative environment for cascade flow simulations: Defining the Cascade Geometry and Mesh Strategy Learn techniques for implementing a simulation domain that accurately represents a section of a cascade, including appropriate mesh refinement strategies for capturing complex flow features. Incorporating Structural Elements and Surface Roughness Explore methods for including detailed structural elements and surface roughness characteristics to simulate realistic flow patterns and energy dissipation in cascades. Turbulence Modeling in Cascade Flow Simulations Dive deep into the critical settings that ensure accurate representation of turbulent multiphase flow in cascades: Selecting Appropriate Turbulence Models for Cascade Flows Understand how to choose and configure suitable turbulence models, such as k-epsilon or k-omega SST, for capturing the complex flow patterns and energy dissipation in cascade structures. Fine-tuning Turbulence Parameters for Enhanced Accuracy Learn methods to adjust turbulence model parameters to account for the unique flow characteristics of cascades, including potential localized turbulence and air entrainment zones. Boundary Conditions and Free Surface Modeling Develop skills to accurately capture the steady-state flow conditions in cascade simulations: Specifying Inlet and Outlet Conditions Master the techniques for defining appropriate inlet and outlet boundary conditions that accurately represent the steady-state flow regime in cascades. Implementing Wall Treatments for Cascade Structures Learn to set up proper wall boundary conditions that account for the complex geometry and potential roughness of cascade surfaces. Capturing Steady-State Free Surface Behavior Discover methods for accurately modeling the steady-state free surface between water and air as it flows through the cascade, a critical aspect of multiphase cascade simulations. Post-Processing and Performance Evaluation Develop expertise in extracting meaningful insights from your cascade simulations: Visualizing Flow Patterns and Air Bubble Distribution Master techniques for creating insightful visualizations of flow patterns, air bubble distributions, and velocity profiles throughout the cascade structure. Analyzing Pressure Distributions and Energy Dissipation Learn to quantify and interpret pressure distributions, energy dissipation rates, and overall hydraulic performance of the cascade under steady-state conditions. Practical Applications and Engineering Relevance Connect simulation insights to real-world hydraulic engineering challenges: Optimizing Cascade Design for Hydropower Systems Explore how CFD simulations of cascades can inform the design of more efficient and effective hydropower structures, including spillways and energy dissipation systems. Enhancing Water Feature Aesthetics and Performance Understand how the principles learned in this module can contribute to the design of visually appealing and functionally optimized water features in landscape architecture and urban design. Why This Module is Essential for Intermediate Multiphase Flow Engineers This intermediate-level module offers a practical application of advanced CFD techniques in hydraulic engineering. By completing this simulation, you’ll gain valuable insights into: Advanced application of the Eulerian multiphase model for simulating complex water-air interactions in structured flow environments Essential CFD techniques for capturing turbulence, free surface behavior, and air entrainment in cascade structures Practical applications of multiphase CFD analysis in hydropower engineering, water feature design, and environmental hydraulics By the end of this episode, you’ll have developed crucial skills in: Setting up and running steady-state simulations of cascades using ANSYS Fluent Interpreting simulation results to assess flow patterns, air entrainment, and energy dissipation in cascade structures Applying CFD insights to enhance understanding and optimization of hydraulic structures and water features This knowledge forms a solid foundation for engineers and researchers looking to specialize in hydraulic engineering and multiphase flow analysis, providing a springboard for advanced studies in hydropower systems, environmental flow structures, and innovative water management solutions. Join us on this exciting journey into the world of cascade CFD simulation, and take your next steps towards becoming an expert in multiphase dynamics modeling for critical hydraulic engineering and water resource management applications!
Episode 1 20m 53s
-
-
Section 8
Sprayer Drone (EULERIAN)
-
Revolutionizing Precision Agriculture: Agricultural Drone Sprayer CFD Simulation Welcome to the “Agricultural Drone Sprayer CFD Simulation” episode of our “MULTI-PHASE Flow: INTERMEDIATE” course. This comprehensive module introduces you to the cutting-edge world of precision agriculture, focusing on the complex dynamics of drone-based crop spraying. Learn how to leverage the Eulerian multiphase flow model in ANSYS Fluent to simulate and analyze the intricate interactions between air and spray droplets in an agricultural field environment, providing essential skills for engineers in agricultural technology, drone design, and environmental science sectors. Understanding the Eulerian Multiphase Model in Agricultural Spray Analysis Before diving into the simulation specifics, let’s explore the fundamental concepts of the Eulerian approach in the context of agricultural drone spraying dynamics. Principles of Eulerian Modeling for Air-Droplet Interactions Discover how the Eulerian multiphase model accurately represents the complex interaction between air (continuous phase) and spray droplets (dispersed phase) in open field environments, capturing crucial phenomena like droplet dispersion and deposition. Applications of Drone Sprayer Simulations in Precision Agriculture Learn about the diverse applications of Eulerian modeling in optimizing spray patterns, minimizing drift, and enhancing overall efficiency in modern agricultural practices. Setting Up the Eulerian Multiphase Model for Drone Sprayer Simulation This section focuses on configuring the Eulerian model for accurate representation of two-phase flow in agricultural spraying: Defining Air and Droplet Phases in the Eulerian Framework Gain insights into properly setting up air as the primary continuous phase and spray droplets as the secondary dispersed phase, including material properties and interaction parameters crucial for accurate spray simulation. Configuring Phase Interactions and Droplet Behavior Understand the critical aspects of modeling phase interactions, including drag forces, turbulent dispersion, and potential evaporation effects for realistic representation of spray behavior in field conditions. Implementing the Agricultural Field Simulation Domain Master the art of creating a representative environment for agricultural spray simulations: Defining the Field Geometry and Mesh Strategy Learn techniques for implementing a simulation domain that accurately represents a section of an agricultural field, including appropriate mesh refinement strategies for capturing spray dynamics. Incorporating Crop Geometry and Ground Interactions Explore methods for including simplified crop geometries and ground surfaces to simulate realistic spray interception and deposition patterns. Modeling Drone Spray Nozzle Configuration and Boundary Conditions Dive deep into the critical settings that ensure accurate representation of the spraying process: Configuring Spray Nozzle Characteristics Understand how to define and implement spray nozzle outlets, including specifying flow rates, droplet size distributions, and initial velocities to match real-world agricultural drone sprayers. Specifying Appropriate Boundary Conditions Learn to define and configure suitable boundary conditions for the simulation domain, including inlet, outlet, and wall conditions that accurately represent open field environments. Turbulence Modeling in Agricultural Spray Simulations Develop skills to accurately capture complex flow patterns in outdoor spraying scenarios: Selecting Appropriate Turbulence Models for Open Field Spraying Master the selection of suitable turbulence models, such as k-epsilon or k-omega SST, for capturing the complex, time-varying flow patterns induced by drone movement and environmental factors. Fine-tuning Turbulence Parameters for Enhanced Accuracy Learn methods to adjust turbulence model parameters to account for the unique flow characteristics of agricultural spraying, including potential wind effects and drone-induced turbulence. Transient Simulation Setup and Solution Strategies Explore the key aspects of time-dependent simulation for capturing dynamic spraying processes: Determining Optimal Time Step Sizes Discover techniques for selecting appropriate time step sizes to capture the rapid changes in spray patterns and droplet trajectories throughout the spraying process. Implementing Adaptive Time-Stepping Techniques Learn to implement adaptive time-stepping methods to efficiently handle varying flow regimes during different stages of the spraying operation, including drone movement and changing environmental conditions. Post-Processing and Performance Evaluation Develop expertise in extracting meaningful insights from your agricultural drone sprayer simulations: Visualizing Spray Dispersion Patterns and Droplet Trajectories Master techniques for creating insightful visualizations of spray dispersion patterns, droplet trajectories, and deposition rates across the simulated field section. Analyzing Spray Coverage and Drift Characteristics Learn to quantify and interpret spray coverage efficiency, potential drift issues, and overall spraying performance under various operational and environmental conditions. Practical Applications and Agricultural Technology Relevance Connect simulation insights to real-world precision agriculture challenges: Optimizing Drone Sprayer Design for Enhanced Efficiency Explore how CFD simulations of agricultural drone sprayers can inform the design of more efficient and precise spraying systems, including nozzle configurations and flight patterns. Assessing Environmental Impact and Minimizing Chemical Drift Understand how the principles learned in this module can contribute to minimizing environmental impact, reducing chemical drift, and enhancing overall sustainability in agricultural spraying operations. Why This Module is Essential for Intermediate Multiphase Flow Engineers This intermediate-level module offers a practical application of advanced CFD techniques in agricultural technology. By completing this simulation, you’ll gain valuable insights into: Advanced application of the Eulerian multiphase model for simulating complex air-droplet interactions in open field environments Essential CFD techniques for capturing turbulence, droplet dispersion, and deposition patterns in agricultural spraying scenarios Practical applications of multiphase CFD analysis in precision agriculture, drone technology, and sustainable farming practices By the end of this episode, you’ll have developed crucial skills in: Setting up and running transient simulations of agricultural drone sprayers using ANSYS Fluent Interpreting time-dependent simulation results to assess spray patterns, coverage efficiency, and potential drift issues Applying CFD insights to enhance understanding and optimization of precision agriculture technologies This knowledge forms a solid foundation for engineers and researchers looking to specialize in agricultural fluid dynamics and multiphase flow analysis, providing a springboard for advanced studies in precision farming technologies, environmental impact assessment, and innovative crop protection solutions. Join us on this exciting journey into the world of agricultural drone sprayer CFD simulation, and take your next steps towards becoming an expert in multiphase dynamics modeling for critical agricultural technology and environmental applications!
Episode 1 12m 21s
-
-
Section 9
Sludge Flow (EULERIAN)
-
Mastering Multiphase Pipeline Dynamics: Slug Flow CFD Simulation Using Eulerian Approach Welcome to the “Slug Flow CFD Simulation” episode of our “MULTI-PHASE Flow: INTERMEDIATE” course. This comprehensive module introduces you to the complex world of slug flow, a critical phenomenon in gas-liquid pipeline transport. Learn how to leverage the Eulerian multiphase flow model in Ansys Fluent to simulate and analyze the intricate dynamics of slug flow, providing essential skills for engineers in oil and gas, chemical processing, and industrial fluid transport sectors. Understanding Slug Flow and Its Industrial Significance Before diving into the simulation specifics, let’s explore the fundamental concepts of slug flow and its importance in various industrial applications. Characteristics of Slug Flow in Multiphase Transport Discover the unique features of slug flow, including alternating liquid slugs and gas pockets, and understand why it’s a crucial consideration in pipeline design and operation. Industrial Applications and Challenges of Slug Flow Learn about the diverse industries affected by slug flow, from oil and gas production to chemical processing, and the challenges it poses to equipment and process efficiency. Fundamentals of the Eulerian Multiphase Model for Slug Flow Simulation This section focuses on the theoretical background of using the Eulerian approach for slug flow modeling: Principles of Eulerian Multiphase Modeling Gain insights into the Eulerian framework for representing multiple phases and their interactions, crucial for accurate slug flow simulation. Advantages of Eulerian Approach in Slug Flow Analysis Understand why the Eulerian model is particularly suited for capturing the complex phase interactions and flow patterns characteristic of slug flow. Configuring Eulerian Multiphase Models in Ansys Fluent Master the art of setting up your simulation environment for slug flow analysis: Defining Gas and Liquid Phases Learn techniques for properly defining and characterizing the gas and liquid phases involved in slug flow, including material properties and interaction parameters. Implementing Phase Interaction Models Explore methods for setting up phase interaction models that accurately capture the dynamics between gas and liquid phases in slug flow regimes. Boundary Conditions and Initial Setup for Slug Flow Simulation Dive deep into the critical settings that ensure accurate representation of slug flow conditions: Specifying Inlet and Outlet Conditions Understand how to define appropriate inlet and outlet boundary conditions that promote the development and propagation of slug flow in your simulation domain. Setting Up Initial Flow Conditions Learn to establish initial conditions that facilitate the formation of slug flow patterns, crucial for achieving realistic simulation results. Turbulence Modeling in Slug Flow Simulations Develop skills to accurately capture the complex turbulent nature of slug flow: Selecting Appropriate Turbulence Models Master the selection of suitable turbulence models, such as k-epsilon or k-omega SST, for capturing the intricate turbulent structures in slug flow. Fine-tuning Turbulence Parameters Learn methods to adjust turbulence model parameters to account for the unique flow characteristics of slug flow regimes in pipelines. Post-Processing and Result Interpretation Develop expertise in extracting meaningful insights from your slug flow simulations: Visualizing Phase Distribution and Velocity Profiles Master techniques for creating insightful visualizations of phase distribution patterns and velocity profiles characteristic of slug flow. Analyzing Slug Characteristics Learn to quantify and interpret key slug flow parameters, including slug frequency, length, and velocity, crucial for pipeline design and operation. Advanced Analysis Techniques for Slug Flow Explore sophisticated methods to gain deeper insights into slug flow behavior: Frequency Domain Analysis of Slug Patterns Discover techniques for analyzing slug flow in the frequency domain to identify dominant frequencies and patterns in slug formation and propagation. Statistical Analysis of Slug Characteristics Learn to apply statistical methods to characterize the variability and distribution of slug properties across your simulation domain and time. Practical Tips for Simulation Stability and Accuracy Enhance your simulation skills with expert advice on improving results: Optimizing Mesh Design for Slug Flow Explore mesh refinement strategies specifically tailored to capture the intricate details of slug flow while maintaining computational efficiency. Implementing Adaptive Time-Stepping Learn to use adaptive time-stepping techniques to efficiently handle the varying time scales present in slug flow simulations. Why This Module is Essential for Intermediate Multiphase Flow Engineers This intermediate-level module offers a practical application of advanced CFD techniques in multiphase pipeline flow. By completing this simulation, you’ll gain valuable insights into: Advanced application of the Eulerian multiphase model for simulating complex gas-liquid interactions in slug flow regimes Essential CFD techniques for capturing turbulence, phase distribution, and transient behavior in pipeline slug flow Practical applications of multiphase CFD analysis in oil and gas, chemical processing, and industrial fluid transport sectors By the end of this episode, you’ll have developed crucial skills in: Setting up and running slug flow simulations using Ansys Fluent Interpreting simulation results to assess slug flow characteristics and their impact on pipeline performance Applying CFD insights to enhance understanding and optimization of multiphase pipeline transport systems This knowledge forms a solid foundation for engineers and researchers looking to specialize in multiphase flow analysis and pipeline design, providing a springboard for advanced studies in flow assurance, process optimization, and innovative multiphase transport solutions. Join us on this exciting journey into the world of slug flow CFD simulation, and take your next steps towards becoming an expert in multiphase dynamics modeling for critical industrial and energy sector applications!
Episode 1 27m 42s
-
-
Section 10
Nano-Fluid (MIXTURE)
-
Revolutionizing Heat Transfer: Nano Fluid in Heat Source Channel Mixture Multiphase CFD Simulation Welcome to the “Nano Fluid in Heat Source Channel Mixture Multiphase CFD Simulation” episode of our “MULTI-PHASE Flow: INTERMEDIATE” course. This comprehensive module introduces you to the cutting-edge world of nanofluid heat transfer, focusing on the complex dynamics of nanoparticle-enhanced fluids in channels with heat sources. Learn how to leverage the Mixture multiphase model in ANSYS Fluent to simulate and analyze the intricate flow and heat transfer characteristics of nanofluids, providing essential skills for engineers in thermal management, energy systems, and advanced cooling technologies. Understanding Nanofluids and Their Role in Enhanced Heat Transfer Before diving into the simulation specifics, let’s explore the fundamental concepts of nanofluids and their significance in modern heat transfer applications. Principles of Nanofluid Behavior in Heat Transfer Discover how nanofluids, consisting of base fluids with suspended nanoparticles, enhance heat transfer capabilities through unique thermal and flow properties. Applications of Nanofluids in Advanced Cooling Systems Learn about the diverse applications of nanofluids in improving the efficiency of heat exchangers, cooling systems, and thermal management solutions across various industries. Setting Up the Mixture Multiphase Model for Nanofluid Simulation This section focuses on configuring the Mixture model for accurate representation of nanofluid behavior: Defining Base Fluid and Nanoparticle Phases Gain insights into properly setting up the base fluid as the primary continuous phase and nanoparticles as the secondary dispersed phase, including material properties crucial for accurate nanofluid simulation. Configuring Phase Interactions and Mixture Properties Understand the critical aspects of modeling phase interactions and calculating effective properties of the nanofluid mixture based on nanoparticle volume fraction. Implementing the Heat Source Channel Simulation Domain Master the art of creating a representative environment for nanofluid heat transfer simulations: Defining Channel Geometry and Heat Source Integration Learn techniques for implementing a simulation domain that accurately represents a channel with an integrated heat source, including appropriate mesh strategies for capturing complex flow and thermal features. Incorporating Material Properties and Thermal Characteristics Explore methods for defining and implementing the thermal properties of both the base fluid and nanoparticles, crucial for accurate heat transfer modeling. Heat Transfer Modeling in Nanofluid Simulations Dive deep into the critical aspects of modeling heat transfer in nanofluid systems: Implementing Energy Equations for Nanofluid Mixtures Understand how to set up and configure energy equations that accurately capture heat transfer from the source to the nanofluid mixture, accounting for the unique properties of nanofluids. Modeling Enhanced Thermal Conductivity of Nanofluids Learn methods to incorporate the enhanced thermal conductivity of nanofluids into your simulation, a key factor in their improved heat transfer performance. Boundary Conditions and Turbulence Modeling Develop skills to accurately capture the flow and thermal conditions in nanofluid simulations: Specifying Inlet, Outlet, and Wall Conditions Master the techniques for defining appropriate boundary conditions, including inlet flow characteristics, outlet pressure conditions, and wall thermal specifications. Selecting and Configuring Turbulence Models for Nanofluid Flow Learn to choose and set up suitable turbulence models that account for the unique flow characteristics of nanofluids in channels with heat sources. Post-Processing and Performance Evaluation Develop expertise in extracting meaningful insights from your nanofluid heat transfer simulations: Visualizing Temperature Distributions and Velocity Profiles Master techniques for creating insightful visualizations of temperature distributions and velocity profiles throughout the channel, highlighting the enhanced heat transfer capabilities of nanofluids. Analyzing Nanoparticle Concentration Patterns and Heat Transfer Coefficients Learn to quantify and interpret nanoparticle concentration distributions and local heat transfer coefficients, crucial for assessing the performance of nanofluid-based cooling systems. Practical Applications and Engineering Relevance Connect simulation insights to real-world thermal management challenges: Optimizing Cooling System Design with Nanofluids Explore how CFD simulations of nanofluid heat transfer can inform the design of more efficient and compact cooling systems for electronics, power plants, and other high-heat applications. Assessing Nanofluid Performance in Various Heat Exchanger Configurations Understand how the principles learned in this module can contribute to evaluating and enhancing the performance of various heat exchanger designs using nanofluids. Why This Module is Essential for Intermediate Multiphase Flow Engineers This intermediate-level module offers a practical application of advanced CFD techniques in nanofluid heat transfer. By completing this simulation, you’ll gain valuable insights into: Advanced application of the Mixture multiphase model for simulating complex nanofluid behavior in heat transfer scenarios Essential CFD techniques for capturing enhanced thermal conductivity, flow patterns, and heat transfer coefficients in nanofluid systems Practical applications of nanofluid CFD analysis in thermal management, energy efficiency, and advanced cooling technologies By the end of this episode, you’ll have developed crucial skills in: Setting up and running nanofluid heat transfer simulations using ANSYS Fluent Interpreting simulation results to assess nanofluid performance in enhancing heat transfer in channels with heat sources Applying CFD insights to optimize thermal management solutions and cooling system designs This knowledge forms a solid foundation for engineers and researchers looking to specialize in advanced heat transfer technologies and multiphase flow analysis, providing a springboard for innovative cooling solutions and energy-efficient thermal management systems. Join us on this exciting journey into the world of nanofluid heat transfer CFD simulation, and take your next steps towards becoming an expert in multiphase dynamics modeling for cutting-edge thermal management applications!
Episode 1 15m 21s
-
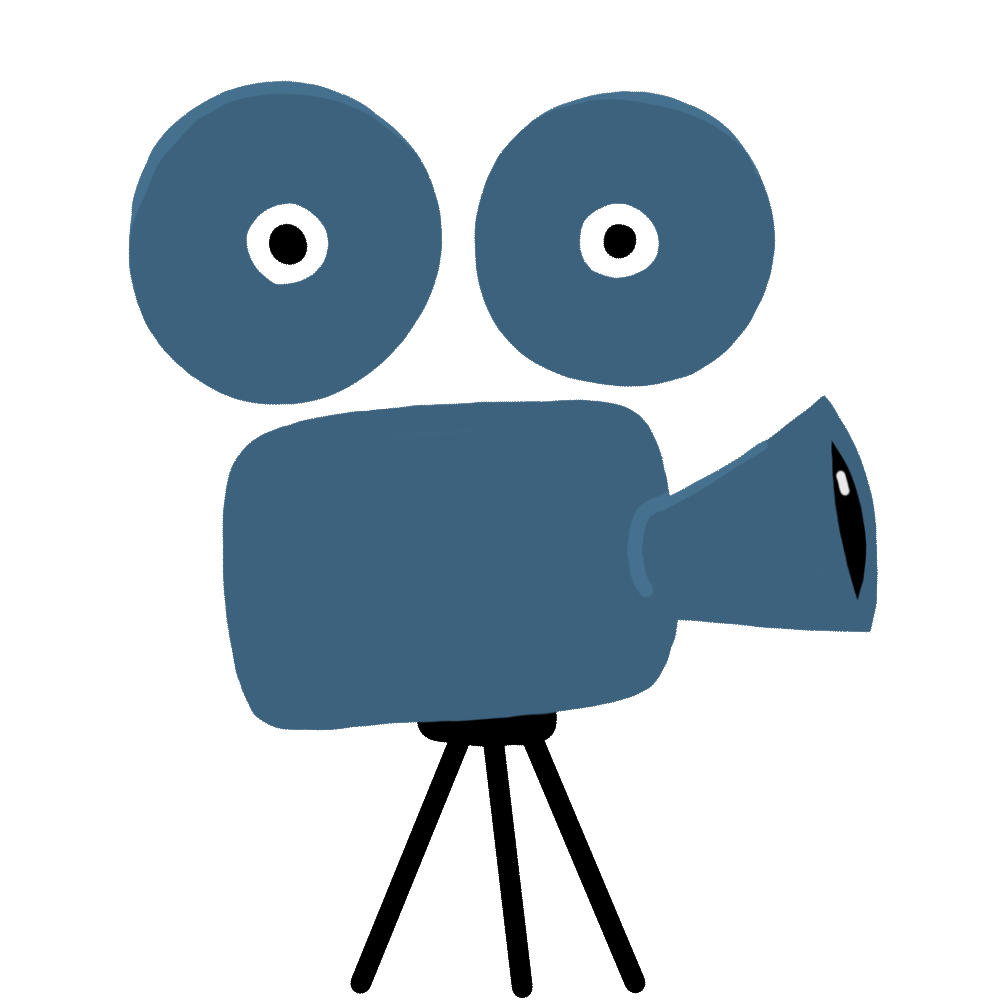
Course In Progress
Course still in development. Check back often for updates.
MULTI-PHASE Flow: INTERMEDIATE - Advanced CFD Mastery with ANSYS Fluent
Elevate your Computational Fluid Dynamics (CFD) expertise to new heights with our comprehensive “MULTI-PHASE Flow: INTERMEDIATE” course. Designed for ANSYS Fluent users with foundational knowledge, this program offers an in-depth exploration of advanced multi-phase simulation techniques across various engineering applications.
Our subscription-based course covers all three main multi-phase sub-models in ANSYS Fluent, providing you with practical, industry-relevant examples that will enhance your ability to tackle complex fluid dynamics challenges. Whether you’re an engineer, researcher, or industry professional, this course will equip you with the skills to excel in multi-phase CFD simulations.
Course Structure: Mastering Multi-Phase CFD Models
Our MULTI-PHASE Flow: INTERMEDIATE course is meticulously structured to provide a balanced approach to learning, with a strong emphasis on the widely-used Volume of Fluid (VOF) model while also covering Eulerian and Mixture models for a well-rounded understanding of multi-phase CFD techniques.
1. Volume of Fluid (VOF) Model (6 Episodes)
Dive deep into free surface flows and complex fluid interfaces:
- Bridge Pillars External Two-Phase Flow: Analyze water-air interactions around structures
- Stepped Spillway (Stair Spillway): Simulate complex hydraulic structures
- Waterfall Using Two-Phase Flow: Master free surface flow in natural environments
- Pigging Oil Flow in a Pipeline: Explore industrial pipeline maintenance simulations
- Open-channel two-phase flow in rough rivers: Study environmental fluid dynamics
- Water Discharge of a Rotating Tank: Investigate centrifugal effects on fluid discharge
2. Eulerian Model (3 Episodes)
Master multi-fluid interactions and particle-laden flows:
- Agricultural Drone Sprayer: Simulate precision agriculture applications
- Cascade Simulation: Analyze multi-phase flow in power generation systems
- Sludge Flow Settling in a Pipe: Investigate particle settling in industrial processes
3. Mixture Model (1 Episode)
Explore advanced heat transfer applications:
- Nano Fluid in Heat Source Channel: Simulate cutting-edge cooling technologies
Key Features of Our Intermediate Course
Our MULTI-PHASE Flow: INTERMEDIATE course offers unique advantages for advancing your CFD expertise:
Hands-On Training with Real-World Applications
Apply your skills to practical, industry-relevant scenarios:
- Simulate complex engineering problems across various sectors
- Gain experience with diverse multi-phase flow phenomena
- Develop problem-solving skills for real-world fluid dynamics challenges
Comprehensive Coverage of Multi-Phase Models
Master all major multi-phase simulation techniques:
- In-depth exploration of the Volume of Fluid (VOF) model
- Practical applications of Eulerian and Mixture models
- Understanding model selection criteria for different scenarios
Learning Outcomes and Skill Development
By completing our MULTI-PHASE Flow: INTERMEDIATE course, you’ll gain:
Advanced Multi-Phase CFD Simulation Techniques
Elevate your simulation capabilities:
- Set up and run complex multi-phase simulations in ANSYS Fluent
- Implement advanced boundary conditions and solver settings
- Troubleshoot and optimize multi-phase CFD models
Industry-Specific Knowledge and Applications
Broaden your expertise across various engineering fields:
- Apply multi-phase CFD to hydraulic engineering and environmental flows
- Simulate industrial processes involving particle-laden flows
- Analyze advanced heat transfer applications with nano-fluids
Course Delivery and Support
Our subscription-based model ensures continuous learning and support:
Flexible Learning Schedule
Tailor your learning experience to your needs:
- Access course materials anytime, anywhere
- Progress through episodes at your own pace
- Revisit complex topics as needed for thorough understanding
Ongoing Support and Updates
Stay at the forefront of CFD technology:
- Regular updates with new episodes and case studies
- Access to a community of CFD professionals and instructors
- Continuous improvement of your multi-phase simulation skills
Why Choose Our MULTI-PHASE Flow: INTERMEDIATE Course?
This course offers unparalleled advantages for advancing your multi-phase CFD expertise:
- Comprehensive coverage of 10 diverse and industry-relevant multi-phase applications
- Balanced focus on VOF, Eulerian, and Mixture models for well-rounded skill development
- Hands-on experience with advanced ANSYS Fluent features for multi-phase simulations
- Real-world engineering scenarios for practical skill application
By enrolling in our MULTI-PHASE Flow: INTERMEDIATE course, you’ll:
- Master complex multi-phase CFD simulations using ANSYS Fluent
- Enhance your problem-solving skills for challenging fluid dynamics issues
- Boost your career prospects in CFD-related fields across various industries
- Join a community of skilled CFD practitioners and expand your professional network
Take the next step in your CFD journey and become a true expert in multi-phase flow simulations. Join us today to unlock new possibilities in your engineering career!
Course Price: $1.00 / Month
Dive into the world of multiphase flow simulation with this comprehensive ANSYS Fluent course designed for beginners. Master the fundamentals of Volume of Fluid (VOF), Eulerian, and Mixture models through hands-on tutorials covering a diverse range of applications. From shower drains to fuel injectors, learn to simulate complex multiphase phenomena using industry-standard CFD tools. This subscription-based course offers a structured approach to building your multiphase modeling skills, equipping you with practical knowledge for real-world engineering challenges.
Subscribe
Benefits of subscribing to the course
- Complete access to All chapters
- Special discount
- Free access to all new and updated content
- Cancel subscription anytime
* You will have access to the course only until your subscription ends; after that, your subscription will be automatically renewed unless you cancel it.
Congratulations
Congratulations! You have successfully subscribed to the course.
You can now start learning the course by clicking the button "Start Learning".
You can manage your subscription like canceling or upgrading the subscription, adding or changing the payment method, etc by clicking the button "Manage Subscriptions".
Add Payment Method
Please enter your payment method details.